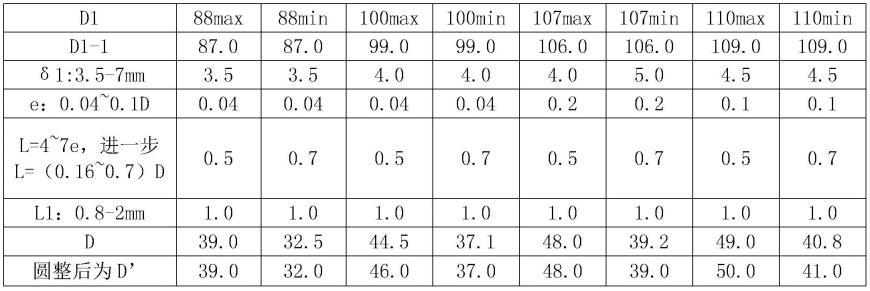
1.本发明属于压缩机技术领域,特别是涉及一种转子式压缩机。
背景技术:2.随着技术发展,转子式压缩机的能效要求越来越高。为提高能效,需要合理筒体内径与压缩机气缸的关系,以便使压缩机成本及能效达到最优。
3.在筒体内径不变的情况下,压缩机气缸内径越大,同样气缸高度下,压缩机可布局排量越大。需求同样冷量时,压缩机筒径越小,在同样材质下,压缩机成本越低。但筒体与气缸缸体内径关系不适当时,压缩机弹簧、滑块将无法正常工作,导致压缩机失效。
技术实现要素:4.本发明在此的目的在于提供一种转子式压缩机,该压缩机能够有效解决压缩机失效问题。
5.为此,本发明提供的转子式压缩机包括压缩机筒体和气缸,所述压缩机筒体的内径与所述气缸的内径满足以下关系:
[0006][0007]
其中:d为气缸直径,d1为压缩机筒体内径,l1为滑块退回时与漏打孔端面之间的距离,δ1为漏刀孔外端面与气缸内壁之间的距离。
[0008]
在一些实施方式中,所述δ为3.5-7mm。
[0009]
在一些实施方式中,所述l1为0.6-3mm。
[0010]
采用本技术方案,能实现的技术问题至少包括:
[0011]
1)本压缩机中筒体和气缸内径之间的关系,一定程度上解决了气缸布置不合理,导致弹簧过长、立定性不好而造成的弹簧、滑块无法正常工作压缩机失效的问题。
[0012]
2)本压缩一定程度上解决了因气缸缸径过大造成的弹簧滑块无法安装问题。
[0013]
3)本压缩机漏刀孔外端面与气缸内壁之间的距离配置为3.5-7mm,一定程度上解决了因气缸边缘太薄造成的弹簧安装失效问题。
附图说明
[0014]
此处的附图被并入说明书中并构成本说明书的一部分,示出了符合本发明的实施例,并与说明书一起用于解释本发明的原理。显而易见地,下面描述中的附图仅仅是本发明的一些实施例,对于本领域普通技术人员来讲,在不付出创造性劳动的前提下,还可以根据这些附图获得其他的附图。在附图中:
[0015]
图1为本发明记载的转子式压缩机结构示意图;
[0016]
图2为本发明记载的转子式压缩机气缸的结构示意图;
[0017]
图3为本发明记载的转子式压缩机筒体及气缸截面示意图;
[0018]
图4为本发明记载的转子式压缩机筒体及气缸截面尺寸关系图;
[0019]
图5为本发明记载的压缩机系统的结构示意图;
[0020]
图6为本发明记载的吸气孔一种结构示意图;
[0021]
图7为图6的平面图;
[0022]
图8为本发明记载的吸气孔另一种结构示意图;
[0023]
图9为图8的平面图;
[0024]
图10为本发明记载的气缸插管钢铜结构示意图;
[0025]
图11为本发明记载的气缸插管锥形引导段的结构示意图;
[0026]
图12为本发明记载的气缸插管缩口引导段的结构示意图;
[0027]
图13为本发明记载的转子外圆与气缸的装配图。
具体实施方式
[0028]
现在将参考附图更全面地描述示例实施方式。然而,示例实施方式能够以多种形式实施,且不应被理解为限于在此阐述的范例;相反,提供这些实施方式使得发明将更加全面和完整,并将示例实施方式的构思全面地传达给本领域的技术人员。
[0029]
本发明提供了一种转子式压缩机,该压缩机的筒体的内径与气缸的内径满足一定关系,使筒体与气缸选择更合理,压缩机能效更高,安全性更好。
[0030]
如图1所示,本公开的转子式压缩机包括气缸101、进气口102、弹簧103、滑块104、排气阀105、安装于气缸101腔体内的转子107、与转子107装配在一起的曲轴106以及压缩机筒体109。气体从进气口102中进入,经压缩后经排气阀105排出。
[0031]
结合图2-4,气缸101包括第一装配端1011、第二装配端1012和装配于第一装配端1011和第二装配端1012之间的带装配腔的装配体1013,第一装配端1011上开设有用于滑块104一端装配的漏打孔110,漏打孔110为非闭合孔,包括第一开口端和第二开口端,以第一开口端和第二开口端为起点,向装配体1013方向延伸开口形成用于提供滑块104滑动的滑道111;滑块104被装配于漏打孔110内的一端与弹簧103的一端装配在一起,弹簧103的另一端装配于第一装配端1011的内侧壁上。转子107被配置位于装配体1013的装配腔内,且能够能够在电场力的作用下沿装配体的腔体内壁滑动,实现对气体的压缩,滑块104在弹簧103处于伸展状态下端部抵触转子107的外壁,在弹簧103和转子107的作用下滑块104在滑道111内滑动实现气体压缩。
[0032]
本公开中,曲轴106具有一偏心部及偏心量e,曲轴106将电机的旋转力传递给转子107,曲轴偏心部带动活塞在装配体的装配腔内旋转,通过偏心量e改变转子与气缸形成的容积,从而实现气体压缩;并通过偏心部及偏心e,使滑块在气缸滑槽内往复运动。通过弹簧103弹力压缩滑块104,使滑块104和转子107紧密结合,隔绝高压腔和低压腔。
[0033]
本公开中,压缩机筒体109的内径与气缸101的内径满足以下关系:d=其中:d为气缸直径,d1为压缩机筒体内径,l1为滑块退回时与漏打孔端面之间的距离,δ1为漏刀孔外端面与气缸内壁之间的距离,如图4所示。
[0034]
本公开中,曲轴6的曲轴偏心e为(0.05~0.1d),滑块长l=4~7e=(0.20~0.7)d。
[0035]
本公开的压缩机通过筒径与气缸体内径的关系,使压缩机缸体与筒径选择更合
理,压缩机能效更高,压缩机可靠性性更好。
[0036]
为了说明本发明所提供的具体的设计方法,以采用r32工质、为φ88、φ100、φ107、110的转子式压缩机筒径为例予以说明:
[0037][0038]
d代表计算出的气缸直径,d’为圆整后实际缸径;d1为筒体内径,d1-1为筒体内径d1减去1mm;表格中单位有max和min是表示本筒径上气缸的最大内径和最小内径。
[0039]
本发明所提供压缩机筒体和气缸的内径关系适用于任何制冷工质使用场合的转子式压缩机;适用于不同的领域应用场合的转子式压缩机,如空调制冷、热泵采暖、冷冻冷藏等;适用于不同排量的转子式压缩机。
[0040]
本公开中,气缸101的第一装配端1011上开设有用于与装配腔连通的吸气孔3,用于与外部辅助设备连通。
[0041]
如图5所示,配置压缩机本体1和气液分离器2,气液分离器2(也称储液器)与吸气孔3连通,用于分离未完全气化的液态制冷剂,保证进入压缩机气缸101内的制冷剂为干蒸汽。
[0042]
气液分离器2的进气管201与管路的连接方式为铜管焊接型,制冷剂经管路进入气液分离器2,气液分离器2的出气弯管202通过连接管5、气缸插管4与吸气孔3连接,实现气液分离器2与气缸101的连通。具体是:连接管5为铜钢结构件,铜管、钢管两者通过炉中钎焊连接形成铜钢结构件,包括钢管端501和铜套端502。连接管5延伸出压缩机本体1,钢管端501有喇叭口与压缩机本体1的筒体109电阻凸焊连接,气缸插管4的一端插装入铜套端502并延伸入吸气孔3,铜套端502与气缸插管4、出气弯管202钎焊连接。
[0043]
本公开中,气缸插管4可以被配置为铜钢结构件,如图10所示。铜管、钢管两者通过炉中钎焊连接形成铜钢结构件,包括钢管部分和铜管部分。钢管部分插入吸气孔3,通过过盈配合进行密封连接,铜管部分与连接管、出气弯管钎焊连接。
[0044]
由于压缩机本体1和气液分离器2均分别加工制造成型,两者之间通过气缸插管4、连接管5连通,气缸插管4的钢管部分外圆、吸气孔尺寸及形状公差需要精度高,否则当气缸插管4被配置为铜钢结构件时,由于钢管部分在装入吸气孔3时,所需的装入力较大,容易将压缩机本体内已定好芯的本体装配精度破坏。如图13所示,在装入较大时,导致cp间隙加大或定心角度偏离设计值,压缩机运行过程中冷媒泄漏加大,容积效率降低。本公开中cp间隙指转子外圆与气缸内径之间的间隙,图13中0.02即为cp间隙。
[0045]
为此,本公开将气缸插管4配置为全铜材质结构件,吸气孔材料为铸铁或粉末冶金材质,铜的气缸插管4与吸气孔3过盈连接,因为铜材质的可塑性,使两者在较小的装入力下,能够有更大的过盈量连接,确保气缸插管4与吸气孔3的可靠密封。
[0046]
本公开中气缸插管4包括a端和b端,a端用于插入吸气孔3与吸气孔3过盈配合连接,气缸插管4的b端用于与辅助设备连通。如图11、12所示,气缸插管4的a端包括配合段401和引导段402,配合段401与吸气孔3过盈配合,引导段402在气缸插管4插入吸气孔3时起到引导作用且易插入。
[0047]
如图11所示,引导段402前端为一锥形结构,长度为ι,取值范围为1mm≤ι≤5mm,引导段402最小外径φdc,配合段402的外径为φd时,φdc/φd≥98%。
[0048]
如图12所示,引导段402为柱形面,当为柱形面时,端部尺寸小于引导段402其它部分尺寸,便于气缸插管4插装,配合段401与引导柱形面圆滑过渡。此结构下,引导段402的长度为ι,取值范围为1mm≤ι≤5mm,其外径φdc略小于配合段外径φd,两者的比值≥98%。
[0049]
本公开比值实现了有效地的引导,比值过大,无引导作用,比值过小,气缸插管4内径有效流通面积成半径平方的数值缩小,增大了制冷剂的流通阻力。
[0050]
应当理解的是,上述对全铜材质的气缸插管4的描述也适用于钢铜结构的气缸插管。
[0051]
铜材质气缸插管优点为可塑性强,缺点是材质软,在气缸插管压入气缸吸气孔过程中,插管外圆与吸气孔边缘作用,产生铜屑,压缩机在吸气过程中,铜屑被制冷剂气体带入泵体内部,易造成机芯卡死故障。因此,结合图6、7所示,本公开的吸气孔3向气缸插管插入端有一扩口段301,与扩口段301连接的为直线段302。扩口段301的扩口母线为圆弧,圆弧半径为r,1mm≤r≤10mm,r与直线段302相切,圆弧深度1mm≤h≤3mm。圆弧与气缸外圆相贯形成相贯线5为一直径为d的圆。吸气孔3直线段302的直径为d,d/d>0.90,此处将比值调整为0.9,比值过大,扩口无法起到引导作用,比值过小,相贯线与气缸端面距离变小。
[0052]
该结构使气缸插管4压入气缸吸气孔3时,气缸插管4外圆与吸气孔3的扩口圆弧接触,通过挤压变形达到过盈配合。
[0053]
扩口段301形成光滑结构,光滑的与吸气孔3相切的扩口结构是为了避免铜材质气缸插管压入气缸吸气孔的过程中产生铜屑。
[0054]
如图8、9所示,本公开中,吸气孔3的扩口段301向外有一倒角,形成倒角结构,倒角深度1mm≤h≤3mm,倒角两边的夹角为α,5
°
≤α≤45
°
且α与吸气孔3的直线段302为圆角r过渡。扩口段301和直线段302之间采用圆角r过渡,且扩口段301为倒角结构,形成光滑的过渡能够避免铜材质气缸插管压入气缸吸气孔过程中,插管外圆与吸气孔锋利的边缘作用,产生铜屑,当铜屑被制冷剂气体带入泵体内部,易造成机芯卡死故障。
[0055]
本公开中,气缸插管4被配置为一薄壁件,厚度δ在0.4≤δ≤0.7范围选取,气缸插管4与气缸吸气孔3之间的过盈量为0.02~0.09。厚度选取过薄插管与气缸吸气孔密封不严,导致气体泄漏,厚度选取过厚,一方面浪费材料,另一方面因为气缸插管与气缸吸气孔为过盈配合,气缸插管需要装入的力增大,容易将已定芯好的泵体结构破坏。在此,提供了一组铜管厚度δ与过盈量配合的范围关系见下表:
[0056]
表1δ与过盈量范围关系表
[0057]
δ值过盈量优选值0.4≤δ≤0.50.07~0.090.5≤δ≤0.60.04~0.070.6≤δ≤0.70.02~0.04
[0058]
本公开,气液分离器2的出气弯管202与吸气口3通过气缸插管4连通,储液器的进气直管与空调器管路相连,从而实现低温低压的制冷剂气体吸入气缸腔体,通过机芯转子的压缩,成为高温高压气体,从压缩机排气管112排出。
[0059]
本公开采用铜质气缸插管,工艺简单,效率高,零件单一,但是因为铜材料较软,与铸铁件过盈连接时,气缸吸气孔的棱边易损伤表面产生铜屑,当铜屑被制冷剂气体带入泵体内部时,易停留在泵体结构件的配合间隙处,造成泵体卡死故障,使压缩失效。本方案中的气缸吸气孔结构,采用r角或圆弧过渡,避免了棱边,同时合理的气缸插管壁厚和过盈量限定,使气缸插管插入气缸吸气孔过程中,插管外圆与吸气孔的扩口圆弧接触,通过挤压变形达到过盈配合。
[0060]
本方案将气缸插管配置为铜钢结构件时,两者通过炉中钎焊连接。零件生产节拍慢,且钢管部分需要精磨外圆确保零件精度,否则钢管压入铸铁或粉末冶金气缸的吸气孔时,硬碰硬,所需的装入力大,易将已定好芯的泵体装配精度破坏,导致cp间隙加大或定心角度偏离设计值,压机运行过程中冷媒泄漏加大,容积效率降低;但本公开采用全铜材质的气缸插管解决了铜钢结构件所存在的问题,更有利于装配。
[0061]
本领域技术人员应当理解的是,本发明包含且不局限于所述的气缸吸气孔向外的圆滑扩口和倒角过渡,还包含其他防止铜气缸插管在过盈配合插入过程中,铸铁气缸的吸气孔尖边铲伤铜气缸插管外圆,产生铜屑的圆滑结构。
[0062]
本公开的压缩机本体还可以采用如一种全封闭型转子式压缩机(公开(告)号:cn106678044a,公开(告)日:2017.05.17)所描述的转子式压缩机;或者,一种转子式压缩机(公开(告)号:cn104564681a,公开(告)日:2015.04.29);或者,一种卧式微型压缩机(公开(告)号:cn103206381a,公开(告)日:2013.07.17);吸气孔3被开设于与压缩机的气缸相连通的位置,实现如气液分离器的辅助装置与气缸连通,使进入气缸的制冷剂为干蒸汽;或者,辅助装置可以是制冷剂储液罐,通过气缸插管4实现压缩机与抽气装置的连通,使制冷剂直接进入压缩机气缸。
[0063]
本公开已由上述相关实施例加以描述,然而上述实施例仅为实施本公开的范例。必需指出的是,已揭露的实施例并未限制本公开的范围。相反,在不脱离本公开的精神和范围内所作的变动与润饰,均属本公开的专利保护范围。