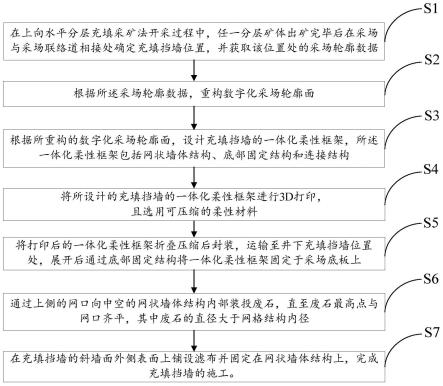
1.本发明属于充填采矿领域,具体涉及一种基于一体化柔性框架的充填挡墙及施工方法。
背景技术:2.在上向水平分层充填采矿法采矿过程中,每一分层矿体开采完毕后,在采场与采场联络道相接处构筑充填挡墙,进行不接顶充填工作,不接顶的目的是为上一水平分层矿体开采提供落矿空间。
3.一般矿山充填挡墙以钢筋混凝土结构为主,施工时在两侧围岩内植入锚杆,架设横向、纵向两排工字钢或钢筋,铺设模板,并在充填挡墙内外两侧架设支撑木棍,防止挡墙倒塌,然后浇筑混凝土,待混凝土凝固后拆模,在挡墙内侧铺设滤布;同时,对于采场断面,在设计过程中形状一般较规整,但实际爆破过程中基本难以实现,所以在充填挡墙构筑过程中采场断面基本属于不规则形状,在施工过程中还需要添加填塞物,保证充填挡墙的密封性。但是,上述充填挡墙施工工序复杂,工人劳动强度大,此外充填挡墙内外两侧架设支撑木制结构有倒塌风险,容易造成充填浆体四溢并严重威胁工人生命安全;另外,当涉及到超过600~800m的深部开采时,高井温导致井下工人工作环境恶劣,此时的充填挡墙施工表现出高劳动强度、高度复杂工序的特征,进一步增加了工人施工的安全隐患,上述充填挡墙施工方式将无法实现。
4.现有技术中,为了解决深部开采时的充填挡墙施工问题,存在以下几种解决方案,但各自均存一定的不足之处。例如,公开号为cn 113356924 a的中国专利提出了一种可拆除利用的巷道充填挡墙及其构筑方法,虽然构筑结构简单、材料少且可开拆除重复使用,能满足井下充填需要,但是外层骨架包括大量圆钢和工字钢,安装拆卸工艺反复繁琐,费时费力,成本较高;公开号为cn 113027519 a的中国专利提出了一种充填料自筑挡墙及构筑方法,在巷道内自下而上设置的若干个充填挡墙体,若干个充填挡墙体呈阶梯状排列在巷道内,每个充填挡墙体包括呈相对设置的两块挡板,两块挡板的边缘均与巷道内的围岩贴合,两块挡板与围岩组成梯形状的充填空间,充填空间内填充充填料,本专利虽然梯形上窄下宽的结构有效提高充填挡墙体的抗滑移和抗倾覆能力,继而提高整个自筑挡墙的强度和稳定性,但是梯形斜面在外侧,仅起到抗滑移作用,每个挡墙需施工多个锚杆,工人劳动量大。公开号为cn 113882896 a的中国专利提出了一种井下可重复回收的柔性充填挡墙及其施工方法,虽然简化了施工工艺,提高了施工效率,改善了装药效果,增大了爆破进尺,减少了综合采矿成本,但是利用管材支撑钻孔壁的同时,孔内管材亦隔绝了炸药与岩石的直接接触,对爆破效果产生了负面影响;公开号为专利cn 112709599 a的中国专利提出了一种拉索式充填挡墙及施工方法,但是结构复杂,组件较多,施工过程中还包括铰接、焊接工艺,施工复杂,工人劳动强度大。
技术实现要素:5.有鉴于此,本发明实施例提供了一种基于一体化柔性框架的充填挡墙及施工方法,预先制备可收缩的一体化充填挡墙柔性框架,在相应位置处展开并固定后,直接装填现场废石,铺设滤布后再进行充填体的料浆充填,施工简便、迅速,工人劳动强度低,且现场废石得以有效利用,提高了充填挡墙施工效率。
6.为实现上述目的,本发明的实施例采用如下技术方案:
7.第一方面,本发明的实施例提供了一种基于一体化柔性框架的充填挡墙施工方法,所述施工方法包括:
8.步骤s1,在上向水平分层充填采矿法开采过程中,任一分层矿体出矿完毕后,在采场与采场联络道相接处确定充填挡墙位置,并获取该位置处的采场轮廓数据;
9.步骤s2,根据所述采场轮廓数据,重构数字化采场轮廓面;
10.步骤s3,根据所重构的数字化采场轮廓面,设计充填挡墙的一体化柔性框架,所述一体化柔性框架包括网状墙体结构、底部固定结构和连接结构;其中:
11.网状墙体结构横截面为直角梯形,垂直于横截面按预定间隔设置若干网状面,包括两端的直角墙面和斜墙面;网状面截止于轮廓面边界的节点相互连接形成网格状侧面,网状墙体结构上下不连接成面,上侧作为网口,网口高度与充填设计高度一致;底部固定结构呈平面网状结构,网状墙体结构设置于所述底部固定结构一端的上侧,其中直角墙面在端部,斜墙面在内侧;连接结构用于连接底部固定结构和网状墙体结构;
12.步骤s4,将所设计的充填挡墙的一体化柔性框架进行3d打印,且选用可压缩的柔性材料;
13.步骤s5,将打印后的一体化柔性框架折叠压缩后封装,运输至井下充填挡墙位置处,展开后通过底部固定结构将一体化柔性框架固定于采场底板上;
14.步骤s6,通过上侧的网口向中空的网状墙体结构内部装投废石,直至废石最高点与网口齐平,其中废石的直径大于网格结构内径;
15.步骤s7,在充填挡墙的斜墙面外侧表面上铺设滤布并固定在网状墙体结构上,完成充填挡墙的施工。
16.作为本发明的一个优选实施例,所述获取该位置处的采场轮廓数据,由人工手持空区监测系统cms扫描设备或其他现场扫描装置,扫描现场的环境,得到采场轮廓数据。
17.作为本发明的一个优选实施例,所述步骤s3所设计的充填挡墙一体化柔性框架中,网状墙体结构在形成直角梯形横截面的斜墙面的外侧网状结构上,设置有第一连接面,第一连接面的数量与连接结构的数量相同;在底部固定结构的平面网格结构与第一连接面相对应的位置处,设置有第二连接面;所述连接结构连接于第一连接面和第二连接面之间,使用状态下呈直线型,与地面形成预定的角度。
18.作为本发明的一个优选实施例,所述连接结构在网状墙体结构斜墙面的两端各自由上至下布置为一组三个,共两组。
19.作为本发明的一个优选实施例,所述网状墙体结构和底部固定结构的网格结构,为正六边形和/或正五边形。
20.作为本发明的一个优选实施例,网状墙体结构和底部固定结构的网格直径为0.5-2.0cm;连接结构的直径为5mm-30mm,长径比大于10。
21.作为本发明的一个优选实施例,步骤s5的封装,将一体化柔性框架折叠并压缩为与墙体的直角墙面一致的平面后,进行封装。
22.第二方面,本发明实施例还提供了一种基于一体化柔性框架的充填挡墙,其特征在于,所述充填挡墙通过上述的施工方法进行生产。
23.本发明实施例提供的基于一体化柔性框架的充填挡墙及施工方法,将cms探测技术与3d打印技术相结合,实现充填挡墙室内设计、地表制作,使传统充填挡墙构筑走向智能化;通过对充填挡墙的结构设计,充填挡墙现场安装工艺简单便捷,极大减少了充填挡墙构筑过程中工人劳动量;墙体结构按照采场轮廓面设计,使得充填挡墙具有良好密封性;作为一体化结构,无需布置木棍进行支撑,安全性较好;工人劳动时间短,工艺简洁,也可应用于深部开采的高井温环境。
附图说明
24.为了更清楚地说明本发明实施例或现有技术中的技术方案,下面将对实施例或现有技术描述中所需要使用的附图作简单地介绍,显而易见地,下面描述中的附图仅仅是本发明的一些实施例,对于本领域普通技术人员来讲,在不付出创造性劳动的前提下,还可以根据这些附图获得其它的附图。
25.图1为本发明实施例基于一体化柔性框架的充填挡墙施工方法流程图;
26.图2为本发明实施例中采场轮廓重构图;
27.图3为本发明实施例中基于一体化柔性框架结构示意图;
28.图4为本发明实施例中基于一体化柔性框架的折叠状态示意图;
29.图5为本发明实施例中充填挡墙轮廓与采场耦合的立体图;
30.图6为本发明实施例中充填挡墙轮廓与采场耦合的后视图;
31.图7为本发明实施例中充填挡墙填装废石后的示意图;
32.图8为本发明实施例中基于充填挡墙的填充体示意图。
33.附图标记说明:
34.1-采场轮廓面,2-第二连接面,3-连接结构,4-底部固定结构,5-网口,6-网状墙体结构,7-采场轮廓,8-废石,9-充填体,10-第一连接面。
具体实施方式
35.下面结合附图对本发明实施例进行详细描述。
36.应当明确,所描述的实施例仅仅是本发明一部分实施例,而不是全部的实施例。基于本发明中的实施例,本领域普通技术人员在没有作出创造性劳动前提下所获得的所有其它实施例,都属于本发明保护的范围。
37.本发明针对目前充填挡墙构筑中存在工人劳动强度大、施工工艺复杂,安全性差以及未来深部开采的不适用性等问题,提出了一种基于一体化柔性框架的充填挡墙及施工方法,同时适用于深部开采。本发明通过cms探测技术获取充填挡墙构筑位置的轮廓面,通过计算机将获取的轮廓面生成三维模型,基于三维模型进行充填挡墙室内设计,使用树脂材料通过3d打印手段将设计好的充填挡墙整体打印,最后运输到采场相应位置完成安装后,执行废石填装、滤布铺设和料浆注入,得到充填墙体,以减少施工过程中工人劳动强度,
简化复杂施工工艺,保障施工过程中工人生命安全,同时保证在深部采矿高井温环境中工人能够轻松便捷施工充填挡墙。
38.图1为本发明实施例所述基于一体化柔性框架的充填挡墙施工方法流程图。如图1所示,所述施工方法包括:
39.步骤s1,在上向水平分层充填采矿法开采过程中,任一分层矿体出矿完毕后,在采场与采场联络道相接处确定充填挡墙位置,并获取该位置处的采场轮廓数据。
40.本步骤中,所述获取该位置处的采场轮廓数据,由人工手持空区监测系统(cavity monitoring system,cms)扫描设备或其他现场扫描装置,扫描现场的环境,得到采场轮廓数据。
41.步骤s2,根据所述采场轮廓数据,重构数字化采场轮廓面。
42.本步骤中,获取采场轮廓数据后在室内通过计算机进行数据处理,将cms设备内数据拷贝到计算机内,由三维建模软件进行采场轮廓面1重构。如图2所示,所重构的采场轮廓面1,为体现采场整个轮廓的三维结构体,可以清楚分辩出采场的边界。
43.步骤s3,根据所重构的数字化采场轮廓面,设计充填挡墙的一体化柔性框架,所述一体化柔性框架包括网状墙体结构、底部固定结构和连接结构。
44.本步骤中,基于重构轮廓面进行充填挡墙三维模型设计,也通过三维建模软件实现。所述一体化柔性框架包括网状墙体结构6、底部固定结构4和连接结构3三个部分。
45.如图3所示,其中,网状墙体结构6横截面为直角梯形,垂直于横截面按预定间隔设置若干网状面,包括两端的直角墙面和斜墙面;网状面截止于轮廓面边界的节点相互连接形成网格状侧面,网状墙体结构上下不连接成面,上侧作为网口5,网口5高度与充填设计高度一致;在形成直角梯形横截面的斜墙面的外侧网状结构上设置有第一连接面10,第一连接面10的数量与连接结构3的数量相同。优选地,所述网状面的网格由正多边形构成,如正六边形、正五边形或正十二边形等。所形成的网格状侧面为阵列式网格,根据节点位置形成相应图案。
46.底部固定结构4呈平面状,占据采场轮郭结构的下部部分平面,是由正多边形构成的网状结构,网状墙体结构6设置于所述底部固定结构4一端的上侧,其中直角墙面在端部,斜墙面在内侧;在网状墙体结构6的斜墙面上设置有连接结构的第一连接面10,在底部固定结构4的平面网格结构与第一连接面10相对应的位置处,设置有第二连接面2。所述的第一连接面10和第二连接面2可以占据网状结构的其中一个网格,也可以是一个强化的节点。
47.所述连接结构3设置于第一连接面10和第二连接面2之间,使用状态下呈直线型,与地面形成一定的角度;在每一组对应的第一连接面10和第二连接面间2设置一个连接结构,连接结构3、斜墙面和底部固定结构4形成稳定的三角形结构。连接结构3的受力点为斜墙面上的第一连接面10和底部固定结构4的第二连接面2,起到抗拉的作用,以防止网状墙体结构6的倒塌。优选地,所述连接结构3在网状墙体结构斜墙面的两端各自由上至下布置为一组三个,共两组。
48.优选地,所述构成网状结构的正多边形,为正六边形和/或正五边形。本实施例中将挡墙主体设计为梯形,斜面在内侧,改变了充填体对充填挡墙的作用方向,使得充填挡墙整体受力得到优化,提高了充填挡墙的稳定性;另外底部固定结构和连接结构在充填过程中被固定在充填体内,能够保证挡墙整体的稳定性。
49.步骤s4,将所设计的充填挡墙的一体化柔性框架进行3d打印,且选用可压缩的柔性材料,网状墙体结构和底部固定结构的网格直径为0.5-2.0cm;连接结构的直径为5mm-30mm,长径比大于10。
50.本步骤中,所述柔性材料优选为抗拉强度较高的柔性树脂基材料。
51.步骤s5,将打印后的一体化柔性框架折叠压缩后封装,运输至井下充填挡墙位置处,展开后通过底部固定结构将一体化柔性框架固定于采场底板上。
52.如图5和图6所示,所打印的充填挡墙一体化柔性框架与现场的采场轮廓7是相适应的,进行相应的安装后,即可得到充填墙体的骨架。
53.本步骤中,所述柔性材料,与刚性材料相对,指材料的挠性。
54.由于打印的一体化柔性框架具有一定的挠度,形成网格的边在外力作用下可发生弯曲、拉伸或压缩,并在撤去外力后恢复原状,从而使得框架可以折叠为任意形状。例如,如图4所示,将一体化柔性框架折叠并压缩为与墙体的直角墙面一致的平面,封装后便于运输、下放及安装。
55.步骤s6,通过上侧的网口向中空的网状墙体结构内部装投废石8,直至废石最高点与网口5齐平,其中废石8的直径大于网格结构内径。
56.步骤s7,在充填挡墙的斜墙面外侧表面上铺设滤布并并固定在网状墙体结构上,防止充填料浆由废石缝隙流出,完成充填挡墙的施工。
57.如图7所示,经过在一体式柔性框架的网状墙体结构内部依次装入废石和铺设滤布,得到具有外向底部固定结构和连接结构的充填墙体。
58.如图8所示,施工完成充填挡墙后,再向采场内注入料浆,直至与网口齐平,养护完成后得到采场的充填体9。浇注料浆时,充填体内的料浆由于滤布的作用,仅由部分水分渗入废石中并导出,料浆则不会由废石缝隙流出;料浆与底部固定结构和连接结构相互交融,形成一体。此时的充填挡墙作为充填体的端部结构,工艺简洁,安全性高,且可充分利用现场废料,所获得的充填体完整度高,同时提高了强度。
59.通过所述基于一体化柔性框架的充填挡墙施工方法,本实施例还提供了一种基于一体化柔性框架的充填挡墙,由以上施工方法得到。在对所述施工方法的描述过程详细说明了墙体的结构,在此不再赘述。
60.下面通过一个具体的实例,对本发明所述基于一体化柔性框架的充填挡墙及施工方法做进一步详细的说明。
61.以山东某金矿矿体的充填开采为例,该矿体具有水平厚度大(40米)、矿岩稳定性好(ii级以上)和倾角缓(20-30度)的特点,矿体埋深距离地表超过800米,开采过程中面临采场温度高(40摄氏度以上)、工人劳动强度高等亟待解决的难题。目前针对该类矿体最合适的采矿方法为上向水平分层充填法,采用竖井和斜坡道联合方式,自下而上按照分层进行回采,分层高度为4米。每个分层内的矿房和矿柱按照垂直矿体走向布置,且矿房和矿柱宽度为3米。每个分层矿房和矿柱回采结束后,在采场与采场联络道相接处铺设挡墙,然后进行尾砂胶结充填,充填高度为3米,空余1米作为上一个分层回采的爆破落矿自由面。
62.该矿原先充填挡墙施工形式主要为混凝土充填挡墙。混凝土充填挡墙施工环节为:
①
为保证混凝土挡墙能够自立,首选在采场与采场联络道相接处先进行地面平整;
②
预先搭建混凝土浇筑模板,模板和模板之间利用8号铁丝进行固定,该环节耗时一般在8个小
时以上;
③
采用jq350型搅拌机制备水泥:石子:水比例为0.5:0.5:1的混凝土料浆并浇筑到搭建好的模板内,养护3天后进行脱模形成充填挡墙。该种混凝土充填挡墙施工完毕并投入使用耗时接近4天,且人工搭建模板和拆卸模板往往需要3-4个人共同完成,工作环境温度大于40℃,劳动强度极大。此外,混凝土充填挡墙消耗的水泥和石子等材料又继续增加了充填挡墙施工成本。
63.采用本发明实施例所提供基于一体化柔性框架的充填挡墙及施工方法,施工该金矿充填采矿时的充填挡墙,步骤如下:
64.确定充填挡墙位置后,采用geosight cms三维激光扫描系统对采场与采场联络道相接处的采场轮廓进行360度旋转扫描,并连续收集采场断面距离和角度数据并生成.xyz文件。将上述.xyz文件导入3dmine软件并生成采场断面实际轮廓的.stm可视化文件。
65.利用犀牛软件设计出与从采场轮廓相匹配的五边形或六边形的充填挡墙的一体化柔性框架,利用工业3d打印设备,并采用高强度树脂(例如,抗拉强度67mpa、拉伸模量2650mpa和比重1.2g/cm3)进行模型整体打印。所述一体化柔性框架包括网状墙体结构、底部固定结构和连接结构,设计完成后,三个部分同时打印完成,是一个完整的整体结构,三个部分之间是紧密相连的。由于所打印的一体化柔性框架整体为网状结构,且采用柔性材料,能够进行弯曲和折叠,将其折叠压缩后封装,例如,采用绳索将其进行捆绑。
66.采用皮卡车将上述弯曲和折叠的网状结构的一体化柔性框架经斜坡道、采场联络道后运至采场边界位置,松开绳索后充填挡墙的网状结构的一体化柔性框能快速回复成折叠前形态,且与采场轮廓紧密接触。采用st2g铲运机将现场的废石填充进入梯形网状结构内,直到废石与上部网口平齐。在梯形面上铺设厚度为0.3mm、延展率为25%的长丝土工无纺布,利用2mm直径的铁丝将上述土工布与梯形斜面网状墙体结构进行固定连接,完成充填挡墙的施工。
67.待上述充填挡墙制备完成后,将充填管路假设进行待充的采空区内,含尾砂和32.5r水泥的充填料浆经地表充填搅拌站搅拌3分钟后经过管道运输充填进入采空区,完成充填体的施工。
68.现场应用取得了良好的效果,相比原先充填挡墙施工,施工周期缩短到4个小时,工人劳动强度大幅降低,此外,利用废石填充制备充填挡墙减少了现场废石,并使得废石得到合理再利用,进一步降低了施工成本。相比原先技术,该施工技术具有劳动强度小、安全程度可靠、综合成本低等显著优点。
69.由以上技术方案可以看出,本发明实施例所提供的基于一体化柔性框架的充填挡墙施工方法,将cms探测技术与3d打印技术相结合,实现充填挡墙室内设计、地表制作,使传统充填挡墙构筑走向智能化;通过对充填挡墙的结构设计,充填挡墙现场安装工艺简单便捷,极大减少了充填挡墙构筑过程中工人劳动量;墙体结构按照采场轮廓面设计,使得充填挡墙具有良好密封性;作为一体化结构,同时对截面形状进行优化,通过具有内侧斜面的梯形,无需再另外布置工字钢或槽钢等支撑构件,安全性较好;工人劳动时间短,工艺简洁,也可应用于深部开采的高井温环境。
70.以上所述,仅为本发明的具体实施方式,但本发明的保护范围并不局限于此,任何熟悉本技术领域的技术人员在本发明揭露的技术范围内,可轻易想到的变化或替换,都应涵盖在本发明的保护范围之内。因此,本发明的保护范围应以权利要求的保护范围为准。