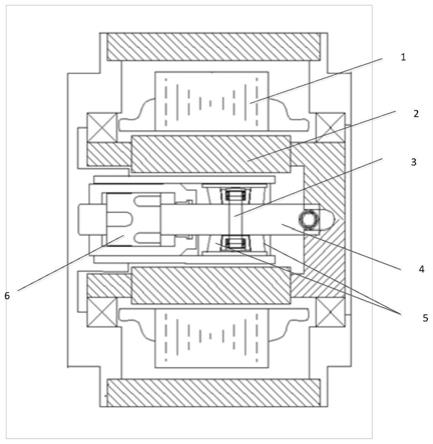
1.本发明涉及电机泵技术领域,尤其涉及单圆锥滚柱二维柱塞电机泵及凸轮轮廓曲面设计方法。
背景技术:2.对电机泵的研究,符合液压技术轻巧集成化、清洁环保、低噪声的发展趋势。振动小噪声低的液压电机泵特别适用于国防军工、航空航天等一些要求低振动低噪声小体积的场合,和深水领域中的需要独立液压源的各种液压工具。也适用于对环境卫生有严格要求的食品加工和精密加工设备领域。
3.二维电机泵主要由电机和二维柱塞泵两大部分组成,设计端面凸轮曲线形成的曲线导轨是二维柱塞泵上关键的部件,滚轮在特殊的轮廓曲面使得柱塞轴向运动和电机驱动下的旋转运动的双向自由度来实现吸排油功能。
4.等加速度曲线滚道目前得到最广泛的应用。基于等接触应力思想的设计方法,在这种曲线导轨的主要区段上,滚动元件与导轨之间的接触应力是均匀的,根据导轨上的接触疲劳剥落凹坑或剥蚀麻斑,都发生在曲线内死点附近的加速区段的起始部位,因此这种设计方法主要采用接触应均匀分布方法进行设计的。但这种曲线的设计计算复杂,加工精度要求高,需要专门的加工工具进行加工,且成本较高。
5.通过等加速曲线凸轮面液压泵的寿命试验,发现滚道上的接触剥落坑或腐蚀点出现在加速段开始处,靠近曲线死点。不同材料的凸轮面经过多次试验,损伤部位相同,说明失效原因不是材料内部局部缺陷等因素。通过进一步分析计算表明,等加速度曲线滚道上的接触应力是不均匀的,且接触应力轨道最高一般在剥落区。
6.其性能和寿命直接在取决于曲线导轨的设计。按照运动学观点和几何学思想的设计方法,不能直接计算和预估其工作寿命,并不能解决整个等加速区段内接触应力不均匀的问题,已日益不能适应技术发展的要求。
技术实现要素:7.为克服上述问题,本发明提供单圆锥滚柱二维柱塞电机泵及凸轮轮廓曲面设计方法。
8.本发明的第一方面提供单圆锥滚柱二维柱塞电机泵,包括电机泵外壳,电机泵外壳内设有转子、定子以及位于转子内部的柱塞泵体;柱塞泵体包括外泵体和内泵体,外泵体具有内腔,内腔中从左至右安装有内泵体和凸轮组件;内泵体的左端面设有吸油孔和排油孔,内泵体内设有缸体,内腔中从左至右安装有内泵体和凸轮组件;内泵体内设有缸体,缸体的外表面设有第一半环形槽和第二半环形槽,吸油孔与第一半环形槽连通,排油孔与第二半环形槽连通;缸体内设有柱塞,柱塞固定连接在泵轴上,且柱塞可沿缸体的轴向作直线往复运动;柱塞的左端与缸体围合成左腔室,柱塞的右端与缸体围合成右腔室,左腔室、右腔室的容积随柱塞的往复运动变化,当柱塞从最左端往最右端轴向运动时,左腔室容积逐
渐变大,右腔室容积逐渐变小;相反,当柱塞从最右端往最左端轴向运动时,右腔室容积逐渐变大,左腔室容积逐渐变小;
9.柱塞的外表面间隔均布有开口方向相反的左配流槽和右配流槽各两个,左配流槽和右配流槽的槽口位置相互错开布置,缸体与左配流槽和右配流槽相对应的位置设有吸油窗口和排油窗口,吸油窗口与第一半环形槽连通,排油窗口与第二半环形槽连通;
10.所述凸轮组件包括左凸轮、右凸轮,左凸轮、右凸轮朝向相对的轴向端面上分别设有凸轮轮廓曲面,凸轮轮廓曲面沿左凸轮、右凸轮轴向的投影呈圆环形,并带有轴向的周期性起伏;左凸轮的凸轮轮廓曲面与右凸轮的凸轮轮廓曲面的相位差90度,左凸轮的凸轮轮廓曲面最高点和最低点分别与右凸轮的凸轮轮廓曲面的最低点和最高点相对应;泵轴上且位于凸轮组件之间的位置固定连接有滚轮组件,滚轮组件包括滚轮架,滚轮架径向穿设泵轴,滚轮架的两端穿出泵轴外并转动连接有滚轮,滚轮与左、右凸轮配合转动;
11.泵轴的右端径向穿设有固定轴,固定轴的两端连接有轴承,泵轴的右端套设有滑套,滑套的右端与转子固定连接;滑套上与轴承相对应的位置的开设有轴向的滑槽,滑槽的左端贯穿滑套;滑槽内设有轴承,轴承可在滑槽内滚动;柱塞在随泵轴转动的同时,在凸轮组件的约束下做直线往复运动;柱塞上的左配流槽和右配流槽分别与缸体上的吸油窗口、排油窗口发生沟通,容积逐渐变大的腔室吸油,容积逐渐减小的腔室排油。
12.进一步,所述凸轮轮廓曲面包括4段曲面,4段曲面包括依次连接的开始区段、加速区段、减速区段、结束区段,开始区段设置在凸轮轮廓曲面的外死点附近,幅角设置在1
°
~3
°
;加速区段为外凸曲面;减速区段为内凹曲面,结束区段设置在凸轮轮廓曲面的内死点附近。
13.本发明的第二个方面提供一种单圆锥滚柱二维柱塞电机泵中凸轮轮廓曲面的设计方法,包括以下步骤:
14.按照基于最小接触应力思想的设计方法,使得输出转矩保持不变,则
[0015][0016][0017][0018][0019]
式中,在直角坐标系中,p为经过滚轮中点的垂直作用力,t为过滚轮中点的水平作用力,n轨道与滚轮间的法向作用力,
[0020]
为滚轮中心沿凸轮运动轨迹的一阶导数,r为滚轮上下底面高的一半,r
′
为滚轮中心的运动轨迹,m为转矩,i为p和n夹角;
[0021]
滚轮曲率半径:
[0022]
r=r
′‑
r
ꢀꢀ
(1.4)
[0023]
对于与凸轮线接触的滚轮接触应力,根据赫兹公式求得,具体如下:
[0024][0025]
式中,e为滚轮间弹性模量,μ为材料泊松比,c为线接触长度,σ为接触应力;求解上列方程式可以得到滚轮中心运动轨迹曲线的各点坐标(a,b),具体如下:
[0026][0027]
根据公式(1.6)设计凸轮的曲面规律。
[0028]
本发明的有益效果是:可以根据曲线的x,y坐标,加工凸轮轮廓曲面规律,在最优凸轮接触应力的凸轮轮廓曲面下,实现柱塞直线左右运动,解决整个等加速区段内接触应力不均匀的问题。具有保持流量稳定,接触应力小,压力脉动小,受力均匀等优点。
附图说明
[0029]
图1是本发明的内部结构示意图。
[0030]
图2是内泵体、凸轮组件和滚轮组件的示意图。
[0031]
图3是左凸轮和滚轮组件的示意图。
[0032]
图4是左、右凸轮的结构示意图。
[0033]
图5是缸体的结构示意图。
[0034]
图6是内泵体和泵轴的结构示意图。
[0035]
图7是图6中a
‑
a向的剖视图。
[0036]
附图标记说明:a、开始区段;b、加速区段;c、减速区段;d、结束区段;1、定子;2、转子;3、滚轮组件;3
‑
1、滚轮;3
‑
2、滚轮架;4、泵轴;5、凸轮组件;6、柱塞;7、内泵体;8、缸体;8
‑
1、吸油孔;8
‑
2、排油孔;8
‑
3、第一半环形槽;8
‑
4、第二半环形槽。
具体实施方式
[0037]
下面将结合附图对本发明专利的技术方案进行清楚、完整地描述,显然,所描述的实施例是本发明一部分实施例,而不是全部的实施例。基于本发明中的实施例,本领域普通技术人员在没有做出创造性劳动前提下所获得的所有其他实施例,都属于本发明保护的范围。
[0038]
在本发明的描述中,需要说明的是,如出现术语“中心”、“上”、“下”、“左”、“右”、“竖直”、“水平”、“内”、“外”等指示的方位或位置关系为基于附图所示的方位或位置关系,仅是为了便于描述本发明和简化描述,而不是指示或暗示所指的装置或元件必须具有特定的方位、以特定的方位构造和操作,因此不能理解为对本发明的限制。此外,如出现术语“第一”、“第二”、“第三”仅用于描述目的,而不能理解为指示或暗示相对重要性。
[0039]
在本发明的描述中,需要说明的是,除非另有明确的规定和限定,如出现术语“安装”、“相连”、“连接”应做广义理解,例如,可以是固定连接,也可以是可拆卸连接,或一体地连接;可以是机械连接,也可以是电连接;可以是直接相连,也可以通过中间媒介间接相连,
可以是两个元件内部的连通。对于本领域的普通技术人员而言,可以具体情况理解上述术语在本发明中的具体含义。
[0040]
参照附图,本发明的第一实施例提供一种单圆锥滚柱二维柱塞电机泵,包括电机泵外壳,电机泵外壳内设有转子2、定子1以及位于转子2内部的柱塞泵体;柱塞泵体包括外泵体和内泵体,外泵体具有内腔,内腔中从左至右安装有内泵体7和凸轮组件5;内泵体7的左端面设有吸油孔8
‑
1和排油孔8
‑
2,内泵体7内设有缸体8,缸体8的外表面设有第一半环形槽8
‑
3和第二半环形槽8
‑
4,吸油孔8
‑
1与第一半环形槽8
‑
3连通,排油孔8
‑
2与第二半环形槽8
‑
4连通;缸体8内设有柱塞6,柱塞6固定连接在泵轴4上,且柱塞6可沿缸体8的轴向作直线往复运动;柱塞6的左端与缸体8围合成左腔室,柱塞6的右端与缸体8围合成右腔室,左腔室、右腔室的容积随柱塞6的往复运动变化,当柱塞6从最左端往最右端轴向运动时,左腔室容积逐渐变大,右腔室容积逐渐变小;相反,当柱塞6从最右端往最左端轴向运动时,右腔室容积逐渐变大,左腔室容积逐渐变小;
[0041]
柱塞6的外表面间隔均布有开口方向相反的左配流槽a、c和右配流槽b、d各两个,左配流槽a、c和右配流槽b、d的槽口位置相互错开布置,缸体与左配流槽a、c和右配流槽b、d相对应的位置设有吸油窗口o、m和排油窗口q、n,吸油窗口o、m与第一半环形槽连通8
‑
3,排油窗口q、n与第二半环形槽连通8
‑
4;
[0042]
所述凸轮组件5包括左凸轮4
‑
1、右凸轮4
‑
2,左凸轮4
‑
1、右凸轮4
‑
2朝向相对的轴向端面上分别设有凸轮轮廓曲面,凸轮轮廓曲面沿左凸轮4
‑
1、右凸轮4
‑
2轴向的投影呈圆环形,并带有轴向的周期性起伏;左凸轮4
‑
1的凸轮轮廓曲面与右凸轮4
‑
2的凸轮轮廓曲面的相位差90度,左凸轮4
‑
1的凸轮轮廓曲面最高点和最低点分别与右凸轮4
‑
2的凸轮轮廓曲面的最低点和最高点相对应;
[0043]
凸轮轮廓曲面包括4段曲面,4段曲面包括依次连接的开始区段、加速区段、减速区段和结束区段。
[0044]
其中,开始区段a设置在凸轮轮廓曲面的外死点附近。在此区段内,凸轮的运动速度为零,减少“闭油现象”和降低工作噪声。考虑到加工分度误差,幅角设置在1
°
~3
°
。
[0045]
加速区段b是决定凸轮轮廓曲面曲面工作寿命的关键区段。在此区段,滚轮与凸轮轮廓曲面之间接触应力最大,是发生接触疲劳剥落破坏的主要区段。滚轮在此区段内完成加速运动,相对于凸轮轮廓曲面中心,这段曲线是外凸的。
[0046]
减速区段c内,滚轮完成减速运动。由于这个区段曲线的形状是内凹的,凸轮轮廓曲面与滚轮之间的接触应力值较小。根据输出转矩的脉动量为零,改善了凸轮轮廓曲面的接触应力的尖峰区。
[0047]
结束区段d设置在凸轮轮廓曲面的内死点附近,在此区段内,滚轮的运动速度为零,与开始区作用一样。
[0048]
泵轴4上且位于凸轮组件5之间的位置固定连接有滚轮组件,滚轮组件3包括滚轮架3
‑
2,滚轮架3
‑
2径向穿设泵轴4,滚轮架3
‑
2的两端穿出泵轴3外并转动连接有滚轮3
‑
1,滚轮与左、右凸轮4
‑
1、4
‑
2配合转动;左、右凸轮4
‑
1、4
‑
2和滚轮3
‑
1之间采用润滑脂润滑方式,可以防止滴油和溅油污损产品,表面上粘附力强,可以保护长时间不锈蚀。用润滑脂润滑时,不需要复杂的密封装置和供油系统即可满足要求。
[0049]
泵轴4的右端径向穿设有固定轴,固定轴的两端连接有轴承,泵轴4的右端套设有
滑套,滑套的右端与转子固定连接;滑套上与轴承相对应的位置的开设有轴向的滑槽,滑槽的左端贯穿滑套;滑槽内设有轴承,轴承可在滑槽内滚动;柱塞6在随泵轴4转动的同时,在凸轮组件5的约束下做直线往复运动;柱塞6上的左配流槽和右配流槽分别与缸体上的吸油窗口、排油窗口发生沟通,容积逐渐变大的腔室吸油,容积逐渐减小的腔室排油。
[0050]
本发明的第二个实施例提供一种单圆锥滚柱二维柱塞电机泵中凸轮轮廓曲面的设计方法,包括以下步骤:
[0051]
按照基于最小接触应力思想的设计方法,使得输出转矩保持不变,则
[0052][0053][0054][0055][0056]
式中,在直角坐标系中,p为经过滚轮中点的垂直作用力,t为过滚轮中点的水平作用力,n轨道与滚轮间的法向作用力,
[0057]
为滚轮中心沿凸轮运动轨迹的一阶导数,r为滚轮上下底面高的一半,r
′
为滚轮中心的运动轨迹,m为转矩,i为p和n夹角;
[0058]
滚轮曲率半径:
[0059]
r=r
′‑
r
ꢀꢀ
(1.4)
[0060]
对于与凸轮线接触的滚轮接触应力,根据赫兹公式求得,具体如下:
[0061][0062]
式中,e为滚轮间弹性模量,μ为材料泊松比,c为线接触长度,σ为接触应力;求解上列方程式可以得到滚轮中心运动轨迹曲线的各点坐标(a,b),具体如下:
[0063][0064]
根据公式(1.6)设计凸轮的曲面规律。
[0065]
具体的工作原理为:将转子与泵轴通过滑套连接在一起,滚轮分别与左、右凸轮配合转动,以至于柱塞实现直线运动;当电机通过传动轴将扭矩传递给柱塞促使周向转动,柱塞的外表面周向分布有左配流槽和右配流槽,当液压油从进油孔入,经过第一半环形槽进入缸体内,柱塞的表面上开设的四个左配流槽和右配流槽与进油孔和排油孔相互配油,通过柱塞的双自由度进行吸油和排油,由于凸轮的约束下,柱塞开始向右运动,油液从进油孔流入缸体内经过两个进油窗口,进入左配流槽a、c后,左侧腔体容积变大,进行吸油,当柱塞旋转一定角度后,左侧腔体油液经排油窗口、第二半环形槽从排油口流出,同时,右侧容积
逐渐增大,油液进入右配流槽b、d进行吸油,左侧容腔受挤压而容积减小,在电机连续转动的工作下,与泵排油孔相连通的窗口持续排油,与进油口相连通的窗口持续吸油,从而实现柱塞在做左右轴向运动的同时也能做旋转周向转动的直线往复运动。利用柱塞平和旋转运动的双向自由度来实现吸排油功能。
[0066]
本说明书实施例所述的内容仅仅是对发明构思的实现形式的列举,本发明的保护范围不应当被视为仅限于实施例所陈述的具体形式,本发明的保护范围也及于本领域技术人员根据本发明构思所能够想到的等同技术手段。