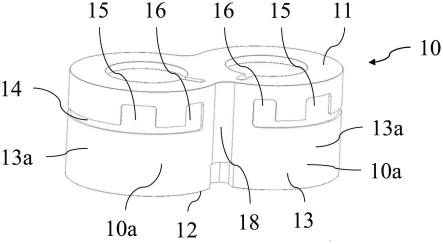
1.本发明涉及一种衬套组件和包括所述衬套组件的对应容积式旋转泵(优选为齿轮泵或凸轮泵)。
2.容积式旋转泵可以有用地应用于各种技术领域。特别地,本发明的泵特别适用于需要随时间改变转速的高压应用。
背景技术:3.如上所述,本发明有用地应用于涉及齿轮或凸轮容积式旋转泵的技术领域。这种类型的泵通常包括两个转子,其中一个转子(称为主动转子)连接到驱动轴并使另一个转子(称为从动转子)旋转。
4.两个转子由衬套组件所支撑的相应轴承载,衬套组件通常由衬环和实际的衬套构成。衬套组件联接在外壳或泵体的内腔中,并在其中轴向浮动,以允许由于作用在组件本身的相对平面上的压力而封装部件。
5.当前使用的衬环可以在面向转子的平面上具有凹坑,或者在面向外壳的封闭法兰的平面上具有垫圈座。这些凹坑或座可用于促进润滑衬套的油的排出,并且-如上所述-补偿由于处于压力下的流体引起的轴向推力,即,以保持转子和衬套的表面除了油膜之外直接接触。其他类型的凹坑允许封装在齿轮齿之间的流体在排出区域中再循环,由此减少脉动和噪声。
6.各种形状和功能的凹坑100在附图2和附图3中可见,附图2表示根据现有技术的衬环半元件10a,相反,附图3表示根据现有技术的整体衬环10。
7.迄今为止,衬环的设计始终致力于一方面获得其轴向平衡,另一方面限制环本身相对于转子轴线的错位,从而试图控制作用在衬环平面上的压力中心。
8.另一方面,从未对环的圆柱形面进行任何干预,以避免由于重压在转子上并且在环本身上释放的的载荷的分布而引起的摩擦和磨损现象,环如前所述在泵壳的孔内自由滑动。
9.迄今为止采用的构造解决方案,虽然基本上适用于该目的,但是在泵承受重应用的情况下具有显著的缺点。
10.事实上,在这些情况下,衬环的力被释放到的主体孔的表面发生磨损,并且对应地,衬环本身发生磨损。两个接触面之间的微小滑动会导致零件的粗糙度劣化,这在比载荷较大的区域引发局部加热现象。材料然后局部塑化并且变得不那么光滑:这导致衬环在瞬态期间卡住,从而对应地劣化泵性能。
11.上述现象借助于图4至图6进行了说明和分析。
12.图4示意性地示出了已知类型的齿轮泵的示例。该泵按照与穿过两个转子轴线的平面正交的平面进行纵向剖切呈现,使得在截面的下部有吸入侧s,在上部有排出侧d。除了示出了泵壳3的吸入侧s上的壁之外,还示出了主动转子2、驱动轴5和两个衬套组件10。由于泵运行期间形成的过压,分布载荷f从排出侧d作用在衬套组件10和转子2两者上。该图突出
了衬环10的微小滑动区域z1和发生卡住的磨损区域z2。
13.图5和图5a提出了申请人进行的静态分析,其对上述现象进行了解释。在图5中,利用四个滑架约束a、b、c、d对由衬环10和转子2构成的结构建模。图5a示出了指示结构的载荷f、力矩t和对应变形d的曲线图。可见,在b点和c点都有最大约束反作用力和最大力矩,它们分别在a点和d点减小。因此,通过沿着整个衬环线性化反作用力,获得梯形分布sj。因此,设置条件不是最佳的,并且导致上述问题。
14.图6中介绍了对该系统的进一步分析,该图示出了由建模软件计算的力线,这些力线是在衬环-转子组件的二维模型内产生的。可见,最大应力集中在上述磨损区域z2处出现在衬环的内边缘;当朝向外边缘移动时,这种集中会迅速降低。
15.文献us 4,087,216公开了一种根据现有技术的旋转流体泵。该泵采用滚针轴承,不使用轴向浮动衬套。
16.鉴于上述内容,本发明所要解决的技术问题是构思一种衬套组件和对应的容积式旋转泵,其至少部分地解决上述现有技术的缺陷,因此具有改善的性能和使用寿命以及更低的瞬态响应时间。
技术实现要素:17.本发明的解决方案思想在于创建加压箱,这些加压箱定位于衬套组件的在使用时与泵壳直接接触的部分(即在吸入侧的内边缘处的部分)下方,以便降低较大应力区域中的比压。
18.鉴于该解决方案的思想,上述技术问题通过一种容积式旋转泵来解决,该容积式旋转泵包括:外壳,该外壳设置有内腔,该内腔具有在排出侧开口的排出口和在相对吸入侧开口的吸入口;一对轴,该对轴在其中间部分承载在内腔内旋转的多个相互啮合的转子,这些转子用于将流体从排出口泵送到吸入口;两个衬套组件,该两个衬套组件布置在转子的相对端,用于支撑轴;所述衬套组件包括:内表面,该内表面面向转子;相对的外表面;以及侧面,该侧面连接两个内表面和外表面,侧面联接在内腔内;其中,衬套组件在其侧面上包括至少一个补偿箱,该补偿箱在离内表面比离外表面更近的位置面向内腔的吸入侧;以及至少一个排放通道,该排放通道将所述补偿箱连接到侧面的面向排出侧的部分。
19.在整个容积式旋转泵的情况下,技术问题还通过上述类型的衬套组件来解决。
20.根据本发明的衬套组件可以包括整体的或两件式的衬环;在这种情况下,排放通道和至少一个补偿箱制作在衬环上,该衬环布置成承载两个内衬套。另一方面,不排除衬套组件可以制成单一元件或两个并置元件,而不存在与其支撑的衬套不同的衬环。
21.由于上述结构,所述补偿箱在使用时被来自排出泵的处于压力下的流体填充。由此限定了相应衬套组件上的矫直扭矩,这有助于释放在根据现有技术的泵中趋于磨损的最大应力区域。
22.换言之,根据本发明的结构旨在排放排出流体并将其带入上述补偿箱中以促进相应衬套组件的支撑。
23.以本身已知的方式,所述衬套组件成形为彼此联接的两个套筒形半组,所述半组制成一体或彼此分离。
24.侧面由此包括两个圆柱形部分,其在半组的分别在排出侧和吸入侧上的两个联接
区域中连接或以任何方式并置。
25.排放通道优选将排出侧上的联接区域与至少一个补偿箱连接;它优选在到达吸入侧上的相对联接区域之前中断。
26.优选地,排放通道采用深度有限的外周槽的形式,该外周槽制作在侧面的至少一个-优选两个-圆柱形部分上。
27.在一个优选实施例中,补偿箱采用沿限定排放通道的周向槽的轴向加宽的形式,例如具有基本上平行六面体形状。
28.优选地,补偿箱相对于排放通道朝向内表面轴向延伸。
29.优选地,补偿箱和排放通道具有相同的深度。
30.在一个优选实施例中,所述补偿箱对于每个衬套组件的每个半组都至少有两个;它们可以通过排放通道本身连接。例如,补偿箱可以包括:至少一个中间补偿箱,该至少一个中间补偿箱拦截排放通道的延伸;以及至少一个末端补偿箱,排放通道终止于该至少一个末端补偿箱。
31.根据本发明的泵的特征和优点将从以下参照附图以非限制性示例的方式给出的实施例示例的描述中变得显而易见。
附图说明
32.附图1至附图12示出了以下内容:
33.图1示出了普通容积式旋转泵、特别是齿轮泵的分解部分立体图,其上没有详细说明本发明的主要方面;
34.图2如上所述示出了根据现有技术的衬套组件的元件的立体图;
35.图3如上所述示出了根据现有技术的另一衬套组件的立体图;
36.图4如上所述示出了现有技术的容积式旋转泵内的力分布的第一示意图;
37.图5如上所述示出了现有技术的容积式旋转泵内的力分布的第二示意图;
38.图5a如上所述示出了由图5所示泵中的转子和衬套组件构成的结构的载荷f、力矩t和对应变形d的曲线图;
39.图6如上所述表示在图5所示泵中的衬套组件-转子组的二维模型内产生的力线;
40.图7示出了根据本发明的容积式旋转泵的衬套组件的立体图;
41.图8示出了图7的衬套组件根据不同角度的立体图;
42.图9仍然示出了图7的立体图,其突出了更大载荷集中的区域;
43.图10示出了图7的衬套组件的侧视图;
44.图11示出了根据本发明的容积式旋转泵内的力分布的示意图;
45.图11a示出了由图11所示泵中的转子和衬套组件构成的结构的载荷f、力矩t和对应变形d的曲线图;和
46.图12表示在图11所示泵中的衬套组件-转子组的二维模型内产生的力线。
具体实施方式
47.参照图1,附图标记1总体上示意性地指示根据本发明制造的具有齿轮的容积式旋转泵。
48.容积式旋转泵1包括一对转子2,特别是齿轮,该对转子由相应的轴5支撑并封闭在外壳3中。第一主动齿轮连接到相对于外壳3具有突出端的驱动轴,并且第二从动齿轮由主动轮转动。在本发明的一个优选实施例中,两个转子2为具有螺旋齿的齿轮。
49.外壳3由由于是已知类型而未表示的两个盖或法兰前后封闭。外壳的一侧具有未在附图中表示的流体吸入口,另一侧具有排出口4。此外,外壳限定内腔,转子2和衬套组件10被引入该内腔中,该内腔在吸入口处具有吸入侧s,在排出口d处具有相对的排出侧。
50.在外壳3内,转子2的轴5的两端由两个衬套组件10支撑,图1中仅表示了其中一个。每个衬套组件10都可以制成一体,如图所示,或者制成两个分开的并置的半组10a,类似于图2的现有技术所提供的半组。优选地,每个衬套组件10都包括衬环和安装在其上的两个衬套19。
51.应当注意,图1没有说明根据本发明的衬套组件10的独特性,这些独特性而是在随后的图7至图10中可见。
52.如可以观察到的,每个衬套组件10都具有:内表面11,该内表面11被布置成除了油膜之外接触转子2;和外表面12,该外表面12与第一表面相对并面向外壳3的盖或法兰的侧面。这两个表面通过由两个圆柱形面13a构成的侧面13连接,两个圆柱形面在排出侧d上的联接区域17和吸入侧s上的联接区域18中连接到彼此。
53.在衬套组件10上设置两个排放通道14,其制成为相应圆柱形面13a上的周向槽。排放通道14从排出侧d上的联接区域17一直延伸到其到达吸入侧s上的两个补偿箱15、16。补偿箱15、16有利地布置在衬套组件10的最大应力h区域中,该区域位于吸入侧s上相对于内表面11靠近的区域中。
54.如在图10中清楚可见的,提供了拦截排放通道14的中间补偿箱15和随后的末端补偿箱16,排放通道14在该末端补偿箱16处中断。
55.补偿箱15、16可以是不同的形状;在本文例示的优选实施例中,补偿箱基本上是平行六面体,其具有与排放通道14的深度基本上相等的深度并且朝向衬套组件10的内表面11延伸。
56.从所述优选构造开始,排放通道14和补偿箱15、16的位置和构造可以借助于以下度量来确定:
[0057]-排放通道14的轴向宽度;
[0058]-每个补偿箱15、16的轴向宽度(优选但非必须相同);
[0059]-排放通道14与衬套组件10的内表面11的距离;
[0060]-每个补偿箱15、16的周向长度(优选但非必须地,末端箱16具有小于中间箱15的长度);
[0061]-两个随后的补偿箱15、16之间的周向距离(优选但非必须大约等于中间箱15的周向长度);
[0062]-箱相对于承载中心轴线的位置。
[0063]
上述度量可以通过数值建模来确定,以根据泵的尺寸和预期用途获得最大载荷再分布,即上述最大应力h区域中的最小表面压力。
[0064]
衬套组件10的上述构造有利于在泵的使用期间排放补偿箱15、16内的处于压力下的流体。这样,在衬套组件10的最大应力区域获得重新对准力fr,其产生对应的重新对准力
矩tr,从而有助于使衬套组件10与泵轴重新对准并重新平衡作用在其上的载荷,由此消除或至少减少局部磨损现象以及由此产生的操作瞬态卡住现象。
[0065]
图11介绍了由图5的图中的补偿箱15、16确定的重新对准力fr和重新对准力矩tr。图11a示出了指示结构的载荷f、力矩t和对应变形d的曲线图。沿着衬套组件10的应力有显著的重新分布,并且在边缘与内表面11的约束反作用力减小。
[0066]
图12示出了由建模软件计算的力线,这些力线是在衬环-转子组的二维模型内产生的。通过与图6中的现有技术模型进行比较,可以注意到,尽管剩余表面部分上的平均压力保持不变,但通过加宽最配合支撑衬套组件10的表面部分,作用力可以更好地分布。
[0067]
由于上述原因,通过进一步计算,最大作用力可以减少约40%。
[0068]
显然,本领域技术人员可以对上述发明进行多种改变和变型,以便满足可能的和特定的需要,所有这些改变和变型都包含在由所附权利要求限定的本发明的保护范围内。