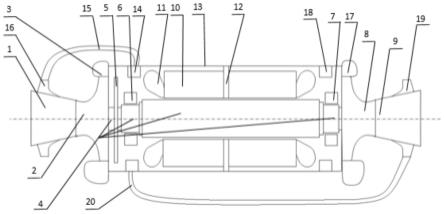
1.本发明涉及气浮空气压缩及输送技术领域,具体涉及一种双侧自吸冷却双叶轮气浮高速直驱离心鼓风机及工作方法。
背景技术:2.每年鼓风机、压缩机、泵等设备的用电量约占当年发电量的三分之一,采用新技术提高上述设备的能效,将直接降低企业用电支出和碳排放指标。现有200kw及以上功率等级的鼓风机中,气浮直驱鼓风机具有效率高、无油润滑的优点,成为替换广泛应用的传统罗茨风机的不二之选。
3.同时,较大功率等级的气浮直驱鼓风机存在高速直驱电机长时间运行散热不畅的难题;同时由于流量的增大,如果采用大比转速单个离心叶轮设计方案叶轮的转速过低,气浮轴承极易损毁。上述两个因素给200kw及以上功率等级的气浮鼓风机设备的研发设计和运行安全带来了巨大风险,极大限制了高效率气浮鼓风机设备的使用。
4.由于气浮直驱鼓风机散热技术和高比转速离心叶轮设计技术尚不成熟,已发生过多起200kw中大功率等级气浮直驱离心鼓风机因高速直驱电机超温烧毁或者气浮轴承抱轴事故,给用户工业生产带来相当严重的经济损失。目前,尚无有效的技术方案解决上述难题。
技术实现要素:5.本发明的目的就在于为了解决上述问题而提供一种双侧自吸冷却双叶轮气浮高速直驱离心鼓风机及工作方法。
6.本发明通过以下技术方案来实现上述目的:
7.双侧自吸冷却双叶轮气浮高速直驱离心鼓风机,包括第一进气管道1、第一离心叶轮2、第一排气蜗壳3、永磁同步电机主轴4、气浮推力盘5、第一气浮径向轴承6、第二气浮径向轴承7、电机冷气进口环腔18、第一抽吸管路15、定子铁芯10、定子绕组11、固定结构12、永磁同步电机外壳13、电机冷气出口环腔14、第一抽吸环腔16、第二进气管道9、第二离心叶轮8、第二排气蜗壳17、第二抽吸管路20和第二抽吸环腔19,其中,第一离心叶轮2、气浮推力盘5、第二离心叶轮8依次固定在永磁同步电机主轴4上,永磁同步电机主轴4的径向轴承支撑处分别由第一气浮径向轴承6和第二气浮径向轴承7支撑,第一进气管道1一端通过第一离心叶轮2外部管道与第一排气蜗壳3相连,第二进气管道9一端通过第二离心叶轮8外部管道与第二排气蜗壳17相连,电机冷气出口环腔14和电机冷气进口环腔18均位于永磁同步电机外壳13内侧以及在定子绕组11的两侧,电机冷气进口环腔18和电机冷气出口环腔14均与永磁同步电机外壳13构成的腔室连通,第一抽吸管路15的一端与第一抽吸环腔16入口相连,另一端与电机冷气出口环腔14连通,第二抽吸管路20的一端与第二抽吸环腔19入口相连,另一端与电机冷气出口环腔14连通,定子绕组11固定于定子铁芯10上,定子铁芯10通过固定结构12固定在永磁同步电机外壳13上,永磁同步电机主轴4的主轴中心线与定子铁芯10
和定子绕组11的中心线重合。
8.所述的第一抽吸环腔16的过流断面面积从入口到出口呈现逐渐增大的趋势,出口过流断面面积是出口过流断面面积的3倍及以上,第一抽吸环腔16的内表面分别与第一抽吸管路15的出口表面、第一进气管道1侧面光滑渐变过渡,曲率半径大于10厘米。
9.所述的第二抽吸环腔19的过流断面面积从入口到出口呈现逐渐增大的趋势,出口过流断面面积是出口过流断面面积的3倍及以上,第二抽吸环腔19的内表面分别与第二抽吸管路20的出口表面、第二进气管道9侧面光滑渐变过渡,曲率半径大于10厘米。
10.所述的第一气浮径向轴承6和第二气浮径向轴承7为动压空气悬浮轴承,转速在1.6万转每分钟至12万转每分钟。
11.所述的永磁同步电机主轴4由主轴支撑段、永磁体和高温合金护套组成,高温合金护套位于永磁体的外侧。
12.所述的双侧自吸冷却双叶轮气浮高速直驱离心鼓风机的主流工质的工作过程是指,主流工质分流成相等质量流量的两部分流体,第一部分流体通过第一进气管道1进入第一离心叶轮2,经过第一离心叶轮2提升压力后从第一排气蜗壳3的出口排出,与第二部分流体汇合进入设备总排气管路,第二部分流体通过第二进气管道19进入第二离心叶轮8,经过第二离心叶轮8提升压力后从第二排气蜗壳17的出口排出,与第一部分流体汇合进入设备总排气管路。
13.所述的双侧自吸冷却双叶轮气浮高速直驱离心鼓风机的永磁同步电机的冷却气体工作过程是指,在第一离心叶轮2和第二离心叶轮8高速旋转产生的抽吸作用下,永磁同步电机的冷却气体从电机冷气进口环腔18进入永磁同步电机外壳13内部腔室,通过永磁同步电机主轴4、定子铁芯10、定子绕组11与永磁同步电机外壳13之间的间隙,带走永磁同步电机工作时产生的热量,流经电机冷气出口环腔14后分流成为两部分冷却流体,第一部分冷却流体先后经过第一抽吸管路15和第一抽吸环腔16进入第一进气管道1,随后汇入主流的第一部分流体,第二部分冷却流体先后经过第二抽吸管路20和第二抽吸环腔19进入第二进气管道9,随后汇入主流的第二部分流体。
14.本发明的有益效果在于:
15.本发明提出了一种造价低、可操作性高的双侧自吸冷却双叶轮气浮高速直驱离心鼓风机及工作方法。本发明将主流流量一分为二,设计两个完全相同的高转速叶轮替代原设计方案中的一个高比转速叶轮,确保了设计转速在气浮轴承安全转速范围内且满足主流流体高效率压缩,在此基础上,开展了高速同步永磁电机设计和电机冷却方案的设计,本发明充分了利用两个主流离心叶轮高速运转时产生的真空抽吸力,通过进气管道、抽吸管路、电机冷气出口环腔和抽吸环腔构成的通道结构,最大限度的提高通过高速直驱电机转子和定子间的冷空气流速和流量,增加了高速直驱电机转子和定子的冷却效率,不需要增加电机冷却离心叶轮,降低了加工成本、主轴轴向长度和电机散热功耗,提升了设备整体能效水平。本发明能有效带走气浮直驱离心鼓风机长时间运行过程中的电机产生的热量,防止气浮直驱离心鼓风机发生电机烧毁的事故。此外,抽吸环腔的过流断面面积从入口到出口逐渐增大以及抽吸环腔内表面分别与抽吸管路出口表面、进气管道侧面光滑渐变过渡均可降低流动损失,增强对冷气的抽吸作用;本发明采用动压空气悬浮轴承,最大限度降低了设备运行过程中的摩擦损耗,同时不增加供气装置;本发明的永磁同步电机主轴由高温合金护
套对永磁体进行固定和保护,提高了设备的安全性。
附图说明
16.图1是本发明双侧自吸冷却双叶轮气浮高速直驱离心鼓风机的示意图。
具体实施方式
17.下面结合附图对本发明作进一步说明:
18.如图1所示,双侧自吸冷却双叶轮气浮高速直驱离心鼓风机,包括第一进气管道1、第一离心叶轮2、第一排气蜗壳3、永磁同步电机主轴4、气浮推力盘5、第一气浮径向轴承6、第二气浮径向轴承7、电机冷气进口环腔18、第一抽吸管路15、定子铁芯10、定子绕组11、固定结构12、永磁同步电机外壳13、电机冷气出口环腔14、第一抽吸环腔16、第二进气管道9、第二离心叶轮8、第二排气蜗壳17、第二抽吸管路20和第二抽吸环腔19,其中,第一离心叶轮2、气浮推力盘5、第二离心叶轮8依次固定在永磁同步电机主轴4上,永磁同步电机主轴4的径向轴承支撑处分别由第一气浮径向轴承6和第二气浮径向轴承7支撑,第一进气管道1一端通过第一离心叶轮2外部管道与第一排气蜗壳3相连,第二进气管道9一端通过第二离心叶轮8外部管道与第二排气蜗壳17相连,电机冷气出口环腔14和电机冷气进口环腔18均位于永磁同步电机外壳13内侧以及在定子绕组11的两侧,电机冷气进口环腔18和电机冷气出口环腔14均与永磁同步电机外壳13构成的腔室连通,第一抽吸管路15的一端与第一抽吸环腔16入口相连,另一端与电机冷气出口环腔14连通,第二抽吸管路20的一端与第二抽吸环腔19入口相连,另一端与电机冷气出口环腔14连通,定子绕组11固定于定子铁芯10上,定子铁芯10通过固定结构12固定在永磁同步电机外壳13上,永磁同步电机主轴4的主轴中心线与定子铁芯10和定子绕组11的中心线重合。
19.作为本发明的优选实施方式,所述的第一抽吸环腔16的过流断面面积从入口到出口呈现逐渐增大的趋势,出口过流断面面积是出口过流断面面积的3倍及以上,第一抽吸环腔16的内表面分别与第一抽吸管路15的出口表面、第一进气管道1侧面光滑渐变过渡,曲率半径大于10厘米。
20.作为本发明的优选实施方式,所述的第二抽吸环腔19的过流断面面积从入口到出口呈现逐渐增大的趋势,出口过流断面面积是出口过流断面面积的3倍及以上,第二抽吸环腔19的内表面分别与第二抽吸管路20的出口表面、第二进气管道9侧面光滑渐变过渡,曲率半径大于10厘米。
21.作为本发明的优选实施方式,所述的第一气浮径向轴承6和第二气浮径向轴承7为动压空气悬浮轴承,转速在1.6万转每分钟至12万转每分钟。
22.作为本发明的优选实施方式,所述的永磁同步电机主轴4由主轴支撑段、永磁体和高温合金护套组成,高温合金护套位于永磁体的外侧。
23.所述主流工质的工作过程是指,主流工质分流成相等质量流量的两部分流体,第一部分流体通过第一进气管道1进入第一离心叶轮2,经过第一离心叶轮2提升压力后从第一排气蜗壳3的出口排出,与第二部分流体汇合进入设备总排气管路,第二部分流体通过第二进气管道19进入第二离心叶轮8,经过第二离心叶轮8提升压力后从第二排气蜗壳17的出口排出,与第一部分流体汇合进入设备总排气管路。
24.所述永磁同步电机的冷却气体工作过程是指,在第一离心叶轮2和第二离心叶轮8高速旋转产生的抽吸作用下,永磁同步电机的冷却气体从电机冷气进口环腔18进入永磁同步电机外壳13内部腔室,通过永磁同步电机主轴4、定子铁芯10、定子绕组11与永磁同步电机外壳13之间的间隙,带走永磁同步电机工作时产生的热量,流经电机冷气出口环腔14后分流成为两部分冷却流体,第一部分冷却流体先后经过第一抽吸管路15和第一抽吸环腔16进入第一进气管道1,随后汇入主流的第一部分流体,第二部分冷却流体先后经过第二抽吸管路20和第二抽吸环腔19进入第二进气管道9,随后汇入主流的第二部分流体。
25.本发明的技术方案不限于上述具体实施例的限制,凡是根据本发明的技术方案做出的技术变形,均落入本发明的保护范围之内。