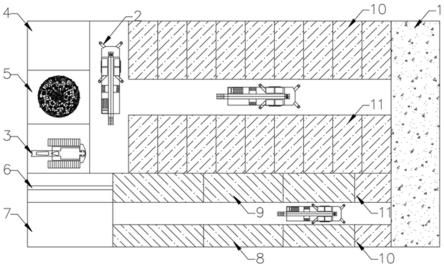
一种洞外狭窄场地tbm快速组装方法
技术领域
1.本发明属于长大隧道tbm施工技术领域,具体涉及一种洞外狭窄场地tbm快速组装方法。
背景技术:2.tbm集机械、电子、液压、技术于一体,技术复杂、结构庞大,集开挖、支护、出渣、通风、排水于一身,是工厂化的隧道生产线。保证洞外组装质量和精度对tbm后期洞内掘进性能、使用寿命乃至维修周期影响重大。tbm成套设备以裸件形式及集装箱形式运输至组装现场。主机部分以裸件抵达,主机附属设备大部分装箱到达,后配套系统大多以裸件运到工地,而其上关键液压,电气部件均装箱到达,将这些不同形式、不同类型的构件按照tbm设计文件精度要求用专用机具组装起来,分别完成主机、桥架、后配套台车及附属设备的组装并用相关部件连接成一体。
3.对于山岭长大隧道一般设置于山岭之间,洞外以桥梁跨越沟壑,长大隧道通常采用tbm施工,经常由于洞外组装场地狭窄,无法满足tbm组装空间需求,从而采取爆破开挖山体移挖做填,从而来满足tbm拼装场地、构件摆放的需求。这种虽然满足了tbm的组装场地的需求及构件的摆放,但是耗费大量人力财力,破坏生态平衡,安全风险高,边坡防护费用高,针对洞口为桥梁的区域,组装完成后需待桥梁施工时要反开挖,增加桥梁成本,施工周期长,针对组装工期要求紧的tbm是不可取的。
4.同时针对山岭长大隧道tbm洞外组装,通常需要至少2台大吨位龙门吊来满足刀盘、桥架、台车等构件的组装及安装,灵活机动性差,安全风险高,大吨位龙门吊需要经过组装、验收、登记等程序准备周期长,同时需要单独配制至少2台大吨位吊车来配合施工,一次性机械设备投入成本高。
技术实现要素:5.本发明提供了一种洞外狭窄场地tbm快速组装方法,重点解决山岭长大隧道步进隧洞洞口tbm场地拼装狭窄导致装机速度慢占用时间长、装机质量控制难、安全风险高、装机成本高、装机秩序控制难、刀盘整体起吊翻转难度大的技术问题。
6.本发明通过下述技术方案实现:一种洞外狭窄场地tbm快速组装方法,包括以下步骤:s1:预备隧洞掘进,洞外组装场地填筑;s2:第1阶段组装、调试、步进;其余台车19按照组装顺序在台车组装区11组装成型;s3:第1+r阶段组装、调试、步进,其中r为不为零的自然数,其中r≥1;s4:整体步进至始发隧洞,掘进。
7.进一步地,步骤s1中还包括以下子步骤:s1.1:组装场地采用预备隧洞洞渣分层回填、分层碾压密实,每层层厚为l,其中l
≤30cm。
8.s1.2:分层回填距设计标高为m后,组装区域、大吨位履带吊及汽车吊活动区域采用钢筋混凝土进行场地硬化,剩余区域采用素混凝土硬化,其中m≤50cm。
9.进一步地,步骤s1中还包括以下子步骤:s1.3:组装场地与隧洞洞口之间设置下凹式刀盘组装区,下凹式刀盘组装区中心处设置步进导向槽,且延伸至隧洞掌子面。
10.进一步地,步骤s1.3中还包括以下子步骤:s1.3.1:待洞外组装场地、下凹式刀盘组装区施工完成后,规划功能区,各功能区的规划依次按照刀盘组装
→
l1区组装
→
l2区桥架组装
→
后配套台车组装进行规划。
11.进一步地,步骤s2.1中还包括以下子步骤:s2.1.1:刀盘分为若干块运输至刀盘组装区,汽车依次吊装若干块刀盘,且将若干块刀盘放置在可调节自由高度的支撑墩顶部,调整刀盘顶面高程后焊接成整体。
12.进一步地,其特征在于,刀盘的组装及安装包括以下步骤:t1:大吨位汽车吊配合大吨位履带吊通过钢丝绳穿过q个吊耳,将刀盘起吊至同一高度h,其中满足q≥4且h>刀盘直径的1/2;t2:移走若干个支撑墩,以大吨位履带吊为主吊机,大吨位汽车吊为辅助吊机,以大吨位汽车吊处的吊耳为向上起吊旋转吊点,大吨位履带吊起吊并收紧钢丝绳、大吨位汽车吊慢速旋转并放松钢丝绳,使得刀盘倾斜最终垂直于地面;t3:大吨位履带吊收紧钢丝绳起吊刀盘,整机转动将刀盘安装至指定位置。
13.进一步地,步骤t1中还包括以下子步骤:t1.1:在刀盘在组装的同时,可借助大吨位汽车吊进行l1区、第1节桥架、第1+n节桥架、第1号台车的组装;t2.2:刀盘及护盾、l1区、第1节及第1+第1+n节桥架、第1号台车组装完成后,整体调试并步进,第1节段组装结束,腾出第1+n节段组装场地,其中满足n≥1。
14.进一步地,在s3步骤中还包括以下子步骤:s3.1:第1阶段组装完成后调试步进的过程中,第1+r阶段组装中的第2号台车、第2+n号台车构件进场后摆放至台车构件摆放区,采用大吨位汽车吊在台车组装区组装成型,第2号台车、第2+n号台车摆放顺序自刀盘组装区至便道方向依次摆放。
15.进一步地,在s3步骤中还包括以下子步骤:s3.2:第1+r阶段组装、调试、步进中采用大吨位汽车吊将在台车组装区依次组装成型的第2号台车、第2+n号台车依次整机起吊安装在第1阶段组装的第1号台车的尾部;s3.3:第2号台车、第2+n号台车依次整机起吊安装在第1阶段组装的第1号台车的尾部后,第1阶段组装与第1+r阶段组装完成后可进行整机调试并向始发隧洞继续步进。
16.本发明与现有技术相比,具有如下的优点和有益效果:1、根据tbm组装顺序,科学规划组装场地,保证装机顺序,避免了大中型二次倒运,缩短装机时间,有效保证了tbm在狭窄的组装场地中有序装机;2、刀盘分块运输至刀盘组装区,精平后焊接完成,大吨位汽车吊配合大吨位履带吊双机抬吊、翻转,安装至指定位置,轻松解决刀盘翻转难的技术问题,操作简单、安全风险低;
3、tbm步进隧洞洞口组装仅采用2台大吨位汽车吊配合1台大吨位履带吊完成装机全过程,其中1台大吨位履带吊仅完成刀盘、机头架等大吨位构件起吊,起吊完成后即可退场,剩余tbm各构件仅采用2台大吨位汽车吊组装完成,相对于传统使用汽车吊配合龙门吊装机灵活机动性高、安全风险低、一次性机械设备投入成本低;4、采用“分段组装、分段调试、分段步进”的组装工艺,在第1阶段组装的同时,可在各规划组装区内进行第1+r阶段的各功能台车的组装,最后逐个整机吊装安装,后一阶段的组装与前一阶段的组装、调试平行作业,装机速度快、占用时间少,同时可保证双主洞钻爆法正常的施工。通过“分段组装、分段调试”发现tbm各功能区所存在的问题,尽可能将其在洞外解决,装机过程中质量有保证。
附图说明
17.此处所说明的附图用来提供对本发明实施例的进一步理解,构成本技术的一部分,并不构成对本发明实施例的限定。在附图中:图1 本发明实施例中洞外tbm组装场地布置图;图2 本发明实施例中tbm刀盘翻转安装示意图;图3 本发明实施例中tbm第n阶段现场组装示意图;图4 本发明实施例中tbm第n+1阶段现场组装示意图;图5 本发明实施例中tbm第n+n阶段现场组装示意图。
18.附图中标记及对应的零部件名称:1-施工便道;2-汽车吊;3-履带吊;4-刀盘各构件存放区;5-刀盘组装区;6-步进导向槽;7-l1区构件存放区;8-桥架构件存放区;9-l2区桥架组装;10-台车构件摆放区;11-台车组装区;12-刀盘;13-护盾;14-撑靴;15-后支撑;16-主梁;17-步进仰拱块;18-桥架;19-台车;20-钢丝绳;21-支撑墩;22-步进隧洞;23-下凹式刀盘组装区;24-吊耳。
具体实施方式
19.为使本发明的目的、技术方案和优点更加清楚明白,下面结合实施例和附图,对本发明作进一步的详细说明,本发明的示意性实施方式及其说明仅用于解释本发明,并不作为对本发明的限定。
20.实施例:如图1至图5所示,本发明包括以下步骤:s1:预备隧洞掘进,洞外组装场地填筑;s2:第1阶段组装、调试、步进;s3:第1+r阶段组装、调试、步进,其中n为不为零的自然数,其中n≥1;s4:整体步进至始发隧洞,掘进。
21.对于山岭长大隧道一般设置于山岭之间,洞外以桥梁跨越沟壑,长大隧道通常采用tbm施工,经常由于洞外组装场地狭窄,无法满足tbm组装空间需求,从而采取爆破开挖山体移挖做填,从而来满足tbm拼装场地、构件摆放的需求。这种虽然满足了tbm的组装场地的需求及构件的摆放,但是耗费大量人力财力,破坏生态平衡,安全风险高,边坡防护费用高,针对洞口为桥梁的区域,组装完成后需待桥梁施工时要反开挖,增加桥梁成本,施工周期
长,针对组装工期要求紧的tbm是不可取的。
22.同时针对山岭长大隧道tbm洞外组装,通常需要至少2台大吨位龙门吊来满足刀盘12、桥架18、台车19等构件的组装及安装,灵活机动性差,安全风险高,大吨位龙门吊需要经过组装、验收、登记等程序准备周期长,同时需要单独配制至少2台大吨位吊车来配合施工,一次性机械设备投入成本高。
23.结合新疆某22.13km级特长隧道,地处高寒高海拔地区,隧道采用“3洞+4竖井”设计方案,采用4座竖井分5段纵向通风,竖井间隔4.4km设置一处,兼顾施工期及运营期正洞的通风作用。中导洞采用敞开式tbm法施工,设计开挖直径8430mm,主机长度约25.0m,整机长度285.0m,主机重量约800t,整机重量约2972.06t,整个刀盘12重量为157.6t,刀盘12分块运输至组装现场焊接成整体,1台大吨位汽车吊2配合1台大吨位履带吊3经过双机抬吊、翻转安装至指定位置。设计步进隧洞22180m,始发隧洞35m,始发隧洞出口端大里程方向150m为阿拉沟大桥0号桥台,为确保桥梁后期施工,始发隧洞洞口填筑140mtbm组装场地,考虑到预备隧洞及始发洞、双主洞的钻爆法正常施工,预留20m施工便道1,因此仅有120m
×
65m(长
×
宽)组装场地。根据现场组装场地的总体规划和施工进度等边界条件限制,tbm采用“分段组装、分段调试、分段步进”的组装工艺,采用220t汽车吊2、75t汽车吊2配合450t履带吊3吊装安装,装机速度快、质量安全可靠。项目自2020年5月29日首批构件到场开始组装,截止至2020年7月14日组装完成,整机组装工期46日。
24.本发明通过tbm组装顺序,科学规划组装场地,保证装机顺序,避免了大中型构件二次倒运,缩短装机时间,有效保证了tbm在狭窄的组装场地中有序装机。
25.刀盘分块运输至刀盘组装区,精平后焊接完成,大吨位汽车吊配合大吨位履带吊双机抬吊、翻转、旋转安装到tbm刀盘设计位置,快速解决刀盘翻转难的技术问题,操作简单、安全风险低。
26.tbm步进隧洞洞口组装仅采用2台大吨位汽车吊配合1台大吨位履带吊完成装机全过程,其中1台大吨位履带吊仅完成刀盘、机头架等大吨位构件起吊,起吊完成后即可退场,剩余tbm各构件仅采用2台大吨位汽车吊组装完成,整个组装过程中机械使用连续,机械利用效率高,相对于传统使用汽车吊配合龙门吊装机灵活机动性高、安全风险低、一次性机械设备投入成本低。
27.采用“分段组装、分段调试、分段步进”的组装工艺,在第1阶段组装的同时,可在各规划组装区内进行第1+r阶段的各功能台车的组装,最后逐个整机吊装安装,后一阶段的组装与前一阶段的组装、调试平行作业,装机速度快、占用时间少,缩短组装工期。通过“分段组装、分段调试”发现各阶段组装中的存在的技术问题,尽可能将其在洞外解决,装机过程中质量有保证。
28.依次按照s2第1阶段组装、调试、步进,再到s3第1+r阶段组装、调试、步进的组装顺序,完成整个tbm洞外组装的施工。
29.需要说明的是,步骤s1中还包括以下子步骤:s1.1:组装场地采用预备隧洞洞渣分层回填、分层碾压密实,每层的层厚为l,其中l≤30cm。
30.s1.2:分层回填距设计标高为m后,组装区域、大吨位履带吊3及汽车吊2活动区域采用钢筋混凝土进行场地硬化,剩余区域采用素混凝土硬化,其中m≤50cm。
31.这里的分层回填距设计标高是指土方回填厚度不大于30cm,土石分层回填不大于40cm,石方分层回填不大于50cm,分层厚度越小,重型压路机碾压完成后压实度越好,填料之间的颗粒越密实,后期的不均匀沉降越小,有利于提高组装区域路堤的整体强度和刚度;整个组装场地长度150m宽度100m包含组装区域,两者处于同一水平高度,组装区域仅供tbm整机组装,剩余区域为大件摆放、履带吊行走等,组装区域和履带吊的活动区域采用钢筋混凝土基础,其余区域采用非钢筋混凝土基础。组装的区域几何尺寸有长度150m宽度8.4m,主要功能是供tbm现场组装,组装区域的中轴线与tbm中轴线、掘进洞的中轴线重合。
32.需要说明的是,步骤s1中还包括以下子步骤:s1.3:组装场地与隧洞洞口之间设置下凹式刀盘组装区23,下凹式刀盘组装区23中心处设置矩形步进导向槽6,且延伸至隧洞掌子面,步进导向槽中心线与掘进隧道中心线重合,且在步进过程中起到步进导向的作用,下凹式刀盘组装区23可消除刀盘底部与l2区及后配套上下之间的垂直高差。
33.需要说明的是,步骤s1.3中还包括以下子步骤:s1.3.1:待洞外组装场地、下凹式刀盘组装区23施工完成后,规划汽车吊2及履带吊3站位及行走轨迹、刀盘12存放区、刀盘组装区5、l1区构件存放区7、桥架构件存放区8、桥架18构件组装区、后配套台车构件摆放区10、后配套台车构件摆放区10等功能区,各功能区的规划依次按照刀盘12组装、l1区组装、l2区桥架组装9、后配套台车19组装进行规划。并且在s2步骤中的第1阶段组装、调试、步进顺序为:刀盘12及护盾13组装、l1区组装、第1节、第1+n节中的l2区桥架组装9、第1号台车19组装,其中本步骤中的n≥1;第1号台车19为主控室(司机室),l1区包含主梁16、机头架、撑靴14装置、后支撑15装置等,所有敞开式tbm都有l1区和l2区,本台tbm的l1区指盾护盾尾部到1号桥架头部的距离,l2区为1号桥架端头至3号桥架尾部,即1号桥架、2号桥架、3号桥架;需要说明的是,步骤s2.1中包括以下步骤:s2.1.1:刀盘12分为若干块运输至刀盘组装区5,刀盘12被分为若干块且运输至刀盘组装区5,汽车吊依次吊装若干块刀盘12,且将若干块刀盘12放置在具备调节自由高度功能的支撑墩21顶部,调整刀盘12顶面高程至同一水平面后焊接成整体,刀盘组装区5设置在紧靠刀盘12安装位置的一侧,且距离不得过远。
34.本发明通过将刀盘12分块运输至刀盘组装区5,精平后进行焊接,焊接完成后,大吨位汽车吊2配合大吨位履带吊3双机抬吊、翻转,安装至指定位置,轻松解决刀盘12翻转难的技术问题,操作简单、安全风险低。
35.需要说明的是,其特征在于,刀盘12的组装及安装包括以下步骤:t1:大吨位汽车吊2配合大吨位履带吊3通过钢丝绳20穿过q个吊耳24,将刀盘12起吊至同一高度h,其中满足q≥4且h>刀盘12直径的1/2;t2:移走若干个支撑墩21,以大吨位履带吊3为主吊机,大吨位汽车吊2为辅助吊机,以大吨位汽车吊2处的吊耳24为向上起吊旋转吊点,大吨位履带吊3起吊并收紧钢丝绳20、大吨位汽车吊2慢速旋转并放松钢丝绳20,使得刀盘12倾斜最终垂直于地面;t3:大吨位履带吊3收紧钢丝绳20起吊刀盘12,整机转动将刀盘12安装至指定位置。
36.tbm步进隧洞22洞口组装仅采用2台大吨位汽车吊2配合1台大吨位履带吊3完成装机全过程,其中1台大吨位履带吊3仅完成刀盘12、机头架等大吨位构件起吊,起吊完成后即可退场,剩余tbm各构件仅采用2台大吨位汽车吊2组装完成,相对于传统使用汽车吊2配合龙门吊装机灵活机动性高、安全风险低、一次性机械设备投入成本低。
37.进一步地,步骤t1中还包括以下子步骤:t1.1:在刀盘12在组装的同时,可借助大吨位汽车吊2进行l1区、第1节桥架18、第1+n节桥架18、第1号台车19的组装;t2.2:刀盘12及护盾13、l1区、第1节及第1+第1+n节桥架18、第1号台车19组装完成后,整体调试并步进,第1节段组装结束,腾出第1+n节段组装场地,其中满足n≥1。
38.需要说明的是,步进的过程中同时在下凹式刀盘组装区23安装步进仰拱块17。
39.需要说明的是,在s3步骤中还包括以下子步骤:s3.1:第1阶段组装完成后调试步进的过程中,第1+r阶段组装中的第2号台车19、第2+n号台车19构件进场后摆放至台车构件摆放区10,采用大吨位汽车吊2在台车组装区11组装成型,第2号台车19、第2+n号台车19摆放顺序自刀盘组装区5至便道方向依次摆放。
40.需要说明的是,在s3步骤中还包括以下子步骤:s3.2:待第1阶段步进腾出第1+n节段台车19组装空间后,采用大吨位汽车吊2将在台车组装区11组装成型的第2号台车19起吊安装在第1号台车19尾部,并进行第1+r阶段调试、步进,腾出第2+n节段台车19组装空间,其中满足n≥1、r≥1;s3.3:同理,第2号台车10、2+n号台车19依次整机起吊安装在第1+r阶段组装的第2号台车19、第2+n号台车的尾部后,同时进行第1+r阶段调试,其中满足n≥1、r≥1;s3.4:待第2+n号台车19组装完成后,进行整机调试并向始发隧洞继续步进。
41.采用“分段组装、分段调试、分段步进”的组装工艺,在第1阶段组装的同时,可在各规划组装区内进行第1+r阶段的各功能台车19的组装,最后逐个整机吊装安装,后一阶段的组装与前一阶段的组装、调试平行作业,装机速度快、占用时间少,同时可保证双主洞钻爆法正常的施工。通过“分段组装、分段调试”发现tbm各功能区所存在的问题,尽可能将其在洞外解决,装机过程中质量有保证。
42.需要说明的是,在 s3步骤中的第1+r阶段组装、调试、步进中采用大吨位汽车吊2将在台车组装区11依次组装成型的第2号台车19、第2+n号台车19依次整机起吊安装在第1阶段组装的第1号台车19的尾部。
43.需要说明的是,所述第2号台车19、第2+n号台车19依次整机起吊安装在第1阶段组装的第1号台车19的尾部后,第1阶段组装与第1+r阶段组装完成后可进行整机调试并向始发隧洞继续步进。
44.需要说明的是,所述步进的过程中同步安装步进仰拱块17。
45.需要说明的是,所述整机步进至始发隧道掌子面开始掘进。
46.现有技术中有的采用1台2
×
100t龙门吊和1台70t汽车吊进行组装,龙门吊机动灵活性差、安装及施工工期长、一次进出场费用高,一次设备投入成本高,在组装的过程中容易造成设备的闲置,龙门吊使用效率较低;而本技术刀盘的组装采用“双机抬吊”,即刀盘起吊、翻转、旋转均采用1台汽车吊配合1台履带吊完成,轻松解决刀盘翻转难的技术问题,刀盘组装时间短,施工速度快、操作简单、安全风险低,灵活机动性强;并且本技术科学合理规
划大型构件存放区、组装区、主机组装区,设置下凹式刀盘组装区,消除刀盘底部与l2和后配套之间的高差,同时步进过程中同步安装步进段仰拱块,达到安全、快速组装、快速步进的目标。
47.现有技术中有的场地比较狭窄,长度仅仅为140m,宽度为20m,不能合理规划组装区、台车存放区,而且后配套台车组装采取平行作业模式,却是在另外一个场地渣场组装成型,再将组装成型的后配套运输到组装场地上整体安装,增加了后配套台车的倒运成本和费用;而本技术后配套1号至1+n节台车进场后在场地内指定区域存放,在tbm刀盘至第1节台车(司机室)组装的同时,采用汽车吊从构件存放区吊装至组装区组装成型按照顺序堆放。
48.以上所述的具体实施方式,对本发明的目的、技术方案和有益效果进行了进一步详细说明,所应理解的是,以上所述仅为本发明的具体实施方式而已,并不用于限定本发明的保护范围,凡在本发明的精神和原则之内,所做的任何修改、等同替换、改进等,均应包含在本发明的保护范围之内。