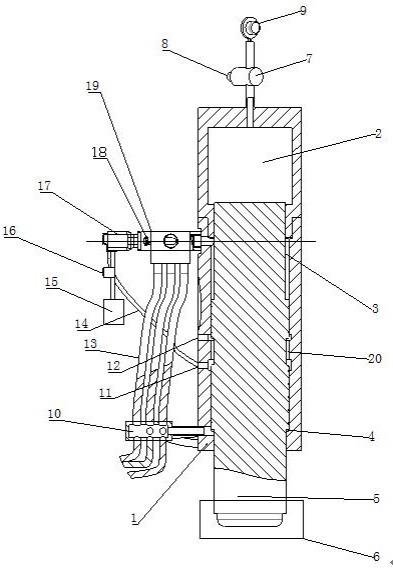
1.本实用新型涉及桩基施工技术领域,特别涉及到一种新型双动力冲击植桩锤。
背景技术:2.氮爆锤工作原理:氮气爆发式液压锤简称氮爆锤。活塞顶部都设置有氮气室也就是活塞式蓄能器,活塞上腔常通回油,活塞下腔由控制阀进行切换,回程时通高压油,冲程时通回油,活塞回程运动时,高压油进入活塞下腔,推动活塞上移,同时活塞顶部压缩氮气室里的氮气,氮气压力上升,液压能转换为气压能而被存储。活塞冲程时,下腔的油路已被切换,从接通高压油转换为接通回油,氮气压力作用于活塞顶部,氮气膨胀做功,同时氮气压力下降,直至回程开始时的最低氮气压力,又开始另一次回程运动。
3.从工作原理上讲,在活塞冲程阶段,油泵的供油是无路可走的,此时的高压油只能由胶管膨胀来吸收或从高压溢流阀溢出,必然造成液压系统的压力冲击,对油泵、管路造成不利影响,同时引起系统发热。氮爆锤的活塞冲击动作完全靠氮气膨胀实现,为了达到一定的冲击能以满足破碎作业的需要,必然要求氮气充气压力较高,一般大于2mpa。液压锤开始工作前,挖掘机必须将液压锤压紧,否则液压锤不能启动,而较高的氮气室充气压力,必然造成挖掘机下压困难,甚至使挖掘机机身抬起,一旦启动后,挖掘机又落下,造成震动,对挖掘机有损害。本实用新型在氮爆锤的工作原理上进行改进,使得设备避免损伤的情况下,提供较大的冲击力,基于此,本实用新型提出了一种新型双动力冲击植桩锤。
技术实现要素:4.针对现有技术中存在的上述技术问题,本实用新型提出了一种新型双动力冲击植桩锤,克服了现有技术的不足。通过低压油腔、高压油腔和泄压油腔的设置,使得液压系统不再承受冲击荷载,保护系统稳定;实现重力和高压空气做功,提高锤杆冲击功,与传统重力式送桩锤相比,质量更轻;在斜桩送桩施工时,该设备输出冲击功受送桩角度影响较小。
5.为了实现上述目的,本实用新型采用如下技术方案:
6.一种新型双动力冲击植桩锤,其特征在于,包括壳体、压气腔、低压油腔、高压油腔、重锤杆、气垫、单向阀、空压机管路、压力表、汇油阀、高压换向油通道、泄油通道、串油管、换向油管、低压油泵、溢流阀、换向马达、限位块、换向阀体、泄压油腔,所述重锤杆为圆柱形结构,重锤杆表面有两段环形凸起结构,所述壳体上设置有导正套,所述重锤杆与壳体之间紧密接触,重锤杆与壳体之间的空隙形成低压油腔、高压油腔和泄压油腔,所述壳体内部的上端预留有压气腔,壳体上安装有单向阀,所述单向阀与压气腔连通,单向阀上安装有压力表,单向阀上预留有空压机管路,所述壳体上预留有泄油通道,泄油通道的一端与泄压油腔连通,另一端直接连接到回油箱,所述壳体上预留有高压换向油通道,高压换向油通道的一端与高压油腔连通,另一端通过换向油管与换向马达连接,所述汇油阀与换向阀体之间通过串油管连接,所述汇油阀与高压油腔连通,所述换向阀体与低压油腔连通,所述低压油泵通过油管与换向马达连接,低压油泵与换向马达之间的油管上安装有溢流阀。
7.优选地,所述重锤杆表面的两段环形凸起结构的凸起高度一致,环形凸起段上设置有油道。
8.优选地,所述气垫为圆形结构,气垫的直径为400mm~800mm,气垫的厚度为150mm~250mm。
9.优选地,所述限位块的旋转角度为90
°
,每次旋转的转动角度一致,均为90
°
。
10.本实用新型所带来的有益技术效果:
11.(1)通过低压油腔、高压油腔和泄压油腔的设置,使得液压系统不再承受冲击荷载,保护系统稳定;(2)实现重力和高压空气做功,提高锤杆冲击功,与传统重力式送桩锤相比,质量更轻;(3)在斜桩送桩施工时,该设备输出冲击功受送桩角度影响较小;(4)结构紧凑,便于制造,使用安全可靠,操作简单方便,适应环境能力强和使用寿 命长。
附图说明
12.图1为本实用新型一种新型双动力冲击植桩锤的结构示意图。
13.图2为本实用新型一种新型双动力冲击植桩锤中重锤杆的结构示意图。
14.其中,1
‑
壳体、2
‑
压气腔、3
‑
低压油腔、4
‑
高压油腔、5
‑
重锤杆、6
‑
气垫、7
‑
单向阀、8
‑
空压机管路、9
‑
压力表、10
‑
汇油阀、11
‑
高压换向油通道、12
‑
泄油通道、13
‑
串油管、14
‑
换向油管、15
‑
低压油泵、16
‑
溢流阀、17
‑
换向马达、18
‑
限位块、19
‑
换向阀体、20
‑
泄压油腔。
具体实施方式
15.下面结合附图以及具体实施方式对本实用新型作进一步详细说明:
16.实施例1:
17.如图1~2所示,一种新型双动力冲击植桩锤,其特征在于,包括壳体1、压气腔2、低压油腔3、高压油腔4、重锤杆5、气垫6、单向阀7、空压机管路8、压力表9、汇油阀10、高压换向油通道11、泄油通道12、串油管13、换向油管14、低压油泵15、溢流阀16、换向马达17、限位块18、换向阀体19、泄压油腔20,所述重锤杆5为圆柱形结构,重锤杆5表面有两段环形凸起结构,所述壳体1上设置有导正套,所述重锤杆5与壳体1之间紧密接触,重锤杆5与壳体1之间的空隙形成低压油腔3、高压油腔4和泄压油腔20,所述壳体1内部的上端预留有压气腔2,壳体1上安装有单向阀7,所述单向阀7与压气腔2连通,单向阀7上安装有压力表9,单向阀7上预留有空压机管路8,所述壳体1上预留有泄油通道12,泄油通道12的一端与泄压油腔20连通,另一端直接连接到回油箱,所述壳体1上预留有高压换向油通道11,高压换向油通道11的一端与高压油腔4连通,另一端通过换向油管14与换向马达17连接,所述汇油阀10与换向阀体19之间通过串油管13连接,所述汇油阀10与高压油腔4连通,所述换向阀体19与低压油腔3连通,所述低压油泵15通过油管与换向马达17连接,低压油泵15与换向马达17之间的油管上安装有溢流阀16。
18.优选地,所述重锤杆5表面的两段环形凸起结构的凸起高度一致,环形凸起段上设置有油道。
19.优选地,所述气垫6为圆形结构,气垫6的直径为400mm~800mm,气垫6的厚度为150mm~250mm。
20.优选地,所述限位块18的旋转角度为90
°
,每次旋转的转动角度一致,均为90
°
。
21.实施例2:
22.采用本实用新型的技术方案进行原理及使用方法的进一步介绍。
23.如图1~2所示,电动机启动后,低压油泵15驱动换向马达17将换向阀芯保持在低压油腔3与泄油通道12相通的状态,此时高压油通过串油管13进入汇油阀10,此时,汇油阀10与高压油腔4连通,不与低压油腔3连通,高压油在高压油腔4建立压力,将重锤杆5向上推动并压缩压气腔2内的空气,低压油腔3内液压油经泄油通道12回油至油箱。压气腔2与外界空压机经单向阀7连通,保证空压机空气及时补充到压气腔2,高压气体不泄漏。
24.当重锤杆5向上运动到达上止点时,高压油腔4与高压换向油通道11相通,高压油经换向油管14驱动换向马达17旋转将换向阀芯旋转至低压油腔3与串油管13相通的状态,换向马达17反向旋转时排出的液压油经溢流阀16回至油箱。
25.当低压油腔3与串油管13相通时,高压油腔4与低压油腔3相通,此时重锤杆5两油腔压差为零,压气腔2和重力,推动重锤杆5向下运动,对气垫6进行冲击,高压油腔4液压油经汇油阀10、串油管13、换向阀芯进入低压油腔3。
26.气垫6下放置钢管桩,混凝土管桩,型钢桩等进行植桩作业,气垫6可避免由于冲击力过大对桩端造成破坏。
27.当重锤杆5到达下止点时,高压换向油通道11与泄油通道12相通,低压油泵15将驱动换向马达17将换向阀芯旋转并保持在低压油腔3与泄油通道12相通的状态。换向马达17正转反转90度由限位块18保证其换向准确。此时进入下一个压气做功过程,并依次循环。
28.本实用新型一种新型双动力冲击植桩锤,通过低压油腔、高压油腔和泄压油腔的设置,使得液压系统不再承受冲击荷载,保护系统稳定;实现重力和高压空气做功,提高锤杆冲击功,与传统重力式送桩锤相比,质量更轻;在斜桩送桩施工时,该设备输出冲击功受送桩角度影响较小;结构紧凑,便于制造,使用安全可靠,操作简单方便,适应环境能力强和使用寿 命长。
29.当然,上述说明并非是对本实用新型的限制,本实用新型也并不仅限于上述举例,本技术领域的技术人员在本实用新型的实质范围内所做出的变化、改型、添加或替换,也属于本实用新型的保护范围。