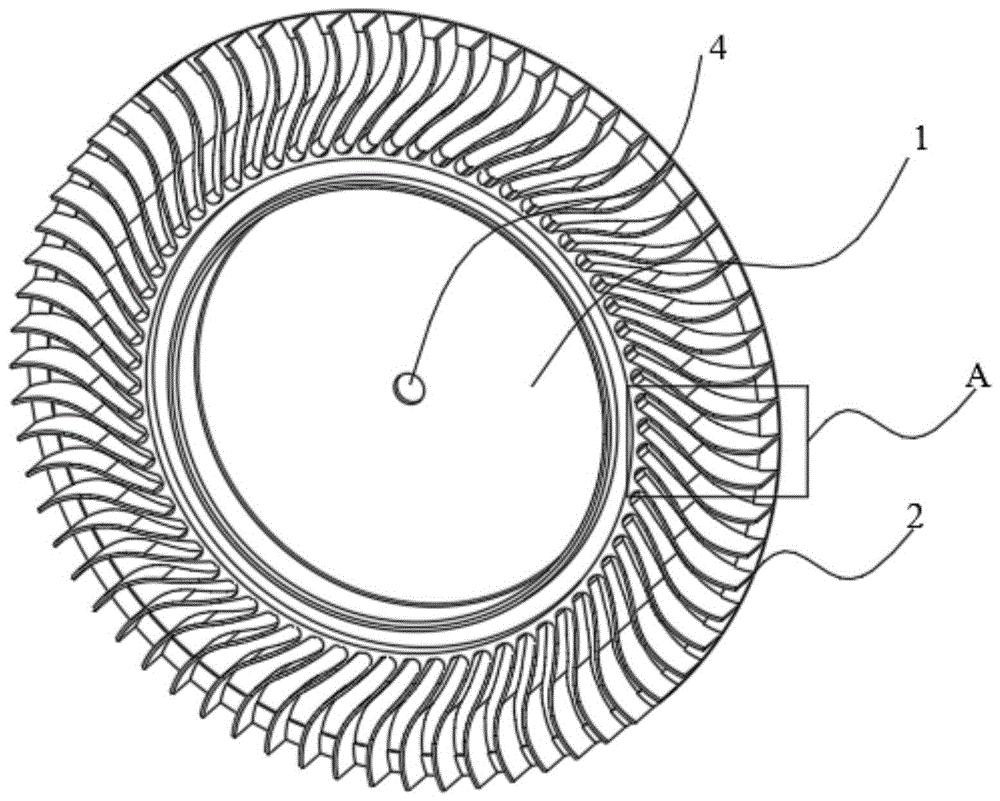
本实用新型属于散热风扇
技术领域:
,特别是涉及一种散热风扇扇叶。
背景技术:
:近年来随着电子产业的发展,电子装置的性能不断提升,其内部芯片组的数量和运算速度不断提升,使得电子装置所散发的热量也相应增加,如果不及时将这些热源散发出去,将极大影响电子装置的性能,甚至将电子装置烧毁。因此,散热元件是电子装置的重要部件之一。散热元件中的扇叶是其核心组件,现有技术的扇叶或采用塑料成型,或采用金属材料冲压成型,塑料成型的扇叶易受到撞击或挤压而损坏,而金属材质冲压成型的扇叶需要通过点焊的方式将各个叶片焊固在轮毂上,由于点焊会造成每一叶片位置及角度的误差,容易导致各叶片引导的气流紊乱或产生风阻效应,进而使制造出的扇叶运行不稳定,冷热冲击后易于形变,对于转动件不利于晃度及动平衡。技术实现要素:本实用新型主要解决的技术问题是提供一种散热风扇扇叶,运行产生的风量大,且运行稳定性高、噪音小,具备耐高温、抗腐蚀、防震动等特性,能够适用于制造笔记本电脑、手机、无人机等小型行动装置中的散热风扇扇叶。为解决上述技术问题,本实用新型采用的一个技术方案是:一种散热风扇扇叶,包括轮毂、位于所述轮毂外围的若干叶片和外连接环,所述外连接环与所述叶片远离所述轮毂的一端固定连接,所述轮毂的中心具有一轴孔;所述轮毂、所述叶片和所述外连接环三者为一体成型,所述轮毂、所述叶片和所述外连接环三者皆为非高分子聚合材料;所述叶片由至少两个弧面段相切连接而成,靠近所述轮毂的一段为叶根弧面段,靠近所述外连接环的一段为叶末弧面段,所述叶根弧面段由所述轮毂的外围向外延伸形成,所述叶根弧面段的延伸方向与所述扇叶的旋转方向相反,所述叶末弧面段的延伸方向与所述扇叶的旋转方向相同。进一步地说,所述叶末弧面段的叶面宽度大于所述叶根弧面段的叶面宽度。进一步地说,所述叶根弧面段的叶面宽度为0.3mm~3.0cm,所述叶末弧面段的叶面宽度为0.4mm~4.0cm。进一步地说,相邻所述叶片之间具有具有连接段。进一步地说,所述叶片的厚度为0.05mm~4.0cm,所述叶片的总长度为3mm~15cm。进一步地说,所述扇叶的直径为5mm~30cm。本实用新型的有益效果至少具有以下几点:1、本实用新型的轮毂、叶片和外连接环皆为非高分子聚合材料,且三者一体成型,具有较佳的结构强度,鼓风扇运转时不会产生微振;2、本实用新型的扇叶,叶片的厚度能够达0.05mm~4.0cm,且结构强度好,其运转时能够保持平衡,不会出现轴向跳动的现象,鼓风扇运转时达到无噪声的效果;3、本实用新型的扇叶,运行时产生的风量大,具备耐高温、抗腐蚀、防震动等特性,能够适用于制造笔记本电脑、手机、无人机等小型行动装置中的散热风扇扇叶。4、本实用新型采用的原料是不锈钢、镁合金或陶土等非高分子聚合材料,相较于塑料材质的产品,本实用新型制成的产品绿色环保,易自然降解,且回收可利用率高。附图说明图1是本实用新型的整体结构示意图之一;图2是图1的A部放大示意图;图3是本实用新型的整体结构示意图之二;图4是图3的B部放大示意图;图5是本实用新型的整体结构示意图之三;附图中各部分标记如下:轮毂1、叶片2、叶根弧面段21、叶末弧面段22、外连接环3、轴孔4、叶根弧面段的叶面宽度W1、叶末弧面段的叶面宽度W2、直径D1、叶片的厚度B3、叶片的总长度L1和扇叶的直径D2。具体实施方式下面结合附图对本实用新型的较佳实施例进行详细阐述,以使本实用新型的优点和特征能更易于被本领域技术人员理解,从而对本实用新型的保护范围做出更为清楚明确的界定。实施例:一种散热风扇扇叶,如图1-图5所示,包括轮毂1、位于所述轮毂外围的若干叶片2和外连接环3,所述外连接环与所述叶片远离所述轮毂的一端固定连接,所述轮毂的中心具有一轴孔4;所述轮毂、所述叶片和所述外连接环三者为一体成型,所述轮毂、所述叶片和所述外连接环三者皆为非高分子聚合材料;所述非高分子聚合材料为不锈钢、镁合金或陶土。所述叶片由至少两个弧面段相切连接而成,靠近所述轮毂的一段为叶根弧面段,靠近所述外连接环的一段为叶末弧面段,所述叶根弧面段由所述轮毂的外围向外延伸形成,所述叶根弧面段的延伸方向与所述扇叶的旋转方向相反,所述叶末弧面段的延伸方向与所述扇叶的旋转方向相同。所述叶末弧面段的叶面宽度大于所述叶根弧面段的叶面宽度。所述叶根弧面段的叶面宽度W1为0.3mm~3.0cm,所述叶末弧面段的叶面宽度W2为0.4mm~4.0cm。相邻所述叶片之间具有连接段,该连接段可以是圆弧连接段或平面连接段。本实施例中该连接段是圆弧连接段,所述圆弧连接段的截面是直径D1为>0.1mm的半圆。所述叶片的厚度B3为0.05mm~4.0cm,所述叶片的总长度L1为3mm~15cm。所述扇叶的直径D2为5mm~30cm。实施例1-实施例4皆是直径为50.4mm,叶片数量为41个,整体高度为2mm的扇叶,但是实施例1-实施例4的扇叶的材质及结构不同,且叶片厚度也不同,具体阐述如下:实施例1的扇叶为PPE(聚苯撑醚)材质,叶片的厚度为0.7mm。实施例2的扇叶为PPE(聚苯撑醚)材质,叶片的厚度为0.5mm。实施例3的扇叶为LCP(液晶聚合物)材质,叶片的厚度为0.3mm,叶片远离轮毂的一端固定连接有外连结环。实施例4的扇叶为非高分子聚合材料射出形成,叶片的厚度为0.15mm,叶片远离轮毂的一端固定连接有外连结环,轮毂的厚度为0.5mm。对实施例1-实施例4中的扇叶进行风量值、气压值和噪音值进行检测,检测结果如下表1:表1:由表1的数值可知,当叶片厚度从0.7mm减少到0.15mm时,风量值增加20.4%,气压值增加8.9%;虽然噪音值有所增加,但是噪音值只增加1.6%,区别不大。表2为塑料材质与非高分子聚合材质的扇叶的轴承温度进行比较(环境温度为23℃)表2:材质轴承温度塑料材质扇叶72.7℃非高分子聚合材质扇叶65.1℃由表2的数值可知,非高分子聚合材质的扇叶的轴承温度比塑料材质的扇叶的轴承温度降低7.6℃。采用压力机对不同材质的扇叶的叶片进行下压,测其内应力值(kgf),结果如表3所示:表3:由表3可知,采用压力机对叶片进行下压,非高分子聚合材质的扇叶产生的内应力远远大于塑料材质的扇叶产生的内应力,具有较佳的强度。以上所述仅为本实用新型的实施例,并非因此限制本实用新型的专利范围,凡是利用本实用新型说明书及附图内容所作的等效结构变换,或直接或间接运用在其他相关的
技术领域:
,均同理包括在本实用新型的专利保护范围内。当前第1页1 2 3