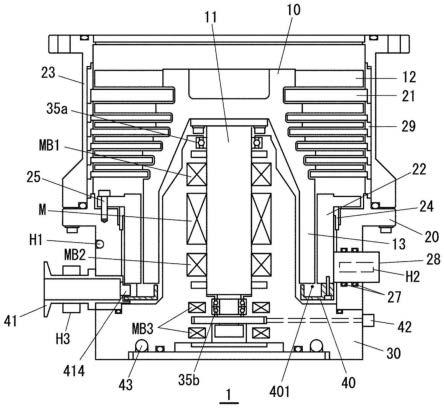
1.本发明涉及一种真空泵。
背景技术:2.涡轮分子泵作为各种半导体制造装置的排气泵而使用,但当在蚀刻工艺等中进行排气时,反应生成物会堆积于泵内部。半导体制造装置中一般使用包括涡轮泵部及螺纹槽泵部的涡轮分子泵,但由于反应生成物越靠近低真空侧越容易堆积,因此大多采用将螺纹槽泵部的定子侧加热至高温的结构。然而,虽因定子加热而螺纹槽泵部中的生成物堆积得以减少,但存在生成物堆积于比螺纹槽泵部更靠下游侧的排出气通路的问题。
3.例如,在专利文献1所记载的发明中,为了抑制在下游侧的排出气通路的一部分即排气管的生成物堆积,采用了将固定于定子的管插入至排气口的内部的结构。排出气通过管而被排出至泵外,因此可防止在排气口内周面的生成物堆积。
4.[现有技术文献]
[0005]
[专利文献]
[0006]
[专利文献1]日本专利特开2016-176339号公报
技术实现要素:[0007]
[发明所要解决的问题]
[0008]
然而,由螺纹槽泵部排出的气体成为被排出至螺纹槽泵部的下游侧流路后流入至管的结构。因此,存在生成物堆积于所述管与螺纹槽泵部之间的下游侧流路的内周面的问题。即,在专利文献1所记载的真空泵中,防止了在排气口内周面的生成物堆积,但生成物堆积于从螺纹槽泵部连至排气口的排气通路(比螺纹槽泵部更靠下游侧的流路)的内周面。
[0009]
[解决问题的技术手段]
[0010]
本发明的形态的真空泵包括:转子,形成有多级旋转叶片及转子圆筒部;定子,形成有多级固定叶片、以及与所述转子圆筒部经由预定的空隙配置的定子圆筒部;第一加热部,将所述定子圆筒部加热至抑制生成物堆积的温度;排气管,设置于收容所述转子及所述定子的框体,将通过所述转子及所述定子排出的气体排出至所述框体的外部;第二加热部,将所述排气管加热至抑制生成物堆积的温度;以及气体通路容器,配置于所述框体内,具有从所述转子圆筒部与所述定子圆筒部的空隙排出的气体流入的流入口、及使流入的气体向所述排气管流出的流出口,且被加热至抑制生成物堆积的温度,其中,所述排气管的气体流入侧端部经由间隙插入至所述气体通路容器的所述流出口。
[0011]
[发明的效果]
[0012]
根据本发明,可减少在形成从排气功能部至排气管的气体通路的构件的表面的生成物堆积。
附图说明
[0013]
图1是表示本发明的真空泵的实施方式的图,且表示涡轮分子泵的剖面。
[0014]
图2是气体通路容器的平面图。
[0015]
图3是排气口的剖面图。
[0016]
图4是图3的a箭视图。
[0017]
图5是对配置有气体通路容器的区域中的气体的流动进行说明的轴向剖面图。
[0018]
图6是图5的c1-c1剖面图。
[0019]
图7是表示比较例的轴向剖面图。
[0020]
图8是图7的c1-c1剖面图。
[0021]
图9(a)~图9(c)是表示变形例1~变形例3的图。
[0022]
[符号的说明]
[0023]
1:涡轮分子泵
[0024]
10:转子
[0025]
11:转子轴
[0026]
12:旋转叶片
[0027]
13:转子圆筒部
[0028]
20:第二泵壳体
[0029]
21:固定叶片
[0030]
22:定子圆筒部
[0031]
23:第一泵壳体
[0032]
24:绝热构件
[0033]
25:螺栓
[0034]
27:o形环
[0035]
28:加热部
[0036]
29:间隔件
[0037]
30:基座
[0038]
35a、35b:机械轴承
[0039]
40:气体通路容器
[0040]
41:排气口
[0041]
42:吹扫气体导入部
[0042]
43:冷却管
[0043]
401:流入口
[0044]
402:外周壁
[0045]
403:内周壁
[0046]
404:底面壁
[0047]
405:流出孔
[0048]
406:螺栓孔
[0049]
406a:沉孔
[0050]
407、414:插入部
[0051]
410:凸缘
[0052]
411:第一管部
[0053]
412:第二管部
[0054]
414:插入部
[0055]
414a:圆管
[0056]
415:凸部
[0057]
b1、b2、b3:区域
[0058]
g:空隙尺寸
[0059]
g:排出气
[0060]
h1~h3:加热器
[0061]
l:长度尺寸
[0062]
m:马达
[0063]
mb1、mb2:磁性轴承(径向磁性轴承)
[0064]
mb3:磁性轴承(轴向磁性轴承)
[0065]
pg:吹扫气体
[0066]
r:面
[0067]
t1、t2、t3:温度
具体实施方式
[0068]
以下,参照图对用于实施本发明的形态进行说明。图1是表示本发明的真空泵的实施方式的图,且表示涡轮分子泵的剖面。涡轮分子泵1包括形成有多级旋转叶片12及转子圆筒部13的转子10、以及形成有多级固定叶片21及定子圆筒部22的定子。在第一泵壳体23的内侧,多级固定叶片21以与多级旋转叶片12对应地层叠的方式进行配置。由多级旋转叶片12及多级固定叶片21构成涡轮泵部。沿泵轴向层叠的多级固定叶片21分别经由间隔件29而配置于第二泵壳体20上。在旋转叶片12及固定叶片21分别形成有沿周向配置的多个涡轮叶片。第一泵壳体23利用螺栓固定于第二泵壳体20,第二泵壳体20利用未图示的固定部件固定于基座30。
[0069]
在转子圆筒部13的外周侧,经由预定的空隙配置有圆筒形状的定子圆筒部22。定子圆筒部22经由热传导率小的绝热构件24而载置于第二泵壳体20上,且通过螺栓25螺固于第二泵壳体20。在转子圆筒部13的外周面或定子圆筒部22的内周面的任一者形成有螺纹槽,由转子圆筒部13及定子圆筒部22构成螺纹槽泵部。
[0070]
在定子圆筒部22的下端螺固有用于防止生成物堆积于基座30及第二泵壳体20的气体通路容器40。设置于第二泵壳体20的排气口41的壳体侧端部(图示右侧的端部)插入至气体通路容器40中。通过由旋转叶片12与固定叶片21构成的涡轮泵部、以及由转子圆筒部13与定子圆筒部22构成的螺纹槽泵部排出的气体流入至气体通路容器40后,从排气口41排出。
[0071]
在转子10固定有转子轴11,所述转子轴11由径向磁性轴承mb1、径向磁性轴承mb2及轴向磁性轴承mb3磁悬浮支承,并由马达m旋转驱动。当磁性轴承mb1~磁性轴承mb3不运转时,转子轴11由机械轴承35a、机械轴承35b支承。此外,在本实施方式中,第二泵壳体20与
基座30为分体,但也可为第二泵壳体20与基座30一体形成的结构。
[0072]
在设置有马达m或磁性轴承mb1~磁性轴承mb3等电气零件的基座30,为了防止因排出的工艺气体进入而引起的腐蚀等不良影响,而设置有用于将惰性气体等吹扫气体导入基座30内的吹扫气体导入部42。导入至基座30内的吹扫气体通过图示上侧的机械轴承35a的间隙,且通过基座30与转子10的间隙而到达螺纹槽泵部的排气侧,并从排气口41排出至泵外。
[0073]
在本实施方式中,第二泵壳体20及基座30、定子圆筒部22、以及排气口41分别被控制为不同的温度。第二泵壳体20及基座30通过设置于第二泵壳体20的加热器h1及设置于基座30的冷却管43被控制为温度t1。在定子圆筒部22设置有包括加热器h2的加热部28,且被控制为温度t2。排气口41通过加热器h3被控制为温度t3。
[0074]
为了抑制生成物堆积,而将面向所排出的工艺气体的通路的定子圆筒部22的温度t2及排气口41的温度t3控制为比较高的温度。温度t2、温度t3是考虑到工艺气体的蒸气压与温度的关系、高速旋转的转子圆筒部13的蠕变应变等而设定。就工艺气体的蒸气压与温度的关系而言,越是配置于压力高的(低真空)区域的零件,越需要设为高温。因此,设定为t3》t2。
[0075]
另一方面,不面向排出气的通路的基座30及第二泵壳体20的温度t1被控制为比定子圆筒部22及排气口41的温度t2、温度t3低的温度。特别是,由于在基座30设置有马达m或磁性轴承mb1~磁性轴承mb3等电气零件,因此无法随意升高温度t1,为了抑制因电气零件自身的发热及加热器加热的影响引起的电气零件的过度的温度上升,而设置有供冷媒流动的冷却管43。
[0076]
对定子圆筒部22进行加热的加热部28以从外周侧向内周侧贯通第二泵壳体20的方式设置。插入至第二泵壳体20的内部空间的加热部28的前端与定子圆筒部22的外周面热接触。加热部28的后端露出至基座30的外部,加热部28与基座30的间隙由o形环27密封。
[0077]
图2是表示安装于定子圆筒部22的下端的气体通路容器40的图,且为从定子侧观察的平面图。气体通路容器40为环状的容器,且具有固定于定子圆筒部22的外周壁402、内周壁403及底面壁404。在外周壁402形成有多个具有沉孔406a的螺栓孔406。利用所述螺栓孔406将气体通路容器40的外周壁402固定于定子圆筒部22的下端面。
[0078]
气体通路容器40的与定子圆筒部22相向的天花板区域(外周壁402与内周壁403之间的区域)成为由螺纹槽泵部(转子圆筒部13及定子圆筒部22)排出的气体流入的圆环状的开口(以下称为流入口)401。在外周壁402,在排气口41(参照图1)相向的位置形成有作为隧道状的通路的流出孔405。从流入口401流入至气体通路容器40内的气体从流出孔405向排气口41排出,进而从排气口41排出至泵外。
[0079]
图3、图4是说明排气口41的形状的图,图3是排气口41的剖面图,图4是图3的a箭视图。此外,在图4中,以双点划线表示供定子圆筒部22以及排气口41的前端部分插入的气体通路容器40。排气口41包括用于将排气口41固定于第二泵壳体20的凸缘410。排气口41具有凸缘410的插入至图示右侧的泵内的第一管部411、及露出至凸缘410的图示左侧的泵外的第二管部412。如图1所示,在第二管部412装设有加热器h3。在第一管部411的前端设置有插入至气体通路容器40的流出孔405内的插入部414。
[0080]
如根据图4的a箭视图可知,插入部414是删除以从凸缘410突出的方式形成的圆管
414a的施加有阴影线的部分h1、部分h2而残留的部分。此外,删除部分h1是与定子圆筒部22相干涉的部分,删除部分h2是与气体通路容器40的底面壁404相干涉的部分。插入部414在与形成于外周壁402的流出孔405的壁部之间空开微小的间隙而插入。在插入部414的图示下侧形成有凸部415。所述凸部415空开间隙而配置于流出孔405的底部,即底面壁404的下侧。
[0081]
图5、图6是对气体通路容器40及排气口41中的气体的流动进行说明的图。图5示出了与图1的情况相同的轴向剖面,图6是图5的c1-c1剖面图。在图5中,实线箭头表示排出气g的流动,虚线箭头表示吹扫气体pg的流动。由于气体通路容器40固定于被控制为温度t2的定子圆筒部22,因此成为与定子圆筒部22大致同一温度。此外,也可代替将气体通路容器40固定于定子圆筒部22进行加热,而设为使加热部28与定子圆筒部22及气体通路容器40两者接触的结构,利用加热部28直接加热气体通路容器40。另外,也可利用与加热部28不同的另一加热部对气体通路容器40进行加热,以使气体通路容器40成为与定子圆筒部22大致同一温度。
[0082]
气体通路容器40是为了防止基座30及第二泵壳体20的面相对于从螺纹槽泵部排出的气体的流动露出而设置。在流出孔405插入有排气口41的泵侧前端(第一管部411的插入部414)。因此,从螺纹槽泵部(转子圆筒部13及定子圆筒部22)排出的排出气g从流入口401流入至气体通路容器40内,且在不接触基座30及第二泵壳体20的情况下通过气体通路容器40内,而从插入至流出孔405的插入部流入至第一管部411。
[0083]
排气口41与定子圆筒部22由各自的加热器控制为不同的温度t3、温度t2(《t3)。因此,在图5、图6的区域b1、区域b2中,在排气口41的第一管部411及插入部414与定子圆筒部22及气体通路容器40之间以彼此不接触的方式形成有微小的间隙。通过设为此种结构,防止温度不同的排气口41与定子圆筒部22之间的热移动,提高了将排气口41与定子圆筒部22控制为不同的目标温度t3、目标温度t2时的控制稳定性。
[0084]
在第一管部411与气体通路容器40的连接部分,为了不相互接触,第一管部411的插入部414空开微小的间隙插入至在外周壁402形成为隧道状的流出孔405内。因此,可减小插入部414与流出孔405的间隙空间对气体的传导,可将从间隙泄漏的排出气g的量抑制得小。例如,在将间隙尺寸设为g,将插入部414的插入量设为l,且l=α
·
g的情况下,通过将α的大小设定为大概2以上,可充分减小气体泄漏量(例如,设定为α=2、g=1)。在区域b2中,在气体通路容器40的底面壁404的图示下侧配置有凸部415,插入部414及凸部415与底面壁404之间的间隙成为迷宫那样的结构,从而可进一步减小排出气g向气体通路容器40的周围区域的泄漏。
[0085]
如此,在本实施方式中,由于设为设置气体通路容器40,将第一管部411的插入部414插入至气体通路容器40的隧道状的流出孔405的结构,因此可充分减小经由插入部分的间隙的气体的泄漏。其结果,可极力抑制排出气g与基座30及第二泵壳体20的内周面的接触,可将在它们的内周面的生成物堆积抑制得小。
[0086]
进而,从吹扫气体导入部42导入至基座30内的吹扫气体pg如虚线箭头那样在转子圆筒部13与基座30的间隙中向下方流动,且充满于在螺纹槽泵部的排气侧配置的气体通路容器40的周围区域。所述吹扫气体pg通过气体通路容器40的内周壁403与转子圆筒部13的间隙、区域b1、区域b2的间隙而进入气体通路容器40内,通过排气口41而排出至泵外。因此,
可通过从间隙流入的吹扫气体pg来阻止排出气g从区域b1、区域b2的间隙漏出至气体通路容器40的外部,从而可更有效地防止生成物堆积于基座30及第二泵壳体20的内周面。
[0087]
图7、图8示出了未将第一管部411的前端插入至气体通路容器40内的情况的一例作为比较例。图7是与图5同样的轴向剖面图,图8是图7的c1-c1剖面图。在比较例的情况下,由于第一管部411未插入至气体通路容器40中,区域b3中的第一管部411与气体通路容器40的间隙比较大,因此排出气容易从间隙泄漏至基座30及第二泵壳体20。因此,生成物堆积于它们的内周面。特别是在由冷却管43冷却的基座30的接近间隙的面r容易堆积生成物。另外,与图5的情况同样地,即便将吹扫气体pg导入至螺纹槽泵部的排气侧,由于间隙大,由流入至排气口41的吹扫气体pg带来的泄漏阻止效果也变低,导致生成物容易堆积于间隙附近的内周面。
[0088]
在实施方式中,设为导入至基座30的马达配置空间的吹扫气体pg绕到螺纹槽泵部的排气侧的结构,但吹扫气体供给结构并不限定于此,例如,亦可设为将吹扫气体pg直接导入至螺纹槽泵部的排气侧的结构。
[0089]
(变形例)
[0090]
图9(a)~图9(c)是表示流出孔405的变形例的图。在图9(a)所示的变形例1中,在外周壁402形成剖面形状为圆形的流出孔405,且插入排气口41的第一管部411的前端部分。第一管部411的插入量为上文所述的l,第一管部411与流出孔405的间隙尺寸为上文所述的g。
[0091]
在图9(b)所示的变形例2中,以从薄的外周壁402向外周侧突出的方式形成插入部407,所述插入部407形成有隧道状的流出孔405。通过使外周壁402变薄,可减轻气体通路容器40的重量。当然,也可将插入部407形成为向外周壁402的内周侧突出。
[0092]
在图9(c)所示的变形例中,示出设为非隧道状的流出孔405的情况。在薄的外周壁402形成流出孔405,将排气口41的第一管部411以其前端向容器内突出的方式插入至所述流出孔405中。在变形例3的情况下,与流出孔405并非如变形例1、变形例2那样为隧道状的情况相比,气体的泄漏量更大,但由于为插入结构,因此与图7、图8的比较例的情况相比,可减少气体泄漏量。
[0093]
本领域技术人员理解,所述例示性的实施方式及变形例为以下形态的具体例。
[0094]
[1]一形态的真空泵包括:转子,形成有多级旋转叶片及转子圆筒部;定子,形成有多级固定叶片、以及与所述转子圆筒部经由预定的空隙配置的定子圆筒部;第一加热部,将所述定子圆筒部加热至抑制生成物堆积的温度;排气管,设置于收容所述转子及所述定子的框体,将通过所述转子及所述定子排出的气体排出至所述框体的外部;第二加热部,将所述排气管加热至抑制生成物堆积的温度;以及气体通路容器,配置于所述框体内,具有从所述转子圆筒部与所述定子圆筒部的空隙排出的气体流入的流入口、及使流入的气体向所述排气管流出的流出口,且被加热至抑制生成物堆积的温度,其中,所述排气管的气体流入侧端部经由间隙插入至所述气体通路容器的所述流出口。
[0095]
特别是,由于气体从转子圆筒部13与定子圆筒部22的空隙排出的区域为低真空,因此容易在基座30或第二泵壳体20的内周面产生生成物堆积,但通过设置经加热的气体通路容器,可抑制在基座30或第二泵壳体20的内周面的生成物堆积。例如,如图5所示,第一管部411的前端的插入部414插入至气体通路容器40的流出孔405中。通过设为此种插入结构,
可减少排出气从插入部414与流出孔405的间隙的漏出,从而可抑制在基座30或第二泵壳体20的内周面的生成物堆积。
[0096]
[2]根据所述[1]所记载的真空泵,其中所述流出口为隧道状的孔,
[0097]
所述排气管的气体流入侧端部以在与所述隧道状的孔的壁面之间形成间隙的方式插入。
[0098]
例如,如图5、图6所示,流出孔405是以贯通厚壁的外周壁402的方式形成的隧道状的孔。因此,间隙空间的长度尺寸l比空隙尺寸g大,所以可增大对气体的传导,从而可进一步减少经由间隙的气体泄漏。
[0099]
[3]根据所述[1]或[2]所记载的真空泵,其中所述气体通路容器为环状的容器,所述流入口为遍及所述转子圆筒部及所述定子圆筒部的气体排出区域的整个区域相向的环状的开口。通过将气体通路容器设为环状的容器,气体通路容器遍及排气功能部的下游侧的环状空间的整个区域配置。
[0100]
[4]根据所述[1]至[3]中任一项所记载的真空泵,其中所述气体通路容器是由所述第一加热部进行加热。
[0101]
[5]根据所述[4]所记载的真空泵,其中所述气体通路容器固定于所述定子圆筒部,且经由所述定子圆筒部而由所述第一加热部进行加热。
[0102]
例如,如图5所示,通过将气体通路容器40固定于定子圆筒部22并利用加热部28直接或间接地加热,而无需另外准备气体通路容器40专用的加热部。
[0103]
[6]根据所述[1]至[5]中任一项所记载的真空泵,还包括:吹扫气体导入部,向所述气体通路容器的周围空间导入吹扫气体,通过导入至所述周围空间的气体,从所述转子圆筒部与所述定子圆筒部的空隙排出的气体不会泄漏至所述气体通路容器的周围。
[0104]
例如,如图5所示,通过向气体通路容器40的周围空间导入吹扫气体pg,吹扫气体pg从与接近气体通路容器40的构件(转子圆筒部13、插入部414、定子圆筒部22等)的间隙流入至气体通路容器40,因此,可减少排出气(工艺气体)从空隙向周围空间的漏出。其结果,可进一步抑制在基座30或第二泵壳体20的内周面的生成物堆积。
[0105]
[7]根据所述[1]至[6]中任一项所记载的真空泵,其中所述排气管不仅包括经由间隙插入至所述流出口的所述气体流入侧端部,还包括与所述气体流入侧端部排列设置并向框体内侧突出的凸部,所述气体通路容器的壁部的一部分经由间隙配置于所述气体流入侧端部与所述凸部之间。
[0106]
例如,如图5所示,通过在气体通路容器40的底面壁404的图示下侧配置凸部415,将插入部414及凸部415与底面壁404之间的间隙设为迷宫那样的结构,可进一步减小排出气g向气体通路容器40的周围区域的泄漏。
[0107]
在上述内容中,已对各种实施方式及变形例进行了说明,但本发明并不限定于这些内容。在本发明的技术性思想范围内考虑到的其他形态也包含于本发明的范围内。例如,在上文所述的实施方式中,以涡轮分子泵为例进行了说明,但本发明也可适用于仅具有由定子及转子圆筒部构成的螺纹槽泵的真空泵。