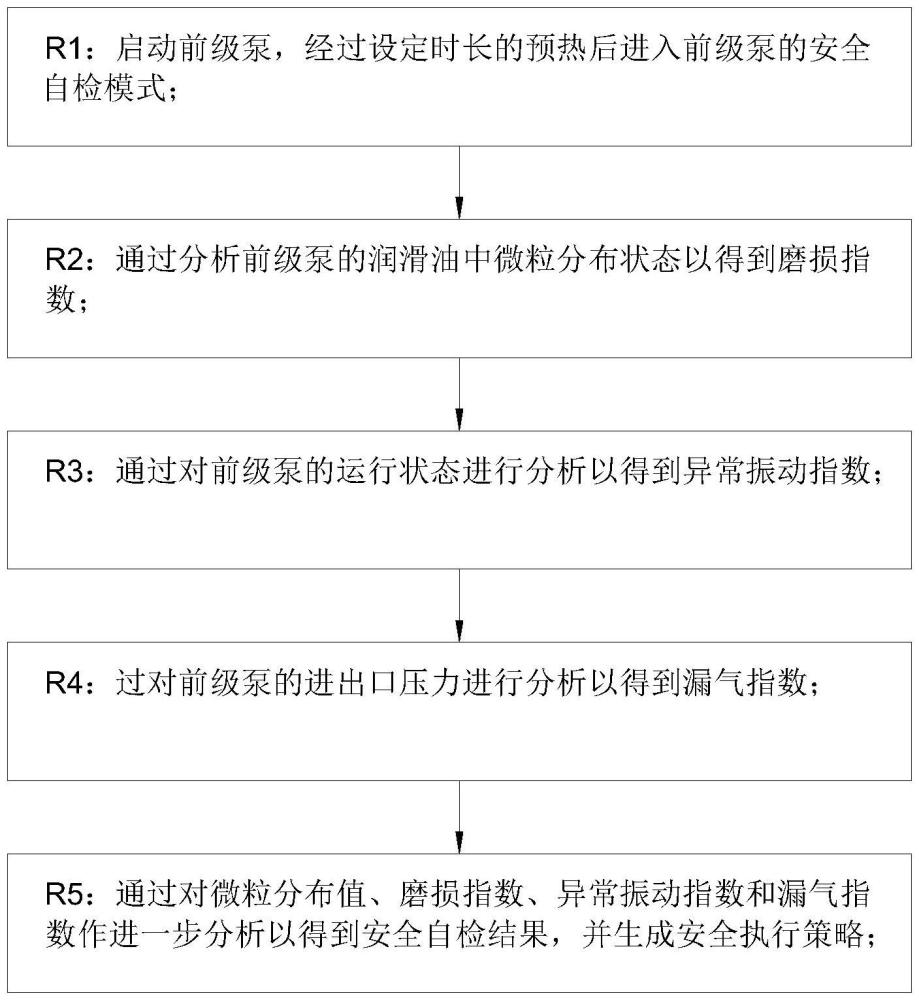
本发明涉及真空镀膜,具体为一种真空镀膜机用前级泵安全自检方法。
背景技术:
1、真空镀膜机通常由多个真空泵组成,包括前级泵和后级泵;前级泵在真空镀膜机中扮演着非常重要的角色,前级泵通过不断抽取镀膜室内的气体以创造出一个适合进行镀膜的真空环境,它直接影响着整个真空镀膜过程的效率和质量;因此前级泵的安全自检尤为重要;
2、目前的前级泵安全自检一般是在开始真空镀膜工作之前进行,其主要依赖于人工进行检查,不仅容易存在因人为检查的主观因素造成的误差和偏差,而且难以发现潜在的微小问题,例如微小的漏气或零件磨损,使得前级泵的安全自检结果不够精准。
技术实现思路
1、本发明的目的在于提供一种真空镀膜机用前级泵安全自检方法,以解决上述背景技术提到的问题。
2、本发明的目的可以通过以下技术方案实现:一种真空镀膜机用前级泵安全自检方法,包括以下步骤:
3、r1:启动前级泵,经过设定时长的预热后进入前级泵的安全自检模式;
4、r2:通过分析前级泵的润滑油中微粒分布状态以得到磨损指数;
5、r3:通过对前级泵的运行状态进行分析以得到异常振动指数;
6、r4:通过对前级泵的进出口压力进行分析以得到漏气指数;
7、r5:通过对微粒分布值、磨损指数、异常振动指数和漏气指数作进一步分析以得到安全自检结果,并生成安全执行策略;具体如下:
8、r51:当微粒分布值大于或等于设定的微粒分布值时,则生成润滑油更换指令,并控制前级泵进行润滑油更换操作;
9、r52:当磨损指数大于或等于设定的磨损阈值时,则生成磨损维护指令;
10、r53:当异常振动指数大于或等于设定的振动指数时,则生成运行维护指令;
11、r54:当漏气指数大于或等于设定的漏气阈值时,则生成漏气危维护指令;
12、r55:当没有生成任何指令时,则输出自检合格;当生成任一一个或者多个指令时,则输出自检不合格,并将生成的指令发送至对应的工程师进行对应的维护;
13、r56:当接收到维护完成指令后则重复上述r2-r55直至输出自检合格为止。
14、优选地,通过分析前级泵的润滑油中微粒分布状态以得到磨损指数,具体为:
15、在前级泵的油底壳内取样以得到润滑油样品,并利用x射线成像技术记录润滑油中微粒在辐射下的影像以得到微粒分布图;
16、通过微粒分布图进行微粒粒径和位置进行分析以得到粒径系数和集中系数,并将其分别记为wλ和zλ;
17、将微粒分布图中所有微粒的粒径进行均值计算以得到粒径均值记为将所有相邻两个微粒之间的间隔距离进行均值计算以得到间隔均值记为
18、将粒径均值间隔均值粒径系数wλ和集中系数zλ代入设定的公式进行计算以得到微粒分布值wz;其中b1和b2分别设定的权重系数;
19、调取距离此次采样时间最近的一次采样时间以及对应的微粒分布值,将两次采集时间进行时间差值计算以得到采样间隔记为c1,并将两次采样对应的微粒分布值进行差值计算以得到分布差值记为c2;
20、获取前级泵的异常磨损指数记为sf,并将其与采样间隔c1和分布差值c2代入设定的公式计算以得到磨损指数cz,其中b3和b4分别为设定的权重系数。
21、优选地,通过微粒分布图进行微粒粒径和位置进行分析以得到粒径系数和集中系数,具体如下:
22、采用激光粒度仪以计算微粒分布图中微粒的粒径,当粒径大于设定的粒径区间中的最大值时,则将对应的微粒记为一级微粒;当粒径处于设定的粒径区间之内时,则将对应的微粒记为二级微粒;当粒径小于设定的粒径区间中的最小值时,则将对应的微粒记为三级微粒;分别统计一级微粒、二级微粒和三级微粒的数量,并将其分别记为w1、w2和w3,将w1、w2和w3代入设定的公式计算以得到粒径系数wλ,其中a1、a2和a3分别为设定的权重系数,且a1>a2>a3>0;
23、将微粒分布图中的相邻两个微粒之间进行距离计算以得到间隔距离,以此类推以得到微粒分布图中所有相邻两个微粒之前的间隔距离,当间隔距离大于设定的间隔区间中的最大值时,则将该间隔距离记为一般集中间隔;当间隔距离处于设定的间隔区间之内时,则将该间隔距离记为中度集中间隔;当间隔距离小于设定的间隔区间中的最小值时,则将该间隔距离记为高度集中间隔;分别统计一般集中间隔、中度集中间隔和高度集中间隔的数量,并将其分别记为z1、z2和z3;将z1、z2和z3代入设定的公式进行计算以得到集中系数zλ;其中a4、a5和a6分别为设定的权重系数,且a6>a5>a4>0。
24、优选地,通过对前级泵的运行状态进行分析以得到异常振动指数,具体如下:
25、通过搭载于前级泵的振动传感器以获取不同采集时刻的振动信号,并据此构建运行振动谱图,设定存在一个前级泵的初始振动谱图;将运行振动谱图与初始振动谱图进行重合比对分析,运行振动谱图和初始振动谱图形成的阴影面积记为差异面积s1;将运行振动谱图的振动峰和初始振动谱图的振动峰分别按照对应的频率从小到大进行依次编号,当两者中序号相同的振动峰所对应的峰值不同时,则记为一次峰值迁移,将该峰值迁移对应的两者振动峰的峰值进行差值计算以得到峰值迁移量;当两者中序号相同的振动峰对应的频率不同时,则记为一次峰距迁移,将该峰距迁移对应的两个振动峰的频率进行差值计算以得到峰值迁移距;
26、统计运行振动谱图与初始振动谱图的重合对比示意图中峰值迁移和峰距迁移的次数,并将其分别记为f1和f2,分别将所有峰值迁移和峰距迁移对应的峰值迁移量和峰值迁移距进行求和计算得到总迁移量和总迁移距,并将其分别记为f3和f4,将f1、f2、f3和f4代入设定的公式进行计算以得到异常振动指数sf,其中f1、f2、f3和f4分别为设定的权重系数。
27、优选地,通过对前级泵的进出口压力进行分析以得到漏气指数,具体如下:
28、通过搭载于前级泵进出口的压力传感器以获取不同采集时刻的前级泵的进口压力记为y1 j和出口压力记为y2j,其中j=1,2,3……n1,n1取值为正整数,n1表示的是采集时刻的总数,j是其中任意一个采集时刻的序号;
29、当进口压力小于设定的标准真空度,则将该采集时刻记为真空异常时刻;将真空异常时刻对应的进口压力与标准真空度进行差值计算以得到真空异常值,统计真空异常时刻的数量记为h1,并将真空异常时刻对应的真空异常值进行求和计算以得到真空异常度记为h2;
30、以采集时刻为横坐标,以压力(压力包括进口压力和出口压力)为纵坐标构建进出口压力和出口压力随时间变化关系图;计算相邻两个进口压力点组成的线段的斜率记为进口斜率,将大于零的进口斜率进行求和计算以得到进口增加度,将小于零的进口斜率进行求和计算并将和值取绝对值以得到进口降低度;将进口增加度和进口降低度进行比值计算以得到增降比记为b;
31、将同一采集时刻的对应的出口压力和进口压力进行差值计算以得到压力差,以此类推以得到每个采集时刻对应的压力差记为y3j;
32、将进口压力记为y1 j、真空异常时刻的数量h1、真空异常度h2、增降比b和压力差y3j通过设定的公式进行计算以得到漏气指数yz,为不同采集时刻的进口压力的平均值;其中g1、g2、g3、g4和g5分别为设定的权重系数。
33、本发明的有益效果:
34、1、通过对润滑油的微粒分布、前级泵的振动和进出口压力进行深化分析以得到微粒分布值、磨损指数、异常振动指数和漏气指数;实现对前级泵的运行状态的全面分析,提高了监测的准确性和可靠性,能够有效避免人工自检的主观性和误差,减少人力资源浪费;
35、2、通过对微粒分布值、磨损指数、异常振动指数和漏气指数的进一步分析,生成相应的安全自检结果及执行策略,实现了对安全隐患的及时响应和处理,有助于降低故障风险,确保设备安全运行;同时当接收到维护完成指令后,前级泵会循环执行自检流程,直至输出自检合格为止,循环自检的机制有助于确保设备的持续安全性;
36、综上所述,前级泵的安全自检方法大大提高前级泵的安全性和运行稳定性,同时也可以减少人工检查的工作量和误差;因此,该前级泵的安全自检方法在现代真空镀膜机中具有广阔的应用前景。