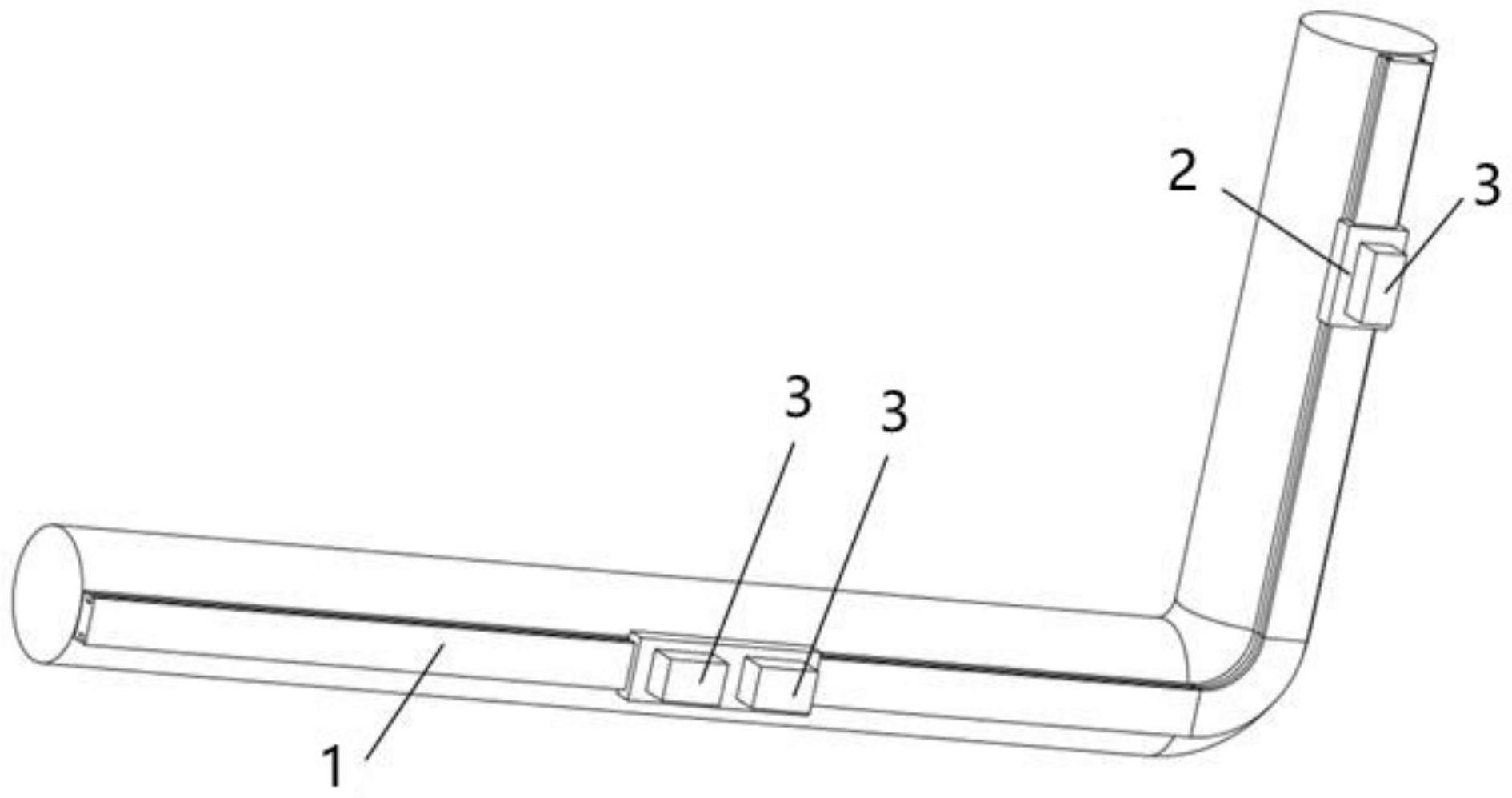
1.本发明涉及基于振动数据的空压机漏气故障监测方法领域,具体涉及一种基于振动数据的空压机漏气故障监测方法。
背景技术:2.空压机是压缩气体发生装置,一般用于气动设备的动力提供,将空气压缩成具备一定压力的气体,该气体连接到气动设备上,使之工作运转,实现能量的转换。压缩气体安全可靠无污染,被广泛运用于生活和生产的各个环节。在矿山生产过程中,空压机是风动机械的动力来源,同时可以向井下工作面提供空气,冲淡和排除各种有害气体和矿尘,是矿井生产与安全保障的重要设备之一。
3.据不完全统计,我国矿山企业中的95%均使用压缩空气,且又连续不停生产的需求,通常采用多组空压机的组合配置。因为空压机工作环境噪音大,温度高,当空压机箱体内部管路发生漏气故障时很难从箱体外部发现,从而造成磨损、腐蚀管路、资源浪费等现象,对煤矿造成巨大经济损失。
4.目前针对空压机的远程监控系统主要基于plc控制,对空压机进行远程控制和管理,在故障监测方面也取得了一些进展,通过在气罐上和空压机上安装压力传感器、在气罐出气管路安装温度传感器的方式来监测压风机是否出现故障。然而,这样的技术方案还存在如下不足之处:
5.1、由于温度传感器属于接触式传感器,损坏率高,检修不便。
6.2、由于温度传感器属于点接触式传感器,不能对空压机的温度进行全方位的监测,故当非接触点发生故障时较难发现,且无法准确判断漏气故障程度与故障发生位置,故如今煤矿企业对于空压机的故障监测仍然主要依靠人工定期巡检。
技术实现要素:7.针对上述存在的技术不足,本发明的目的是提供一种基于振动数据的空压机漏气故障监测方法,其在空压机箱体内管路上设置可移动的振动传感器来采集空压机内部的振动情况,通过对采集到的振动信号进行分析处理,通过算法获取漏气故障是否存在以及故障发生位置,其效果好,成本低,具有较好的实时性。
8.为解决上述技术问题,本发明采用如下技术方案:
9.本发明提供一种振动数据的空压机漏气故障监测方法,具体包括以下步骤:
10.s1、布设故障监测装置:在空压机箱体内气体管路的外壁上设置若干组用于检测管路内部振动状态且能够主动沿管路方向滑动的故障监测装置,故障监测装置与上位机通讯连接;
11.s2、上位机获取空压机在不同故障状态下的振动数据信息并将这些振动数据信息换算成特征向量集,得到特征向量集到空压机故障状态标签集的映射;
12.s3、故障监测装置采集管路内振动数据并传输给上位机,上位机将振动数据信息
与内部故障状态标签集对比,确定空压机管路的故障状态并发出警报;
13.s4、确定故障位置,具体步骤为:
14.s41、将两个各状态历经过程的随机信号x(t)和y(t)的相互关系函数r
xy
(τ)表达为:
[0015][0016]
其中,t是信号周期;y(t+τ)是信号y(t)时移τ后的样本;互相关函数r
xy
(τ)达到最大值时对应的时移τ0反映两个信号相关程度最高时的时间间隔;
[0017]
s42、确定漏气点o处产生的振动信号沿管路方向传播的速度v1;在管路一端的p1、p2点处利用仪器接收振动信号x1和x2,x1和x2之间接收时差为
△
t
12
,p1、p2之间距离为
△
d
12,
振动信号x1和x2互相关函数取得最大值时对应的时移τ
12
就是
△
t
12
,即
△
t
12
=τ
12
,则振动信号在管路的传播速度为
[0018]
s43、在管路另一端的p3点利用仪器接收到的振动信号x3与振动信号x1进行互相关分析,在互相关函数取得最大值时的时移τ
13
就是p1和p3之间接收到振动信号的时间差,即
△
t
13
=τ
13
,则漏气点o距离p1和p3之间沿管路方向的中心线的距离
[0019]
优选地,步骤s1中故障监测装置包括设在管路外壁上的滑轨1,所述滑轨1上设有若干能够滑动的滑块2,滑块2上设有用于获取管内振动信号的振动传感器3,滑块2内设有与滑轨1啮合的滚轮以及驱动滚轮工作的电机,电机连接有控制器,控制器与上位机通讯连接。
[0020]
优选地,步骤s2中获取特征向量集到空压机故障状态标签集映射的具体过程为:
[0021]
步骤1、在空压机的不同故障状态下以第一采样率采集空压机在第一预设时长内的振动数据,得到空压机的不同状态下的训练振动数据;
[0022]
步骤2、对待空压机的每种故障状态下的训练振动数据,按照第二预设时长划分为多个训练振动数据分组;
[0023]
步骤3、对每个训练振动数据分组并分别提取训练特征向量,将训练特征向量对应的空压机的故障状态作为该训练特征向量的标签,带有标签的所有训练特征向量构成训练数据集;
[0024]
步骤4、利用训练数据集训练机器学习分类器,得到特征向量集到空压机故障状态标签集的映射。
[0025]
优选地,步骤s3中确定空压机管路的故障状态的具体方法为:
[0026]
步骤1、以第二采样率采集空压机在第三预设时长内的振动数据,得到空压机检测振动数据;
[0027]
步骤2、对于空压机的检测振动数据,按照第二预设时长划分为多个检测振动数据
分组;
[0028]
步骤3、对每个检测振动数据分组采用与步骤s2中提取训练特征向量相同的方法来提取检测特征向量,得到检测特征向量集;
[0029]
步骤4、将检测特征向量集输入训练后的机器学习分类器,输出空压机故障状态标签,从而确定空压机的故障状态。
[0030]
优选地,步骤s3中故障状态包括正常状态和异常状态,正常状态为空压机正常运行,异常状态包括振动异常状态和漏气状态。
[0031]
本发明的有益效果在于:本发明在空压机箱体内管路上设置可移动的振动传感器来采集空压机内部的振动情况,通过对采集到的振动信号进行分析处理,通过算法获取漏气故障是否存在以及故障发生位置,通过滑块定期滑动,定点采集信号,可以有效避免因漏气点距离传感器过远导致振动信号减弱,从而导致故障识别不精确的问题,其效果好,成本低,能达到较好的实时性。
附图说明
[0032]
为了更清楚地说明本发明实施例或现有技术中的技术方案,下面将对实施例或现有技术描述中所需要使用的附图作简单地介绍,显而易见地,下面描述中的附图仅仅是本发明的一些实施例,对于本领域普通技术人员来讲,在不付出创造性劳动的前提下,还可以根据这些附图获得其他的附图。
[0033]
图1为本发明实施例提供的故障监测装置在气体管路外壁上的安装示意图;
[0034]
图2为本发明实施例提供的故障监测装置的结构示意图;
[0035]
附图标记说明:
[0036]
1、滑轨;2、滑块;3、振动传感器。
具体实施方式
[0037]
下面将结合本发明实施例中的附图,对本发明实施例中的技术方案进行清楚、完整地描述,显然,所描述的实施例仅仅是本发明一部分实施例,而不是全部的实施例。基于本发明中的实施例,本领域普通技术人员在没有做出创造性劳动前提下所获得的所有其他实施例,都属于本发明保护的范围。
[0038]
如图1至图2所示,一种基于振动数据的空压机漏气故障监测方法,具体包括以下步骤:
[0039]
s1、布设故障监测装置:在空压机箱体内某段气体管路的外壁上设置若干组用于检测管路内部振动状态且能够主动沿管路方向滑动的故障监测装置,故障监测装置与上位机通讯连接,上位机选择电脑终端或移动终端;
[0040]
故障监测装置包括设在管路外壁上的滑轨1,所述滑轨1上设有3个能够滑动的滑块2,滑块2上设有用于获取管内振动信号的振动传感器3,滑块2内设有与滑轨1啮合的滚轮以及驱动滚轮工作的电机,电机连接有控制器,控制器与上位机通讯连接,振动传感器3包括拾振器和测量电路,其中拾振器用于感知气体管路的振动,测量电路将工程振动的参量转换成电信号,经电子线路放大后传入上位机进行显示和记录。
[0041]
s2、上位机获取空压机在不同故障状态下的振动数据信息并将这些振动数据信息
换算成特征向量集,得到特征向量集到空压机故障状态标签集的映射;
[0042]
获取特征向量集到空压机故障状态标签集映射的具体过程为:
[0043]
步骤1、在空压机的不同故障状态下以第一采样率采集空压机在第一预设时长内的振动数据,得到空压机的不同状态下的训练振动数据;
[0044]
步骤2、对待空压机的每种故障状态下的训练振动数据,按照第二预设时长划分为多个训练振动数据分组;
[0045]
步骤3、对每个训练振动数据分组并分别提取训练特征向量,将训练特征向量对应的空压机的故障状态作为该训练特征向量的标签,带有标签的所有训练特征向量构成训练数据集;
[0046]
步骤4、利用训练数据集训练机器学习分类器,得到特征向量集到空压机故障状态标签集的映射。
[0047]
s3、故障监测装置采集管路内振动数据并传输给上位机,上位机将振动数据信息与内部故障状态标签集对比,确定空压机管路的故障状态并发出警报;
[0048]
确定空压机管路的故障状态的具体方法为:
[0049]
步骤1、以第二采样率采集空压机在第三预设时长内的振动数据,得到空压机检测振动数据;
[0050]
步骤2、对于空压机的检测振动数据,按照第二预设时长划分为多个检测振动数据分组;
[0051]
步骤3、对每个检测振动数据分组采用与步骤s2中提取训练特征向量相同的方法来提取检测特征向量,得到检测特征向量集;
[0052]
步骤4、将检测特征向量集输入训练后的机器学习分类器,输出空压机故障状态标签,从而确定空压机的故障状态;
[0053]
故障状态包括正常状态和异常状态,正常状态为空压机正常运行,异常状态包括振动异常状态和漏气状态。
[0054]
s4、确定故障位置,具体步骤为:
[0055]
s41、将两个各状态历经过程的随机信号x(t)和y(t)的相互关系函数r
xy
(τ)表达为:
[0056][0057]
其中,t是信号周期;y(t+τ)是信号y(t)时移τ后的样本;互相关函数r
xy
(τ)达到最大值时对应的时移τ0反映两个信号相关程度最高时的时间间隔;
[0058]
s42、确定漏气点o处产生的振动信号沿管路方向传播的速度v1;在管路一端两个振动传感器3的所在位置上(设为p1、p2),利用仪器接收振动信号x1和x2,x1和x2之间接收时差为
△
t
12
,p1、p2之间距离为
△
d
12
,振动信号x1和x2互相关函数取得最大值时对应的时移τ
12
就是
△
t
12
,即
△
t
12
=τ
12
,则振动信号在管路的传播速度为
[0059]
s43、在管路另一端第三个振动传感器3的位置(设为p3点),利用仪器接收到的振
动信号x3与振动信号x1进行互相关分析,在互相关函数取得最大值时的时移τ
13
就是p1和p3之间接收到振动信号的时间差,即
△
t
13
=τ
13
,则漏气点o距离p1和p3之间沿管路方向的中心线的距离
[0060]
上位机中内置有振动信号故障识别和位置定位算法模型,其通过控制滑块2的往复移动,同时滑块2上的振动传感器3获取管道振动信号并传输给上位机,上位机对来自振动传感器3的信号进行分析和识别,通过机器学习识别管路故障,通过相关分析获得振动信号在所在管路上的传播速度,进而获得空压机故障位置,当振动信号的变化满足所设定振动变化特征时则认定空压机处于非正常工作状态。
[0061]
本发明可用于监测矿用空压机气体管路漏气故障,同时能够自动判断出管路漏气故障发生位置,实时性好,判断准确。
[0062]
实施例二,步骤s1中,滑轨1上设置2个滑块,第一个滑块2上设置2个振动传感器3,2个振动传感器3的位置即为p1、p2点,第二个滑块2上设置第三个振动传感器3,该振动传感器3的位置为p3点,p1、p2点的2个振动传感器3用来确定振动信号的传播速度,p3和p1位置的两个振动传感器3配合用来定位故障发生位置,其余步骤同实施例1相同。
[0063]
显然,本领域的技术人员可以对本发明进行各种改动和变型而不脱离本发明的精神和范围。这样,倘若本发明的这些修改和变型属于本发明权利要求及其等同技术的范围之内,则本发明也意图包含这些改动和变型在内。