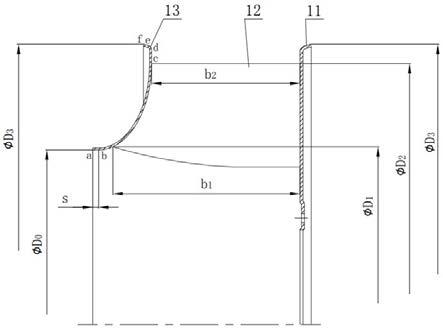
[0001]
本发明涉及通风机技术领域,特别涉及一种离心叶轮,本发明还涉及包括上述离心叶轮的通风机。
背景技术:[0002]
离心叶轮主要包括后盘、前盘 及设置于其间的若干叶片,其中前盘的内孔为叶轮入口。前盘的基本形式有平直前盘、锥形前盘和弧形前盘。前盘截面形状对叶片流道内的流动状态影响较大,进而对通风机性能有显著的影响,效率较高的叶轮多采用弧形前盘(通常采用圆弧形)。一般地说,前盘内侧前端的半径r应尽可能大一些,以便减弱叶轮入口气流转弯时的分离及其损失。但是,前盘前端的半径扩大后会造成叶轮体积的增大,增大成本,使用场合也会受限,因此,在尽可能有限的范围内,改进叶轮前盘的长度和弧线形状,使其相比现有的圆弧形叶轮前盘更能适应离心叶轮的气流特征,使气流转弯顺畅、流场尽可能趋于稳定从而减少气体的旋涡和分离。
[0003]
技术实现要素:[0004]
离心叶轮的气流特征为,在叶轮进口一侧,主体气流从轴向进入叶轮后,其流动包括了两个大转弯:一个是从轴向转为径向的90
°
转弯、一个是因叶轮旋转叶片对气体的作用而形成的圆周方向的弯转,即前盘内径附近气流通常是不均匀的,容易产生气流分离,导致叶轮内的流场进一步恶化,从而影响叶轮对气体做功的效率,进而降低通风机压力和增加功耗。因而,通常尽量将前盘内径处的弧线转弯半径设计得大一些,使气流转弯顺畅、流场尽可能趋于稳定从而减少气体的旋涡和分离。
[0005]
另一方面,在叶轮内部,叶片之间的每一个流体通道由相邻两叶片、前盘和后盘包围而成:在叶片型线已经确定的情况下,前盘的形状就决定了每一个直径下的叶片通道的轴向宽度和通流面积,对叶片流道内的流动状态形成显著的影响,通常情况下希望叶片通道内形成均匀减速的流动,从而在叶片外径处的末端使气流以较低的速度排出叶轮,对于离心叶轮而言,从叶轮内径到叶轮外径的叶片通道的宽度为逐步增大,为了形成等速或减速流道,前盘设计为向后盘倾斜,即随直径的增大,叶片的宽度逐步减小
----
叶片出口宽度b
2
小于叶片进口宽度b
1
。
[0006]
基于以上叶轮内部的气流流动特征,本发明主要通过设计改善叶轮的进口段和内部主体段两部分的结构,来减少气流在叶轮进口处轴向转为径向,以及因叶轮旋转对气体造成的圆周方向的弯转,造成的旋涡和分离。本发明在目前广泛使用的圆弧形截面形状前盘的基础上,通过优化前盘的截面弧线形状,进一步优化叶轮进口处和叶轮叶道内的气体流动状态,以提高叶轮对气体做功的效率进而提高叶轮及通风机的气动性能和效率。
[0007]
本发明通过以下技术方案来实现上述目的:一种离心叶轮,所述叶轮包括前盘、后盘以及均匀夹设在所述前盘和后盘之间的多个
叶片,相邻叶片以及前盘、后盘围成的空间为叶轮内的气流通道,气流从所述前盘轴向进入叶轮,通过叶片之间的流道后,从叶轮外周流出,所述前盘从气流进口到出口,依次包括平直进口段、主体弧形段、平直出口段、出口翻边段,所述平直进口段为直筒状,平直出口段为为圆环状,所述主体弧形段的进口端与所述平直进口段相切连接,所述主体弧形段的出口端与所述平直出口段相切连接,前盘内孔直径为d
0
,其平直出口段的内径为d
2
。进一步的,所述主体弧形段的母线在直角坐标中满足以下方程: + =1,u为所述主体弧形段的径向宽度,v为所述主体弧形段的轴向高度,过所述主体弧形段出口端作叶轮的轴向平行线得到直角坐标的x轴,过所述主体弧形段进口端作叶轮的径向平行线得到直角坐标的y轴,x轴和y轴的交点为直角坐标的原点o,其中,x、y满足:0≤x≤v,-u≤y≤0。
[0008]
进一步的,连接所述主体弧形段的进口端和出口端得到的直线,该直线与所述叶轮的径向中心线之间的夹角为θ=30
°
~40
°
, u=0.5
×
(d
2
~d
0
),v=u
×
tgθ,原点o至后盘内侧平面的水平距离为“b
2
+v”,原点o至叶轮中心线的垂直距离为“0.5
×
d
2”。
[0009]
进一步的,所述主体弧形段的轴向高度与所述主体弧形段的径向宽度之比为0.6~0.8。
[0010]
进一步的,所述平直进口段的轴向长度为s满足:s=(0.01~0.02)
×
d
2
,其中d
2
为叶片的外径。
[0011]
一种通风机,包括离心叶轮和进风口,所述叶轮套设在所述所述进风口外,所述叶轮和所述进风口轴向重叠长度为t
1
满足: t
1
=(0.01~0.02)
×
d
2
。
[0012]
与现有技术相比,本发明的有益效果如下:本发明的前盘主体弧形段,既照顾到气体刚进入叶轮后的转弯需要前盘转弯处半径尽量大,又照顾到叶片之间通道面积的逐步从小到大的过渡,使得气体从流向叶片前端到进入叶轮之后的流动均有一定程度的明显改善,从而提高了叶轮的做功效率和性能参数。
[0013]
本发明主要通过在叶轮前盘增加了平直进口段,改善了由于气流进入叶轮时从轴向转为径向时,引起的气体分离和漩涡。并且,在前盘进口出增加了平直进口段,还具有以下作用:1.增大了前盘的刚性,其内圈可耐受叶轮长期运转带来的疲劳负荷而不易撕裂;2.增加了进口环的圆度,更好地保证进风口与叶轮装配时,其间的径向间隙t
3
周向均匀;3.增加了进口环的圆度,因为前盘在模具拉伸压型加工时候,由于形成了一段直筒段,其收缩回弹更小,使得在叶轮组装焊接的情况下,从工艺上看,定位更准确,更加好地保证叶轮的跳动和动平衡,如图1所示;4.因为前盘形状总体上看为锥弧形,如进风口与叶轮在装配时,其轴向位置向叶轮一侧偏移会带来二者之间的径向配合间隙明显增大,即通风机的内泄漏明显增大,使得通风机压力明显降低。现由于圆环状进口圈具有一定的轴向长度s,因而不会因为进风口与叶轮装配时的轴向位置略有偏移(特别向叶轮内侧略有偏移)时,二者之间的径向间隙明显增大,导致通风机内泄漏增加,出口流量减少、压力降低和功耗增大, 如图2所示;5.加设平直进口段意味着前盘及叶轮的轴向高度略有增加,可使得通风机装配时,与没有进口平直段相比,进风口的轴向安装位置向外移动了距离s,进风口的末端与叶片前端的距离t
2
增加了s,有利于稳定叶轮入口气流,为叶片对气体高效做功提供了更佳的进口气
流条件。
附图说明
[0014]
图1是本发明叶轮组焊时前盘中心定位示意图;图2是现有技术前盘入口处为弧形时与进风口的配合对比图;图3是本发明通风机装配图;图4是本发明通风机叶轮结构图;图5是本发明通风机叶轮前盘内侧母线示意图;图6为实施例2与对比样机1的静压对比曲线图;图7为实施例2与对比样机1的静压效率对比曲线图;图8为实施例3与对比样机2的静压对比曲线图;图9为实施例3与对比样机2的静压效率对比曲线图。
[0015]
附图标记说明如下:1、叶轮;2、进风口;3、大圆盘;4、芯轴;11、后盘;12、叶片;13、前盘。
具体实施方式
[0016]
下面结合附图对本发明作进一步说明:实施例1本实施例具体说明在前盘入口处增加平直进口段的作用。
[0017]
如图1所示,离心叶轮的后盘11、叶片12、前盘13在组装焊接时,通过垂直的芯轴4和大圆盘3定位前盘的中心,其中,芯轴为叶轮1的轴向中心线,大圆盘与前盘入口端的内壁之间的间隙为δ,对前盘的水平方向和竖直方向都进行了定位。现有技术的前盘,前盘内圆由于模具压型时收缩变形不均匀,存在一定程度的椭圆度,为保证前盘最小内直径能套住大圆盘,势必将大圆盘外径车小,造成前盘圆周方向质量分布不匀以及前盘弧线与叶片弧线贴合不严密,焊接时强行连接有变形,存在跳动和初始动不平衡量偏大,必须依靠叶轮整体整形来保证跳动和动平衡精度合格。与现有技术相比,本发明的前盘内圆的圆度更好,工艺间隙δ的取值可以更小,前盘中心偏离叶轮中心可能的程度更小,能确保前盘中心定位更准确,不但前盘弧线与叶片前端边缘弧线更加贴合,焊接时的变形小,而且前盘及叶轮部件的质量偏心量更小,因此叶轮的跳动小,动平衡精度高。
[0018]
另外,在进风口2和叶轮1的装配中,现有技术中前盘入口处为弧线时,由于装配过程中引起的误差,进风口套入前盘内的深度略有不同时,也就是轴向重叠不同时,会造成进风口和前盘之间的径向间隙t
3
明显增大。如图2所示,前盘入口为弧线时,当进风口与前盘的轴向重叠长度为6mm时,进风口与前盘的径向间隙为4.2mm。当进风口朝前盘内再轴向伸入到8mm时,进风口与前盘的径向间隙为4.6mm,径向间隙增加了0.4mm。在叶轮的高速运转下,0.4mm的间隙对于气流的影响是很明显的,容易造成通风机内泄漏增加,出口流量减少、压力降低和功耗增大。
[0019]
本申请中,在前盘入口增加了平直进口段,由于其具有一定的轴向长度s,因而不会因为进风口与叶轮装配时的轴向位置略有偏移,特别向叶轮内侧略有偏移时,二者之间的径向间隙明显增大。在平直进口段长度范围内,进风口在轴向的移动,进风口与前盘的径
向间隙是不变的。
[0020]
进一步的,如图3所示,加设平直进口段意味着前盘及叶轮的轴向高度增加,可使得通风机装配时,与没有进口平直段相比,进风口的轴向安装位置向外移动了距离s,s为平直进口段的轴向长度,相当于进风口的末端与叶片前端的距离t
2
增加了s,有利于稳定叶轮入口气流,为叶片对气体高效做功提供了更佳的进口气流条件。
[0021]
实施例2本实施例具体说明主体弧形段的作用。
[0022]
本发明的实施例2和对比样机1相比较,除了主体弧线段截面弧线不同之外,其通风机其余部分均完全相同,配用的电机及运行转速也相同。对比样机1主体弧线段截面形状为圆弧,实施例2主体弧线段截面形状为本发明的主体弧形段曲线,包括平直进口段“ab”,主体弧形段“bc”,平直出口段“cd”和出口翻边段“def”。
[0023]
实施例2和对比样机1相关尺寸如下:d
2
=526.6 mmd
0
=352.5 mmd
3
=566 mms=6 mmu=87 mmv=53.5 mmθ=31.6
°
v/u=0.615实施例2和对比样机1的性能曲线对比见图6-图7;相同风量工况点性能参数对比见表1。
[0024]
表1 转速(r/min)风量(m
3
/h)静压(pa)静压效率(%)对比样机117808424851.666.5实施例217808424884.768.5相同风量的工况下,实施例2与对比样机1相比,静压提高了33.1pa,静压效率提高了2 %。
[0025]
实施例3本实施例通过另一种叶轮尺寸具体说明主体弧形段的作用。
[0026]
本发明的实施例3和对比样机2相比较,除了主体弧线段截面弧线不同之外,其通风机其余部分均完全相同,配用的电机及运行转速也相同。对比样机2主体弧线段截面形状为圆弧,实施例3的主体弧线段截面形状为本发明的主体弧形段曲线。
[0027]
实施例3和对比样机2相关尺寸如下:d
2
=639.6 mmd
0
=444 mmd
3
=716 mms=7 mmu=97.8 mm
v=68 mmθ=34.8
°
v/u=0.695实施例3和对比样机2的性能曲线对比见图8-图9;相同风量工况点性能参数对比见表1。
[0028]
表2 转速(r/min)风量(m
3
/h)静压(pa)静压效率(%)对比样机2145013230845.470.2实施例3145013230872.571.8相同风量的工况下,实施例3与对比样机2相比,静压提高了27.1pa,静压效率提高了1.6 %。
[0029]
结论:本发明的改进方案,主要是通过前盘截面弧线形状的优化,使得叶轮内叶片前端进气条件得以改善和叶片之间的通道内流场得到了优化,从而提高了叶轮对气体做功的效率,明显提高了通风机的性能和效率、降低了能耗和噪声,而叶轮主要特征尺寸及工艺加工方式并没有改变,具有一定的经济和社会价值。
[0030]
以上显示和描述了本发明的基本原理、主要特征和优点。本行业的技术人员应该了解,本发明不受上述实施例的限制,上述实施例和说明书中描述的只是说明本发明的原理,在不脱离本发明精神和范围的前提下,本发明还会有各种变化和改进,这些变化和改进都落入本发明要求保护的范围内。