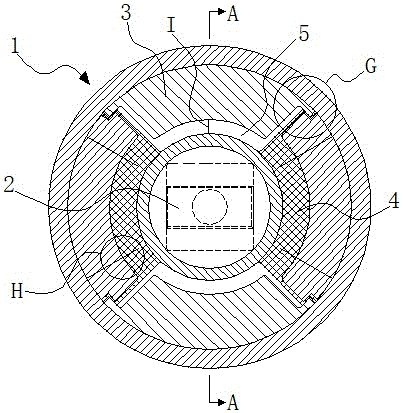
本实用新型涉及一种液体橡胶复合节点,尤其涉及一种带有管体流道的液体橡胶复合节点。
背景技术:
:根据动力学要求转臂节点在直线高速运行(高频振动)时,提供较大的径向刚度保证运行稳定性,提高临界速度;在过曲线(低频大振幅)时,提供较小的刚度性能保证过曲线性能,减小磨耗;普通节点难以实现上述特性,特别对于老线路,轮轨及线路磨损较大,维护成本高,因此需要使用一种新产品同时具备上述特性—液体橡胶复合节点。液体橡胶复合转臂节点工作原理:主要通过在橡胶部件内部设计两中空型腔结构,通过流道设计将两空腔连通,预先在一型腔内灌注密封不可压缩的(粘性)液体。在载荷作用下两空腔内的容积发生变化,液体在两腔之间流动产生阻尼,消耗振动能量,达到衰减振动的目的。低频振动时,液体经通道上下流动,起到大阻尼效果,高频率区段液体来不及流动,阻尼值较小,有效隔离振动,且高频振动下动刚度基本稳定保持不变,起到防止动态硬化的作用。系统的频率比基本保持不变,依然起到良好的减振效果。经过检索,找到相关的国内专利文献如下:1、公告号为cn102644693a,公告日为2012年8月22日的中国发明专利公开了一种带液体阻尼橡胶关节动刚度调节方法,在橡胶关节内设有两个以上的封闭空腔,封闭空腔与封闭空腔之间通过节流通道相互连通,且在节流通道上设置控制节流通道过流面积的调节装置,通过调节装置调节节流通道的大小,以达到调节阻尼力的大小,得到所需的橡胶关节动刚度。2、公告号为cn105501242a,公告日为2016年4月20日的中国发明专利公开了一种橡胶节点,其包括:芯轴、外套和橡胶层;所述橡胶层填充在所述芯轴和外套之间,所述橡胶层以芯轴为对称的两侧分别开设有第一空腔和第二空腔,所述橡胶节点内设置有连接所述第一空腔和第二空腔的第一连通通道,所述第一空腔和第二空腔内注有液体且所述液体未充满所述第一空腔和第二空腔。3、公告号为cn204845947u,公告日为2015年12月9日的中国实用新型专利公开了一种轴箱节点,其包括一芯轴、一弹性套件、一壳体,所述芯轴的中部开设一贯穿所述芯轴的通孔,所述弹性套件套设于所述芯轴的外壁,所述弹性套件上具有一第一腔体、一第二腔体,所述第一腔体的底部、所述第二腔体的底部分别与所述通孔的两端连通形成一空腔体,所述空腔体内具有液体,所述壳体套设于所述弹性套件的外部。4、公告号为cn109455191a,公告日为2019年3月12日的中国发明专利公开了一种变刚度转臂节点,转臂节点包括外套、主簧、辅助簧、芯轴,芯轴表面缠绕油液管道,主簧由橡胶和金属件两部分硫化成一体,主簧的金属件部分与芯轴压装在一起,主簧的两端压装有辅助簧,辅助簧也是与主簧相对应的由橡胶和金属件两部分硫化成一体,主簧和辅助簧外围压装有外套,以芯轴为对称轴,在外套和主簧之间设两个油腔,两个油腔分别与对应的油液管道的两端口相通。为了进一步优化液体橡胶复合节点的性能,需要产品提供较大的轴向刚度,实现较大的动静比,这样上述专利文献中的现有液体橡胶复合节点就难以实现了。综上,急需设计一种新型的液体橡胶复合节点,使其能提供较小的径向刚度及较大的轴向刚度,实现较大的动静比,从而优化液体橡胶复合节点的产品性能。技术实现要素:本实用新型所要解决的技术问题是针对现有技术中存在的缺陷,提供一种带有管体流道的液体橡胶复合节点,其能提供较小的径向刚度及较大的轴向刚度,实现较大的动静比,从而优化了液体橡胶复合节点的产品性能。为解决上述技术问题,本实用新型所采取的技术方案为:一种带有管体流道的液体橡胶复合节点,包括外套、芯轴和中间隔套,中间隔套与芯轴通过橡胶硫化粘接在一起,中间隔套装配到外套中,在芯轴中设置有管体流道,在中间隔套上还设置有多个空间,当硫化后,利用橡胶与所述多个空间形成相互独立的多个液体空腔,多个液体空腔中设置有液体且多个液体空腔之间通过管体流道相连通。优选的,所述芯轴包括内、外两部分,内部为芯轴本体,外部为芯轴外套,芯轴本体装配到芯轴外套中;在芯轴本体的外周面上设置有流道槽,流道槽围绕分布在芯轴本体的外周面上,沿流道槽的长度方向,在流道槽中设置有管体,管体的两端分别与多个液体空腔相连通。优选的,流道槽设置在芯轴本体的外周面上,装配后,芯轴外套的内周面直接与管体相接触,将管体压紧在流道槽中。优选的,在芯轴本体的外周面上设置凹槽区域,流道槽设置在凹槽区域的槽底面上,在凹槽区域内中还设置有压套,装配后,利用芯轴外套的内周面与压套相接触,再通过压套将管体压紧在流道槽中。优选的,在压套上还设置有两个压套通孔,在芯轴外套上与压套通孔相对应位置处设置有两个外套通孔,外套通孔与压套通孔相连通,管体的一端伸入到一个压套通孔中并与所述一个压套通孔固接,从而使得管体的一端通过一个外套通孔与一个液体空腔相连通,管体的另外一端伸入到另外一个压套通孔中并与所述另外一个压套通孔固接,从而使得管体的另外一端通过另外一个外套通孔与另外一个液体空腔相连通。优选的,在压套的外周面上且位于管体端部处还均开有环形密封槽,在环形密封槽中放置环形密封圈,当芯轴本体过盈装配到芯轴外套中后,利用芯轴外套的内周面压紧环形密封圈形成管体端部处的密封结构。优选的,在中间隔套上设置有多个空间,空间类似于通孔状,其外侧端和内侧端均为开口状;硫化后的橡胶封堵住每个空间的内侧端端口,利用一个弧形盖板封堵住所述每个空间的外侧端端口,从而使得所述每个空间均形成一个液体空腔。优选的,在弧形盖板的内周弧面上设置有朝芯轴凸出的凸块;利用凸块与橡胶相接触提供非线性刚度,利用凸块与芯轴接触形成硬止挡限位。优选的,中间隔套采用整体式隔套或采用多瓣式隔套,所述液体空腔设置有两个,两个液体空腔关于中间隔套的轴线对称分布在中间隔套上。本实用新型的有益效果在于:本实用新型通过在中间隔套上挖空与硫化后的橡胶形成多个独立的能储存液体的液体空腔,再在芯轴中设置管体流道,利用管体流道将多个液体空腔连通起来形成液体橡胶复合节点,这样能提供较小的径向刚度及较大的轴向刚度,实现较大的动静比,从而优化了液体橡胶复合节点的产品性能。采用管体来对液体进行导流,使得液体只能沿管体长度方向流动,而不会发生横向窜流,进一步提高了产品的可靠性。通过对管体流道形成方法的设计,便于产品的装配。通过对液体空腔具体形成方法的设计,使得液体空腔能顺利形成,保证了产品质量。当中间隔套设计成多瓣式隔套时,通过对其装配结构及工艺的设计,保证了过盈装配完成后,相邻的每个瓣体的相互接近的两端端面之间直接接触,不会有橡胶涉入其中,能进一步提高装配后产品的性能。当中间隔套设计成多瓣式隔套时,将中间隔套采用非等分设计,尽可能的扩大了液体空腔的体积空间。将中间隔套之间的橡胶分成为中间段橡胶和端部橡胶,通过调整中间段橡胶的径向厚度和端部橡胶的轴向厚度对节点的径向刚度和轴向刚度进行调整。附图说明图1为本实用新型实施例1中沿芯轴径向的节点剖面结构示意图;图2为沿图1中a-a线的剖视结构示意图;图3为图2中的芯轴的剖视结构示意图;图4为图2中d部的放大结构示意图;图5为当芯轴上表面不包胶时,图2中的d部处放大结构示意图;图6为本实用新型实施例1中沿芯轴径向的中间隔套的剖面结构示意图;图7为图1中g部的放大结构示意图;图8为图1中h部的放大结构示意图;图9为中间隔套未装配到外套中时,图1中h部处的放大结构示意图;图10为图6中一个弧形盖板的剖面结构示意图;图11为本实用新型实施例2中沿芯轴轴向剖切且位于外套一端端部处的节点局部剖视结构示意图;图中:1.外套,112.外套翻边部,2.芯轴,211.芯轴本体,212.芯轴外套,2121.外套通孔,2122.注液通孔,3.中间隔套,311.左弧形瓣体,312.右弧形瓣体,313.上弧形瓣体,314.下弧形瓣体,4.橡胶,411.芯轴上表面包胶,412.包胶通孔,413.中间段橡胶,414.端部橡胶,5.液体空腔,6.管体流道,611.流道槽,612.管体,7.凹槽区域,711.槽底面,8.压套,811.压套通孔,9.焊缝,10.环形密封圈,11.弧形盖板,111.凸块,12.台阶部,13.注液孔,14.台阶部一,15.台阶部二,16.端部密封圈。具体实施方式下面结合附图和具体实施例对本实用新型的技术方案做进一步详细的阐述。实施例1:如图1和图2所示,一种带有内槽流道液体橡胶复合节点的形成方法,其是在外套1和芯轴2之间增设中间隔套3,将中间隔套3与芯轴2通过橡胶4硫化粘接在一起,再将形成一体的中间隔套与芯轴装配到外套1中;在芯轴2中设置管体流道,在中间隔套3上挖空形成多个空间,当硫化后,利用橡胶4与所述多个空间形成相互独立的多个液体空腔5,多个液体空腔5中设置有液体(图中未示出)且多个液体空腔5之间通过管体流道6相连通。通过上述方法形成的液体橡胶复合节点,能提供较小的径向刚度及较大的轴向刚度,实现较大的动静比,从而优化了液体橡胶复合节点的产品性能。申请人通过将几个样品进行试验数据如下:径向刚度轴向刚度动静比试样15.6813.166.5:1试样25.5712.627:1试样35.5412.386:1试样45.3413.026:1试样55.2511.685:1如图3和图4所示,管体流道的形成方法如下:将芯轴2设置成内、外两部分,内部为芯轴本体211,外部为芯轴外套212,芯轴本体211过盈装配到芯轴外套212中。在芯轴本体211的外周面上设置有流道槽611,流道槽611呈螺旋状围绕分布在芯轴本体211的外周面上,在这里,流道槽611也可以不呈螺旋状围绕,而是以其他形状设置。沿流道槽611的长度方向,在流道槽611中设置有管体612,即管体612也围绕分布在芯轴本体211的外周面上,管体612可采用铜管或其他材料制成的有一定柔性的管体。流道槽611起到对管体612的定位作用,便于管体612的装配。管体612的两端分别与多个液体空腔5相连通。另外,通过对流道槽611的围绕状态的形状,从而也能调整管体612在芯轴本体211的外周面上的形状。采用管体来对液体进行导流,使得液体只能沿管体长度方向流动,而不会发生横向窜流,进一步提高了产品的可靠性。流道槽611的布置方式有两种,一种是直接在芯轴本体211的外周面上设置,然后将管体612放置到流道槽611中,再将芯轴本体211过盈装配到芯轴外套212中,装配后,芯轴外套212的内周面直接与管体612相接触,将管体612压紧在流道槽611中;另外一种就是本实施例所采用的(如图4所示),先在芯轴本体211的外周面上需要布置流道槽的区域设置凹槽区域7,即沿芯轴本体211的周向在芯轴本体211的外周面上设置有一整圈的凹槽区域7,流道槽611是设置在凹槽区域7的槽底面711上的,这样实际上是将流道槽611的布置区域下沉,当管体612放置到流道槽611中后,再在凹槽区域7内设置压套8,将管体612压紧在流道槽611中,这样能便于管体的装配及定位,也能保证在工作中管体的稳固性。为了便于压套8的安装,可将压套8对半剖开,再安装到芯轴本体211的凹槽区域7中。如图1和图4所示,在本实施例中,液体空腔设置有两个(如图1中位于上方的上方液体空腔和位于下方的下方液体空腔),在工作时,两个液体空腔需要连通起来,以保证液体能在两个液体空腔之间来、回流动。本实施例是在压套8上还设置有两个压套通孔811,在芯轴外套212上与压套通孔811相对应位置处设置有两个外套通孔2121,外套通孔2121与压套通孔811相连通,管体612的一端伸入到一个压套通孔811中并与所述一个压套通孔811固接,从而使得管体612的一端通过一个外套通孔2121与一个液体空腔5相连通,管体的另外一端伸入到另外一个压套通孔中并与所述另外一个压套通孔811固接,从而使得管体的另外一端通过另外一个外套通孔与另外一个液体空腔5相连通。在这里,管体两端是分别焊接在两个压套通孔811中的,焊接完成后在位于管体端部处留有焊缝9,为了进一步提高管体端部处的密封性,在压套8的外周面上且位于管体端部处还均开有环形密封槽,在环形密封槽中放置环形密封圈10,当芯轴本体211过盈装配到芯轴外套212中后,利用芯轴外套212的内周面压紧环形密封圈10形成管体端部处的密封结构。在装配时,为保证管体612的端部与外套通孔2121之间相连通,需要保证管体612的端部朝向芯轴轴向投影面上的投影与外套通孔2121的一端朝向芯轴轴向投影面上的投影相互完全重合或部分重合,因此,将管体612的直径设为c1,将外套通孔2121的直径设为c2,则c1<c2,这样减小了装配难度。另外,为保证芯轴通孔213的另外一端与液体空腔5相连通,需要在芯轴上表面包胶411和芯轴下表面包胶上开有包胶通孔412,使得液体空腔5通过包胶通孔412与外套通孔2121和管体612的一端相连通,这样做会增加一定的装配难度。因此,我们也可以采用另外一种方案,如图5所示,将位于液体空腔内的芯轴上表面包胶和芯轴下表面包胶清除掉,或可以在位于液体空腔内的芯轴上表面和位于液体空腔内的芯轴下表面上不设置包胶,这样使得液体空腔5直接通过外套通孔2121和管体612的一端相连通,减小了装配难度。如图1、图4和图6所示,液体空腔的形成方法如下:先在中间隔套3上挖出两个空间(如图6中的空间x1和x2),空间x1和空间x2类似于通孔状,其外侧端和内侧端均为开口状,在这里,将靠近芯轴2一侧的空间的一端看成内侧端,将远离芯轴2一侧的空间的一端看成外侧端,为了保证液体空腔能储存液体,需要将每个空间的两端开口进行密封以使得每个空间相互独立成形,在本实施例中,将空间内侧端开口进行密封时,是利用橡胶4进行密封的,即:在当将芯轴2与中间隔套3之间通过橡胶4硫化粘接在一起后,通过设计,利用硫化后的橡胶4封堵住空间的内侧端端口;将空间外侧端开口进行密封时,是在挖空后的中间隔套3上加盖一个弧形盖板11,利用弧形盖板11封堵住空间的外侧端端口,这样使得每个空间均形成独立的液体空腔。如图7所示,在空间外侧端开口周边的中间隔套3上开有台阶部12,台阶部12沿空间外侧端开口设置一整圈,弧形盖板11盖在台阶部12上,台阶部12的一个作用是用于作为定位结构,便于弧形盖板11定位装配。在本实施例中,芯轴、外套、压套、中间隔套和弧形盖板均可采用金属材料制成。为了进一步保证空间的外侧端端口的密封性,还需要通过以包胶和压装的方式相配合来完成,即在本实施例中,将橡胶4包胶至台阶部12上,此处的包胶厚度可以根据实际情况进行设置。装配时,先是将芯轴2和挖空的中间隔套3通过橡胶4硫化成一体,将橡胶包胶至台阶部12上,再在台阶部12上盖上弧形盖板11,使得弧形盖板11与台阶部12上的包胶相接触,再将带有弧形盖板11的中间隔套3过盈装配到外套1中,利用装配后产生的作用力将弧形盖板11压紧在台阶部12上,使得台阶部12上的包胶产生变形,起到密封效果。当外套1组装好后,还可以进一步对其设计一定的缩径量,进一步提高密封效果。中间隔套可采用整体式隔套,也可采用多瓣式隔套。在本实施例中采用的就是多瓣式隔套,如两瓣式、三瓣式等结构,具体的来说本实施例采用的是四瓣式隔套,如图6所示,本实施例中的中间隔套3为四瓣式隔套,包括左弧形瓣体311、右弧形瓣体312、上弧形瓣体313和下弧形瓣体314,四个瓣体周向围合形成隔套。如图9所示,当中间隔套与芯轴通过橡胶硫化粘接后未进行过盈装配前,相邻的每个瓣体的相互接近的两端端面之间均留有间隙e(如图9中的左弧形瓣体311的一端和下弧形瓣体314的一端之间的间隙e),在橡胶4中且位于每个间隙e处也留有开口间隙f;但是,当节点过盈装配好后,如图8所示,受到作用力的影响下,间隙e和相邻的开口间隙f均消失不见,即每个瓣体的相互接近的两端端面相互接触,开口间隙f也被变形的橡胶4填满,这样能进一步提高装配后产品的性能。如图9所示,在本实施例中,开口间隙f为u型凹槽,该u型凹槽的开口朝向间隙e且u型凹槽的两侧边沿中间隔套的径向延长的延长线分别与位于间隙e处的两个瓣体的相互接近的两端端面相重合,u型凹槽的深度是根据实际装配工况来设计的。通过设置开口间隙f能保证装配后,每个瓣体的相互接近的两端端面相互直接接触,其之间不会有橡胶涉入其中。在多瓣式中间隔套的设计中,可采用等分设计,也可以采用非等分设计,在本实施例中,采用的是非等分的设计,即以中间隔套的中心点为圆点,多个弧形瓣体对应的圆心角度是不相等的,如图6所示,上弧形瓣体313的弧度和下弧形瓣体314对应的圆心角度均设为α,左弧形瓣体311和右弧形瓣体312对应的圆心角度均设为β,且α>β。这是因为,在本实施例中,挖空的弧形瓣体为上弧形瓣体313的弧度和下弧形瓣体314,挖空后,沿上弧形瓣体313的弧度和下弧形瓣体314方向(即图中y向)为空向,沿左弧形瓣体311和右弧形瓣体312方向(即图中x向)为实向,将空向上的弧形瓣体的弧度尽量增大,能尽量增大液体空腔的容积,从而有利于产品性能的提升。另外,能够降低空向的径向刚度。在本实施例中,α采用120度,β采用60度。挖空的瓣体可以是多瓣式中间隔套中的任意瓣体,在本实施例中,是将关于芯轴2的轴向对称设置的上弧形瓣体313的弧度和下弧形瓣体314挖空形成的液体空腔的。为了使液体橡胶能提供非线性刚度特性,采用对金属盖和芯轴之间的配合结构设计方案实现。如图1和图10所示,在弧形盖板11的内周弧面上设置有朝芯轴2凸出的凸块111,在工作时,当节点受到载荷作用时,凸块111与橡胶4相接触提供非线性刚度特性,在载荷的进一步作用下,凸块111与芯轴2接触形成硬止挡限位保护功能。在本实施例中,凸块111靠近芯轴2一端的下端周面设置为弧形面,该弧形面的曲率与芯轴的曲率相匹配。凸块111的体积大小可以根据实际需求来设计,通过控制凸块111的大小从而能对液体空腔5的体积大小进行控制,使得节点成为大体积液体空腔的节点和小体积液体空腔的节点。大体积液体空腔的节点能够容纳更多的液体,而小体积液体空腔的节点在同样的刚度下,能够提供更大的动态刚度特性。在本实施例中,凸块111的体积设计得比较大,从而使得节点成为了一种小体积液体空腔的节点。将凸块111靠近芯轴2一端的下端周面与芯轴2之间的间隙设为i,通过调整间隙i的大小,能够对非线性刚度曲线进行调整。在本实施例中,在两个弧形盖板11的内周弧面上均设置有凸块111,两个凸块111分别位于两个液体空腔5中。如图3所示,芯轴外套212是这样形成的,以芯轴外套212的中心轴线k为母线,以两端高、中间底的马鞍状面j为旋转面所形成的一个芯轴外套。如图2所示,这样设置芯轴外套212使得芯轴外套212和中间隔套3之间的橡胶4分成两部分,一部分橡胶为中间段橡胶413,另外一部分为位于中间段橡胶413两端的端部橡胶414,中间段橡胶413沿芯轴径向上的厚度设为径向厚度h1,端部橡胶414沿芯轴轴向上的厚度设为轴向厚度h2。在工作时,中间段橡胶413主要提供径向刚度,端部橡胶414主要提供轴向刚度,这样通过调整径向厚度h1和轴向厚度h2就能对节点的径向刚度和轴向刚度进行调整。在芯轴2上还设置有注液孔13,注液孔13与液体空腔5相连通,刚开始时,液体通过注液孔13注入液体空腔5中,然后密封。如图4所示,在未密封前,注液孔13的一端与外界相连通,注液孔13的另外一端与在芯轴外套212上开设的注液通孔2122相连通,而注液通孔2122又与一个液体空腔5相连通,从而最终使得注液孔13的另外一端与一个液体空腔5相连通以方便注入液体。实施例2:如图11所示,与实施例1相比,本实施例的不同之处在于:本实施例中的外套1的两端部是采用翻边扣压设计结构的。在中间隔套3的一端上设置有连续状的台阶部一14和台阶部二15,台阶部一14位于下方位置(靠近芯轴的位置),台阶部二15位于上方位置(远离芯轴的位置),外套1的一端端面与台阶部二15的侧向垂直面沿垂向上齐平,在台阶部二15上放置有端部密封圈16,在未进行翻边扣压时,端部密封圈16的高度高于台阶部二15的高度,即端部密封圈16位于台阶部二15和外套1之间的位置。在外套1的一端端面上延伸设置有外套翻边部112,翻边操作时,利用外套翻边部112翻边折弯将端部密封圈16压紧,利用端部密封圈16密封住外套1和中间隔套3之间的接触面的端部缝隙p,进一步增加节点的密封性能。外套翻边部112翻边至台阶部一14的侧向垂直面上,从而利用台阶部一14对翻边操作进行翻边定位。翻边操作后,外套翻边部112的端部与台阶部一14的水平底面之间留有间隙t。中间隔套3的另外一端上也设置有连续状的台阶部一和台阶部二,在整体外套的另外一端端面上也延伸设置有外套翻边部,中间隔套的另外一端处的翻边扣压设计结构和上述中间隔套的一端处的翻边扣压设计结构是一样的,在此不再累述。综上,本实用新型通过在中间隔套上挖空与硫化后的橡胶形成多个独立的能储存液体的液体空腔,再在芯轴中设置管体流道,利用管体流道将多个液体空腔连通起来形成液体橡胶复合节点,这样能提供较小的径向刚度及较大的轴向刚度,实现较大的动静比,从而优化了液体橡胶复合节点的产品性能。采用管体来对液体进行导流,使得液体只能沿管体长度方向流动,而不会发生横向窜流,进一步提高了产品的可靠性。通过对管体流道形成方法的设计,便于产品的装配。通过对液体空腔具体形成方法的设计,使得液体空腔能顺利形成,保证了产品质量。当中间隔套设计成多瓣式隔套时,通过对其装配结构及工艺的设计,保证了过盈装配完成后,相邻的每个瓣体的相互接近的两端端面之间直接接触,不会有橡胶涉入其中,能进一步提高装配后产品的性能。当中间隔套设计成多瓣式隔套时,将中间隔套采用非等分设计,尽可能的扩大了液体空腔的体积空间。将中间隔套之间的橡胶分成为中间段橡胶和端部橡胶,通过调整中间段橡胶的径向厚度和端部橡胶的轴向厚度对节点的径向刚度和轴向刚度进行调整。本实施例中所述的“多个”即指“两个或两个以上”的数量。以上实施例仅供说明本实用新型之用,而非对本实用新型的限制,有关
技术领域:
的技术人员在不脱离本实用新型的精神和范围的情况下,还可以做出各种变化或变换,因此所有等同的技术方案也应该属于本实用新型的保护范围,本实用新型的保护范围应该由各权利要求限定。当前第1页12