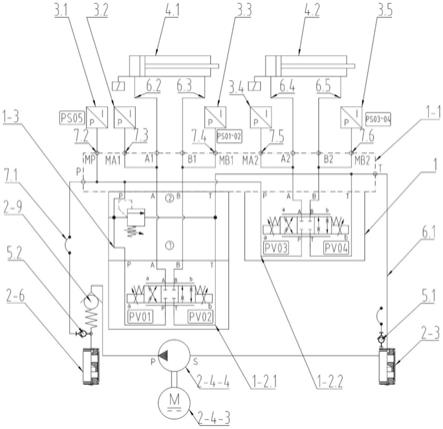
一种可调收-扩喷管作动环微型高精度电液比例同步系统
1.技术领域:本发明属于涡喷发动机控制技术领域,特别涉及一种可调收-扩喷管作动环微型高精度电液比例同步系统,及其系统预处理方法。
2.
背景技术:当今大国角力的战场形态给智能化的作战技术提出了更高层次的要求,其中,空中机械化集群突击,以空制地,夺取空地立体优势这一作战方略集中凸显出与之相契合的作战效能。高机动性能空中作战装备作为基础性关键单元,具备不可替代的发展优势。对于一些导弹、无人侦察机、靶机等辅助型作战训练设备,同样面临早期发动机的优化改型以满足部队日益发展的需求。
3.可调收-扩喷管作为涡喷发动机燃烧气体排放和推力供给的关键结构,可实现超音速飞机的加力-收力功能,从而使得飞机在各种工作状态下都能获得良好的机动性能。气流方向的精确控制是满足上述技术要求的关键一环,微小的推力矢量偏差将导致不可预期的显著动作变化,为此,始终保持各段喷管动作的一致性和严格同步尤为重要。对于作战训练用小型涡喷发动机的加力改型,有关尾喷管气流方向控制的现有设计结构和技术并不成熟,相关试验验证不够充分,有关应用和介绍也不够普及。现有经验主要是采用电动执行器实现尾喷管的收-扩控制。
4.采用电动执行器控制尾喷管的收-扩通常存在以下几方面问题:1) 适应性不强,电驱系统动力输出有限,功率质量比较小,宽范围加力需求优势不足;涡喷发动机单位质量的增加作用于飞机上将放大7~8倍,系统须具有更高的功率质量比;2) 控制精度不高,针对尾喷管周围高温差幅度和快热传导速度的恶劣工况环境,作动结构变形所带来的控制难度增加,设备自身的结构和电驱性能亦易收到影响;3) 成本高,需使用航天领域专用微型高精度电驱系统,价格昂贵,且自主开发难度大,不符合产品的经济性要求。
5.公开于该背景技术部分的信息仅仅旨在增加对本发明的总体背景的理解,而不应当被视为承认或以任何形式暗示该信息构成已为本领域一般技术人员所公知的现有技术。
6.
技术实现要素:本发明的目的在于提供一种可调收-扩喷管作动环微型高精度电液比例同步系统,包括:位于中部机舱的比例控制阀组、位于前端进气段上侧的液压站、位于前端进气段下侧的传感器组、位于尾喷管前端的伺服油缸;液压站中的电机泵组与高压油箱组成闭式油气弹性动力源主体设备,电机泵组通过测压软管向比例控制阀组输出高压油,闭式油气弹性动力源主体设备与提供吸回油的低压油箱一道,组成液压循环系统;两个比例控制阀组通过硬管连通两只伺服油缸,两只伺服油缸分别推动发动机喷管两侧的作动环;传感器组通过测压软管连接比例控制阀组,用于监测和传送压力数据供其机载控制器分析处理;当需要相对长期保持某一喷管开度时,控制系统通过伺服油缸的位移传感器监测到实际位移产生临界微小变化,或通过传感器组分析出油缸双腔压力异常,则其发
出指令控制油缸按常规动作模式动作至既定位置。
7.本发明专利针对一种超音速靶机的小型涡喷发动机(小型涡喷发动机”简称“微发”或“小发”,加力需求≤600kg),在现有结构和有限空间的基础上,通过专用电液比例系统控制喷管作动环的精确同步运动,同时兼顾设备的宽温度适应性、轻量化和经济性,满足飞机所需的加/收力指标,从而使其具备良好的机动性能。利用液压传动在大功率质量比、动作平稳性、自动控制、无级调速等方面的优势,本电液比例同步系统通过对喷管收-扩的协同调节控制实现某小型涡喷发动机600kg级轴向推力矢量的加力需求。
8.优选地,上述技术方案中,比例控制阀组、液压站、传感器组、伺服油缸、带排气测压接头、硬管及测压软管总质量≤7kg,满足发动机整体质量和性能要求。
9.优选地,上述技术方案中,比例控制阀组主要由:比例控制阀块、比例换向阀、和溢流阀组成;比例换向阀与比例控制阀块间螺栓固定,溢流阀为螺旋插装式结构,固定于比例控制阀块上;比例控制阀块采用7075-t6材质,表面阳极氧化处理;比例换向阀采用3通径板式阀,响应频率40~50hz。
10.优选地,上述技术方案中,比例控制阀组外形结构配套中部机舱环形槽结构(圆柱面开半圆形凹槽),缩减了比例控制阀组的长宽高外形尺寸,使之适配上述环形槽结构,铰接式管接头与测压接头安装于比例控制阀块上;通过换装扁平形德驰插头、铰接式管接头和测压接头配搭等形式,充分实现了紧凑化和轻量化的整体结构要求。
11.优选地,上述技术方案中,液压站主要由自制管接头、自制铰接式接头、低压油箱、电机泵组、六角头空心螺栓、高压油箱、固定half板前、固定half板后、单向阀组成;高压齿轮泵与高压油箱通过自制管接头和自制铰接式接头连通,单向阀固定于自制管接头和自制铰接式接头内部中央;单向阀为微型螺旋插装式结构;低压油箱具有同高压油箱类似的功能结构,具备高低温能量吸收和冗余储能/储油能力,采用圆筒形紧凑化设计,有效容积前者稍大于后者,两者均为自研系列化产品;低压油箱前端设有与高压齿轮泵配套的条形油口安装结构,用于系统吸回油和测压,低压油箱的吸油口通过六角头空心螺栓与高压齿轮泵直连;低压油箱后端设有5/8
”ꢀ
18 unf接口小型充气阀。
12.优选地,上述技术方案中,高压油箱每次向比例控制阀组输出的油液流量为从系统额定工作压力降至额定负载对应压力时高压油箱变化的那部分工作容积;低压油箱的有效容积和压力等级在考虑气体冷缩因素的基础上适配高压油箱工作之所需,并使得高压齿轮泵工作在允许的进口真空度或相对压力范围内。通过考虑各工况下温差所带来的气体冷缩和油液热胀,对该工作容积进行修正,同时考虑比例控制余量系数及阀泄漏,以确保流量的充分供给和系统的合理运行。
13.优选地,上述技术方案中,高压齿轮泵的直流电机+齿轮箱采用24v供电微型圆柱石墨电刷电机;具备高动态特性和转矩密度,运转平稳;高压齿轮泵采用微排量高压产品(定义1cc/r以下为微排),具备高容积效率和低泄漏量,自吸能力强,确保系统所需流量和压力稳定输出的同时进一步提高了系统效率、减少发热;即使油缸处于持续动作状态,电机泵组每次向高压油箱蓄能的时间亦小于每两次蓄能之间的间隔时间;固定half板将液压站各段连成一整体,并通过螺钉与进气段表面结构相连固定。
14.优选地,上述技术方案中,当监测到传感器组的压力处于低压能时,电机泵组得电
动作向高压油箱蓄能,至达到高压限值时停止,实现二次动力输出的同时,提高了系统的功率利用效率,有效避免了能量损耗和发热问题。
15.优选地,上述技术方案中,液压站中所有自制结构件均采用7075-t6材质以满足轻量化和高强度的技术要求。
16.优选地,上述技术方案中,p口(高压油箱出口至比例控制阀组(1)p口)和传感器组的连接均采用测压接头+测压软管的形式,既增加了布置的灵活性,又减轻了常规连接的重量;考虑到本系统高低温、冲击碰撞等极端工况,系统中所有软管及电缆(电缆指的是比例换向阀上的德驰插头的出线电缆)使用pa-6尼龙波纹管包裹,硬管使用碳钢材质确保较高的温度-压降特性,机体后端油缸连接管路(硬管)使用玻纤编制无缝硅胶护套整体包裹,确保系统安全可靠运行。
17.优选地,上述技术方案中,伺服油缸为一体式活塞与活塞杆结构,伺服油缸置于尾喷管前端;伺服油缸总高≤32mm,总长≤200mm;伺服油缸整体满足系统额定工作压力和尾喷管前端-30℃~+135℃的环境温度要求,尾喷管附近机体表面敷设有预隔热层,尾喷管前端最高应有200多度,在此温度下油缸无法正常运行,损坏油缸结构,故此敷设有预隔热层,预隔热层是事先敷设好,隔热层和尾喷管属于现有技术,与本系统创新无直接关联。
18.优选地,上述技术方案中,伺服油缸包括:缸体,盖合在缸体两侧开口处的后缸盖、前缸盖,一端置于缸体内的活塞杆,活塞杆的另一端从前缸盖延伸出缸体,铰接式管接头组合体固连在靠近后缸盖一侧的缸体上、用于连通比例控制阀组,铰接式管接头组合体结构小巧,位移传感器从后缸盖插入缸体内、用于测量活塞杆的行程。位移传感器采用油缸内置安装结构产品,一体式ptfe塑封出线形式,其线性度误差≤0.1mm,结合控制系统16bit的模拟量分辨精度,为0.5mm以内的同步偏差控制提供了理论保障。
19.前缸盖和活塞杆的配合处设有防尘圈和杆密封,前缸盖和缸体的装配处设有缸体密封,后缸盖和缸体的装配处设有缸体密封,活塞杆和缸体内壁配合处设有活塞密封、活塞支撑环组成。
20.活塞杆前端设计有与作动环固定接口相连的万向连接关节;铰接式管接头组合体结构小巧,杆密封、缸体密封、活塞密封均采用氟橡胶vit和/或聚四氟乙烯ptfe材质;位移传感器采用油缸内置安装结构产品,一体式ptfe塑封出线形式,其线性度误差≤0.1mm,结合控制系统16bit的模拟量分辨精度,为0.5mm以内的同步偏差控制提供了理论保障。
21.一种可调收-扩喷管作动环微型高精度电液比例同步系统搭建预处理方法,在前文所述系统搭建完成时,将预先准备好的压力表工装接入充气工具,分别对低压油箱和高压油箱进行预充气,确保量程和精度(≤1.6级)匹配;通过调试或清洗的方式预先将油缸和管路中注满油液,并在调试动作时通过低压油箱上的测压接头排出系统管路中多余气体,而后通过测压接头向低压油箱中注油加压至所需设定的最高储能压力。溢流阀对由于工作和环境异常而导致的压力升高这一潜在风险起到安全保护作用,进一步提高系统功能动作的稳定性和可靠性。
22.一种可调收-扩喷管作动环微型高精度电液比例同步控制方法,其特征在于:伺服油缸由各自的比例换向阀单独控制;内置pid闭环控制调节功能的plc通过向比例换向阀的线圈输出实时电流控制阀芯相应侧开度大小,从而实现伺服油缸伸缩动作的实时位置闭环
控制;plc接收位移传感器发来的油缸使能、伸出和缩回开关量信号以触发油缸动作的执行。
23.优选地,上述技术方案中,伺服油缸(4)伸缩动作的整个过程具有相同的运动加速度绝对值。
24.本系统采用三角形速度-时间控制算法作为伺服油缸4的基本运动模式,目标动作时间t’确定后,前一半时间控制伺服油缸4恒加速运动至峰值动作速度v
max
,后一半时间控制伺服油缸4恒减速运动至最终停止,整个运动过程具有相同的运动加速度绝对值,从而确保油缸动作的稳定性。
25.△
aoba和
△
aob的面积分别即为伺服油缸4的实时理论位移sa和目标位移值s’,分别将速度和位移同时间之间的关系va(t)和sa(t)导入plc,控制器根据对应参数化软件(基于pc)中给定的“单位行程对应动作时间”值自动计算任意动作工况下的目标动作时间t’,通过在软件界面中对相关参数进行在线监测和修改优化,及对“比例电磁铁非线性输出调节”窗口进行设定以屏蔽比例阀“死区”并改善其非线性问题,实现对伺服油缸4运动过程的精确控制。
26.plc接收来自位移传感器4-6的实时实际位移值作为反馈,并与实时理论位移值sa(t)或目标位移值s’进行比较,形成位置闭环控制;实时理论速度值va(t)产生sa(t),决定实时理论阀芯开度。通过对pid控制中相关系数的设定,最终输出经修正的实时位移令值;本系统中,比例换向阀1-2采用3通径板式阀,具有精确阀芯适配性、低泄漏、长寿命等优点,响应频率40~50hz;位移传感器4-6采用4~20ma模拟量信号输出形式,线性度误差≤0.1mm,接收端plc分辨精度16bit,位移传感器4-6结构上采用油缸内置及一体式ptfe塑封出线形式;液压回路中溢流阀1-3在具备优异开关响应速度的同时,亦具备可以忽略不计的极低泄漏量技术指标。综合上述控制功能实现形式及技术性能指标,实现了对双缸全行程位移偏差≤0.5mm的高精度同步控制。
27.与现有技术相比,本发明具有如下有益效果:本电液比例同步系统具有较大的功率质量比,结构紧凑,模块化集成度高,高温差幅度、气压变化及冲击等工况环境适应性好,同步控制精度高(双缸全行程位移偏差≤0.5mm),控制简单,性能稳定可靠,功率利用充分,经济性好(标准化、自主系列化、通用化设计),可作为成套设备满足小型涡喷发动机的宽范围轴向加力需求。
28.附图说明:图1 为电液比例同步系统原理图;图2液压站三维示意图;图3液压站俯视图;图4比例控制阀组主视图;图5比例控制阀组俯视图;图6伺服油缸左侧视图;图7伺服油缸俯视图(剖视);图8系统同步控制框图;图9三角形速度-时间控制算法图示;图10系统pid闭环控制调节框图。
29.图中:1、比例控制阀组;2、液压站;3、传感器组;4、伺服油缸;5、带排气测压接头;1-1、比例控制阀块;1-2.1、1-2.2均为比例换向阀;1-3、溢流阀;1-4、铰接式管接头;1-2.1-1、1-2.2-1均为德驰插头;2-1、自制管接头;2-2、自制铰接式接头;2-3、低压油箱;2-4、电机泵组;2-5、六角头空心螺栓;2-6、高压油箱;2-7、固定half板前、2-8、固定half板后;2-9、单向阀;3.1、传感器组;3.2、传感器组;3.3、传感器组;3.4、传感器组;3.5、传感器组;4-1、缸体;4-2、后缸盖;4-3、前缸盖;4-4、活塞(杆);4-5、铰接式管接头组合体;4-6、位移传感器;4-7、防尘圈;4-8、杆密封(斯特封);4-9、缸体密封(o形圈);4-10、活塞密封(格莱圈);4-11、活塞支撑环;5.1、测压接头;6.1、6.2、6.3、6.4、6.5均为硬管;7.1、7.2、7.3、7.4、7.5、7.6均为测压软管;1-4.1、1-4.2、1-4.3、1-4.4均为铰接式管接头;1-5.1、1-5.2均为测压接头;2-3-1、小型充气阀;2-4-1、钟形罩联轴器;2-4-2、钟形罩联轴器;2-4-3、直流电机+齿轮箱;2-4-4、高压齿轮泵;需要说明的是:附图标记中的点“.”指代相同零件的不同数量,横杠
“‑”
指代同一部件下的二级组成零件或部件。
30.具体实施方式:下面对本发明的具体实施方式进行详细描述,但应当理解本发明的保护 范围并不受具体实施方式的限制。
31.除非另有其它明确表示,否则在整个说明书和权利要求书中,术语“包括”或其变换如“包含”或“包括有”等等将被理解为包括所陈述的元件或组成部分,而并未排除其它元件或其它组成部分。
32.一种可调收-扩喷管作动环微型高精度电液比例同步系统,包括:位于中部机舱的比例控制阀组1、位于前端进气段上侧的液压站2、位于前端进气段下侧的传感器组3、位于尾喷管前端的伺服油缸4;液压站2中的电机泵组2-4与高压油箱2-6组成闭式油气弹性动力源主体设备,电机泵组2-4通过测压软管向比例控制阀组1输出高压油,闭式油气弹性动力源主体设备与提供吸回油的低压油箱2-3一道,组成液压循环系统;两个比例控制阀组1通过硬管连通两只伺服油缸4,两只伺服油缸4分别推动发动机喷管两侧的作动环;传感器组3通过测压软管连接比例控制阀组1,用于监测和传送压力数据供其机载控制器(上位机)分析处理。当需要相对长期保持某一喷管开度时,控制系统通过伺服油缸4的位移传感器监测到实际位移产生临界微小变化,或通过传感器组3分析出油缸双腔压力异常,则其发出指令控制油缸按常规动作模式动作至既定位置。
33.比例控制阀组1、液压站2、传感器组3、伺服油缸4、带排气测压接头5、硬管6.1及测压软管7总质量≤7kg。
34.比例控制阀组1主要由:比例控制阀块1-1、比例换向阀1-2、和溢流阀1-3组成;比例换向阀1-2与比例控制阀块1-1间螺栓固定,溢流阀1-3为螺旋插装式结构,固定于比例控制阀块1-1上;比例控制阀块1-1采用7075-t6材质,表面阳极氧化处理;比例换向阀1-2采用3通径板式阀,响应频率40~50hz;溢流阀1-3在具备优异开关响应速度的同时,同样具备可以忽略不计的极低泄漏量技术指标。
35.比例控制阀组1外形结构配套中部机舱环形槽结构(圆柱面开半圆形凹槽),缩减了比例控制阀组1的长宽高外形尺寸,使之适配上述环形槽结构,铰接式管接头1-4与测压接头1-5安装于比例控制阀块1-1上;通过换装扁平形德驰插头1-2-1、铰接式管接头和测压接头配搭等形式,充分实现了紧凑化和轻量化的整体结构要求。
36.液压站2主要由自制管接头2-1、自制铰接式接头2-2、低压油箱2-3、电机泵组2-4、六角头空心螺栓2-5、高压油箱2-6、固定half板前2-7、固定half板后2-8、单向阀2-9组成;高压齿轮泵2-4-4与高压油箱2-6通过自制管接头2-1和自制铰接式接头2-2连通,单向阀2-9固定于自制管接头2-1和自制铰接式接头2-2内部中央;单向阀2-9为微型螺旋插装式结构;低压油箱2-3具有同高压油箱2-6类似的功能结构,具备高低温能量吸收和冗余储能/储油能力,采用圆筒形紧凑化设计,有效容积前者稍大于后者,两者均为自研系列化产品。
37.低压油箱2-3前端设有与高压齿轮泵2-4-4配套的条形油口安装结构,用于系统吸回油和测压,低压油箱2-3的吸油口通过六角头空心螺栓2-5与高压齿轮泵2-4-4直连;低压油箱2-3后端设有5/8”18 unf接口小型充气阀2-3-1。
38.高压油箱2-6每次向比例控制阀组1输出的油液流量为从系统额定工作压力降至额定负载对应压力时高压油箱2-6变化的那部分工作容积;低压油箱2-3的有效容积和压力等级在考虑气体冷缩因素的基础上适配高压油箱2-6工作之所需,并使得高压齿轮泵2-4-4工作在允许的进口真空度或相对压力范围内。
39.高压齿轮泵2-4-4的直流电机+齿轮箱2-4-3采用24v供电微型圆柱石墨电刷电机;高压齿轮泵2-4-4采用微排量高压产品(定义1cc/r以下为微排),电机泵组2-4每次向高压油箱2-6蓄能的时间亦小于每两次蓄能之间的间隔时间;固定half板2-7、2-8将液压站2各段连成一整体,并通过螺钉与进气段表面结构相连固定。
40.当监测到传感器组3.1的压力处于低压能时,电机泵组2-4得电动作向高压油箱2-6蓄能,至达到高压限值时停止。
41.液压站2中所有自制结构件均采用7075-t6材质。
42.p口(高压油箱2-6出口至比例控制阀组1p口)和传感器组3的连接均采用测压接头+测压软管的形式,系统中所有软管及电缆(电缆指的是比例换向阀1-2上的德驰插头1-2-1的出线电缆)使用pa-6尼龙波纹管包裹,硬管6使用碳钢材质确保较高的温度-压降特性,机体后端油缸连接管路,硬管6.2~6.5使用玻纤编制无缝硅胶护套整体包裹,确保系统安全可靠运行。
43.伺服油缸4为一体式活塞与活塞杆结构,伺服油缸4油缸置于尾喷管前端;伺服油缸4油缸总高≤32mm,总长≤200mm;伺服油缸4整体满足系统额定工作压力和尾喷管前端-30℃~+135℃的环境温度要求,尾喷管附近机体表面敷设有预隔热层,尾喷管前端最高应有
200多度,在此温度下油缸无法正常运行,损坏油缸结构,故此敷设有预隔热层,事先敷设好,隔热层和尾喷管与本系统无关。
44.伺服油缸4包括:缸体4-1,盖合在缸体4-1两侧开口处的后缸盖4-2、前缸盖4-3,一端置于缸体4-1内的活塞杆4-4,活塞杆4-4的另一端从前缸盖4-3延伸出缸体4-1,铰接式管接头组合体4-5固连在靠近后缸盖4-2一侧的缸体4-1上、用于连通比例控制阀组1,铰接式管接头组合体4-5结构小巧,位移传感器4-6从后缸盖4-2插入缸体4-1内、用于测量活塞杆4-4的行程。位移传感器4-6采用油缸内置安装结构产品,一体式ptfe塑封出线形式,其线性度误差≤0.1mm,结合控制系统16bit的模拟量分辨精度,为0.5mm以内的同步偏差控制提供了理论保障。
45.前缸盖4-3和活塞杆4-4的配合处设有防尘圈4-7和杆密封4-8,前缸盖4-3和缸体4-1的装配处设有缸体密封4-9,后缸盖4-2和缸体4-1的装配处设有缸体密封4-9,活塞杆4-4和缸体4-1内壁配合处设有活塞密封4-10、活塞支撑环组成4-11。
46.活塞杆4-4前端设计有与作动环固定接口相连的万向连接关节;杆密封4-8、缸体密封4-9、活塞密封4-10均采用氟橡胶vit和/或聚四氟乙烯ptfe材质;一种可调收-扩喷管作动环微型高精度电液比例同步系统搭建预处理方法,在前文所述系统搭建完成时,将预先准备好的压力表工装接入充气工具,分别对低压油箱2-3和高压油箱2-6进行预充气,确保量程和精度(≤1.6级)匹配;通过调试或清洗的方式预先将油缸和管路中注满油液,并在调试动作时通过低压油箱2-3上的测压接头5.1排出系统管路中多余气体,而后通过测压接头5.1向低压油箱2-3中注油加压至所需设定的最高储能压力。溢流阀1-3对由于工作和环境异常而导致的压力升高这一潜在风险起到安全保护作用。
47.结合发动机功能布置区域,系统由比例控制阀组1(位于中部机舱)、液压站2(位于前端进气段上侧)、传感器组3(位于前端进气段下侧)、伺服油缸4(位于尾喷管前端)、管路电缆辅件及相关结构件等组成。
48.其中,液压站2中的电机泵组2-4与高压油箱2-6组成闭式油气弹性动力源主体设备,向比例控制阀组1输出持续高压油,其与提供吸回油的低压油箱2-3一道,组成液压循环系统;两只伺服油缸4分别推动喷管两侧作动环,各自由比例换向阀1-2(图里是1-2.1和1-2.2)单独位置闭环控制,在有限的结构利用空间内精确实现喷管同步稳定收、扩的同时,最大限度改善了由于结构热变形而带来的动作偏差;当监测到传感器组3.1的压力处于低压能时,电机泵组2-4得电动作向高压油箱2-6蓄能,至达到高压限值时停止,实现二次动力输出的同时,提高了系统的功率利用效率,有效避免了能量损耗和发热问题;传感器组3.2~3.5监测油缸两腔压力,并换算成工作负载供整机分析处理;溢流阀1-3对由于工作和环境异常而导致的压力升高这一潜在风险起到安全保护作用,进一步提高系统功能动作的稳定性和可靠性。
49.图3为液压站2外形结构示意图。其中,自制管接头2-1和自制铰接式接头2-2连通高压齿轮泵2-4-4与高压油箱2-6,单向阀2-9为微型螺旋插装式结构,固定于两接头内部中央,整体遵循紧凑化配套设计;低压油箱2-3具有同高压油箱2-6类似的功能结构,具备高低温能量吸收和冗余储能/储油能力,采用圆筒形紧凑化设计,有效容积前者稍大于后者,两
者均为自研系列化产品。2-3前端设有与高压齿轮泵2-4-4配套的条形油口安装结构,用于系统吸回油和测压,其吸油口同时通过六角头空心螺栓2-5与2-4-4直连。2-3后端设有5/8
”ꢀ
18 unf接口小型充气阀,可满足低压下的充气精度;直流电机+齿轮箱2-4-3采用24v供电微型圆柱石墨电刷电机,具备高动态特性和转矩密度,运转平稳;高压齿轮泵2-4-4采用微排量高压产品,具备高容积效率和低泄漏量,自吸能力强,确保系统所需流量和压力稳定输出的同时进一步提高了系统效率、减少发热;即使油缸处于持续动作状态,电机泵组2-4每次向高压油箱2-6蓄能的时间亦小于每两次蓄能之间的间隔时间;两者均可满足10000米高空和进气段-30~+80℃环境温度工况下的使用需求;固定half板2-7、2-8将液压站2各段连成一整体,并通过螺钉与进气段表面结构相连固定。2中所有自制结构件均采用7075-t6材质以满足轻量化和高强度的技术要求。
50.高压油箱2-6每次向比例控制阀组1输出的油液流量为从系统额定工作压力降至额定负载对应压力时2-6变化的那部分工作容积。通过考虑各工况下温差所带来的气体冷缩和油液热胀,对该工作容积进行修正,同时考虑比例控制余量系数及阀泄漏,以确保流量的充分供给和系统的合理运行;同理,低压油箱2-3的有效容积和压力等级在考虑气体冷缩因素的基础上满足高压油箱2-6工作之所需,并使得高压齿轮泵2-4-4工作在允许的进口真空度或相对压力范围内。
51.图4~5为比例控制阀组1外形结构示意图。其中,比例控制阀块1-1采用7075-t6材质,表面阳极氧化处理增强其环境适应性,多余部分通过钻孔去料进一步减轻了重量;本系统采用三角形速度-时间控制算法作为伺服油缸4的基本运动模式,目标动作时间t’确定后,前一半时间控制伺服油缸4恒加速运动至峰值动作速度vmax,后一半时间控制伺服油缸4恒减速运动至最终停止,整个运动过程具有相同的运动加速度绝对值,从而确保油缸动作的稳定性。
52.△
aoba和
△
aob的面积分别即为伺服油缸4的实时理论位移sa和目标位移值s’,分别将速度和位移同时间之间的关系va(t)和sa(t)导入plc,控制器根据对应参数化软件(基于pc)中给定的“单位行程对应动作时间”值自动计算任意动作工况下的目标动作时间t’,通过在软件界面中对相关参数进行在线监测和修改优化,及对“比例电磁铁非线性输出调节”窗口进行设定以屏蔽比例阀“死区”并改善其非线性问题,实现对伺服油缸4运动过程的精确控制。
53.plc接收来自位移传感器4-6的实时实际位移值作为反馈,并与实时理论位移值sa(t)或目标位移值s’进行比较,形成位置闭环控制;实时理论速度值va(t)产生sa(t),决定实时理论阀芯开度。通过对pid控制中相关系数的设定,最终输出经修正的实时位移令值;本系统中,比例换向阀1-2采用3通径板式阀,具有精确阀芯适配性、低泄漏、长寿命等优点,响应频率40~50hz;位移传感器4-6采用4~20ma模拟量信号输出形式,线性度误差≤0.1mm,接收端plc分辨精度16bit,位移传感器4-6结构上采用油缸内置及一体式ptfe塑封出线形式;液压回路中溢流阀1-3在具备优异开关响应速度的同时,亦具备可以忽略不计的极低泄漏量技术指标。综合上述控制功能实现形式及技术性能指标,实现了对双缸全行程位移偏差≤0.5mm的高精度同步控制。
54.比例控制阀组1外形结构配套中部机舱现有空间设计,通过换装扁平形德驰插头、铰接式管接头和测压接头配搭等形式,充分实现了紧凑化和轻量化的整体结构要求。
55.图6~7为伺服油缸4结构示意图。采用一体式活塞与活塞杆结构,活塞(杆)4-4前端后期可根据需要设计与作动环固定接口相连的万向连接关节;铰接式管接头组合体4-5结构小巧,油缸总高≤32mm,总长≤200mm,满足尾喷管前端紧凑化安装空间要求;油缸密封件采用vit(氟橡胶)和/或ptfe(聚四氟乙烯)材质;位移传感器4-6采用油缸内置安装结构产品,一体式ptfe塑封出线形式,其线性度误差≤0.1mm,结合控制系统16bit的模拟量分辨精度,为0.5mm以内的同步偏差控制提供了理论保障;油缸整体满足系统额定工作压力和尾喷管前端-30℃~+135℃的环境温度要求(尾喷管附近机体表面敷设有预隔热层,尾喷管前端最高应有200多度,在此温度下油缸无法正常运行,损坏油缸结构,故此敷设有预隔热层,预隔热层是事先敷设好,隔热层和尾喷管属于现有技术,与本系统创新无直接关联。)。
56.针对本系统管路连接件部分,p口和传感器组3的连接均采用测压接头+测压软管的形式,既增加了布置的灵活性,又减轻了常规连接的重量;考虑到本系统高低温、冲击碰撞等极端工况,系统中所有软管及电缆使用pa-6尼龙波纹管包裹,硬管使用碳钢材质确保较高的温度-压降特性,机体后端油缸连接管路使用玻纤编制无缝硅胶护套整体包裹,确保系统安全可靠运行。
57.元器件选型方面,采用参数富余设计,确保全范围指标覆盖;阀组、阀件、管路等采用集成化布置,尽可能设计选用标准化、自主系列化和通用化产品;对于关键功能器件或辅件使用业界知名认可的可靠产品。
58.比例控制阀组、液压站、传感器组、伺服油缸、带排气测压接头、硬管及测压软管总质量≤7kg,满足发动机整体质量和性能要求。
59.在前文所述系统搭建完成时,将预先准备好的压力表工装接入充气工具,分别对低压油箱2-3和高压油箱2-6进行预充气,确保量程和精度(≤1.6级)匹配;通过调试或清洗的方式预先将油缸和管路中注满油液,并在调试动作时通过低压油箱2-3上的测压接头5.1排出系统管路中多余气体,而后通过5.1向2-3中注油加压至所需设定的最高储能压力。
60.本发明中,对于伺服油缸4的控制如图8所示。每条伺服油缸4由各自的比例换向阀1-2单独控制。plc内置pid闭环控制调节功能,其通过向比例换向阀1-2的线圈输出实时电流控制阀芯相应侧开度大小,从而实现伺服油缸4伸缩动作的实时位置闭环控制。plc仅需接收外部发来的油缸使能、伸出和缩回开关量信号以触发油缸动作的执行。
61.本系统采用三角形速度-时间控制算法作为伺服油缸4的基本运动模式(如图9所示),目标动作时间t’确定后,前一半时间控制伺服油缸4恒加速运动至峰值动作速度v
max
,后一半时间控制伺服油缸4恒减速运动至最终停止,整个运动过程具有相同的运动加速度绝对值,从而确保油缸动作的稳定性。
62.△
aoba和
△
aob的面积分别即为伺服油缸4的实时理论位移sa和目标位移值s’,分别将速度和位移同时间之间的关系va(t)和sa(t)导入plc,控制器根据对应参数化软件(基于pc)中给定的“单位行程对应动作时间”值自动计算任意动作工况下的目标动作时间t’,通过在软件界面中对相关参数进行在线监测和修改优化,及对“比例电磁铁非线性输出调节”窗口进行设定以屏蔽比例阀“死区”并改善其非线性问题,实现对伺服油缸4运动过程的精确控制。
63.plc接收来自位移传感器4-6的实时实际位移值作为反馈,并与实时理论位移值sa(t)或目标位移值s’进行比较,形成位置闭环控制,其内置pid位置闭环控制调节框图如图
10所示;实时理论速度值va(t)产生sa(t),决定实时理论阀芯开度。通过对pid控制中相关系数的设定,最终输出经修正的实时位移令值;本系统中,比例换向阀1-2采用3通径板式阀,具有精确阀芯适配性、低泄漏、长寿命等优点,响应频率40~50hz;位移传感器4-6采用4~20ma模拟量信号输出形式,线性度误差≤0.1mm,接收端plc分辨精度16bit,位移传感器4-6结构上采用油缸内置及一体式ptfe塑封出线形式;液压回路中溢流阀1-3在具备优异开关响应速度的同时,亦具备可以忽略不计的极低泄漏量技术指标。
64.综合上述控制功能实现形式及技术性能指标,实现了对双缸全行程位移偏差≤0.5mm的高精度同步控制。
65.当需要相对长期保持某一喷管开度时,若控制系统通过伺服油缸4的位移传感器4-6监测到实际位移产生临界微小变化,或通过传感器组3分析出油缸双腔压力异常,则其发出指令控制油缸按基本运动模式动作至既定位置。
66.前述对本发明的具体示例性实施方案的描述是为了说明和例证的目的。这些描述并非想将本发明限定为所公开的精确形式,并且很显然,根据上述教导,可以进行简单的改变和变化。对示例性实施例进行选择和描述的目的在于解释本发明的特定原理及其实际应用,从而使得本领域的技术人员能够实现并利用本发明的各种不同的示例性实施方案以及各种不同的选择和改变。本发明的范围意在由权利要求书及其等同形式所限定。