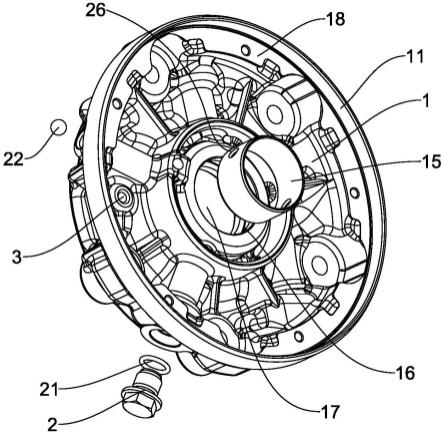
1.本实用新型涉及汽车结构领域,具体涉及一种用于混合动力变速器的分油器总成。
背景技术:2.分油器总成一般通过螺栓固定在壳体上,通过与壳体结合面密封配合,实现自动变速器液压系统高、低压油路的分配与传递,具备体积小,油路转换灵活等特点,能很好地降低自动变速器壳体液压油路复杂程度和油道的加工难度;传统分油器总成一般由分油器壳、油道堵头、衬套等结构组成,往往要求具备一定的承载强度,壳体通常采用铸铁材料(如灰铸铁或球墨铸铁),质量较重,而衬套的安装需要一定的方向性,增加装配工艺防错难度。混和动力(以下简称混动)变速器分油器总成一般设置在驱动电机定子腔体的内侧,其上往往还安装有旋变定子,需有一定的减弱磁场干扰能力。
技术实现要素:3.本实用新型的目的是提供一种能够减弱磁场对旋变定子活动干扰的能力的用于混合动力变速器的分油器总成。
4.为实现上述目的,本实用新型采用如下技术方案:用于混合动力变速器的分油器总成,包括分油器壳体,所述分油器壳体上设有环形凸缘,所述环形凸缘围合成用于包络旋变定子的放置腔,所述放置腔的口部设有隔磁罩,当旋变定子设置于所述放置腔内时旋变定子的两端分别与所述放置腔的底部和隔磁罩相抵,所述分油器壳体上设有低压油路、若干个第一高压油路和第二高压油路,所述分油器壳体中间设有通孔,所述通孔内配合设有耐磨衬套,耐磨衬套内设有油孔。
5.使用时,首先将旋变定子放入到环形凸缘上的放置腔内,再通过隔磁罩盖在旋变定子上进行与分油器壳体固定,将旋变定子包络在隔磁罩与环形凸缘之间,使用时通过隔磁罩进行减弱磁场对旋变定子活动干扰的能力。
6.优选地,所述放置腔的底部形成有若干个用于支承旋变定子的凸板,所述放置腔位于隔磁罩与凸板之间,所述环形凸缘的环形内壁用于旋变定子的径向定位。
7.优选地,所述分油器壳体的通孔中部设有环形凹槽,所述环形凹槽与耐磨衬套之间配合设有环形油路,所述环形油路以实现耐磨衬套压装不指定方向。
8.优选地,所述耐磨衬套与分油器壳体的通孔过盈配合。
9.优选地,每个所述第一高压油路的一端与环形油路连接,每个所述第一高压油路-的另一端采用带o型圈的螺堵进行密封,系统中高压油经第一高压油路进入环形油路,再经耐磨衬套中的油孔进入系统;每个所述第二高压油路一端相互连接,每个所述第二高压油路另一端采用带o型圈的螺堵进行密封,系统中高压油经第二高压油路再次回到系统中;所述低压油路一端采用密封钢球进行密封,系统中低压油经低压油路再次回到系统。上述设置通过高压油路采用带o型圈的螺堵密封,避免了因材质热变形量不一致,造成高压油路过
盈封堵失效的隐患,可实现承受最高100bar系统油压不失效。
10.优选地,所述分油器壳体上设有用于线束端子固定的等电位凸台。
11.优选地,所述分油器壳体采用比铸铁材料强度更高的铝合金材质压制成。通过选择比铸铁材料强度更高的铝合金材质,使其铸造及加工工艺性优于铸铁材料,减轻了重量,提高燃油经济性。
12.本实用新型具有的优点是1、能够在保持分油器总成实现油路分配与传递、承载及包络关联件的情况下,通过选择比铸铁材料强度更高的铝合金材质,使其铸造及加工工艺性优于铸铁材料,减轻了重量,提高燃油经济性;2、通过本分油器壳体结构设计,可实现关联件旋变定子和隔磁罩盖的安装定位;减少磁场干扰作用;3、通过分油器内孔环形凹槽设计,实现了衬套压装简易化;4、通过采用螺堵密封高压油路,可实现承受最高100bar系统油压不失效;5、通过设置等电位凸台结构,可实现关联件等电位功能。
附图说明
13.图1为本实用新型一种用于混合动力变速器的分油器总成的结构示意图。
14.图2为本实用新型用于混合动力变速器的分油器总成的前视图。
15.图3为图2中a-a的剖视图。
16.图中,分油器壳体1、环形凸缘11、环形油路12、隔磁罩13、放置腔14、耐磨衬套15、环形凹槽16、通孔17、凸板18、螺堵2、o型圈21、密封钢球22、低压油路23、第一高压油路24、第二高压油路25、油孔26、等电位凸台3。
具体实施方式
17.下面根据附图和具体实施例对本实用新型作进一步描述。
18.由图1至图3所示,本实用新型的一种用于混合动力变速器的分油器总成,包括分油器壳体1,分油器壳体1采用比铸铁材料强度更高的铝合金材质压制成,分油器壳体1上设有用于线束端子固定的等电位凸台3,分油器壳体1上设有环形凸缘11,环形凸缘11围合成用于包络旋变定子的放置腔14,放置腔14的口部设有隔磁罩13,当旋变定子设置于放置腔14内时旋变定子的两端分别与放置腔14的底部和隔磁罩13相抵,放置腔14的底部形成有若干个用于支承旋变定子的凸板18,放置腔14位于隔磁罩13与凸板18之间,环形凸缘11的环形内壁用于旋变定子的径向定位。
19.由图1、图3所示,分油器壳体1中间设有通孔17,通孔17内配合设有耐磨衬套15,耐磨衬套15中设有油孔26,分油器壳体1的通孔17中部设有环形凹槽16,环形凹槽16与耐磨衬套15之间配合设有环形油路12,环形油路12以实现耐磨衬套15压装不指定方向,耐磨衬套15与分油器壳体1的通孔17过盈配合。
20.由图1、图2所示,分油器壳体1上设有两个第一高压油路24、两个第二高压油路25与低压油路23,可实现100bar系统油压下不泄露;每个第一高压油路24的一端与环形油路12连接,每个第一高压油路24的另一端采用带o型圈21的螺堵2进行密封,系统中高压油经第一高压油路24进入环形油路12,再经耐磨衬套16中的油孔26进入系统;每个第二高压油路25一端相互连接,每个第二高压油路25另一端采用带o型圈21的螺堵2进行密封,系统中高压油经第二高压油路25再次回到系统中;低压油路23一端采用密封钢球22进行密封,系
统中低压油经低压油路23再次回到系统。
21.在使用时,首先对分油器壳体1固定,耐磨衬套15对准通孔17,通孔17的环形凹槽16的结构设计以实现耐磨衬套15压装不指定方向,方便进行装配。
22.其次,将环形凸缘11的环形内壁对旋变定子径向定位将旋变定子放入到隔磁罩13与凸板18之间的放置腔14内,然后将隔磁罩13盖在旋变定子上,通过螺栓对准凸板18上的螺纹孔进行隔磁罩13与凸板18固定,再通过等电位凸台3对线束端子固定。
23.第一高压油路24和第二高压油路25可实现100bar系统油压下不泄露,每个第一高压油路24的一端与环形油路12连接,每个第一高压油路24的另一端采用带o型圈21的螺堵2进行密封,系统中高压油经第一高压油路24进入环形油路12,再经耐磨衬套16中的油孔26进入系统;每个第二高压油路25一端相互连接,每个第二高压油路25另一端采用带o型圈21的螺堵2进行密封,系统中高压油经第二高压油路25再次回到系统中;低压油路23一端采用密封钢球22进行密封,系统中低压油经低压油路23再次回到系统,可实现100bar系统油压下不泄露。
24.最后,将分油器连接在混合动力变速器上,混合动力变速器启动带动分油器启动,一个高压油由系统经高压油路24进入环形油路12,经耐磨衬套16中的油孔再次回到系统;另一个高压油由系统经两个相互连接的高压油路25再次回到系统;低压油由系统经低压油路23再次回到系统;通过环形凸缘11与隔磁罩13之间配合形成的封闭腔14减少磁场干扰作用。