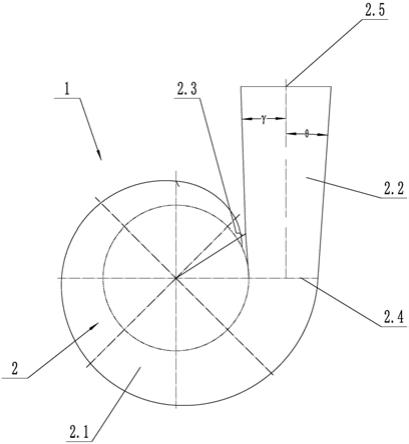
1.本实用新型涉及单级离心泵蜗壳领域,尤其是涉及一种系列化单级离心泵蜗壳。
背景技术:2.离心泵是依靠动力轴输入的旋转动能将叶轮入口的低压液体变为叶轮出口的高压和高速液体,在蜗壳内收集并降速扩压转化为压力能,驱动流体输送。泵的蜗壳起到收集旋转叶轮外圆周围送出的液体,将高速的液流进行低损耗降速,转换为压力能,送向泵出口扩散段。扩散段进一步降速扩压,降低流速,扩大压力,减少泵出口的流动损耗。单级蜗壳式离心泵的结构由泵体、叶轮组成的水力部件,泵盖、密封垫、动密封、紧固螺栓等组成的承压部件,含有转轴的轴承箱,以及动力机械和联轴器、安装底座等组成。
3.离心泵的流量扬程水力性能需满足装置工况的需求。而装置和工况往往各不相同,这样就会导致需要无数个不同设计的水力部件。为适应不同装置和不同流量扬程工况的需求,同时又避免规格太多导致生产制造成本较大,单级蜗壳式离心泵水力部件按额定流量和额定扬程分档设计规格,每个规格满足一定范围内的工况需求。其中按额定扬程分档一般是按叶轮外径分档,因为泵的扬程与叶轮外径密切相关,且按叶轮外径分档的好处是,通过泵体开口的孔径分档,不同流量的叶轮可以采用同一个孔径,即泵盖的配合孔径可以相同,有利于泵盖的通用化。
4.同时,为降低离心泵的制造成本提高生产效率,单级离心泵通常按系列化设计,一个系列的离心泵包含数个按轴径分档的通用轴承箱部件和密封部件,外露部分的密封部件位于泵盖端部和轴承箱之间,其尺寸是一定的,参考api610标准有最小空间要求。每个轴承箱部件按最大承载能力(应力和变形)适配系列内一部分水力部件。但是因为同一轴承箱所配套的水力部件流量有大小,对于流量较小的泵,叶轮出口流道宽度和泵体压水室进口宽度较小,压水室断面面积较小,可以做成简单的矩形断面;流量较大的泵,为减少液体与压水室壁面的摩擦损失,降低压水室中的液体流速,从而提高泵的效率,将压水室断面轴向宽度沿径向方向逐步扩大,形成梯形断面。但由于泵体端部需要与泵盖联接密封并承受压力,需要在泵体与泵盖的联接端部开螺纹孔以安装联接螺栓。螺纹孔的底部需保留一定的壁厚防止渗漏,如美国api610标准,就规定了承压泵体螺纹孔底部的壁厚不小于螺纹孔径的一半。而这圈螺纹孔恰恰位于压水室梯形断面部位外侧,因此在螺纹孔直径一定的情况下,泵体端部的最小有效轴向厚度也确定了。
5.这样导致的结果是:流量越大的泵体,压水室梯形断面的轴向宽度越大,泵体流道中心到与泵盖的联接端面的轴向尺寸越大;而流量较小的泵体的压水室断面轴向宽度较小,泵体流道中心到与泵盖的联接端面的轴向尺寸可以较小,也可以与同一轴系的流量最大的泵体的轴向尺寸一致。如果两者泵体的轴向尺寸做成一致,则较小流道的泵体与泵盖联接端部将有较大的轴向实体厚度,既容易造成泵体的铸造缩松缺陷,同时也浪费了泵体的材料,还使得叶轮的轴向悬臂不必要地加大,加大了转轴的扰度,降低了泵的运转可靠性。而如果两者泵体的轴向尺寸做成不一致,则由于配套的是同一个轴系,两型泵的流道中
心到轴承箱定位端的距离一致,则需要依靠中间不同轴向尺寸的泵盖进行联接,泵盖无法通用,生产管理和制造成本较高,同时叶轮的轴向悬臂量还是按最大流量的泵而定,加大了转轴的扰度,影响机械密封端面的垂直度而降低密封能力,且悬臂增加会提高泵的振动值,降低了泵运转的可靠性。因此,需要设计一种系列化单级离心泵蜗壳,使泵体上靠泵盖一侧的通流表面为垂直于轴中心线的平面,用于设置联接用螺纹孔的实体轴向厚度根据设计规则是确定的,无需考虑压水室流道断面形状,当设计不同泵流量同叶轮外径时,靠泵盖侧的泵体轴向壁厚可以相同,泵盖可以设计成通用。
6.中国专利申请公开号cn1176303c,公开日为2004年11月17日,名称为“梯形或矩形截面流道离心泵及冲压焊接成型制造方法”,公开了一种泵及制造工艺方法,确切地说是梯形或矩形截面流道离心泵及冲压焊接成型制造方法。其特征在于壳体由进水管1、蜗壳3和压水室4焊合组成:蜗壳3中部呈碗状,其碗状大口端沿径为台阶形,同轴的另一端中部设有进水管口,蜗壳3径向上设有出水管口。其制造方法特征在于采用钢性模具冲压成形梯形或矩形流道蜗壳、进水管和压水室,焊合后形成壳体。本实用新型设计合理,迷宫密封部件不需专门单独制造,结构相对简单,节能、节材、生产效率高、制造过程无污染。但是该专利中的离心泵仍存在上述问题。
技术实现要素:7.本实用新型为了克服现有技术中泵体的轴向尺寸做成不一致时,需要依靠中间不同轴向尺寸的泵盖进行联接,泵盖无法通用,生产管理和制造成本较高的问题,提供一种系列化单级离心泵蜗壳,当设计不同泵流量同叶轮外径时,靠泵盖侧的泵体轴向壁厚可以相同,泵盖可以设计成通用形状。
8.为了实现上述目的,本实用新型采用以下技术方案:
9.一种系列化单级离心泵蜗壳,包括蜗壳本体,蜗壳本体内设有水流通道,水流通道包括相互连通的压水室和扩散段,压水室的起始端为隔舌,压水室和扩散段的连接处为喉部,所述压水室由隔舌处向喉部位置逐渐增大的一组断面联接组成,压水室断面一侧为直角梯形,另一侧为矩形,矩形靠近泵盖一侧,整个压水室断面组成直角梯形。
10.上述技术方案中,压水室采用轴向不对称断面,以中心线为基准,其中靠泵盖侧的断面为矩形,另一侧为直角梯形,使泵体上靠泵盖一侧的通流表面为垂直于轴中心线的平面,用于设置联接用螺纹孔的实体轴向厚度根据设计规则是确定的,无需考虑压水室流道断面形状,当设计不同泵流量同叶轮外径时,靠泵盖侧的泵体轴向壁厚可以相同,泵盖可以设计成通用形状;而且由于该处轴向壁厚按设计规则可以按最小值设计,在密封腔轴向尺寸一定时,叶轮处的悬臂量可以设计得较小,有效减小了转轴的扰度,提高了密封的可靠性,降低了泵的振动。
11.作为优选,所述扩散段的出口处为泵体出口,扩散段由喉部至泵体出口,通流面积逐步扩大,断面由直角梯形逐步过渡为圆形,最终与泵体出口通径形状一致。所述结构设计可以通过扩散段将压水室的直角梯形形状的端面过渡为泵体出口的圆形形状。
12.作为优选,所述扩散段侧壁母线与扩散段中心线之间的角度不大于5
°
。如果扩散角过大可能造成液体脱流而降低效率,由于是轴向不对称断面,因此需按单侧扩散角控制,扩散段四个方向的扩散角α、β、γ、θ单侧扩散角控制在5
°
内,既能有效将动能转化成压力
能,又减小由此造成的能量损耗,保证较高的泵效率。
13.作为优选,所述喉部位置的压水室的断面形状与扩散段的端面形状相同且重合。所述结构保证压水室与扩散段平滑过渡。
14.作为优选,所述压水室断面的直角梯形和矩形的拐角处通过圆弧过渡,整个压水室断面为类直角梯形。所述结构便于铸造加工,并有利于减少断面的湿周长度,提升压水室效率,并使与扩散管的过渡更顺滑。
15.作为优选,所述压水室的各断面面积以喉部断面积a为基准,按等速度法确定其余各包角φ部位的断面积s。所述结构可以保证各个端面流速的一致性和稳定性。
16.作为优选,所述直角梯形的直角边到与泵盖的联接端为泵体的实体,设置有安装紧固联接件的螺纹孔。用于设置联接用螺纹孔的实体轴向厚度根据设计规则是确定的,无需考虑压水室流道断面形状;当设计不同泵流量同叶轮外径时,靠泵盖侧的泵体轴向壁厚可以相同,泵盖可以设计成通用。
17.一种系列化单级离心泵蜗壳水力设计方法,用于设计上述的一种系列化单级离心泵蜗壳,所述喉部面积a根据水力设计计算确定,各断面面积以扩散段的喉部断面积a为基准,按等速度法确定其余各包角φ部位的断面积s,即s=φ/360*a。所述结构可以保证各个端面流速的一致性和稳定性。
18.作为优选,所述直角梯形的直角边到与泵盖的联接端为泵体的实体,设置有安装紧固联接件的螺纹孔,其轴向壁厚根据所需的螺孔深度和剩余壁厚最低要求确定最小壁厚,并根据同一轴型的轴向控制尺寸确定实际设计壁厚。由于该处轴向壁厚按设计规则可以按最小值设计,在密封腔轴向尺寸一定时,叶轮处的悬臂量可以设计得较小,有效减小了转轴的扰度,提高了密封的可靠性,降低了泵的振动。
19.作为优选,所述扩散段最小长度l按断面最大形变方位的形变尺寸r进行计算确定,l=r*tg5
°
,保证各断面间光滑过渡。扩散长度按照l=r*tg5
°
控制,在设计时可以根据扩散段进出断面图,按最大的断面间距值r直接计算确定所需的出口管高度,既可以方便快捷地确定泵体出口的高度,又保证扩散段内液体有序扩散实现有效的能量转换。
20.本实用新型的有益效果是:(1)当设计不同泵流量同叶轮外径时,靠泵盖一侧的泵体轴向壁厚可以相同,泵盖可以设计成通用;(2)用于设置联接用螺纹孔的实体轴向厚度根据设计规则是确定的,无需考虑压水室流道断面形状:(3)在密封腔轴向尺寸一定时,叶轮处的悬臂量可以设计得较小,有效减小了转轴的扰度,提高了密封的可靠性,降低了泵的振动;(4)扩散段四个方向的扩散角单侧扩散角控制在5
°
内,既能有效将动能转化成压力能,又减小由此造成的能量损耗,保证较高的泵效率。
附图说明
21.图1是本实用新型中水流通道的结构示意图;
22.图2是本实用新型中压水室处的水流通道断面结构示意图;
23.图3是本实用新型中泵体出口处的水流通道断面结构示意图;
24.图4是本实用新型中喉部处的水流通道断面结构示意图;
25.图5是本实用新型泵体的外形结构示意图。
26.图中:蜗壳本体1、水流通道2、压水室2.1、扩散段2.2、隔舌2.3、喉部2.4、泵体出口
2.5。
具体实施方式
27.下面结合附图和具体实施例对本实用新型做进一步的描述。
28.实施例1:
29.如图1所示,一种系列化单级离心泵蜗壳水力设计方法,包括蜗壳本体1,蜗壳本体1内设有水流通道2,水流通道2由压水室2.1和扩散段2.2组成,所述结构便于铸造加工,并有利于减少断面的湿周长度,提升压水室效率,并使与扩散管的过渡更顺滑。压水室2.1的起始端为隔舌2.3,压水室2.1和扩散段2.2的连接处为喉部2.4,扩散段2.2的出口处为泵体出口2.5;所述压水室2.1以叶轮外圆外侧的设计基圆为基准,由隔舌2.3部位开始沿叶轮旋转方向向泵扩散段2.2入口的喉部2.4逐渐增大的一组断面联接组成。所述喉部2.4的端面面积a根据水力设计计算确定,各断面面积以扩散段2.2入口喉部2.4断面积a为基准,按等速度法确定其余各包角φ部位的断面积s,即s=φ/360*a;如图2所示,所述压水室2.1断面一侧为直角梯形,另一侧为矩形,所述梯形和矩形底部倒圆,图2中,双点划线轮廓未做倒圆前的断面形状,即整个压水室2.1断面为近似直角梯形。所述直角梯形的直角边一侧(矩形一侧)靠近泵盖端。所述直角梯形的直角边到与泵盖的联接端为泵体的实体,设置有安装紧固联接件的螺纹孔,其轴向壁厚根据所需的螺孔深度和剩余壁厚最低要求确定最小壁厚,并根据同一轴型的轴向控制尺寸确定实际设计壁厚。如图3和图4所示,所述扩散段2.2由喉部2.4至泵体出口2.5,通流面积逐步扩大,断面由直角梯形逐步过渡为圆形,最终与泵出口通径形状一致;如图1和图5所示,所述扩散段2.2侧壁母线与扩散段2.2中心线之间的角度不大于5
°
,扩散段2.2最小长度l按断面最大形变方位的形变尺寸r进行计算确定,l=r*tg5
°
,保证各断面间光滑过渡。
30.上述方案形成的离心泵蜗壳压水室2.1,与现有技术的泵压水室2.1的主要区别,是压水室2.1采用轴向不对称断面,以中心线为基准,其中靠近泵盖一侧的断面为矩形,另一侧为梯形。这样设计,使泵体上靠近泵盖一侧(图3中的右侧)的通流表面为垂直于轴中心线的平面,用于设置联接用螺纹孔的实体轴向厚度根据设计规则是确定的,无需考虑压水室2.1流道断面形状。当设计不同泵流量同叶轮外径时,靠近泵盖一侧的泵体轴向壁厚可以相同,泵盖可以设计成通用;而且由于该处轴向壁厚按设计规则可以按最小值设计,在密封腔轴向尺寸一定时,叶轮处的悬臂量可以设计得较小,有效减小了转轴的扰度,提高了密封的可靠性,降低了泵的振动。扩散段2.2的侧壁形状需要控制,原因是如果扩散角过大将可能造成液体脱流而降低效率,由于是轴向不对称断面,因此需按单侧扩散角控制,扩散段2.2四个方向的扩散角α、β、γ、θ单侧扩散角控制在5
°
内,既能有效将动能转化成压力能,又减小由此造成的能量损耗,保证较高的泵效率。扩散段2.2长度按照l=r*tg5
°
控制,在设计时可以根据扩散段2.2进出断面图,按最大的断面间距值r直接计算确定所需的出口管高度,既可以方便快捷地确定泵出口的高度,又保证扩散段2.2内液体有序扩散实现有效的能量转换。
31.本实用新型的有益效果是:当设计不同泵流量同叶轮外径时,靠泵盖一侧的泵体轴向壁厚可以相同,泵盖可以设计成通用;用于设置联接用螺纹孔的实体轴向厚度根据设计规则是确定的,无需考虑压水室流道断面形状:在密封腔轴向尺寸一定时,叶轮处的悬臂
量可以设计得较小,有效减小了转轴的扰度,提高了密封的可靠性,降低了泵的振动;扩散段四个方向的扩散角单侧扩散角控制在5
°
内,既能有效将动能转化成压力能,又减小由此造成的能量损耗,保证较高的泵效率。