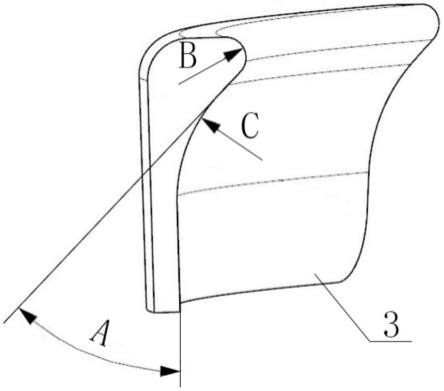
1.本实用新型涉及风罩技术领域,具体涉及利于降低旋转阶次噪音的导风圈结构,应用于新能源车型以及高nvh性能要求的风扇产品面临的车内外风叶主阶次噪音突出的场合。
背景技术:2.目前,传统的直流有刷电机和无刷电机风扇,在导风圈位置,设计的出风口导流结构如图1所示,导风圈均采用间距布置的导风内圈2和导风外圈1,其中导风外圈1的截面为竖置的z型结构,导风内圈2为j型结构,导风圈位置高度需要高出风叶翻边高度,这样既可以保证流量不损失,也可以保证导风圈以及整体的设计强度,存在以下技术缺陷:1)、导风圈高度需要根据系统设计匹配的尺寸以及风叶叶型来决定具体的安放位置、高度和角度,需要丰富的设计经验和实验数据才能给出具体的设计参数,通用效果差;2)、由于导风圈结构基本上是均匀且轴向对称设计结构,统一高度和方向,完全不能考虑到风叶旋转时,流场方向性以及声音相位角度的问题,例如车内某一个局部位置存在噪音较大的现象,对于风扇进风口结构设计以及出风口结构设计提出了更高难度的要求;3)、传统阶次噪音改善的手段,包括风叶叶型改进、风罩整体设计改进、筋条形状改进、配合空间改进等等,均需要重新开模具生产,生产成本高。
技术实现要素:3.针对现有技术存在的问题,本实用新型提供利于降低旋转阶次噪音的导风圈结构,以解决上述至少一种技术问题。
4.本实用新型的技术方案是:利于降低旋转阶次噪音的导风圈结构,安装在风罩出风口,所述风罩出风口包括导风圈,导风圈上设置有数个绕圆周布置的凸台,任意一个凸台上部均通过加强筋与导风圈内部中心的挡圈连接,任意相邻凸台之间的导风圈上均设置有开口向上的开口槽,开口槽内至少设置有一件导风叶;导风叶的一端及底面与靠近其的开口槽连接为一体,导风叶的另一端与靠近其的开口槽之间留有第一空间,第一空间所在的弧长根据流体噪音计算,并通过了实物验证。
5.本实用新型采用在导风圈上设置多个开口槽,无需根据系统设计匹配的尺寸以及风叶叶型重新设计导风圈,无需对风扇进风口结构以及出风口结构重新设计,仅需要根据现有风叶设计叶型,结合流场分析以及噪音测试的声场分布,分析出在导风圈上需要添加的导风叶的具体位置、角度以及高度,适用范围广;在现有模具基础上添加镶块生产导风叶,从而实现小变动就能完成噪音优化,节约了大量时间和人力物力,不需要重新开模具,降低了生产成本,这是在传统设计基础上,略微增加局部设计结构,降低了旋转阶次噪音,满足了客户要求。
6.优选,所述导风叶包括第一导风叶,第一导风叶为第一劣弧段,第一劣弧段沿着垂直方向的截面为倒置的j型结构,其中倒置的j型结构下端直板与导风圈的壁厚尺寸相同,j
型结构的折弯部朝向导风圈的圆心一侧,j型结构的中部靠近导风圈的圆心一侧为圆弧过渡面;j型结构的钩部末端设置有倒圆角。
7.本实用新型采用倒置j型结构的第一导风叶,依次通过倒置的j型结构下端直板、圆弧过渡面、倒圆角降低局部位置点噪音,从而降低了旋转阶次噪音。
附图说明
8.图1为现有技术的导风圈结构示意图。
9.图2为本实用新型的第一导风叶、第二导风叶安装结构示意图。
10.图3为本实用新型的第一导风叶三维图。
11.图4为本实用新型的第二导风叶三维图。
具体实施方式
12.下面结合附图对本实用新型做进一步的说明。
13.一种利于降低旋转阶次噪音的导风圈结构设置方法,包括以下步骤:
14.1)、在风罩出风口的导风圈5上设置数个绕圆周均布且开口向上的开口槽,开口槽位于相邻的加强筋之间;
15.2)、根据现有风叶设计叶型,结合流场分析以及噪音测试的声场分布,分析出在导风圈5上需要添加的导风叶的具体位置、角度以及高度;
16.3)、导风叶结构包括第一导风叶3、第二导风叶4,根据计算机仿真设计将第一导风叶3、第二导风叶4单个或多个组合,并确定其在导风圈5上的具体位置;
17.4)、在现有模具基础上添加相应的镶块生产导风叶;
18.5)、将导风圈结构安装后进行实物验证,导风圈结构改进后,86%占空比(2490rpm)稳态工况下,总声压级下降0.3db,优化不大,但对于旋转阶次噪音的优化很明显,下降了6.5db左右。在升速噪音结果来看,总声压级基本上和原设计重叠,优化不明显,但旋转主阶次噪音,在整个转速区间都优化很明显,差值优化明显的位置,最大可以达到10db以上。本发明在现有模具基础上添加镶块生产导风叶,从而实现小变动就能完成噪音优化,节约了大量时间和人力物力,不需要重新开模具,降低了生产成本。
19.实施例一、利于降低旋转阶次噪音的导风圈结构,参考图2,安装在风罩出风口,所述风罩出风口包括导风圈5,导风圈5上设置有数个绕圆周布置的凸台,任意一个凸台上部均通过加强筋与导风圈5内部中心的挡圈连接,任意相邻凸台之间的导风圈5上均设置有开口向上的开口槽,开口槽内至少设置有一件导风叶;导风叶的一端及底面与靠近其的开口槽连接为一体,导风叶的另一端与靠近其的开口槽之间留有第一空间,第一空间所在的弧长根据流体噪音计算,并通过了实物验证。本实用新型采用在导风圈上设置多个开口槽,无需根据系统设计匹配的尺寸以及风叶叶型重新设计导风圈,无需对风扇进风口结构以及出风口结构重新设计,仅需要根据现有风叶设计叶型,结合流场分析以及噪音测试的声场分布,分析出在导风圈上需要添加的导风叶的具体位置、角度以及高度,适用范围广;这是在传统设计基础上,略微增加局部设计结构,降低了旋转阶次噪音,满足了客户要求。
20.实施例二、在实施例一的基础上,所述开口槽为u型开口槽,u型开口槽的底边与两侧竖边之间均设置有第一圆角;导风叶的一端底部设置有第二圆角,第二圆角与第一圆角
尺寸相同,导风叶上与第二圆角相邻的竖边及底边与其接触处的u型开口槽连接为一体,第一空间位于导风叶的另一端与靠近其的u型开口槽之间。本实用新型采用导风叶的一端与u型开口槽连接为一体,降低了噪音;通过第一圆角与第二圆角配合,增加了接触端的面积,增加了局部刚性,提升了导风圈的整体强度。
21.实施例三、在实施例二的基础上,参考图3,所述导风叶包括第一导风叶3,第一导风叶3为第一劣弧段,第一劣弧段沿着垂直方向的截面为倒置的j型结构,其中倒置的j型结构下端直板与导风圈5的壁厚尺寸相同,j型结构的折弯部朝向导风圈5的圆心一侧,j型结构的中部靠近导风圈5的圆心一侧为圆弧过渡面,圆弧过渡面的半径为c;j型结构的钩部末端设置有倒圆角,圆角的半径为b。本实用新型采用倒置j型结构的第一导风叶,依次通过倒置的j型结构下端直板、圆弧过渡面、倒圆角降低局部位置点噪音,从而降低了旋转阶次噪音。
22.实施例四、在实施例三的基础上,所述圆弧过渡面与j型结构的折弯部连接处之间还设置有导风面,导风面与垂直面之间的夹角a为锐角。本实用新型采用导风面进一步解决噪音分布的均匀性问题,依次通过倒置的j型结构下端直板、圆弧过渡面、导风面、倒圆角降低局部位置点噪音,从而降低了旋转阶次噪音。
23.实施例五、在实施例四的基础上,导风面与垂直面之间的夹角a=45
°
,j型结构的钩部末端圆角的半径b=2mm;圆弧过渡面的半径c=15mm。
24.实施例六、在实施例二的基础上,参考图2、图4,所述导风叶还包括第二导风叶4,第二导风叶4为第二劣弧段,第二劣弧段与导风圈5的壁厚尺寸相同,第二劣弧段沿着垂直方向的截面为竖置的长方形。所述第二导风叶4的一端下方与u型开口槽的接触端设置有对应的第三圆角,第三圆角与第一圆角尺寸相同,第二导风叶4上与第三圆角相邻的竖边及底边与其接触处的u型开口槽连接为一体。所述第二导风叶4的另一端上方设置有第四圆角,第一空间位于第二导风叶4的另一端与靠近其的u型开口槽之间;第四圆角与靠近其的u型开口槽之间的空间为第二空间,第二空间与第一空间相通。本实用新型采用第二导风叶的一端与u型开口槽连接为一体,降低了噪音;通过第一圆角与第三圆角配合,增加了接触端的面积,增加了局部刚性,提升了导风圈的整体强度。
25.具体实施时,在风罩出风口位置,根据不同风扇叶型,匹配相应的局部风圈结构。根据叶型调整角度和高度范围,以满足实测单体阶次噪音要求和整车nvh要求。
26.以上仅是本实用新型的优选实施方式,应当指出,对于本技术领域的普通技术人员来说,在不脱离本实用新型原理的前提下,还可以做出若干改进和润饰,这些改进和润饰也应视为本实用新型的保护范围。