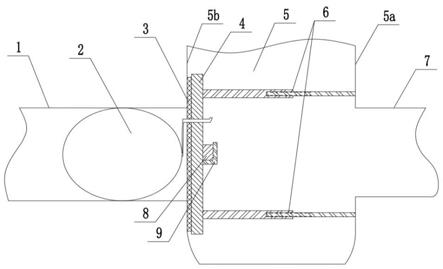
1.本发明属于地埋排污管检修施工技术领域,具体涉及一种大口径深埋位排污管截流封口施工方法。
背景技术:2.大口径深埋位排污管,一般指管道直径不小于1200mm、埋位基本在6-8m以上的污水排放管,在一些特殊区域其埋位甚至达到了15米以上,排污管内污水流量大、流水高,以直径1500m 排污管为例,其污水日流量达到8万吨,管道设计压力为1.6mpa; 为便于定期检修、清洁和疏通,一般在排水管道交汇处、转弯处、管径或坡度改变处、跌水处以及直线管段上每隔一段距离设置检查井,检查井与管路连通,检查井内的水位至少高出排污管;当需要实施定期检修或管道抢修、维护时,先需要对检修或抢修段内的排污管进行截流封堵,然后通过抽水机排出截流段内的污水;排污管截流封堵一般选择在排污管与检查井的交汇处,在排污管管口采用橡胶气囊与砖墙把管口封堵,先用橡胶气囊堵住管道,然后在管口进行砌墙,现有的砖墙封堵管口在实际应用中主要存在以下问题:1)施工难度高:检查井的水位高于排污管,排污管管口砌墙是潜水作业,不同于陆地一般砌墙,施工难度相当大,而且因施工人员需潜入水中进行施工,对施工人员就提出了潜水作业的要求;2)施工周期长:砌墙是一块块转通过特种水泥连接在一起,以直径1500mm排污管为例,在一切基本正常的情况下完成砌墙大概需要半天左右,而拆墙更费时,因墙体的抗冲击强大要求高,砖块之间的粘结力比较大,所以拆墙作业一般需要一天以上的作业时间;3)封堵成本高:砌墙封堵因在水中作业,且墙体的抗冲击强度要求高,因此对水泥的要求极高,采用的水泥都是特种水泥,以直径1500mm排污管为例,管口封堵墙建造所用的砖头与水泥的材料成本约在1万元人民币左右,而当检修或抢修作业结束后墙体需拆除,水泥、砖块都成了废品,增加了建筑垃圾的排放量,建筑垃圾的处置又需要承担相应的费用;4)施工危险性高:首先砌墙作业是完全潜入水中作业且作业时间长,管道内的污水有各种腐烂物,长时间作业风险高;其次,施工过程中如果前部的橡胶气囊不能承受管内排水的冲击,橡胶气囊会被冲出,封口砖墙倒塌,馆内污水以跟更急更大的流量冲出,施工人员可能会被管内急流冲走,特别是当施工过程中出现暴雨等恶劣天气,或上游排放量突然增加时,相邻检查井内的水位升高,管内的水流就会更急,冲击力更大,这种情形会导致砌墙、拆墙施工过程中的作业人员面临极大的被流水冲走的风险;5)抢检修作业危险性高:此类风险主要由施工质量达不到设定要求导致抗冲击强度可达不到涉及要求而导致,砌墙施工为潜水作业,工作人员潜入污水中进行砌墙,工作环境极其恶劣,墙体质量稳定性受到人为因素比较多,比如作业人员的熟练程度、潜水作业的视线障碍、现场施工过程中的水泥固化条件等,可能会导致墙体质量达不到设定要求,从而降低了墙体的抗冲击能力,当检修或抢修实施期间遭遇暴雨或超大流量排放时,因临时排放管路的排水能力又往往低于正常管道,这样检查井内的水位会急剧上升,截流封堵位所承受
的压力也会急剧上升,如果超出极限墙体就会被冲垮,在管道内实施检修或抢修作业的员工就会遭遇到突发而知的超级污水,就将面临被污水冲走的危险。
3.综上所述,大口径、深埋位排污管的截流封堵用传统的砌墙方法存在多种弊端,寻找成本低、施工容易与安全、抗冲击能力大且稳固的封堵方法,是大口径深埋位排污管检修或抢修作业实施中迫切需要解决的问题。
技术实现要素:4.本发明旨在利用检查井本身的抗冲击能力与封口钢板稳定的抗冲击能力、并基于化整为零的施工思路,提供一种技术方案大口径深埋位排污管截流封口施工方法,以克服现有技术中存在的问题。
5.所述的大口径深埋位排污管截流封口施工方法,待封排污管与检查井的井内壁交汇相连,其特征在于由一组调节撑杆借助检查井的对向井内壁将一组封口钢板密封顶设在井内壁上构成排污管封口结构,一组封口钢板通过连接钢条构成一个组合体,相邻封口钢板之间密封配合,其施工过程包括以下步骤:1)材料准备,包括但不限于:封口钢板与调节撑杆各一组、连接钢条一根,其中封口钢板至少两块,调节撑杆配置数量为封口钢板配置数的两倍,连接钢条与封口钢板上分别设置对应的螺栓连接孔;2)逐一将封口钢板下放到检查井内并挡在与待封排污管交汇的检查井的井内壁上,一组封口钢板完全挡住待封排污管的管口;3)用一条连接钢条将一组封口钢板连接成一个整体,连接钢条与各块封口钢板之间通过螺栓固定连接;4)每一块封口钢板与检查井的对向井内壁之间上下部分别采用水平设置的调节撑杆撑紧。
6.2. 如权利要求1所述的大口径深埋位排污管截流封口施工方法,其特征在于所述封口钢板的厚度要求其抗冲击强度大于排污管管壁的抗冲击强度,封口钢板的长度大于排污管外径,一组封口钢板的宽度之和大于排污管外径,其中两块封口钢板中部的边侧位置同方向设置用于安装连接钢条的钢条插槽,所述步骤2)中设置钢条插槽的两块钢板安装在两侧。
7.3. 如权利要求1所述的大口径深埋位排污管截流封口施工方法,其特征在于所述各封口钢板上的螺栓连接孔配合设置在居中位置,所述连接钢条采用钢板或槽钢制作成型,其抗弯曲强度大于封口钢板的抗冲击强度,连接钢条上对应封口钢板组合后的螺栓孔间距对应设置一组螺栓孔,所述步骤3)中连接钢条与各封口钢板之间通过所设置的螺栓孔采用螺栓连接固定。
8.4. 如权利要求1所述的大口径深埋位排污管截流封口施工方法,其特征在于所述调节撑杆采用可调螺杆结构,所述步骤中旋转可调螺杆伸长调节撑杆至调节撑杆两端与封口钢板、检查井内壁顶触配合,调节撑杆与封口钢板的配合位设置在待封排污管的管口的外部。
9.5. 如权利要求1所述的大口径深埋位排污管截流封口施工方法,其特征在于所述步骤中相邻封口钢板之间配合设置板间密封垫,封口钢板组合体与内壁(5a)之间配合设置
密封垫。
10.6. 如权利要求1所述的大口径深埋位排污管截流封口施工方法,其特征在于所述的步骤2)之前包括以下步骤:从待封排污管与检查井交汇的管口将橡胶气囊装入待封排污管,并将橡胶气囊充气至其外壁顶触到待封排污管的内壁;所述一组封口钢板的其中一块上配合设置穿线孔及与其密封配合的密封圈,在所述步骤2)中通过穿线孔及密封圈密封引出所述橡胶气囊的充气管与固定绳。
11.所述的大口径深埋位排污管截流封口施工方法设计新颖、构思合理,本方案将一组封口钢板与一组调节撑杆借助检查井双向的内壁在待封排污管的管口构建非常稳固且高强度的排污管封口钢墙,封口钢墙使用过程中始终能保持稳定的高抗冲击能力,可完全避免被冲垮坍塌等情形的发生,切实保障封口相关施工与抢检修作业过程的安全性,应用本方案可使封口的建设与拆除作业过程都极其简单且作业时间短、劳动强度小、施工可控性高,,可明显提高施工效率,且封堵用材料可以重复利用,降低施工成本,减少建筑垃圾的排放,促进节能减排、减少资源、保护环境。
附图说明
12.图1为本发明应用现场示意图;图2为所述封口钢板组合方法示意图;图中:1-待封排污管、2-橡胶气囊、3-密封垫、4-封口钢板、5-检查井、5a-对向井内壁、5b-井内壁、6-调节撑杆、7-待检排污管、8-连接钢条、9-钢条插槽、10-螺栓、11-穿线孔、12-板间密封垫。
具体实施方式
13.现结合说明书附图,详细说明本发明的具体实施方式:如图所示为大口径深埋位排污管截流封堵施工现场,检查井5为方形结构,排污管位于检查井5下部,图1所示区域内截流排水前均为灌装所排污水区域,检查井5内污水液面高于排污管,需截流排水区域为检查井5右侧的待检排污管7,截流封堵施工在左侧的待封排污管1与检查井5交汇处进行,由一组调节撑杆6借助检查井5的对向井内壁5a将一组封口钢板4紧紧顶设在待封排污管1的管口所在的检查井5的井内壁5b上形成排污管封口结构,一组封口钢板4至少有两块组成,通过连接钢条8把全部封口钢板4构建成一个组合体,相邻封口钢板4之间密封配合,一组封口钢板4的组合体与井内壁5b之间密封配合,现场施工包括以下步骤:1)材料准备,包括但不限于:橡胶气囊2及相应充气装备一套、封口钢板4与调节撑杆6各一组、连接钢条8一根、相关密封件、以及吊机设备等,橡胶气囊2的规格、封口钢板4的规格分别根据待封排污管1直径来选择确定;其中橡胶气囊2充足气后的最大直径大于待封排污管1的内径;所述封口钢板4至少两块,封口钢板4的厚度要求其抗冲击强度大于排污管管壁的抗冲击强度,封口钢板4的长度大于排污管外径,一组封口钢板4的宽度之和大于排污管外径,其中两块封口钢板4中部的边侧位置同方向设置连接钢条8的钢条插槽9,钢条插槽9可以采用l型槽钢焊接在封口钢板4上成型,各封口钢板4上的居中位置配合设置螺栓连接
孔,并在其中一块封口钢板4上配合设置穿线孔11与密封圈;所述调节撑杆6配置数量为封口钢板4配置数的两倍,采用可调螺杆结构,只需旋转内杆就可以调整调节撑杆6的长度,调节撑杆6调节后的最小长度小于封口钢板4与检查井5的对面内壁之间的距离,而调节后的最大长度大于于封口钢板4与检查井5的对向井内壁5a之间的距离;所述连接钢条8采用钢板或槽钢制作成型,考虑其抗弯曲强度大于封口钢板4的抗冲击强度,连接钢条8上对应封口钢板4组合后的螺栓孔间距对应设置一组螺栓孔,连接钢条8的长度小于封口钢板4的组合宽度;2)从待封排污管1与检查井5交汇的管口将橡胶气囊2装入待封排污管1内,并将橡胶气囊2充气至其外壁顶触到排污管内壁,将管内污水阻隔;3)逐一将封口钢板4下放到检查井5内,并将封口钢板4挡在与待封排污管1交汇的检查井5的井内壁5b上,设置钢条插槽9的两块封口钢板4对应放置在两侧最外面,钢条插槽9的开口向上,一组封口钢板4完全挡住待封排污管1的管口,并在封口钢板4与排污管端面之间设置密封垫3、相邻封口钢板4的拼接处分别设置板间密封垫12;放置开设穿线孔11封口钢板4时将步骤2)中所述橡胶气囊2的充气管与固定绳从穿线孔11引出,并安装好密封圈,使得橡胶气囊2的充气管与固定绳密封穿过封口钢板4;4)将连接钢条8横向插入两侧封口钢板4上的钢条插槽9内,再通过各封口钢板4上设置的螺栓连接孔与连接钢条8上对应设置的一组螺栓连接孔,用螺栓10将连接钢条8与每一块封口钢板4进行固定,形成一个连体机构的封口用钢板;5)每一块封口钢板4与检查井5的对向井内壁5a之间分别在上下部位置用水平设置的调节撑杆6撑紧,调节撑杆6与封口钢板4的配合位设置在待封排污管1的管口的外部,安装时旋转可调螺杆使调节撑杆6伸长至调节撑杆6两端与封口钢板4、对向井内壁5a分别顶触配合;通过上述施工步骤,一组调节撑杆6借助检查井5的对向井内壁5a将封口钢板4紧紧顶设在待封排污管1的管口所在的检查井5的井内壁5b上,形成了非常稳固的排污管封口钢墙,抗冲击强度高且结构稳定,能始终保持得到保持,不会在施工及使用过程中发生结构变化而导致坍塌等。
14.上述实施例中构建的封口钢墙的施工过程简单,现场作业人员在污水中的作业时间短、作业方法简单,降低了施工难度与强度,改善了现场作业条件,且施工中干扰因素少,能确保施工预期实施;同时所构建的封口钢墙的抗冲击能力设计上高于排污管的抗冲击能力,且具有非常好的稳固性,可为后续抢检修实施提供安全可靠的作业环境,即使出现突发的排水量增加,也无法将封口钢板4冲开,切实保障了抢检修的安全施工环境,确保抢检修顺利实施。
15.上述实施例中构建的顶设在待封排污管1管口的封口钢墙需要拆除时,先缩短调节调节撑杆6至其两端与封口钢板4、对向井内壁5a松开,然后退出螺栓10以解除连接钢条8与封口钢板4之间的固定连接,移开连接钢条8,再将封口钢板4逐一吊出检查井5,同时清理密封垫3、板间密封垫12,整个拆除过程及其简单,劳动强度低、施工时间短,现场作业环境安全性明显提升,且构建封口钢墙的封口钢板4、调节撑杆6、连接钢条8可以重复利用,施工成本能得到及其显著的降低,建筑施工垃圾的排放量降到了最低,将施工垃圾减量排放落到实处,促进环境保护的有效推进。
16.上述实施例中,封堵用钢板采用两块或两块以上封口钢板4的组合结构,基于化整为零的施工模式,便于在检查井5内运送封口钢板4与排污管前摆放操作,如封口钢板4采用整体结构,受其重量、宽度限制,使得在狭小的深井内无法作业;以1500米直径的排污管为例,可设计采用三块厚度2cm、长度2m、宽度0.6m的封口钢板4,因此在施工过程中搬运、安装、拆除的作业对象是厚度2cm、长度2m、宽度0.6m的封口钢板4,在1500米直径排污管对应的检查井内就具有了充足的施工操作空间,便于施工实施。