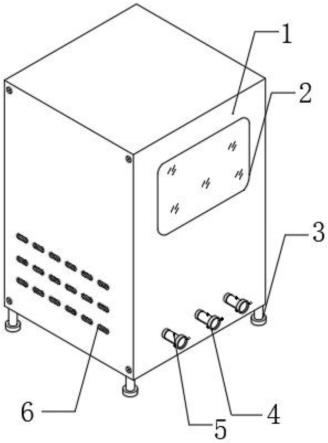
1.本实用新型属于气动隔膜泵技术领域,涉及一种气动隔膜泵故障检测装置。
背景技术:2.气动隔膜泵是一种新型输送机械,是国内最新颖的一种泵类。采用压缩空气为动力源,对于各种腐蚀性液体均可使用。
3.根据中国专利号为“cn212774707u”公开了“一种气动隔膜泵故障检测装置”,包括标准气源、进水设备和工况模拟设备;所述标准气源的出口连接气动隔膜泵的动力入口;所述进水设备连接所述气动隔膜泵的入口,用于给所述气动隔膜泵的入口提供流体;所述工况模拟设备用于将所述气动隔膜泵出口处流体调整至模拟工况。本实用新型为气动隔膜泵提供标准气源,并在气动隔膜泵出口处对流体的物理参数进行工况模拟,通过模拟结果观察气动隔膜泵是否能正常工作,还可以在检测现场直观找出气动隔膜泵的故障点。
4.上述技术方案在实际检测的过程中,由于连接管道的固定式设置,不方便与气动隔膜泵的连接,影响检测效率,同时在检测的过程中无法保证连接处的密封性,容易造成检测数据有偏差,从而影响气动隔膜泵故障的精准定位。
技术实现要素:5.本实用新型的目的在于提供一种气动隔膜泵故障检测装置,以解决上述背景技术中提出的问题。
6.本实用新型的目的可通过下列技术方案来实现:一种气动隔膜泵故障检测装置,包括检测箱体和气动隔膜泵进液管,所述检测箱体的一侧固定设有固定管,所述固定管的顶部固定安装有检测传感器,所述固定管的内部固定安装有万向管,所述万向管的端头处固定设有连接座,所述连接座与气动隔膜泵进液管套接,所述连接座的两侧均螺纹连接有螺纹固定杆,两根所述螺纹固定杆的端头处与气动隔膜泵进液管的外壁接触连接,所述连接座的内部固定设有环形密封气囊,所述环形密封气囊的进气端固定设有支气管,所述检测箱体的底部开设有空腔,所述空腔的底部固定安装有储液箱,所述储液箱的内部固定安装有循环泵,所述循环泵的出液端与固定管的一端固定连接,所述空腔一侧分别安装有第一气泵和第二气泵,所述第一气泵的出气端通过导管与气动隔膜泵的进气端固定连接,所述第二气泵的出气端与支气管的一端固定连接。这样设置的目的是通过设有的连接座便于与气动隔膜泵进液管套接,并通过环形密封气囊的配合,有效的保证了连接部位的密封性,有效的避免了因连接部位密封问题,影响检测数据的准确性,从而影响气动隔膜泵故障检测定位。
7.在上述的一种气动隔膜泵故障检测装置中,所述空腔的一侧等距开设有多个气孔,多个所述气孔的内部均固定安装有防尘网。这样设置的目的是通过防尘网的设置,具有较好的防尘效果。
8.在上述的一种气动隔膜泵故障检测装置中,所述检测箱体正面的顶部固定安装有
数据显示面板,所述检测箱体的内部固定安装有处理器,多个所述检测传感器均通过处理器与数据显示面板电性连接。这样设置的目的是通过数据显示面板显示检测数据。
9.在上述的一种气动隔膜泵故障检测装置中,所述连接座的内径与气动隔膜泵进液管的端头处尺寸相匹配。这样设置的目的是降低连接部位的缝隙。
10.在上述的一种气动隔膜泵故障检测装置中,所述检测箱体底端的四个边角处均固定安装有支撑腿,四个所述支撑腿的底端开设有均匀分布的防滑纹。这样设置的目的是保证检测箱体的稳定。
11.在上述的一种气动隔膜泵故障检测装置中,两个所述螺纹固定杆的端头处均固定设有旋钮。这样设置的目的是方便螺纹固定杆的转动。
12.与现有技术相比,本实用新型一种气动隔膜泵故障检测装置的优点为:
13.1、通过设有的连接座便于与气动隔膜泵进液管套接,并通过环形密封气囊的配合,有效的保证了连接部位的密封性,有效的避免了因连接部位密封问题,影响检测数据的准确性,从而影响气动隔膜泵故障检测定位。
14.2、连接座与固定管之间设置有万向管,通过万向管的设置,便于调节连接座的方向,同时可调节连接座的位置,方便检测箱体与气动隔膜泵的连接,有效的提高了检测效率。
附图说明
15.图1是本实用新型一种气动隔膜泵故障检测装置的结构示意图。
16.图2是本实用新型一种气动隔膜泵故障检测装置的连接座结构示意图。
17.图3是本实用新型一种气动隔膜泵故障检测装置的空腔内部结构示意图。
18.图4是本实用新型一种气动隔膜泵故障检测装置的固定管与连接座连接结构示意图。
19.图中,1、检测箱体;2、数据显示面板;3、支撑腿;4、连接座;5、检测传感器;6、气孔;7、气动隔膜泵进液管;8、环形密封气囊;9、螺纹固定杆;10、支气管;11、空腔;12、第一气泵;13、第二气泵;14、储液箱;15、循环泵;16、固定管;17、万向管。
具体实施方式
20.以下是本实用新型的具体实施例并结合附图,对本实用新型的技术方案作进一步的描述,但本实用新型并不限于这些实施例。
21.如图1-4所示,本实用新型一种气动隔膜泵故障检测装置,包括检测箱体1和气动隔膜泵进液管7,检测箱体1的一侧固定设有固定管16,固定管16的顶部固定安装有检测传感器5,检测传感器5主要用于气动隔膜泵的数据检测,固定管16的内部固定安装有万向管17,万向管17的端头处固定设有连接座4,连接座4与气动隔膜泵进液管7套接,连接座4的两侧均螺纹连接有螺纹固定杆9,两根螺纹固定杆9的端头处与气动隔膜泵进液管7的外壁接触连接,连接座4的内部固定设有环形密封气囊8,环形密封气囊8的进气端固定设有支气管10,检测箱体1的底部开设有空腔11,空腔11的底部固定安装有储液箱14,储液箱14的内部固定安装有循环泵15,循环泵15的出液端与固定管16的一端固定连接,空腔11一侧分别安装有第一气泵12和第二气泵13,第一气泵12的出气端通过导管与气动隔膜泵的进气端固定
连接,第二气泵13的出气端与支气管10的一端固定连接。
22.如图1、图2、图3和图4所示,本实用新型一种气动隔膜泵故障检测装置,空腔11的一侧等距开设有多个气孔6,多个气孔6的内部均固定安装有防尘网,气孔6的设置,便于第一气泵12和第二气泵13的抽放气,检测箱体1正面的顶部固定安装有数据显示面板2,检测箱体1的内部固定安装有处理器,多个检测传感器5均通过处理器与数据显示面板2电性连接,连接座4的内径与气动隔膜泵进液管7的端头处尺寸相匹配,检测箱体1底端的四个边角处均固定安装有支撑腿3,四个支撑腿3的底端开设有均匀分布的防滑纹,两个螺纹固定杆9的端头处均固定设有旋钮。
23.具体实施,在使用该气动隔膜泵故障检测装置时,首先将气动隔膜泵进液管7插入至连接座4的内部,接着人为的转动螺纹固定杆9,通过螺纹固定杆9将气动隔膜泵进液管7固定,然后人为的打开第二气泵13,通过第二气泵13对环形密封气囊8进行充气,保证了气动隔膜泵进液管7与连接座4连接的密封性,接着将第一气泵12的出气端与气动隔膜泵的进气端固定连接,之后打开循环泵15和检测传感器5进行检测。
24.本说明书中未作详细描述的内容属于本领域专业技术人员公知的现有技术。本文中所描述的具体实施例仅仅是对本实用新型精神作举例说明。本实用新型所属技术领域的技术人员可以对所描述的具体实施例做各种各样的修改或补充或采用类似的方式替代,但并不会偏离本实用新型的精神或者超越所附权利要求书所定义的范围。