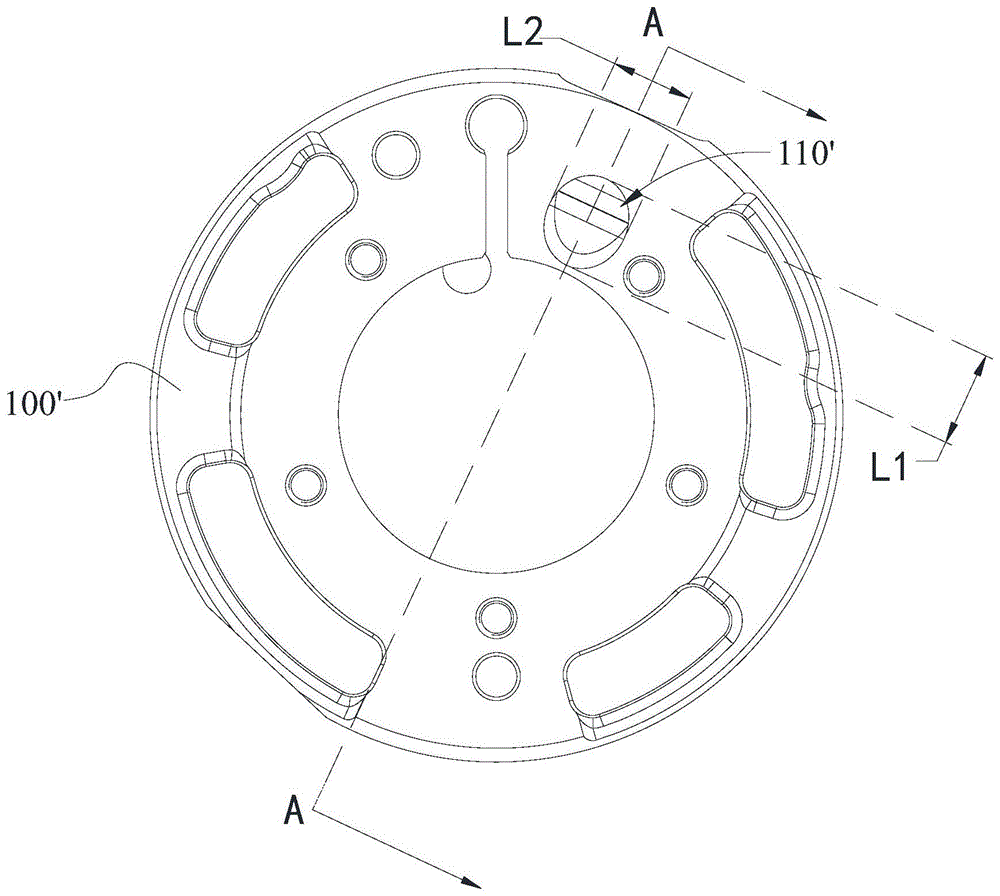
本发明属于压缩机
技术领域:
,尤其涉及一种旋转式双缸空压机构以及双缸单吸气压缩机。
背景技术:
:相关技术中,双缸单吸气压缩机,具有两个气缸,一般两个气缸上均设计吸气孔,同时储液器上也有两个吸气管,分别与两个气缸连通。为降低成本,可通过减少吸气孔的方式来降低成本,并将吸气孔设置在中隔板上。但,众所周知在双缸双吸气的结构中,中隔板的厚度远小于气缸厚度,因此,如果将吸气孔设置在中隔板上,那么就必须将中隔板加厚。这样一来一方面成本方面下降空间有限,更为重要的是整个压缩结构的高度将会加高,这种变化会使压缩结构的可靠性恶化。因此,为了改善上述情况,如图1、图2,可将双缸单吸气的吸气孔101'设在气缸100'上,具体地,在双缸单吸气结构中,两气缸分别为第一气缸和第二气缸,且第一气缸100'开设连通至吸气孔101'的进气孔102'。这样避免了加厚中隔板,从而很好的解决了上述问题。与此同时,通向第二气缸的孔为出气孔103'。通常情况下,在装配过程中,储液器通过锥形管与压缩机构进行连接。密封锥形管插入吸气孔101'的深度最低要求为c,对于第一气缸而言,由于出气孔103'的设置,使得锥形管插入吸气孔101'的深度减小,那么锥形管于进气孔处插接可靠性降低,锥形管于吸气孔101'处易松动,导致气体易泄露;同时,气缸在周向上的机械强度不足。技术实现要素:本发明的目的在于克服上述现有技术的不足,提供了一种旋转式双缸空压机构,其旨在解决双缸单吸气压缩机中与储液器连通的气缸进气口处连接可靠性差以及气缸在周向上的机械强度不足的问题。本发明是这样实现的:一种旋转式双缸空压机构,包括沿第一方向依次设置的第一气缸、中隔板和第二气缸,第一气缸开设第一压缩腔,第一气缸于其外周开设有沿第二方向开设的吸气孔,第一压缩腔于其腔壁开设有沿第二方向开设并与吸气孔连通的进气孔,第一气缸于与中隔板相贴合的侧面开设连通至进气孔的出气孔,在垂直于第一方向的截面上,出气孔在第二方向的孔长小于出气孔在垂直于第二方向上的孔长,中隔板开设贯通设置的导气孔,第二气缸开设有第二压缩腔,导气孔用于将出气孔连通至第二压缩腔,第二方向与第一方向垂直。可选地,出气孔在第二方向的孔长与出气孔在垂直于第二方向上的孔长之比为1.1-1.4。可选地,出气孔的开设方向为第三方向,起点为出气孔中心点并沿第三方向布置且背离中隔板方向设置的直线为第一直线,起点为出气孔中心点并沿第二方向布置且背离第一压缩腔设置的直线为第二直线,第一直线与第二直线之间形成的角度为锐角。可选地,沿第三方向布置且背离中隔板方向设置的直线与沿第二方向布置且背离第一压缩腔设置的直线之间形成的角度为25-45°。可选地,出气孔的孔形为椭圆形;或出气孔为由两相对设置且平行的直线段以及连接于两直线段的两端部之间的弧线段构成的跑道形,两直线段的间距小于两弧线段的最大间距。可选地,导气孔为沿第一方向贯通设置的通孔结构。可选地,导气孔的轴线在第一气缸指向第二气缸的方向由中隔板的周边向中心倾斜。可选地,第二气缸开设有斜通孔,斜通孔的一端连通导气孔,另一端连通第二压缩腔,斜通孔的轴线与导气孔的轴线平行;或者,斜通孔的轴线与第二气缸的轴线的夹角大于导气孔的轴线与第二气缸的轴线的夹角。可选地,第一压缩腔为沿第一方向贯通设置的通孔结构;第二压缩腔为沿第一方向贯通设置的通孔结构。本发明还提供一种双缸单吸气压缩机,包括上述的旋转式双缸空压机构。该旋转式双缸空压机构将双缸单吸气的吸气孔设在气缸上,避免了加厚中隔板,与此同时,出气孔在第二方向的孔长小于出气孔在垂直于第二方向上的孔长,在与现有技术出气孔的孔形面积相同的情况下,能够增加n+t的尺寸,在具体设置,相对现有技术的结构,能够确保n≥c的同时,还能确保t≥d/10,其中,确保n≥c,能够提高锥形管于进气孔处插接可靠性,防止锥形管于进气孔处松动,从而避免压缩气体泄露,而确保t≥d/10,则确保了第一气缸在周向上的机械强度。由上可知,该结构简单,并未增加制造成本,与此同时,还增加了该旋转式双缸空压机构中能够提高进气管于吸气孔处插接可靠性以避免压缩气体泄露,以及确保了第一气缸在周向上的机械强度。附图说明为了更清楚地说明本发明实施例中的技术方案,下面将对实施例中所需要使用的附图作简单地介绍,显而易见地,下面描述中的附图仅仅是本发明的一些实施例,对于本领域普通技术人员来讲,在不付出创造性劳动的前提下,还可以根据这些附图获得其他的附图。图1是现有技术中旋转式双缸空压机构中一开有吸气孔的气缸仰视图;图2是图1中aa方向剖视图;图3是本发明提供的旋转式双缸空压机构的一种实施例的剖视图;图4是本发明提供的旋转式双缸空压机构的另一种实施例中第一气缸的仰视图;图5是图4中bb方向的剖视图。附图1、2标号说明:标号名称标号名称100'气缸101'吸气孔102'进气孔103'出气孔附图2至图5标号说明:标号名称标号名称100第一气缸110第一压缩腔101吸气孔102进气孔103出气孔200中隔板201导气孔300第二气缸310第二压缩腔320斜通孔具体实施方式为了使本发明的目的、技术方案及优点更加清楚明白,以下结合附图及实施例,对本发明进行进一步详细说明。应当理解,此处所描述的具体实施例仅用以解释本发明,并不用于限定本发明。本发明实施例提供一种旋转式双缸空压机构。请参阅图3至图4,该旋转式双缸空压机构包括沿第一方向依次设置的第一气缸100、中隔板200和第二气缸300。在此需要说明的是,双缸空压泵体在具体使用过程中,还包括其他与本申请发明点无关的结构部件,如第一轴承、与第一轴承配合的第一曲轴、与第一曲轴连接并位于第一气缸100内的第一活塞、第二轴承、与第二轴承配合的第二曲轴以及与第二曲轴连接并位于第二气缸300内的第二活塞,等等,在此不一一罗列,且附图中并未示出这些结构。在此需要说明的是,第一方向可是从上往下方向,此时,第一气缸100、中隔板200和第二气缸300是从上往下依次设置,此时,该双缸空压泵体为立式,第一方向也可是从左往右方向,第一气缸100、中隔板200和第二气缸300从左往右依次设置,此时,该双缸空压泵体为卧式。第一气缸100开设第一压缩腔110,第一气缸100于其外周开设有沿第二方向开设的吸气孔101,该吸气孔101用于供连通储液器的进气管插入,以使经储液器的气体能够经吸气孔101进入到旋转式双缸空压机构。第一压缩腔110于其腔壁开设有沿第二方向开设并与吸气孔101连通的进气孔102,第一气缸100于与中隔板200相贴合的侧面开设连通至进气孔102的出气孔103,这样,于吸气孔101处吸入的气体分别流向进气孔102和出气孔103,其中,流向进气孔102的气体将进入到第一压缩腔110,流向出气孔103的气体将进入第二气缸300。其中,第二方向与第一方向垂直。在垂直于第一方向的截面上,出气孔103在第二方向的孔长小于出气孔103在垂直于第二方向上的孔长,具体请参阅图2,现有技术中,该出气孔103'在第一气缸100'端面的形状为椭圆形,l1为该椭圆的长轴长度,l2为该椭圆的短轴长度。如果l1过大,则无法保证n≥c,则导致第一气缸与外部进气管的连接强度不足;或者无法保证t≥d/10,第一气缸100在周向上的机械强度不足;或者二者均不能满足要求。其中,c为密封锥形管插入吸气孔101'的深度最低要求,n为吸气孔101'到第一气缸100'外壁面最近的距离,t为吸气孔101'到第一气缸100'内壁面最近的距离,d为进气孔102'的孔径。基于本实施例的出气孔103结构的设置,在与现有技术出气孔103'的孔形面积相同的情况下,能够增加n+t的尺寸,在具体设置,相对现有技术的结构,能够在确保n≥c的同时,还能确保t≥d/10,其中,确保n≥c,能够提高进气管于吸气孔101处插接可靠性,防止进气管于吸气孔101处松动,从而避免压缩气体泄露,而确保t≥d/10,则确保了第一气缸100在周向上的机械强度。中隔板200在第一方向上开设贯通设置的导气孔201,第二气缸300开设有第二压缩腔310,导气孔201用于将出气孔103连通至第二压缩腔310,这样,流向出气孔103的气体将经导气孔201进入到第二压缩腔310。在此需要说明的是,c为密封锥形管插入吸气孔101的深度最低要求,n为出气孔103到第一气缸100外壁面最近的距离,t为出气孔103到第一气缸100内壁面最近的距离,d为进气孔102的孔径。该旋转式双缸空压机构将双缸单吸气的吸气孔101设在气缸上,避免了加厚中隔板200,与此同时,出气孔103在第二方向的孔长小于出气孔103在垂直于第二方向上的孔长,在与现有技术出气孔103’的孔形面积相同的情况下,能够增加n+t的尺寸,在具体设置,相对现有技术的结构,能够确保n≥c的同时,还能确保t≥d/10,其中,确保n≥c,能够提高锥形管于进气孔102处插接可靠性,防止锥形管于进气孔102处松动,从而避免压缩气体泄露,而确保t≥d/10,则确保了第一气缸100在周向上的机械强度。由上可知,该结构简单,并未增加制造成本,与此同时,还增加了该旋转式双缸空压机构中能够提高进气管于吸气孔101处插接可靠性以避免压缩气体泄露,以及确保了第一气缸100在周向上的机械强度。优选地,出气孔103在第二方向的孔长与出气孔103在垂直于第二方向上的孔长之比为1.1-1.4。请参阅图5,在本发明一个实施例中,提供一种旋转式双缸空压机构,出气孔103的开设方向为第三方向,起点为出气孔中心点并沿第三方向布置且背离中隔板200方向设置的直线为第一直线,起点为出气孔中心点并沿第二方向布置且背离第一压缩腔110设置的直线为第二直线,第一直线与第二直线之间形成的角度为锐角,即出气孔103与吸气孔101不垂直。这样,减少了流向出气孔103的气体的转向角度,从而避免了减少气体于出气孔103处流速的下降,即降低了流速损失,从而有利于保证该旋转式双缸空压机构的压缩效率,提高该旋转式双缸空压机构的压缩能效。进一步地,出气孔103的开设方向为第三方向,沿第三方向布置且背离中隔板200方向设置的直线与沿第二方向布置且背离第一压缩腔110设置的直线之间形成的角度为为25-45°。在本发明一个实施例中,提供一种旋转式双缸空压机构,出气孔103的孔壁为光滑壁面,出气孔103的孔壁不存在拐角结构,避免了气流在流经出气孔103减损流速。请参阅图4,在本发明一个实施例中,提供一种旋转式双缸空压机构,出气孔103的孔形为椭圆形。在本发明一个实施例中,提供一种旋转式双缸空压机构,出气孔103为由两相对设置且平行的直线段以及连接于两直线段的两端部之间的弧线段构成的跑道形,两直线段的间距小于两弧线段的最大间距。在本发明一个实施例中,提供一种旋转式双缸空压机构,导气孔201为沿第一方向贯通设置的通孔结构,在实际生产过程中,有利于简化中隔板200生产制造难度,从而有利于降低生产制造成本。进一步地,导气孔301的轴线在第一气缸100指向第二气缸300的方向由中隔板200的周边向中心倾斜,以减小气流的流动损失。在本发明一个实施例中,提供一种旋转式双缸空压机构,第二气缸300开设有斜通孔320,斜通孔320的一端连通导气孔201,另一端连通第二压缩腔310,斜通孔320的轴线与导气孔201的轴线平行,即斜通孔320与导气孔201不垂直,以减小气流的流动损失,提高压缩能效比。在本发明一个实施例中,提供一种旋转式双缸空压机构,斜通孔320的轴线与第二气缸300的轴线的夹角大于导气孔的轴线与第二气缸300的轴线的夹角,即斜通孔与导气孔201不垂直,以减小气流的流动损失,提高压缩能效比。在本发明一个实施例中,提供一种旋转式双缸空压机构,第一压缩腔110为沿第一方向贯通设置的通孔结构,在实际生产过程中,有利于简化第一气缸100生产制造难度,从而有利于降低生产制造成本在本发明一个实施例中,提供一种旋转式双缸空压机构,第二压缩腔310为沿第一方向贯通设置的通孔结构,在实际生产过程中,有利于简化第二气缸300生产制造难度,从而有利于降低生产制造成本在本发明一个实施例中,提高一种双缸单吸气压缩机,该双缸单吸气压缩机构包括旋转式双缸空压机构,该旋转式双缸空压机构的具体结构参照上述实施例,由于本旋转式双缸空压机构采用了上述所有实施例的全部技术方案,因此同样具有上述实施例的技术方案所带来的所有有益效果,在此不再一一赘述。在本发明实施中,第一气缸100和第二气缸300的内经均为d,双缸单吸气压缩机的外经为d0,d/d0≥0.42。在本发明实施例中,出气孔103在第二方向的孔长与出气孔103在垂直于第二方向上的孔长之比为1.1-1.4。以上仅为本发明的较佳实施例而已,并不用以限制本发明,凡在本发明的精神和原则之内所作的任何修改、等同替换或改进等,均应包含在本发明的保护范围之内。当前第1页1 2 3