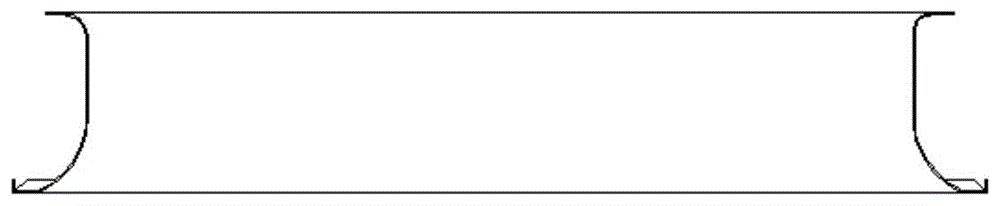
本发明涉及风机设备领域,特别是涉及一种导流圈装置及轴流风机。
背景技术:
:导流圈多用于空调外机,是使用轴流风叶的空调外机风道中的重要部件之一,导流圈装置一般设置在轴流风机安装顶板上,呈上小下大结构,如图1所示,下端有弧度的口为进风口,现有技术中对于导流圈设置的弧度、高度缺乏细化研究,大多依据现场经验,对于不同弧度、高度、角度对于轴流风机性能的影响缺乏理论支撑。技术实现要素:本发明的目的在于解决现有技术中导流圈的集流效果无法达到理想状态的技术问题,本发明提供了一种导流圈装置及轴流风机。本发明通过以下技术方案来实现上述目的:本申请提出了一种导流圈装置,设置在轴流风机的安装顶板上,包括:出风口圆弧段,上边沿呈外扩状;喉部段;以及进风口圆弧段,下边沿呈外扩状,与所述安装顶板固定连接;所述喉部段位于出风口圆弧段和进风口圆弧段之间,喉部段上端与出风口圆弧段相切连接,喉部段下端与进风口圆弧段相切连接。进一步地,所述喉部段向导流圈中心倾斜。进一步地,沿所述喉部段下端点做垂线,喉部段与所做垂线的夹角为γ,喉部段的长度为a,喉部段向导流圈中心倾斜的最大宽度为a*sinγ。进一步地,所述出风口圆弧段上顶点与喉部段上端点的连线与喉部段夹角为α,20°≤α≤45°+γ。进一步地,所述出风口圆弧段的半径ra:0.05d≤ra≤0.08d,其中d为轴流风机风叶轮的直径。进一步地,所述进风口圆弧段依次包括第一圆弧b段、第二圆弧c段以及第三圆弧d段,第一圆弧b段上端与所述喉部段下端相切连接,第二圆弧c段上方与第一圆弧b段下端平滑连接,第二圆弧c段下方与所述安装顶板倒圆角形成第三圆弧d段,第三圆弧d段向内形成内凹槽;所述第二圆弧c段下端延长线与所述安装顶板相切。进一步地,所述第一圆弧b段的半径rb:0.2d≤rb≤0.3d,其中d为轴流风机风叶轮的直径;所述第二圆弧c段的半径rc:rb/5≤rc≤rb/3;所述第三圆弧d段的半径rd:0.02c≤rd≤0.05c,其中c为所述导流圈装置的高度,150mm≤c≤300mm。进一步地,所述第三圆弧d段的圆心与所述第二圆弧c段的圆心的水平距离为rd+b,其中0.5rc≤b≤3rc/5。进一步地,所述出风口圆弧段边缘处设置有用于安装网罩和支架的安装平台。本申请还提出了一种轴流风机,包括风叶轮和安装顶板,还包括导流圈装置,所述风叶轮的直径最大段位置对准所述导流圈装置喉部段上端点设置;所述导流圈装置位于所述喉部段上端点处的直径为:d+2*δ-2*(a*sinγ),其中d为轴流风机风叶轮的直径,δ为风叶轮的间隙,a为喉部段的高度,γ为喉部段与所述喉部段下端与进风口圆弧段的切点处垂线f的夹角。与现有技术相比,本发明的有益效果如下:(1)包括出风口圆弧段、喉部段以及进风口圆弧段的导流圈结构能很好的发挥类似集流器的效果,减少其损失系数,改善进风流场。(2)喉部段向导流圈中心倾斜,一般导流筒中部都是直的,没有斜度,本申请在考虑风叶轮和导流圈间隙的时候,发现喉部段设置一个小的斜度,在实际测试中能显著提高风机的性能。(3)风口圆弧段边缘处设置有用于安装网罩和支架的安装平台,安装平台的设置能减少网罩和支架安装时对出风口弧段的破坏,保证了网罩和支架安装的贴合度。(4)出风口圆弧段的半径ra:0.05d≤ra≤0.08d,其中d为轴流风机风叶轮直径,这个范围内的圆弧度对轴流风机出风流场有很大的改善,能提高轴流风机静压效率,降低出风动能,对于出风口安装条件差的场合,有很好的效果,减少出风的助力,有效的降低对风机的寿命影响。附图说明图1是现有导流圈的截面示意图;图2是实施例一导流圈装置安装在安装顶板上的示意图;图3是图2导流圈装置的截面图;图4是图3的截面尺寸图;图5是实施例二的轴流风机示意图。具体实施方式下面结合附图对本发明作进一步说明:实施例一:一种导流圈装置100,用于轴流风机,设置在轴流风机安装顶板200表面,如图2-4所示,依次包括:出风口圆弧段110、喉部段120以及进风口圆弧段130。出风口圆弧段110上边沿呈外扩状,进风口圆弧段130下边沿呈外扩状,与安装顶板200固定连接,出风口圆弧段110和进风口圆弧段130之间通过喉部段120连接,喉部段120上端与出风口圆弧段110相切连接,喉部段120下端与进风口圆弧段130相切连接。出风口圆弧段110边缘处设置有用于安装网罩和支架的安装平台111,安装平台111的设置能减少网罩和支架安装时对出风口弧段的破坏,保证了网罩和支架安装的贴合度。出风口圆弧段110的半径ra:0.05d≤ra≤0.08d,其中d为轴流风机风叶轮直径,这个范围内的圆弧度对轴流风机出风流场有很大的改善,能提高轴流风机静压效率,降低出风动能,对于出风口安装条件差的场合,有很好的效果,减少出风的助力,有效的降低对风机的寿命影响。进风口圆弧段130依次包括第一圆弧b段、第二圆弧c段以及第三圆弧d段,第一圆弧b段上端与喉部段120下端相切连接,第二圆弧c段上方与第一圆弧b段下端平滑连接,第二圆弧c段下方与安装顶板200表面倒圆角形成第三圆弧d段,第三圆弧d段向内形成内凹槽,该凹槽能使安装面平整,保证风筒圆度,其中第二圆弧c段下端延长线与安装顶板20表面0相切。第一圆弧b段的半径rb:0.2d≤rb≤0.3d,其中d为轴流风机风叶轮直径。第二圆弧c段的半径rc:rb/5≤rc≤rb/3,第二圆弧c段是为了考虑导流圈的整体高度和扩大第一圆弧b段的进风面积而设置的。第三圆弧d段的半径rd:0.02c<=rd<=0.05c,其中c为导流圈装置的高度,150mm≤c≤300mm。根据以上参数设置的导流圈装置,能很好的发挥类似集流器的效果,减少其损失系数,改善进风流场。第三圆弧d段的圆心与第二圆弧c段的圆心的水平距离为rd+b,其中0.5rc≤b≤3rc/5。所述喉部段120向导流圈中心倾斜,一般导流筒中部都是直的,没有斜度,本申请在考虑风叶轮和导流圈间隙的时候,发现喉部段120设置一个小的斜度,在实际测试中能显著提高风机的性能。具体地,沿喉部段120下端点做垂线,喉部段120与所做垂线的夹角为γ;喉部段120的长度为a,喉部段120向内倾斜的最大宽度为a*sinγ,且0≤a*sinγ≤2mm。同时从剖面图上可见,出风口圆弧段110上顶点与喉部段120上端点的连线与喉部段120夹角为α:其中,20°≤α≤45°+γ。实施例二:一种轴流风机,如图5所示,包括风叶轮300和安装顶板200,还包括导流圈装置100,导流圈装置100设置在安装顶板200上。其中风叶轮300在安装时,风叶轮直径最大段位置k对准导流圈装置喉部段120上端点m设置。轴流风机风叶轮在运转中,叶片不可避免要变形,将风叶轮的直径最大段位置对准喉部上端点设置,这样风叶轮在运转中即减少了叶顶间隙,能有效防止风叶轮和导流筒在工况中的擦边问题。导流圈装置位于喉部段120上端点处的最小直径为:d+2*δ-2*(a*sinγ),其中d为轴流风机风叶轮的直径,δ为风叶轮的间隙,a为喉部段120的高度,γ为喉部段120与所述喉部段120下端与进风口圆弧段130的切点处垂线f的夹角。作为一种优选方案,选择直径d为950mm的风叶轮,rb选择为0.25d=237.5mm,rc=0.6rb=142.5mm,b=0.7rc=99.75mm,喉部段120向内倾斜的最大宽度为1.5mm,风叶轮的设计间隙为6mm,导流圈装置位于所述喉部段120上端点处的最小直径为959mm,导流圈装置的高度c设置为200mm。进行测试后发现,与采用普通导流圈的轴流风机相比,采用本申请改进后的轴流风机每个工况的的风量都提高,最大提高了300m^3/h,每个工况的功率基本都降低,最大降低幅度为87w,同时离出风口1米处噪音降低了3.5分贝。表(1)示出了采用本申请导流圈的d950风机(1#风机)和采用普通导流圈的d950风机(2#风机)进行测试的数据对比,可见,在同样工况条件下,采用本申请导流圈的d950风机(1#风机)的风机内压力、轴功率相对于采用普通导流圈的d950风机(2#风机)均有所下降,出风量高于采用普通导流圈的d950风机(2#风机)。表1采用本申请导流圈的d950风机(1#风机)和采用普通导流圈的d950风机(2#风机)进行测试的数据对比(1表(2)出了采用本申请导流圈的d950风机(1#风机)和采用普通导流圈的d950风机(2#风机)在同一工况条件下,沿4个方向的噪音对比,可见,在同样工况条件下,采用本申请导流圈的d950风机(1#风机)的风机噪音相对于采用普通导流圈的d950风机(2#风机)均有所下降。表2采用本申请导流圈的d950风机(1#风机)和采用普通导流圈的d950风机(2#风机)进行测试的数据对比(2)噪音1噪音2噪音3噪音42#风机68.268.167.367.91#风机64.9↓65↓63.9↓64.3↓以上显示和描述了本发明的基本原理、主要特征和优点。本行业的技术人员应该了解,本发明不受上述实施例的限制,上述实施例和说明书中描述的只是说明本发明的原理,在不脱离本发明精神和范围的前提下,本发明还会有各种变化和改进,这些变化和改进都落入要求保护的本发明范围内。当前第1页12