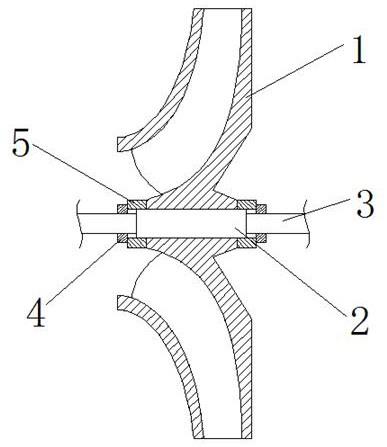
[0001]
本发明涉及离心泵技术领域,尤其涉及一种耐磨高强度离心泵叶轮。
背景技术:[0002]
离心泵是指靠叶轮旋转时产生的离心力来输送液体的一种叶片泵,依靠旋转的叶轮在旋转过程中,由于叶片和液体的相互作用,叶片将机械能传给液体,使液体的压力能增加,达到输送液体的目的。离心泵有立式、卧式、单级、多级、单吸、双吸、自吸式等多种类型。广泛应用于适用于工业和城市给排水、能源、冶金、化工、纺织、造纸、石油、电力、造纸、食品制药和合成纤维等部门。
[0003]
目前,现有的离心泵结构常规单一,离心泵叶轮的耐磨强度一般,安全隐患较大。
技术实现要素:[0004]
为解决上述问题,本发明公开了一种耐磨高强度离心泵叶轮,有效提高离心泵叶轮整体的耐磨强度。
[0005]
具体方案如下:一种耐磨高强度离心泵叶轮,其特征在于:包括叶轮主体,所述叶轮主体的中部设有方形孔,所述方形孔中固定安装有与其相适配的滑套,所述滑套的中部沿其中轴线方向设有圆形通孔,所述圆形通孔中穿插有传动轴,所述传动轴为水平设置的圆杆状结构,所述传动轴的左右两段外侧分别设有第一外螺纹和第二外螺纹,所述第一外螺纹和第二外螺纹的螺旋方向相反,所述叶轮主体的两侧对称设有限位组件,所述限位组件包括与传动轴螺纹连接的限位环,所述限位环与叶轮主体之间设有卡套,所述卡套套设在传动轴外。
[0006]
进一步的,所述滑套的左右两端均伸出方形孔的左右两端,所述卡套的中部通孔与滑套的外形相适配。
[0007]
进一步的,所述叶轮主体的制造工艺为:第一步,将al置于真空炉坩埚底部,然后向真空炉坩埚内添加mg、zn、si、cu、fe;接着将真空炉坩埚抽内真空度0.8mpa,进行高温精炼;之后降温冷却出坩埚,浇注成合金锭;将得到的合金锭进行固溶处理,接着进行时效处理,之后备用;第二步,将合金锭进行淬火;然后进行第一次冷轧和退火,在第一次冷轧变形量达50%后,进行第二次冷轧和退火,在冷轧变形量再达到70%后,获得离心泵叶轮铸件。
[0008]
进一步的,所述获得离心泵叶轮铸件继续进行热等静压处理,然后进行自然冷却至室温;之后再利用金属机械加工设备,对离心泵叶轮外形、尺寸等进一步精确加工,得到成品离心泵叶轮。
[0009]
进一步的,检验得到的成品离心泵叶轮表面有无明显结疤、裂纹和渣沟,内部无明显缩孔、疏松等缺陷,对不合格的重新加工,检验合格的为成品,入库。
[0010]
本发明的有益效果在于:结构独特新颖,可有效提高离心泵叶轮整体的耐磨强度,并方便在传动轴上调节离心泵叶轮的横向位置。
附图说明
[0011]
图1为本发明一种耐磨高强度离心泵叶轮的结构示意图。
[0012]
附图标记列表:1-叶轮主体,2-滑套,3-传动轴,4-限位环,5-卡套。
具体实施方式
[0013]
下面结合附图和具体实施方式,进一步阐明本发明,应理解下述具体实施方式仅用于说明本发明而不用于限制本发明的范围。
[0014]
如图所示,一种耐磨高强度离心泵叶轮,包括叶轮主体1,所述叶轮主体1的中部设有方形孔,所述方形孔中固定安装有与其相适配的滑套2,所述滑套2的中部沿其中轴线方向设有圆形通孔,所述圆形通孔中穿插有传动轴3,所述传动轴3为水平设置的圆杆状结构,所述传动轴3的左右两段外侧分别设有第一外螺纹和第二外螺纹,所述第一外螺纹和第二外螺纹的螺旋方向相反,所述叶轮主体1的两侧对称设有限位组件,所述限位组件包括与传动轴3螺纹连接的限位环4,所述限位环4与叶轮主体1之间设有卡套5,所述卡套5套设在传动轴3外。
[0015]
在本实施例中,所述滑套2的左右两端均伸出方形孔的左右两端,所述卡套5的中部通孔与滑套2的外形相适配。
[0016]
在本实施例中,叶轮主体1的制造工艺为:第一步,将al置于真空炉坩埚底部,然后向真空炉坩埚内添加mg、zn、si、cu、fe;接着将真空炉坩埚抽内真空度0.8mpa,进行高温精炼;之后降温冷却出坩埚,浇注成合金锭;将得到的合金锭进行固溶处理,接着进行时效处理,之后备用;第二步,将合金锭进行淬火;然后进行第一次冷轧和退火,在第一次冷轧变形量达50%后,进行第二次冷轧和退火,在冷轧变形量再达到70%后,获得离心泵叶轮铸件。
[0017]
在本实施例中,所述获得离心泵叶轮铸件继续进行热等静压处理,然后进行自然冷却至室温;之后再利用金属机械加工设备,对离心泵叶轮外形、尺寸等进一步精确加工,得到成品离心泵叶轮。
[0018]
在本实施例中,检验得到的成品离心泵叶轮表面有无明显结疤、裂纹和渣沟,内部无明显缩孔、疏松等缺陷,对不合格的重新加工,检验合格的为成品,入库。
[0019]
本发明方案所公开的技术手段不仅限于上述实施方式所公开的技术手段,还包括由以上技术特征任意组合所组成的技术方案。