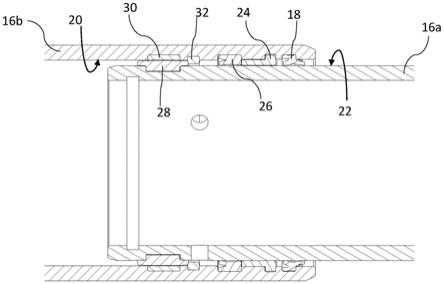
[0001]
本发明涉及伸缩缸和包括该伸缩缸的翻斗卡车。
背景技术:[0002]
伸缩缸通常包括多个直径逐渐减小的管,这些管相互嵌套,并且可伸展且可缩回。对于伸缩缸的有效运行而言很重要的是,在伸展或缩回过程中,每个管都应与其他管对齐。
技术实现要素:[0003]
根据第一方面,提供了一种伸缩缸,其包括:外管;内管,其至少部分地设置在外管内,并且可以沿着一行程在内管完全缩回到外管内的行程的起点与内管完全从外管伸出的行程的终点之间在外管内纵向位移;引导环,其设置在外管的内表面的凹部中,并构造成与内管的外表面接触,以在整个行程中使内管与外管对准;设置在内管的外表面的凹部中的滑动件以及设置在外管的内表面的凹部中的耐磨带,其中,滑动件和耐磨带构造成当内管处于行程的终点处时彼此接触,以在行程的终点处使内管对准在外管内。
[0004]
耐磨带可以包括纤维增强复合材料。耐磨带可以被预加应力,使得其被偏压以将其固定在外管的内表面的凹部中。
[0005]
滑动件可以包括斜切部。耐磨带可包括斜切部。
[0006]
根据第二方面,提供了一种翻斗卡车,其包括翻斗卡车本体,该翻斗卡车本体可致动以通过根据第一方面的伸缩缸的伸展或缩回而绕枢转轴线枢转。
附图说明
[0007]
现在将参考附图仅以举例的方式描述本发明的实施方式,其中:
[0008]
图1示意性地示出了翻斗卡车的透视图;以及
[0009]
图2示意性地示出了伸缩缸的相邻阶梯部的剖视图。
具体实施方式
[0010]
图1示出了翻斗卡车1,有时称为倾倒卡车,其包括牵引车2和拖车4。拖车4具有拖车底盘或车架6,并且翻斗主体8可枢转地安装在该拖车底盘或车架上。翻斗主体8围绕定位在车架6的后方处的横向轴线10可枢转地安装在车架6上,即后方翻斗。
[0011]
在其他实施例中,翻斗主体可以围绕沿着底盘的侧方定位的纵向轴线可枢转地安装,即侧方翻斗。翻斗主体8呈具有敞开顶部的长方体容器的形式。翻斗主体8的后方面板(或门)12在其上边缘处铰接并且可以被锁定和解锁,从而使得其可以被打开以允许翻斗主体8的内容物被清空。设置有伸缩液压缸14,其在下端处可枢转地附接到底盘6的中间,并且在上端处可枢转地附接到翻斗主体8的底部。在其他实施例中,筒的上端可以附接到翻斗主体的其他部分,诸如前方或侧方,并且筒的下端可附接到底盘的其他部分,诸如朝向前方或朝向后方。
[0012]
伸缩缸14包括在底盘6的前方与翻斗主体8的前方之间纵向伸展的多个管阶梯部16。在该实施例中,存在四个管阶梯部16,其直径从底盘6的前方向翻斗主体8的前方逐渐减小。因此,管阶梯部16构造成在完全缩回位置时彼此嵌套。伸缩缸14可以伸展(如图1所示)以使翻斗主体8围绕轴线10枢转到完全翻倒位置,在该完全翻倒位置中,在后方面板12被解锁的情况下,翻斗主体8内的任何载荷被清空到地面上。伸缩缸14也可以缩回至完全缩回位置以使翻斗主体8枢转回到静止位置,在该静止位置中,翻斗主体8被放置在底盘6上。
[0013]
在典型的伸缩缸中,从每个管阶梯部到下一个相邻管阶梯部的过渡部包括内管(直径较小)和外管(直径较大)。
[0014]
为了使典型的伸缩缸能够在伸出或缩回时准确而可靠地运动,内管与外管之间的径向间隙应做得尽可能小,尤其是在最大伸展时。在先前考虑的布置中,这是通过将外管的内表面加工成高尺寸公差来完成的。但是,这是复杂且昂贵的过程。此外,外管必须接下来被制造成具有较厚的壁,以便能够机加工掉内表面。
[0015]
图2示出了本发明的液压缸14的一部分的截面图,该液压缸包括两个相邻的管阶梯部16,一个管阶梯部16的直径小于另一个管阶梯部16的直径。在此将具有较小直径的管阶梯部称为内管16a,并且在此将具有较大直径的管阶梯部称为外管16b。
[0016]
在该实施例中,内管16a和外管16b由钢制成。在其他实施例中,内管和外管可以由任何合适的材料制成。内管16a至少部分地设置在外管16b内并且与外管16b同心。
[0017]
内管16a在外管16b内沿纵向方向(即平行于内管16a和外管16b的纵向方向)可位移。内管16a在行程的起点与行程的终点之间沿着行程可运动,内管16a在该行程的起点中完全缩回在外管16b内,内管16a在该行程的终点中完全伸出外管16b。图2示出了在行程的终点处的内管16a。
[0018]
外管16b在管的一端处包括擦拭件18,内管16a从该擦拭件伸展。擦拭件18是环形的,并且设置在外管的内表面20的凹部中。擦拭件18构造成接触内管16a的外表面22,以便在内管16a沿着行程运动时擦拭内管16a的外表面22。这确保了污物在内管16a缩回到外管16b之前被从该内管去除。
[0019]
外管16b在外管16b内包括与擦拭件18相邻的引导环24。引导环24是环形的,并且设置在外管16b的内表面20的凹部中。引导环24构造成在内管16a的整个行程中接触内管16a的外表面22。引导环24构造成在外管16b内引导内管16a,以确保内管16a沿着行程在外管16b内正确对准。
[0020]
外管16b还包括环形密封件26,该环形密封件设置在外管16b的内表面20中的与引导环24相邻的凹部中。密封件26构造成将管16的内腔与外部环境流体密封,从而使得伸缩缸14内的加压液压流体无法从伸缩缸14逸出。
[0021]
内管16a包括环形滑动件28,该环形滑动件设置在内管16a的外表面22中的凹部中、在内管16a的被接收在外管16b内的端部中。
[0022]
外管16b还包括止动环32,该止动环设置在外管16b的内表面20中的与密封件26相邻的凹部内。止动环32是环形的,并且构造成用作滑动件28的止动件,以防止内管16a从外管16b进一步伸展。因此,滑动件28与止动环32的接触指示行程的终点。在其他实施例中,止动环可以构造成用作内管上的另一止动部件的止动件,从而使得当止动部件与止动环接触时,内管可以替代地位于行程的终点处。
[0023]
外管16b还包括设置在外管16b的内表面20中的凹部中的环形耐磨带。耐磨带30定位成使得其在内管16a处于行程的终点处时(即,当滑动件28与止动环32接触或非常接近与止动环32接触时)与滑动件28相对。耐磨带30和滑动件28构造成当内管16a处于或紧邻行程的终点处时彼此接触,以便使内管16a在行程的终点处或非常接近终点处对准在外管16b内。使内管16a对准在外管16b内涉及使内管16a的纵向轴线相对于外管16b的纵向轴线的偏移最小化。理想地,内管16a的纵向轴线平行于外管16b的纵向轴线。
[0024]
如上所述,以前考虑过的系统需要对外管的整个内表面进行加工,以便使滑动件能够在行程的终点处准确地对准内管,并且使滑动件能够沿着行程的其余部分在外管内不受阻碍地运动。
[0025]
然而,具有如上所述的耐磨带30和配合的滑动件28可以允许更加经济有效地制造外管16b。特别地,可以不需要或减少需要对外管16b的内表面20的加工。可以精确地加工用于接收耐磨带30的凹部,并且因此,高精度的具有已知厚度的耐磨带30可以在行程的终点处与滑动件28相对,其间的径向间隙很小,从而使内管16a的纵向轴线相对于外管16b的纵向轴线的偏转最小化。
[0026]
具有如上所述的配合的耐磨带30和滑动件28还允许制造具有较薄壁的外管16b。较薄壁确保滑动件28不会沿着行程受到外管16b的阻碍,而无需加工外管16b的内表面20。尽管这将导致滑动件28与外管16b的内表面20之间的径向间隙更大,但这不会影响在行程的终点处内管16a对准在外管16b内,因为滑动件28与耐磨带30接触。
[0027]
申请人已经发现,在具有8个带有未加工的内表面20的管阶梯部16的伸缩缸中,与没有耐磨带的类似伸缩缸相比,对于具有耐磨带30的完全伸展的伸缩缸14而言,管阶梯部16的偏转减小了约26%。
[0028]
本申请还发现,与不具有耐磨带的伸缩缸相比,具有仅2个管阶梯部16的较小的伸缩缸14还导致对于具有耐磨带30的伸缩缸14而言偏转减小了约8%。2个管阶梯部与8个管阶梯部的伸缩缸之间的改进中的差异可以通过存在更少的管阶梯部来解释(即,对于具有更多管阶梯部16的伸缩管而言,后一个管阶梯部16的偏转中的减小将会更高,因为每对管阶梯部之间存在额外的偏转)。
[0029]
该实施例中的耐磨带30包括纺织纤维增强的聚酯树脂。在其他实施例中,耐磨带可以包括任何合适的材料,诸如玻璃纤维复合材料、碳纤维复合材料、黄铜或任何合适的塑料。在该实施例中,耐磨带30和滑动件28包括斜切的边缘,以使滑动件28在耐磨带30上的运动平稳。在其他实施例中,仅滑动件可以包括斜切部,或者仅耐磨带可以包括斜切部,以便使滑动件在耐磨带上的运动平稳。在进一步的实施例中,耐磨带和滑动件可以均不包括斜切部。
[0030]
在该实施例中,耐磨带30被预加应力,从而使得其被偏压以迫使耐磨带30径向向外进入到外管16b中的凹部中。因此,预加应力的耐磨带30构造成将其自身固定在凹部中。在其他实施例中,可以利用合适的粘合剂或通过另一合适的固定工艺将耐磨带粘附到凹部中。
[0031]
具有如上所述的预加应力的耐磨带30允许耐磨带30如上所述将其自身固定在外管16b的凹部内,从而使得不需要粘合剂。这意味着耐磨带30与滑动件28之间的径向间隙可以被更加精确地预测,因为将不必考虑粘合剂层。这样,可以使滑动件28与耐磨带30之间的
径向间隙最小化。
[0032]
应当理解,本发明不限于上述实施方式,并且在不脱离本文描述的概念的情况下可以进行各种修改和改进。除相互排斥的地方外,任何特征均可单独使用或与任何其他特征组合使用,并且本发明扩展至并包括本文所述一个或多个特征的所有组合和子组合。