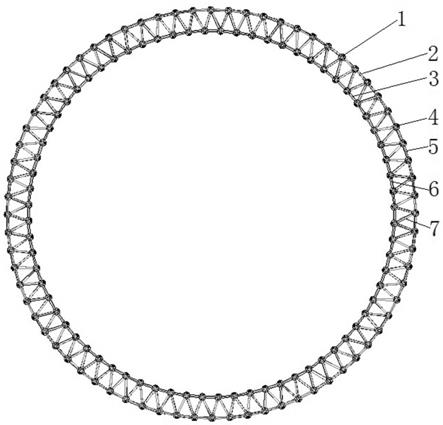
1.本发明涉及地铁盾构隧道始发施工技术领域,尤其是一种负环管片结构及其施工方法。
背景技术:2.负环管片为盾构施工中,在反力架及盾构千斤顶之间安装的环状管片,以提供盾构机向前的推力,使盾构机盾尾进入洞门圈,直到地层与正环管片之间摩擦力足以抵消盾构前进所需推力时方可拆除的一种临时管片。
3.目前国内外常用的管片类型有钢筋混凝土管片、铸铁管片、球墨铸铁管片、钢管片、复合管片,上述各类管片均具有其优势和劣势,具体如下:钢筋混凝土负环管片成本低、使用最多、耐久性好、可构建实用、无障碍衬砌,但自重较大,运输以及拆除极困难,且拆除过程中边角容易破碎,重复使用率低。
4.铸铁管片延性和强度接近于钢材,管片较轻,安装方便,耐腐蚀性好,机械加工后管片精度高,但金属消耗量大、机械加工成本高,且具有脆性破坏特性。
5.球墨铸铁管片强度好、耐久性好、制作精度高,可承受特殊载荷,但管片自重大,材料成本高,焊接困难。
6.钢管片重量轻、强度高、可重复利用性好,但焊接变形大,制作工艺要求高。
7.复合管片与钢筋混凝土管片相比厚度小,管片轻,但强度比钢筋混凝土管片大、抗渗性好;与铸铁管片相比,它具有抗压性、韧性高等特点;与钢管片相比金属消耗量小;但耐腐蚀性差,成本高。
技术实现要素:8.本发明的目的是根据上述现有技术的不足,提供了一种负环管片结构及其施工方法,通过采用环形桁架结构,在保证负环管片整体结构受力要求的基础上,实现负环管片的现场快速拼装,解决负环管片重复使用率低,负环施工成本高,管片自重较大,拆除困难,拆解后体积大,运输不便等问题。
9.本发明目的实现由以下技术方案完成:一种负环管片结构,其特征在于:该负环管片结构为环形桁架结构,其包括由内环和外环所构成的管片单元,其中所述内环和所述外环分别包括环向布置的若干受力杆,所述内环的各受力杆之间通过内环连接杆可拆卸式连接固定构成整体结构,所述外环的各受力杆之间通过外环连接杆可拆卸式连接固定构成整体结构,所述内环和所述外环的受力杆之间通过骨架连接杆可拆卸式连接固定构成整体结构。
10.所述受力杆的杆体上设置有连接盘,所述连接盘分别与所述内环连接杆、所述外环连接杆和所述骨架连接杆之间通过插销构成盘扣连接。
11.所述连接盘、所述内环连接杆、所述外环连接杆和所述骨架连接杆上分别设置有销孔,所述插销可插入所述销孔内实现连接。
12.所述负环管片结构包括两个或两个以上的管片单元,所述受力杆的两端分别设置有公插头和母接头,相邻的所述管片单元的受力杆之间通过所述公插头和所述母接头的配合构成插入式连接以实现相邻的所述管片单元之间的轴向连接。
13.所述负环管片结构与盾构机盾尾的形状、尺寸相吻合适配。
14.一种涉及上述负环管片结构的施工方法,其特征在于:所述施工方法包括以下步骤:将受力杆、内环连接杆、外环连接杆、骨架连接杆自下而上拼装构成首环管片单元;将拼装完成的首环管片向外顶推一定距离,并进行下一环管片单元的拼装,在拼装时,先将下一环管片单元的受力杆的公插头插入首环管片单元的受力杆的母接头内,而后通过内环连接杆、外环连接杆和骨架连接杆将其受力杆连接成环;以此往复,进行所有管片单元的拼装直至完成负环管片结构。
15.本发明的优点是:降低施工成本,可实现快速组装和拆除;提高负环管片整体结构稳定性,减小单个杆件受力,确保单个杆件受力满足要求,大大减小拆解后的空间体积;提高负环管片结构的重复利用率,降低运输成本;各配件因受力明确不易损坏,且各配件的标准化程度高,即使单个配件发生损坏也可实现快速更换;结构简单合理,施工安全性极高,适于推广。
附图说明
16.图1为本发明的主视图;图2为本发明的立体结构示意图;图3为本发明的立体结构示意图;图4为本发明中受力杆的结构示意图;图5为本发明中受力杆连接盘的结构示意图;图6为本发明中连接杆的结构示意图;图7为本发明中插销的结构示意图。
具体实施方式
17.以下结合附图通过实施例对本发明特征及其它相关特征作进一步详细说明,以便于同行业技术人员的理解:如图1-7所示,图中标记1-14分别表示为:负环管片结构1、外环2、内环3、受力杆4、外环连接杆5、内环连接杆6、骨架连接杆7、连接盘8、公插头9、母接头10、销孔11、连接杆12、销孔13、插销14。
18.实施例:如图1所示,本实施例中的负环管片结构1为环形桁架结构,其包括由外环2和内环3所拼装构成的管片单元。负环管片结构1包括若干沿轴向连接的管片单元,若干管片单元可拼接构成整体结构。
19.具体而言,如图1至图3所示,外环2包括若干受力杆4,各受力杆4之间通过外环连接杆5环向连接固定构成整体结构;内环3包括若干受力杆4,各受力杆4之间通过内环连接杆6环向连接固定构成整体结构。同时,外环2和内环3的各受力杆4之间通过骨架连接杆7径向连接固定构成整体结构。
20.如图4所示,受力杆4的杆体上设置有用于与各连接杆对接的连接盘8。如图5所示,
该连接盘8呈圆盘状,其周向均匀布置有若干销孔11。销孔11的数量及位置满足于外环连接杆5、内环连接杆6、骨架连接杆7的连接位置要求。
21.如图6所示,其图示的连接杆12为外环连接杆5、内环连接杆6、骨架连接杆7的代表示意结构,即外环连接杆5、内环连接杆6、骨架连接杆7均为连接杆12的结构形状,但外环连接杆5、内环连接杆6、骨架连接杆7因其各自连接位置的不同而存在一定不同,例如:因外环2和内环3均为环状,因此外环连接杆5和内环连接杆6均为具有弧度的杆件,而连接外环2和内环3的骨架连接杆7则一般为直杆。各连接杆的两端分别开设有销孔13,该销孔13与连接盘8上所开设的销孔11构成匹配。结合图7所示,将插销14插入销孔13和销孔11时,可实现各连接杆(外环连接杆5、内环连接杆6、骨架连接杆7)与连接盘8之间的连接固定,从而实现外环2的各受力杆4之间的盘扣连接、内环3的各受力杆4之间的盘扣连接以及内、外环的受力杆4之间的连接。
22.在本实施例中,结合图2至图4所示,每个管片单元的受力杆4上设置有沿轴向间隔布置的两环外环2和内环3,这两环外环2和内环3分别安装在受力杆4的两个连接盘8上。
23.如图4所示,受力杆4的一端设置有公插头9,另一端设置有母接头10,该公接头9和母接头10的结构相吻合适配,使公插头9可插装在母接头10的内部。在使用时,相邻的管片单元的各受力杆4之间可通过公插头9与母插头10之间的配合,以将相邻的两环管片单元轴向连接并构成整体结构。
24.在本实施例中,在公插头9和母接头10的连接位置还可通过设置开槽并插入限位件的方式,使公插头9和母接头10之间得到限位锁定,避免两者之间发生相对旋转,从而导致负环管片结构1的破坏。
25.本实施例通过标准化的杆件所拼装构成的负环管片结构1的整体结构稳定性大大提高,减小单个杆件受力,确保单个杆件受力满足要求。由于负环管片结构1主要受到轴向力,通过相邻管片单元之间的插入式连接,可利用负环管片结构1所受的轴向力提高各管片单元之间的结构整体性;同时,采用桁架结构连接的受力杆4可均匀分摊所受作用力,避免因局部受力过大而导致的结构破坏。此外,当负环管片结构1使用完毕后,可通过拆除插销14解除各杆件之间的连接锁定,将负环管片结构1拆解为以杆件为单位的部件,可大大减小拆解后所占的空间体积,便于重复利用。
26.本实施例在施工时,包括如下施工步骤:1)盾构机具备始发条件后,在整圈盾尾内焊接圆形钢管,做好盾尾间隙预留措施。由于负环管片结构1的外径比盾尾内径小,因此通过焊接圆形钢管对负环管片结构1的位置进行限位,确保负环管片相对于盾尾居中,并进一步保证两者尽量同心,防止由于重力或盾尾刷挤压导致单侧盾尾间隙过大或过小。
27.2)将负环管片结构1的各连接杆件运输至盾尾内,将各杆件参照图1至图3的结构自下而上开始组装整环管片:3)采用千斤顶油缸将整环管片向外顶推,以确保下一环管片拼装间距,开始下一环管片拼装,拼装前先将受力杆4的公接头9直接插入上一环受力杆4的母接头10内,然后通过受力杆4、外环连接杆5、内环连接杆6将各受力杆4连接成环。
28.4)重复步骤3),直到完成所需负环管片拼装。
29.虽然以上实施例已经参照附图对本发明目的的构思和实施例做了详细说明,但本
领域普通技术人员可以认识到,在没有脱离权利要求限定范围的前提条件下,仍然可以对本发明作出各种改进和变换,故在此不一一赘述。