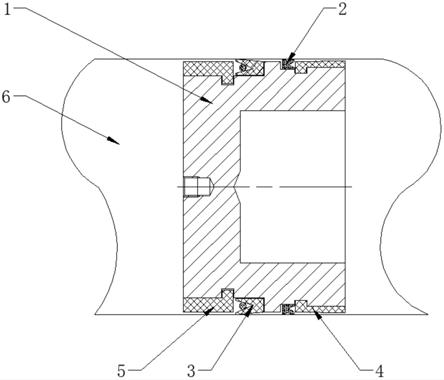
1.本实用新型涉及气缸活塞技术领域,具体为一种便捷安装的活塞组合密封装置。
背景技术:2.当前普遍安装使用的活塞密封组件中,多为弹簧泛塞密封和密封圈配套镶圈密封的组合件;亦或者为弹簧泛塞密封与格兰圈密封的配合使用;在实际应用中,在液控执行器频繁启闭之间,其活塞密封磨损相对较大,使用寿命偏低;在安装中普遍存在前置密封圈定位安装不到位、嵌装偏角等情况,检修效率和检修质量无法保障;当前的密封组合件有效密封性能偏差,运行一段时间后会出现不同程度的渗油现象,对传动部件、驱动部件、现场环境等均会造成较大污染和影响。
技术实现要素:3.本实用新型的目的在于提供一种便捷安装的活塞组合密封装置,以解决上述背景技术中在实际应用中,在液控执行器频繁启闭之间,其活塞密封磨损相对较大,使用寿命偏低;在安装中普遍存在前置密封圈定位安装不到位、嵌装偏角等情况,检修效率和检修质量无法保障;当前的密封组合件有效密封性能偏差,密封效果差,运行一段时间后会出现不同程度的渗油现象,对传动部件、驱动部件、现场环境等均会造成较大污染和影响的问题。
4.为实现上述目的,本实用新型提供如下技术方案:一种便捷安装的活塞组合密封装置,包括活塞和缸体,所述缸体的内部滑动连接有活塞,所述活塞外表面的两端分别开设有第一导向嵌槽和第二导向嵌槽,所述活塞外表面的中部开设有第一密封嵌槽和第二密封嵌槽,所述第一密封嵌槽和第二密封嵌槽分别与第一导向嵌槽和第二导向嵌槽相连,所述第一导向嵌槽的内部卡合连接有出口导向套,所述第二导向嵌槽的内部卡合连接有进口导向套,所述第一密封嵌槽的内部卡合连接有嵌装密封,所述第二密封嵌槽的内部卡合连接有半星型密封,所述活塞临近出口导向套的一端中心开设有安装螺孔。
5.作为本实用新型的一种优选技术方案,所述半星型密封临近进口导向套的一端设为星型密封v端,所述半星型密封远离进口导向套的一端设为星型密封平端。
6.作为本实用新型的一种优选技术方案,所述嵌装密封由聚醚聚氨酯制成。
7.作为本实用新型的一种优选技术方案,所述嵌装密封包括嵌装外密封和o型圈,所述嵌装外密封临近出口导向套的一端开设有v形槽,所述v形槽的内部卡合连接有o型圈。
8.作为本实用新型的一种优选技术方案,所述进口导向套和出口导向套均为四氟套,所述四氟套由聚四氟乙烯制成。
9.作为本实用新型的一种优选技术方案,所述第一导向嵌槽临近嵌装密封的一端和第二导向嵌槽临近半星型密封的一端分别开设有第一限位槽和第二限位槽,所述进口导向套内侧临近嵌装密封的一端和出口导向套内侧套临近半星型密封的一端分别固定设置有第一限位圈和第二限位圈,所述第一限位圈和第二限位圈分别与第一限位槽和第二限位槽卡和连接。
10.与现有技术相比,本实用新型的有益效果是:将前置o型圈、外侧密封圈组合结构优化为半星型密封圈,使得密封组件安装更为便捷、高效,避免定位安装不到位、嵌装偏角的现象,提升检修效率和检修质量;密封材质为聚醚聚氨酯,使得活塞更为耐磨,有效避免因自身劣化对油缸的磨损等,确保传动系统运行的平稳性,对于传动本身,确保高承压和高频次动作,延长使用寿命;解决了密封性能不足的问题,使得活塞密封在高频次动作,高承压下,可保证密封性能;密封结构为v型嵌o型圈的高承压结构,确保内部楔形更为稳固。
附图说明
11.图1为本实用新型的截面图;
12.图2为本实用新型活塞的截面图;
13.图3为本实用新型半星型密封的截面图;
14.图4为本实用新型嵌装密封的截面图。
15.图中:1、活塞;11、第一密封嵌槽;12、第一导向嵌槽;13、安装螺孔;14、第二密封嵌槽;15、第二导向嵌槽;2、半星型密封;21、星型密封平端;22、星型密封v端;3、嵌装密封;31、嵌装外密封;32、o型圈;4、进口导向套;5、出口导向套;6、缸体。
具体实施方式
16.下面将结合本实用新型实施例中的附图,对本实用新型实施例中的技术方案进行清楚、完整地描述,显然,所描述的实施例仅仅是本实用新型一部分实施例,而不是全部的实施例。基于本实用新型中的实施例,本领域普通技术人员在没有做出创造性劳动前提下所获得的所有其他实施例,都属于本实用新型保护的范围。
17.请参阅图1
‑
4,本实用新型提供了一种便捷安装的活塞组合密封装置,包括活塞1和缸体6,缸体6的内部滑动连接有活塞1,活塞1外表面的两端分别开设有第一导向嵌槽12和第二导向嵌槽15,活塞1外表面的中部开设有第一密封嵌槽11和第二密封嵌槽14,第一密封嵌槽11和第二密封嵌槽14分别与第一导向嵌槽12和第二导向嵌槽15相连,第一导向嵌槽12的内部卡合连接有出口导向套5,第二导向嵌槽15的内部卡合连接有进口导向套4,第一密封嵌槽11的内部卡合连接有嵌装密封3,第二密封嵌槽14的内部卡合连接有半星型密封2,活塞1临近出口导向套5的一端中心开设有安装螺孔13。
18.优选的,半星型密封2临近进口导向套4的一端设为星型密封v端22,半星型密封2远离进口导向套4的一端设为星型密封平端21,星型密封平端21与进油油液和活塞嵌槽形成楔形支撑,半星型密封2上端、下端、行进端均设置v型槽,形成星型密封v端22,与进油油液与缸体6内壁形成倒楔形,互为阻力,保障密封性能。
19.优选的,嵌装密封3由聚醚聚氨酯制成,使得活塞1更为耐磨,高承压,对于传动本身,确保高承压和高频次动作。
20.优选的,嵌装密封3包括嵌装外密封31和o型圈32,嵌装外密封31临近出口导向套5的一端开设有v形槽,v形槽的内部卡合连接有o型圈32,嵌装外密封31为嵌装密封本体,前进方向倾角密封,与液压油、缸壁形成楔形油膜,利用双向阻力承压,确保密封性能,嵌装外密封31通过开设的v形槽卡合安装o型圈32,o型圈32用于形成双楔形油膜,确保首道密封的高承压属性。
21.优选的,进口导向套4和出口导向套5均为四氟套,四氟套由聚四氟乙烯制成,进口导向套4与出口导向套5形成双向四氟套结构。
22.优选的,第一导向嵌槽12临近嵌装密封3的一端和第二导向嵌槽15临近半星型密封2的一端分别开设有第一限位槽和第二限位槽,进口导向套4内侧临近嵌装密封3的一端和出口导向套5内侧套临近半星型密封2的一端分别固定设置有第一限位圈和第二限位圈,第一限位圈和第二限位圈分别与第一限位槽和第二限位槽卡和连接,通过活塞1上的限位槽与进口导向套4和出口导向套5内侧固定设置的限位圈卡合,从而加强进口导向套4和出口导向套5的固定。
23.具体使用时,本实用新型一种便捷安装的活塞组合密封装置,活塞1在缸体6内部往复运动,活塞1通过第一导向嵌槽12和第二导向嵌槽15分别卡合安装出口导向套5和进口导向套4,通过第一密封嵌槽11和第二密封嵌槽14分别卡合安装嵌装密封3和半星型密封2,嵌装密封3包括嵌装外密封31和o型圈32,活塞密封安装的便捷性,避免原有o型圈32外侧镶裹密封的偏离,避免对整体密封性能的影响,使得密封组件安装更为便捷、高效,避免定位安装不到位、嵌装偏角的现象,嵌装外密封31为嵌装密封本体,前进方向倾角密封,与液压油、缸壁形成楔形油膜,利用双向阻力承压,确保密封性能,嵌装外密封31上嵌设o型圈32,o型圈32用于形成双楔形油膜,确保首道密封的高承压属性,嵌装密封3由聚醚聚氨酯制成,使得活塞1更为耐磨,高承压,对于传动本身,确保高承压和高频次动作,延长使用寿命,半星型密封2的两端分别设为星型密封v端22和星型密封平端21,星型密封平端21与进油油液和活塞嵌槽形成楔形支撑,半星型密封2上端、下端、行进端均设置v型槽,形成星型密封v端22,与进油油液、缸体6内壁形成倒楔形,互为阻力,保障密封性能,避免了运行一段时间后会出现不同程度的渗油现象和对传动部件、驱动部件、现场环境等均会造成较大污染和影响,将前置o型圈、外侧密封圈组合结构优化为半星型密封圈,密封结构为v型嵌o型圈的高承压结构,确保内部楔形更为稳固,密封性能更为高效,提升检修效率和检修质量,进口导向套4在进口方向驱除活塞1行程内杂物,确保首道活塞密封行程侧的清洁,保障密封本体不被杂质损害,出口导向套5在出口方向驱除活塞1行程内杂物,确保二次活塞密封行程侧的清洁,保障密封本体不被杂质损害。
24.尽管参照前述实施例对本实用新型进行了详细的说明,对于本领域的技术人员来说,其依然可以对前述各实施例所记载的技术方案进行修改,或者对其中部分技术特征进行等同替换,凡在本实用新型的精神和原则之内,所做的任何修改、等同替换、改进等,均应包含在本实用新型的保护范围之内。