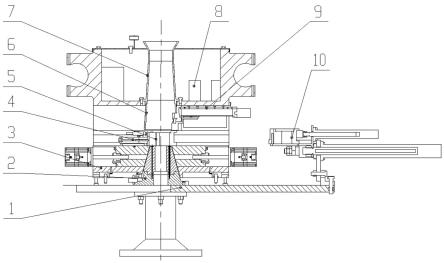
1.本发明涉及石油修井作业设备领域,特别涉及一种油田小修作业轮转接箍卡芯油管吊卡及作业工艺。
背景技术:2.随着国家对油气资源的不断开发,现有的大多数油田已经进入到石油开采的中、后期阶段,修井任务也越来越繁重。据统计,我国油田作业中有85%以上为小修作业,而在小修作业中,工作量最大、耗时最长的工作是起下管柱,分为油管起下作业和抽油杆起下作业。现阶段对于管杆起下动作,国内普遍采用双吊卡起下管杆串作业工艺。小修作业大部分作业工艺需要井口工人参与体力劳动,使井口工人的工作强度大,作业环境恶劣,作业安全隐患较高,进而小修作业效率也会随之降低。
3.针对上述问题,在不影响小修作业的工作效率的前提下,尽可能的降低井口工人的工作强度,减少井口工人的作业安全隐患,研制本发明装置形成“一吊一卡”的模式。
4.本发明属于石油修井抽油杆作业设备项目发明专利族关键技术,目前本团队已经授权的中国发明专利超过十件,密切关联共同实现油田小管杆自动化作业。本发明与中国专利zl202011073476.x《一种油田修井作业抽油杆自动吊卡及使用方法》、中国专利zl202011573843.2《一种可实现自动找正功能的抽油杆自动吊卡及使用方法》、中国专利zl202011048977.2《一种实现抽油杆自动化的油田修井作业工艺》、中国专利zl202011093257.8《一种双瓣顶升式抽油杆修井作业动力卡瓦及作业工艺》、中国专利zl202010998186.x《一种井口定位的集成导向式立式作业修井猫道及使用方法》、中国专利zl202110462646.1《基于车载修井机的抽油杆机械化小修作业集成设备与工艺》和中国专利zl202110792254.1《主从式可视化遥控小修机械化作业控制系统及方法)等发明专利族密切关联,共同完成管杆自动化/机械化作业。
5.另外,本团队申请的发明专利号为zl202111632553.5,专利名称为《一种轮转凸缘卡芯小修抽油杆吊卡及使用方法》,提供一种轮转式抽油杆吊卡设计方法和作业工艺,与本发明与具有相辅相成关系,本发明扩大至油管作业范围,包含该专利未使用的新结构和新作业工艺。
技术实现要素:6.本发明的目的就是针对现有技术存在的上述缺陷,提供一种油田小修作业轮转接箍卡芯油管吊卡及作业工艺,替代井口工人作业,实现机械/自动化作业,在不改变作业工况下,无需工人频繁的拔插吊卡销子、摘换吊卡,极大的降低井口工人的工作强度,减少井口工人的作业安全隐患,同时可以提高修井作业的工作效率。
7.本发明提到的一种油田小修作业轮转接箍卡芯油管吊卡,其技术方案是:包括底座模块、卡芯支撑模块、壳体模块、承托模块、油管接箍卡芯、锁销模块、导向模块、控制模块、推动模块、送料模块,底座模块的上侧安装壳体模块,壳体模块的中部安设卡芯支撑模
块,所述油管接箍卡芯支撑油管,安装在壳体模块中部,且在壳体模块内导槽内滑动,壳体模块内设置油管接箍卡芯工作位置和待机位置;推动模块位于油管接箍卡芯上部壳体模块内,推动电磁铁吸合油管接箍卡芯,由直线模组推动油管接箍卡芯实现油管接箍卡芯在工作位置和待机位置转换;卡芯支撑模块和承托模块在油管接箍卡芯下部,共同支撑油管接箍卡芯,其中在起升油管工况时,由承托模块独立承托油管接箍卡芯,在停止底板工况时,卡芯支撑模块支撑油管接箍卡芯;承托模块的贯通式丝杆步进电机驱动接箍卡芯左支撑体和接箍卡芯右支撑体实现打开和闭合,闭合工况时,接箍卡芯左支撑体和接箍卡芯右支撑体承托油管接箍卡芯,打开工况时,油管吊卡上升,油管接箍卡芯从接箍卡芯左支撑体和接箍卡芯右支撑体中间下落,脱离壳体模块座于卡芯支撑模块;导向模块位于油管接箍卡芯正上方,油管自下而上进入导向模块后,油管导向套将油管导入中心作业位置;控制模块位于壳体模块上部腔体内,实现油管吊卡驱动和控制;送料模块安装在底座模块,位于油管吊卡侧面,将油管接箍卡芯送入和取出油管吊卡和卡芯支撑模块。
8.优选的,上述壳体模块包括支撑调节螺栓、底部接近开关、超声传感器、底部接近开关安装座、超声传感器安装座、壳体、承托定位块、定位块销轴、吊环槽、吊环槽销和上盖壳,所述壳体的底部设有支撑调节螺栓、底部接近开关、超声传感器,底部接近开关安装在底部接近开关安装座上,底部接近开关安装座固定在壳体的底部;所述壳体的中间开孔,孔内自下而上依次安装承托模块、油管接箍卡芯、推动模块和锁销模块,同时也是安装滑动通道;壳体中部竖直方向是油管接箍卡芯作业区域,下部为锥形空间,安装卡芯支撑模块,上部为导向模块,用于实现油管居中;其中,承托定位块是承托模块的接箍卡芯左支撑体、接箍卡芯右支撑体运动的定位面,定位块销轴实现承托定位块定位;两个吊环槽对称安装在壳体的上部,用于连接修井机大钩的两个吊环,吊环槽外端安装吊环槽销,上盖壳连接在壳体上端,实现壳体模块封闭。
9.优选的,上述壳体包括进入锥面、支撑面、工作面、工作导向面、推动面、导向安装面、工作位置和待机位置,其中,进入锥面为锥体结构,油管接箍进入导向面;支撑面是承托模块工作面;工作面是油管接箍卡芯移动支撑工作面;工作导向面为与油管接箍卡芯的导向面接触面,实现油管接箍卡芯的导向,防止旋转发生;推动面是推动模块的工作面,也是锁销模块所在安装面;导向安装面是用于安装导向模块,居中安装;工作位置和待机位置是油管接箍卡芯两个位置,其中工作位置位于油管吊卡竖直轴线中心。
10.优选的,上述承托模块由贯通式丝杆步进电机、接箍卡芯左支撑体、接箍卡芯右支撑体、接箍卡芯托板和电机安装板组成,所述接箍卡芯左支撑体和接箍卡芯右支撑体组成接箍卡芯支撑体,共同支撑油管接箍卡芯,所述贯通式丝杆步进电机连接并带动接箍卡芯支撑体在壳体内左右移动,接箍卡芯左支撑体和接箍卡芯右支撑体拼合一体;接箍卡芯托板连接在接箍卡芯支撑体侧面,与接箍卡芯支撑体上面平齐,作为油管接箍卡芯滑动支撑体支撑上面的油管接箍卡芯;所述接箍卡芯左支撑体和接箍卡芯右支撑体组合形成内锥体空腔,与卡芯支撑模块形成的锥体相对应;所述接箍卡芯托板与接箍卡芯支撑体连接且齐平,用于支撑油管接箍卡芯。
11.优选的,上述油管接箍卡芯由接箍承托面、喇叭口、行程定位面、导向面、送料电磁铁吸合面、锁销槽和推动电磁铁吸合面组成,所述油管接箍卡芯的接箍承托面下沉,承托油
管接箍,且下沉弧形结构对油管接箍形成自锁,接箍上提,油管接箍卡芯与油管脱开;所述油管接箍卡芯的前部开喇叭口,喇叭口的两侧开锁销槽,喇叭口上面为行程定位面,为油管接箍卡芯进入油管通道;油管接箍卡芯上部为送料电磁铁吸合面,为推动模块的推动电磁铁吸合平面;油管接箍卡芯的两侧为导向面,用于防止油管接箍卡芯转动;油管接箍卡芯的后部为送料电磁铁吸合面,为送料电磁铁吸合平面。
12.优选的,上述锁销模块由支撑板、行程开关、右推杆、电动推杆、定位销轴、转动支撑销轴、左推杆、销轴、锁止板连接、锁止板和套筒组成,所述支撑板通过螺栓连接在接箍卡芯左支撑体上面,左推杆、右推杆和电动推杆组成杠杆结构,电动推杆推动左推杆和右推杆以转动支撑销轴为支点实现开合,进而带动左推杆和右推杆前端锁销卡入锁销槽内;所述电动推杆为左推杆和右推杆开合动力机构,通过销轴与左推杆和右推杆连接;所述锁止板连接安装在支撑板上,通过转动支撑销轴和定位销轴实现在支撑板定位连接;所述锁止板用于承托油管接箍,在油管接箍卡芯处于工作位置时,锁止板处于喇叭口内,与油管接触或接近,实现与油管接箍卡芯其他部分组成油管接箍承托面;所述套筒安装在支撑板和锁止板连接之间,用于调整安装高度;所述行程开关安装在支撑板上,在油管接箍卡芯处于工作位置时,接触油管接箍卡芯的行程定位面停止。
13.优选的,上述导向模块由油管导向套、顶部超声传感器安装座和顶部超声传感器组成,所述油管导向套下部的导向回口为倒锥体结构,安装在接箍卡芯左支撑体上方,引导油管上行至内径最小处的收敛口实现接箍居中,进而引导油管居中;所述油管导向套上部的导向进口为锥体结构,引导油管接箍返回;所述顶部超声传感器安装在顶部超声传感器安装座上。
14.优选的,上述的推动模块包括推动电磁铁、电磁铁连接板、弹簧、弹簧轴、推动支架和直线模组,所述推动电磁铁、电磁铁连接板、弹簧和弹簧轴组成浮动电磁吸合结构,在工作位置吸合油管接箍卡芯,推动油管接箍卡芯在工作位置和待机位置切换;所述浮动电磁吸合结构略高于油管接箍卡芯高度,油管接箍卡芯在浮动电磁吸合结构推动电磁铁通过;推动动力采用直线模组,推动推动电磁铁吸合油管接箍卡芯在工作位置和待机位置切换;所述推动支架是框架结构,安装推动模块的直线模组,与推动面接触并与推动面两端面接触实现位置固定,推动支架通过螺栓连接在壳体外端,整体可移除壳体,以便于调整直线模组自带行程开关以调整推动电磁铁的行程。
15.优选的,上述的送料模块包括导向直线轴承座、导向光轴、薄六角螺母、送进行程开关安装座、送进行程开关、送料盒、送料电磁铁、送料电磁铁安装座、侧安装板、送料液压缸、推动行程开关、推动行程开关安装座、安装基板、推动行程开关调整环和送进液压缸,实现将油管接箍卡芯送入和取出壳体模块;所述送料模块包含两个送料移动机构:一是送进液压缸带动导向光轴进退,进而实现送料盒带动油管接箍卡芯第一级进退;二是送料液压缸通过送料电磁铁带动油管接箍卡芯实现第二级进退;所述导向直线轴承座、导向光轴、薄六角螺母、送料盒、侧安装板、安装基板和送进液压缸组成第一级进退机构;两个所述导向光轴安装在导向直线轴承座内,导向直线轴承座和送进液压缸均安装在侧安装板上,导向光轴前端连接送料盒,送进液压缸带动送料盒沿导向光轴进退;所述导向光轴安装在导向直线轴承座上,前部用两个薄六角螺母固定,防
止螺栓松动;所述送料盒、送料电磁铁、送料电磁铁安装座和送料液压缸组成第二级进退机构,进而实现油管接箍卡芯的第二级进退;所述导向光轴后端安装推动行程开关调整环,用于调整检测送进液压缸送进距离;所述送进行程开关安装在送进行程开关安装座上,在第一级进退机构接触壳体时,送进行程开关接触发出信号进而控制送料模块动作;所述送料模块的导向直线轴承座、送料液压缸和送料电磁铁安装座安装在侧安装板上,侧安装板连接安装基板,安装基板通过螺栓安装在底板上;所述侧安装板和安装基板通过螺栓连接,侧安装板开环形螺栓槽,侧安装板和安装基板高度可调,进而实现油管接箍卡芯高度可调,以利于油管接箍卡芯准确送入壳体的待机位置;所述送料电磁铁安装在送料电磁铁安装座上,吸合油管接箍卡芯;所述送料盒连接送料液压缸液压杆端,送料盒后端连接送进液压缸前端安装座,送进液压缸液压杆连接送料电磁铁,送料电磁铁连接吸合油管接箍卡芯;所述送料电磁铁安装在送料电磁铁安装座上,送料电磁铁安装座连接在送料液压缸的活塞杠上,送料液压缸安装在送料盒后部,送料液压缸进退吸合带动油管接箍卡芯进退,实现油管接箍卡芯无偏转进退。
16.优选的,上述底座模块包括四通连接法兰和底板两部分,四通连接法兰的上侧固定底板,用于安装支撑油管吊卡;所述卡芯支撑模块由下卡芯支撑体、上卡芯支撑体组成,下卡芯支撑体的上部设有上卡芯支撑体。
17.本发明提到的油田小修作业轮转接箍卡芯油管吊卡的作业工艺,包括下油管作业工艺流程和起油管作业工艺流程:其中,下油管作业工艺流程,包括如下过程:(一)首先翻转立式猫道将油管翻转至井口中心上竖直位置,接箍卡芯a处于油管吊卡壳体的接箍卡芯通道内的待机位置,接箍卡芯b承托下油管坐落于卡芯支撑模块上;(二)油管吊卡下移,油管在油管导向套作用下自上而下套入油管,顶部超声传感器感知到油管后,油管吊卡停止前进;(三)plc控制器控制推动模块动作,通过推动电磁铁吸合带动接箍卡芯a由待机位置前进工作位置,直至完全卡住油管杆身,同时锁销模块闭合;(四)油管吊卡上行直至接箍卡芯a承托油管接箍缘面;(五)油管吊卡下行直至油管下端对正下油管,油管上卸扣钳完成油管上扣作业;(六)油管吊卡小幅上行后停止,送料模块将接箍卡芯b取出;(七)油管吊卡下行直至落到卡芯支撑模块上,此时接箍卡芯的锁销模块打开,承托模块打开,接箍卡芯左支撑体和接箍卡芯右支撑体分离直至接箍卡芯可以从接箍卡芯左支撑体和接箍卡芯右支撑体通过,油管吊卡上升,接箍卡芯a留在卡芯支撑模块上,接箍卡芯a承托油管接箍;(八)在进行步骤(七)同时,送料模块将取出的接箍卡芯b送入到油管吊卡壳体的接箍卡芯通道内的待机位置;(九)油管吊卡上行过程,接箍卡芯左支撑体和接箍卡芯右支撑体闭合,油管吊卡进行下一根油管的下放作业;(十)通过接箍卡芯a和接箍卡芯b轮转作业实现油管承托和起升/下降作业,循环进行,达到双接箍卡芯轮转作业实现下油管作业。
18.起油管作业工艺流程,包括如下过程:(一)接箍卡芯a承托油管接箍坐于卡芯支撑模块上面,接箍卡芯b处于油管吊卡壳体的接箍卡芯通道内的待机位置上,处于待机状态;(二)油管吊卡下行,下行过程中接箍卡芯承托模块打开,油管吊卡下行直至卡芯支撑模块(2)上端高于接箍卡芯a的下端位置;(三)承托模块关闭,接箍卡芯左支撑体和接箍卡芯右支撑体闭合,同时接箍卡芯锁销模块闭合;(四)在进行上述步骤(三)的同时,送料模块将处于接箍卡芯通道内的待机位置的接箍卡芯b取出,接箍卡芯b暂存在循环送料模块上,接箍卡芯b处于等待状态;(五)油管吊卡上行直至下油管接箍露出,然后再上行一段距离;(六)送料模块将处于等待状态的接箍卡芯b送入卡芯支撑模块上,直至卡住下油管的管身;(七)油管吊卡下行直至接箍卡芯b卡住油管接箍面后停止下行;(八)翻转立式猫道卡爪上行软夹持住油管杆身,上卸扣动力钳完成卸扣;(九)翻转立式猫道卡爪上行硬夹持住油管杆身,油管吊卡下行小段距离,接箍卡芯锁销模块打开,直线模组通过推动模块的推动电磁铁吸合推动接箍卡芯a到接箍卡芯通道内的待机位置;(十)油管吊卡上行脱开油管后停止,翻转立式猫道将油管送至水平位置;然后油管吊卡下行,去进行下一根油管的起升作业,实现接箍卡芯轮转作业;通过接箍卡芯a和接箍卡芯b轮转作业实现油管承托和起升/下降作业,循环进行,达到双接箍卡芯轮转作业实现起油管作业。
19.与现有技术相比,本发明的有益效果具体如下:本发明的双接箍卡芯轮转作业,不仅实现油管起下作业,而且在工作台上起到油管卡瓦作用,实现传统意义的“一吊一卡”;本发明的双接箍卡芯下沉面与油管接箍接触,实现承托,起到锁定油管接箍作用,提高作业安全性;本发明锁销模块再次锁定接箍卡芯,且锁止板与接箍卡芯等高,起到支撑油管接箍作业,增强对油管接箍支撑能力,进一步提高作业安全性;本发明的双接箍卡芯轮转作业,是承托接箍面,而不是夹持油管管身,避免多种油管卡瓦采用卡瓦牙夹持油管管身对油管带来的伤害;本发明推动模块通过电磁吸合实现接箍卡芯,无需准确定位,且作业高效;本发明接箍卡芯在导向作用下进退,具体在壳体的导向面作用下进退,防止接箍卡芯旋转,确保接箍卡芯的进入锥面正对油管管身,利于接箍卡芯进入后承托油管接箍;本发明接箍卡芯通过推动模块实现承托/脱离油管接箍面,与现有手动油管吊卡类似,提高作业安全性和作业效率。
附图说明
20.图1是本发明的总体主视图;图2是本发明的总体俯视图;图3是本发明的底座模块主视图;图4是本发明的底座模块俯视图;图5是本发明的卡芯支撑模块主视图
图6是本发明的卡芯支撑模块下卡芯支撑体主视图;图7是本发明的卡芯支撑模块下卡芯支撑体俯视图;图8是本发明的壳体模块主视图;图9是本发明的壳体模块壳体主视图;图10是本发明的壳体模块壳体剖视图;图11是本发明的承托模块的结构示意图;图12是本发明的油管接箍卡芯俯视图;图13是本发明的油管接箍卡芯的主视图;图14是本发明的油管接箍卡芯的剖视图;图15是本发明的锁销模块俯视图;图16是本发明的锁销模块主剖视图;图17是本发明的导向模块主视图;图18是本发明的导向模块油管导向套主剖视图;图19是本发明的推动模块主视图;图20是本发明的控制模块俯视图;图21是本发明的送料模块主视图;上图中:底座模块1、卡芯支撑模块2、壳体模块3、承托模块4、油管接箍卡芯5、锁销模块6、导向模块7、控制模块8、推动模块9、送料模块10;四通连接法兰1.1、底板1.2;下卡芯支撑体2.1、上卡芯支撑体2.2;支撑调节螺栓3.1、底部接近开关3.2、超声传感器3.3、底部接近开关安装座3.4、超声传感器安装座3.5、壳体3.6、承托定位块3.7、定位块销轴3.8、吊环槽3.9、吊环槽销3.10、上盖壳3.11;进入锥面3.6.1、支撑面3.6.2、工作面3.6.3、工作导向面3.6.4、推动面3.6.5、导向安装面3.6.6、工作位置3.6.7、待机位置3.6.8;贯通式丝杆步进电机4.1、接箍卡芯左支撑体4.2、接箍卡芯右支撑体4.3、接箍卡芯托板4.4、电机安装板4.5;接箍承托面5.1、喇叭口5.2、行程定位面5.3、导向面5.4、送料电磁铁吸合面5.5、锁销槽5.6、推动电磁铁吸合面5.7;支撑板6.1、行程开关6.2、右推杆6.3、电动推杆6.4、定位销轴6.5、转动支撑销轴6.6、左推杆6.7、销轴6.8、锁止板连接6.9、锁止板6.10、套筒6.11;油管导向套7.1、顶部超声传感器安装座7.2、顶部超声传感器7.3、导向进口7.1.1、电磁铁送料进口7.1.2、安装耳板7.1.3、收敛口7.1.4、导向回口7.1.5;射频器安装座8.1、射频器8.2、动力电源8.3、动力电源箱体8.4、直线模组驱动器8.5、丝杆步进电机驱动器8.6、导轨8.7、plc控制器8.8;推动电磁铁9.1、电磁铁连接板9.2、弹簧9.3、弹簧轴9.4、推动支架9.5、直线模组9.6;导向直线轴承座10.1、导向光轴10.2、薄六角螺母10.3、送进行程开关安装座10.4、送进行程开关10.5、送料盒10.6、送料电磁铁10.7、送料电磁铁安装座10.8、侧安装板
10.9、送料液压缸10.10、推动行程开关10.11、推动行程开关安装座10.12、安装基板10.13、推动行程开关调整环10.14、送进液压缸10.15。
具体实施方式
21.以下结合附图对本发明的优选实施例进行说明,应当理解,此处所描述的优选实施例仅用于说明和解释本发明,并不用于限定本发明。
22.实施例1,参照图1-2,本发明提到的一种油田小修作业轮转接箍卡芯油管吊卡,包括底座模块1、卡芯支撑模块2、壳体模块3、承托模块4、油管接箍卡芯5、锁销模块6、导向模块7、控制模块8、推动模块9、送料模块10,底座模块1的上侧安装壳体模块3,壳体模块3的中部安设卡芯支撑模块2,所述油管接箍卡芯5支撑油管,安装在壳体模块3中部,且在壳体模块3内导槽内滑动,壳体模块3内设置油管接箍卡芯5工作位置3.6.7和待机位置3.6.8;推动模块9位于油管接箍卡芯5上部壳体模块3内,推动电磁铁9.1吸合油管接箍卡芯5,由直线模组9.6推动油管接箍卡芯5实现油管接箍卡芯5在工作位置3.6.7和待机位置3.6.8转换;卡芯支撑模块2和承托模块4在油管接箍卡芯5下部,共同支撑油管接箍卡芯5,其中在起升油管工况时,由承托模块4独立承托油管接箍卡芯5,在停止底板1.2工况时,卡芯支撑模块2支撑油管接箍卡芯5;承托模块4的贯通式丝杆步进电机4.1驱动接箍卡芯左支撑体4.2和接箍卡芯右支撑体4.3实现打开和闭合,闭合工况时,接箍卡芯左支撑体4.2和接箍卡芯右支撑体4.3承托油管接箍卡芯5,打开工况时,油管吊卡上升,油管接箍卡芯5从接箍卡芯左支撑体4.2和接箍卡芯右支撑体4.3中间下落,脱离壳体模块3座于卡芯支撑模块2;导向模块7位于油管接箍卡芯5正上方,油管自下而上进入导向模块7后,油管导向套7.1将油管导入中心作业位置;控制模块8位于壳体模块3上部腔体内,实现油管吊卡驱动和控制;送料模块10安装在底座模块1,位于油管吊卡侧面,将油管接箍卡芯5送入和取出油管吊卡和卡芯支撑模块2。
23.参照图8-10,本发明的壳体模块3包括支撑调节螺栓3.1、底部接近开关3.2、超声传感器3.3、底部接近开关安装座3.4、超声传感器安装座3.5、壳体3.6、承托定位块3.7、定位块销轴3.8、吊环槽3.9、吊环槽销3.10和上盖壳3.11,所述壳体3.6的底部设有支撑调节螺栓3.1、底部接近开关3.2、超声传感器3.3,底部接近开关3.2安装在底部接近开关安装座3.4上,底部接近开关安装座3.4固定在壳体3.6的底部;所述壳体3.6的中间开孔,孔内自下而上依次安装承托模块4、油管接箍卡芯5、推动模块9和锁销模块6,同时也是安装滑动通道;壳体3.6中部竖直方向是油管接箍卡芯5作业区域,下部为锥形空间,安装卡芯支撑模块2,上部为导向模块7,用于实现油管居中;其中,承托定位块3.7是承托模块4的接箍卡芯左支撑体4.2、接箍卡芯右支撑体4.3运动的定位面,定位块销轴3.8实现承托定位块3.7定位;两个吊环槽3.9对称安装在壳体3.6的上部,用于连接修井机大钩的两个吊环,吊环槽3.9外端安装吊环槽销3.10,上盖壳3.11连接在壳体3.6上端,实现壳体模块3封闭。
24.参照图9,本发明的壳体3.6包括进入锥面3.6.1、支撑面3.6.2、工作面3.6.3、工作导向面3.6.4、推动面3.6.5、导向安装面3.6.6、工作位置3.6.7和待机位置3.6.8,其中,进入锥面3.6.1为锥体结构,油管接箍进入导向面;支撑面3.6.2是承托模块4工作面;工作面3.6.3是油管接箍卡芯5移动支撑工作面;工作导向面3.6.4为与油管接箍卡芯5的导向面
5.4接触面,实现油管接箍卡芯5的导向,防止旋转发生;推动面3.6.5是推动模块9的工作面,也是锁销模块6所在安装面;导向安装面3.6.6是用于安装导向模块7,居中安装;工作位置3.6.7和待机位置3.6.8是油管接箍卡芯5两个位置,其中工作位置3.6.7位于油管吊卡竖直轴线中心。
25.参照图11,本发明的承托模块4由贯通式丝杆步进电机4.1、接箍卡芯左支撑体4.2、接箍卡芯右支撑体4.3、接箍卡芯托板4.4和电机安装板4.5组成,所述接箍卡芯左支撑体4.2和接箍卡芯右支撑体4.3组成接箍卡芯支撑体,共同支撑油管接箍卡芯5,所述贯通式丝杆步进电机4.1连接并带动接箍卡芯支撑体在壳体3.6内左右移动,接箍卡芯左支撑体4.2和接箍卡芯右支撑体4.3拼合一体;接箍卡芯托板4.4连接在接箍卡芯支撑体侧面,与接箍卡芯支撑体上面平齐,作为油管接箍卡芯5滑动支撑体支撑上面的油管接箍卡芯5;所述接箍卡芯左支撑体4.2和接箍卡芯右支撑体4.3组合形成内锥体空腔,与卡芯支撑模块2形成的锥体相对应;所述接箍卡芯托板4.4与接箍卡芯支撑体连接且齐平,用于支撑油管接箍卡芯5。
26.参照图12-14,本发明的油管接箍卡芯5由接箍承托面5.1、喇叭口5.2、行程定位面5.3、导向面5.4、送料电磁铁吸合面5.5、锁销槽5.6和推动电磁铁吸合面5.7组成,所述油管接箍卡芯5的接箍承托面5.1下沉,承托油管接箍,且下沉弧形结构对油管接箍形成自锁,接箍上提,油管接箍卡芯5与油管脱开;所述油管接箍卡芯5的前部开喇叭口5.2,喇叭口5.2的两侧开锁销槽5.6,喇叭口5.2上面为行程定位面5.3,为油管接箍卡芯5进入油管通道;油管接箍卡芯5上部为送料电磁铁吸合面5.5,为推动模块9的推动电磁铁9.1吸合平面;油管接箍卡芯5的两侧为导向面5.4,用于防止油管接箍卡芯5转动;油管接箍卡芯5的后部为送料电磁铁吸合面5.5,为送料电磁铁10.7吸合平面。
27.参照图15-16,本发明的锁销模块6由支撑板6.1、行程开关6.2、右推杆6.3、电动推杆6.4、定位销轴6.5、转动支撑销轴6.6、左推杆6.7、销轴6.8、锁止板连接6.9、锁止板6.10和套筒6.11组成,所述支撑板6.1通过螺栓连接在接箍卡芯左支撑体4.2上面,左推杆6.7、右推杆6.3和电动推杆6.4组成杠杆结构,电动推杆6.4推动左推杆6.7和右推杆6.3以转动支撑销轴6.6为支点实现开合,进而带动左推杆6.7和右推杆6.3前端锁销卡入锁销槽5.6内;所述电动推杆6.4为左推杆6.7和右推杆6.3开合动力机构,通过销轴6.8与左推杆6.7和右推杆6.3连接;所述锁止板连接6.9安装在支撑板6.1上,通过转动支撑销轴6.6和定位销轴6.5实现在支撑板6.1定位连接;所述锁止板6.10用于承托油管接箍,在油管接箍卡芯5处于工作位置3.6.7时,锁止板6.10处于喇叭口5.2内,与油管接触或接近,实现与油管接箍卡芯5其他部分组成油管接箍承托面;所述套筒6.11安装在支撑板6.1和锁止板连接6.9之间,用于调整安装高度;所述行程开关6.2安装在支撑板6.1上,在油管接箍卡芯5处于工作位置3.6.7时,接触油管接箍卡芯5的行程定位面5.3停止。
28.参照图17-18,本发明的导向模块7由油管导向套7.1、顶部超声传感器安装座7.2和顶部超声传感器7.3组成,所述油管导向套7.1下部的导向回口7.1.5为倒锥体结构,安装在接箍卡芯左支撑体4.2上方,引导油管上行至内径最小处的收敛口7.1.4实现接箍居中,进而引导油管居中;所述油管导向套7.1上部的导向进口7.1.1为锥体结构,引导油管接箍返回;所述顶部超声传感器7.3安装在顶部超声传感器安装座7.2上;油管导向套7.1的外壁安设安装耳板7.1.3,油管导向套7.1的下侧设有电磁铁送料进口7.1.2。
29.参照图19,本发明的推动模块9包括推动电磁铁9.1、电磁铁连接板9.2、弹簧9.3、弹簧轴9.4、推动支架9.5和直线模组9.6,所述推动电磁铁9.1、电磁铁连接板9.2、弹簧9.3和弹簧轴9.4组成浮动电磁吸合结构,在工作位置3.6.7吸合油管接箍卡芯5,推动油管接箍卡芯5在工作位置3.6.7和待机位置3.6.8切换;所述浮动电磁吸合结构略高于油管接箍卡芯5高度,允许油管接箍卡芯5在浮动电磁吸合结构,允许推动电磁铁9.1通过;推动动力采用直线模组9.6,推动推动电磁铁9.1吸合油管接箍卡芯5在工作位置3.6.7和待机位置3.6.8切换;所述推动支架9.5是框架结构,安装推动模块9的直线模组9.6,与推动面3.6.5接触并与推动面3.6.5两端面接触实现位置固定,推动支架9.5通过螺栓连接在壳体3.6外端,整体可移除壳体3.6,以便于调整直线模组9.6自带行程开关以调整推动电磁铁9.1的行程。
30.参照图20,本发明的控制模块8包括射频器安装座8.1、射频器8.2、动力电源8.3、动力电源箱体8.4、直线模组驱动器8.5、丝杆步进电机驱动器8.6、导轨8.7和plc控制器8.8组成,实现除了送料模块10外的油管吊卡控制;油管吊卡的控制模块8提供主从式控制方式,为本领域技术人员所熟知的现有技术,不再详述;plc控制器8.8通过射频器8.2接受自动化修井装备主控制器,控制除送料模块10外的油管吊卡工作。具体包括:接受各种传感器型号,控制直线模组驱动器8.5、两台丝杆步进电机驱动器8.6、推动电磁铁9.1、送料电磁铁10.7和电动推杆6.4等执行件工作,进而实现油管吊卡整机工作;所述直线模组驱动器8.5驱动直线模组9.6工作;所述丝杆步进电机驱动器8.6驱动贯通式丝杆步进电机4.1工作;所述动力电源8.3安装在动力电源箱体8.4内,为油管吊卡提供电源;所述控制模块8安装在壳体3.6上部壳体内,其中射频器8.2接收天线需要通过斜向下孔伸出壳体3.6,避免电磁屏蔽,斜向下孔防止或减少雨水和灰尘进入。
31.参照图21,本发明的送料模块10包括导向直线轴承座10.1、导向光轴10.2、薄六角螺母10.3、送进行程开关安装座10.4、送进行程开关10.5、送料盒10.6、送料电磁铁10.7、送料电磁铁安装座10.8、侧安装板10.9、送料液压缸10.10、推动行程开关10.11、推动行程开关安装座10.12、安装基板10.13、推动行程开关调整环10.14和送进液压缸10.15,实现将油管接箍卡芯5送入和取出壳体模块3;所述送料模块10包含两个送料移动机构:一是送进液压缸10.15带动导向光轴10.2进退,进而实现送料盒10.6带动油管接箍卡芯5第一级进退;二是送料液压缸10.10通过送料电磁铁10.7带动油管接箍卡芯5实现第二级进退;所述导向直线轴承座10.1、导向光轴10.2、薄六角螺母10.3、送料盒10.6、侧安装板10.9、安装基板10.13和送进液压缸10.15组成第一级进退机构;两个所述导向光轴10.2安装在导向直线轴承座10.1内,导向直线轴承座10.1和送进液压缸10.15均安装在侧安装板10.9上,导向光轴10.2前端连接送料盒10.6,送进液压缸10.15带动送料盒10.6沿导向光轴10.2进退;所述导向光轴10.2安装在导向直线轴承座10.1上,前部用两个薄六角螺母10.3固定,防止螺栓松动;所述送料盒10.6、送料电磁铁10.7、送料电磁铁安装座10.8和送料液压缸10.10组成第二级进退机构,进而实现油管接箍卡芯5的第二级进退;所述导向光轴10.2后端安装推动行程开关调整环10.14,用于调整检测送进液压缸10.15送进距离;所述送进行程开关
10.5安装在送进行程开关安装座10.4上,在第一级进退机构接触壳体3.6时,送进行程开关10.5接触发出信号进而控制送料模块10动作;所述送料模块10的导向直线轴承座10.1、送料液压缸10.10和送料电磁铁安装座10.8安装在侧安装板10.9上,侧安装板10.9连接安装基板10.13,安装基板10.13通过螺栓安装在底板1.2上;所述侧安装板10.9和安装基板10.13通过螺栓连接,侧安装板10.9开环形螺栓槽,侧安装板10.9和安装基板10.13高度可调,进而实现油管接箍卡芯5高度可调,以利于油管接箍卡芯5准确送入壳体3.6的待机位置3.6.8;所述送料电磁铁10.7安装在送料电磁铁安装座10.8上,吸合油管接箍卡芯5;所述送料盒10.6连接送料液压缸10.10液压杆端,送料盒10.6后端连接送进液压缸10.15前端安装座,送进液压缸10.15液压杆连接送料电磁铁10.7,送料电磁铁10.7连接吸合油管接箍卡芯5;所述送料电磁铁10.7安装在送料电磁铁安装座10.8上,送料电磁铁安装座10.8连接在送料液压缸10.10的活塞杠上,送料液压缸10.10安装在送料盒10.6后部,送料液压缸10.10进退吸合带动油管接箍卡芯5进退,实现油管接箍卡芯5无偏转进退。
32.参照图3-4,本发明的底座模块1包括四通连接法兰1.1和底板1.2两部分,四通连接法兰1.1的上侧固定底板1.2,用于安装支撑油管吊卡;参照图6-8,卡芯支撑模块2由下卡芯支撑体2.1、上卡芯支撑体2.2组成,下卡芯支撑体2.1的上部设有上卡芯支撑体2.2。
33.具体作业工艺过程:下面以下油管为例,描述油管吊卡作业工艺流程,为了便于理解工艺流程,设定接箍卡芯a和接箍卡芯b以示区别:一首先翻转立式猫道将油管翻转至井口中心上竖直位置,接箍卡芯a处于油管吊卡壳体3.6的接箍卡芯通道内的待机位置3.6.8,接箍卡芯b承托下油管坐落于卡芯支撑模块2上;二油管吊卡下移,油管在油管导向套7.1作用下自上而下套入油管,顶部超声传感器7.3感知到油管后,油管吊卡停止前进;三plc控制器8.8控制推动模块9动作,通过推动电磁铁9.1吸合带动接箍卡芯a由待机位置3.6.8前进工作位置3.6.7,直至完全卡住油管杆身,同时锁销模块6闭合;四油管吊卡上行直至接箍卡芯a承托油管接箍缘面;五油管吊卡下行直至油管下端对正下油管,油管上卸扣钳完成油管上扣作业;六油管吊卡小幅上行后停止,送料模块10将接箍卡芯b取出;七油管吊卡下行直至落到卡芯支撑模块2上,此时接箍卡芯的锁销模块6打开,承托模块4打开,接箍卡芯左支撑体4.2和接箍卡芯右支撑体4.3分离直至接箍卡芯可以从接箍卡芯左支撑体4.2和接箍卡芯右支撑体4.3通过,油管吊卡上升,接箍卡芯a留在卡芯支撑模块2上,接箍卡芯a承托油管接箍;八在进行步骤七同时,送料模块10将取出的接箍卡芯b送入到油管吊卡壳体3.6的接箍卡芯通道内的待机位置3.6.8;九油管吊卡上行过程,接箍卡芯左支撑体4.2和接箍卡芯右支撑体4.3闭合,油管吊卡进行下一根油管的下放作业;十通过接箍卡芯a和接箍卡芯b轮转作业实现油管承托和起升/下降作业,循环进行,达到双接箍卡芯轮转作业实现下油管作业。
34.下面以起油管为例,描述油管吊卡作业工艺流程:一接箍卡芯a承托油管接箍坐于卡芯支撑模块2上面,接箍卡芯b处于油管吊卡壳体3.6的接箍卡芯通道内的待机位置3.6.8上,处于待机状态;二油管吊卡下行,下行过程中接箍卡芯承托模块4打开,油管吊卡下行直至卡芯支撑模块2上端高于接箍卡芯a的下端位置;三承托模块4关闭,接箍卡芯左支撑体4.2和接箍卡芯右支撑体4.3闭合,同时接箍卡芯锁销模块6闭合;四在进行上述步骤三的同时,送料模块10将处于接箍卡芯通道内的待机位置3.6.8的接箍卡芯b取出,接箍卡芯b暂存在循环送料模块10上,接箍卡芯b处于等待状态;五油管吊卡上行直至下油管接箍露出,然后再上行一段距离;六送料模块10将处于等待状态的接箍卡芯b送入卡芯支撑模块2上,直至卡住下油管的管身;七油管吊卡下行直至接箍卡芯b卡住油管接箍面后停止下行;八翻转立式猫道卡爪上行软夹持住油管杆身,上卸扣动力钳完成卸扣;九翻转立式猫道卡爪上行硬夹持住油管杆身,油管吊卡下行小段距离,接箍卡芯锁销模块6打开,直线模组9.6通过推动模块9的推动电磁铁9.1吸合推动接箍卡芯a到接箍卡芯通道内的待机位置3.6.8;十油管吊卡上行脱开油管后停止,翻转立式猫道将油管送至水平位置;然后油管吊卡下行,去进行下一根油管的起升作业,实现接箍卡芯轮转作业;通过接箍卡芯a和接箍卡芯b轮转作业实现油管承托和起升/下降作业,循环进行,达到双接箍卡芯轮转作业实现起油管作业。
35.本发明接箍卡芯5、导向套等尺寸调整,满足系列化尺寸油管作业需要。
36.本发明主要针对油管自动化作业设计,适用于抽油杆作业。
37.以上所述,仅是本发明的部分较佳实施例,任何熟悉本领域的技术人员均可能利用上述阐述的技术方案加以修改或将其修改为等同的技术方案。因此,依据本发明的技术方案所进行的相应简单修改或等同变换,尽属于本发明要求保护的范围。