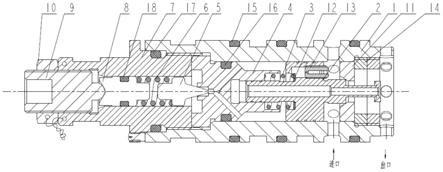
[0001]
本发明涉及一种插装型分体阀口内流式高压溢流阀,属于运载火箭推力矢量控制执行技术领域。
背景技术:[0002]
在运载火箭伺服系统工作过程中需要将系统多余的液压油溢流回油箱,进而保证系统压力的稳定,同时需要使用安全阀,限制系统的最大压力,在系统压力过高时实现卸荷,防止压力过载。
[0003]
而现有技术中,溢流阀结构存在工艺性差、尺寸大、应用受限等问题。如中国专利申请号为cn201921880196.2的一种高压溢流阀,该专利记载的为直动外流式结构,无法应用于内流式结构场合,且直动式结构应用于大流量场合将使弹簧调节困难。
技术实现要素:[0004]
本发明要解决的技术问题是:克服现有技术的不足,提供了一种插装型分体阀口内流式高压溢流阀,进口压力通过阻尼孔进入主弹簧腔,主弹簧腔压力作用在导阀上,当进口压力大于导弹簧设定值时导阀开启,主弹簧腔油液通过主阀中心孔流向低压区,使主弹簧腔压力降低,在阻尼孔作用下,主阀前后形成压力差,最终使主阀开启。当进口压力小于导弹簧设定值时,导阀关闭,主弹簧腔重新建立起压力,主阀芯两端压力相同,主阀芯在主弹簧作用下关闭。
[0005]
本发明目的通过以下技术方案予以实现:
[0006]
一种插装型分体阀口内流式高压溢流阀,包括阀体、主阀芯、主弹簧、导阀座、导阀、导弹簧、导阀体、滑动轴、调节螺钉、分体阀口、阻尼塞、螺母;
[0007]
所述阻尼塞安装在主阀芯内并紧固连接;所述主阀芯和分体阀口依次安装在阀体内,分体阀口通过螺母与阀体紧固连接;所述主阀芯内设有回油孔,回油孔经螺母与外部连通;
[0008]
所述导阀座安装在阀体内,且导阀座的局部套装在主阀芯上,所述主弹簧位于导阀座和主阀芯之间;所述导阀体与阀体连接后压紧导阀座;所述导阀位于导阀体和导阀座之间;所述滑动轴安装在导阀体内,导弹簧位于滑动轴和导阀之间,调节螺钉与导阀体连接后用于调节滑动轴;
[0009]
所述导阀座在靠近导阀的一端交错设有进油通道与回油通道,导阀开启后,油液经进油通道后通过回油通道由回油孔流出。
[0010]
上述插装型分体阀口内流式高压溢流阀,优选的,所述分体阀口与阀体之间为过盈配合。
[0011]
上述插装型分体阀口内流式高压溢流阀,优选的,所述阻尼塞和主阀芯之间涂胶。
[0012]
上述插装型分体阀口内流式高压溢流阀,优选的,所述主阀芯的轴线与回油孔的轴线重合。
[0013]
上述插装型分体阀口内流式高压溢流阀,优选的,所述回油孔在主阀芯的尾端设有双倒角。
[0014]
上述插装型分体阀口内流式高压溢流阀,优选的,还包括锁紧螺母,用于锁紧调节螺钉。
[0015]
上述插装型分体阀口内流式高压溢流阀,优选的,还包括调整垫片,安装于主阀芯和主弹簧之间。
[0016]
上述插装型分体阀口内流式高压溢流阀,优选的,还包括密封圈,密封圈用于溢流阀与外部结构密封、导阀座和阀体密封、导阀体和阀体密封、滑动轴和导阀体密封。
[0017]
上述插装型分体阀口内流式高压溢流阀,优选的,所述阀体上设有进口和出口;油液经进口进入阀体的内腔,然后通过阻尼塞进入主阀芯的内腔,然后流入导阀座与阀体之间的腔体,最后通过进油通道达到导阀;导阀开启后,油液经回油通道、回油孔后,从阀体的出口流出。
[0018]
上述插装型分体阀口内流式高压溢流阀,优选的,所述主阀芯的尾部和分体阀口将进口和出口隔离。
[0019]
本发明相比于现有技术具有如下有益效果:
[0020]
(1)本发明为内流式先导高压溢流阀,在伺服系统中工作过程中将系统多余的液压油溢流回油箱,进而保证系统压力的稳定,也可用作安全阀,限制系统的最大压力,在系统压力过高时实现卸荷,防止压力过载;其可应用于内流式结构场合,同时本发明结构紧凑,质量轻,亦可应用于对空间及质量要求较高的溢流阀或安全阀场合。
[0021]
(2)本发明阀芯与分体阀口形成主阀口,其中分体阀口与阀体通过过盈配合进行安装,并通过螺母进行紧固,此分体形式可有效提高阀体机加工艺性,降低零件加工难度,较好的保证主阀口精度。
[0022]
(3)本发明设计有阻尼塞,其与主阀芯通过螺纹连接后通过涂胶进行紧固,保证阀门工作过程中阻尼塞的可靠稳定,阻尼塞上设置有阻尼孔,可通过安装不同阻尼塞来调整阻尼孔大小,从而调整阀门启闭特性,进而不同尺寸公差及弹簧的阀门可通过调整阻尼孔来满足技术要求。
[0023]
(4)本发明主阀芯中心孔为导阀回油孔,导阀座交错设置进油通道与回油通道,主弹簧腔油液通过导阀座上导阀进口孔道进入导阀前端;导阀开启后先导阀出口油液通过导阀座上导阀回油孔进入主阀芯中心孔道,最终回流至溢流阀低压出口,此种将先导阀回油与主阀芯中心孔结合的方式有效的减小了溢流阀体积与重量。
[0024]
(5)本发明主阀芯尾端出油口设计有双倒角,可使出口出油成放射状,有效防止回油腔压力不稳导致导阀启闭不畅;同时主阀芯尾端外部设计有内槽,使主阀口开启后高压油液冲击作用在阀芯尾端内槽上,以改善流场,防止高压下出口压力波动导致阀口开启不畅。
[0025]
(6)本发明滑动轴8左端设计有锥角,调节螺钉头部设计为圆头结构,调节螺钉圆头与滑动轴锥角相解除,从而使调节滑动轴时可有效防止出现因滑动轴或调节螺钉同轴度误差导致滑动轴偏置进而使弹簧卡滞的问题。
附图说明
[0026]
图1为插装型分体阀口内流式高压溢流阀结构原理图;
[0027]
图2为主阀芯结构图;
[0028]
图3为主阀芯尾端放大图;
[0029]
图4为导阀座结构图;
[0030]
图5为导阀进油示意图;
[0031]
图6为导阀回油示意图;
[0032]
图7为阀体结构图;
[0033]
图8为分体阀口装配结构图;
[0034]
图9为阻尼塞结构图;
[0035]
图10为阻尼塞装配图;
[0036]
图11为滑动轴结构图;
[0037]
图12为调节螺钉结构图。
具体实施方式
[0038]
为使本发明的目的、技术方案和优点更加清楚,下面将结合附图对本发明的实施方式作进一步详细描述。
[0039]
一种插装型分体阀口内流式高压溢流阀,包括阀体1、主阀芯2、主弹簧3、导阀座4、导阀5、导弹簧6、导阀体7、滑动轴8、调节螺钉9、分体阀口11、阻尼塞13、螺母14;
[0040]
所述阻尼塞13安装在主阀芯2内并紧固连接;所述主阀芯2和分体阀口11依次安装在阀体1内,分体阀口11通过螺母14与阀体1紧固连接;所述主阀芯2内设有回油孔,回油孔经螺母14与外部连通;
[0041]
所述导阀座4安装在阀体1内,且导阀座4的局部套装在主阀芯2上,所述主弹簧3位于导阀座4和主阀芯2之间;所述导阀体7与阀体1连接后压紧导阀座4;所述导阀5位于导阀体7和导阀座4之间;所述滑动轴8安装在导阀体7内,导弹簧6位于滑动轴8和导阀5之间,调节螺钉9与导阀体7连接后用于调节滑动轴8;
[0042]
所述导阀座4在靠近导阀5的一端交错设有进油通道与回油通道,导阀5开启后,油液经进油通道后通过回油通道由回油孔流出。
[0043]
作为本发明的一种优选方案,所述分体阀口11与阀体1之间为过盈配合。
[0044]
作为本发明的一种优选方案,所述阻尼塞13和主阀芯2之间涂胶。
[0045]
作为本发明的一种优选方案,所述主阀芯2的轴线与回油孔的轴线重合。所述回油孔在主阀芯2的尾端设有双倒角。
[0046]
作为本发明的一种优选方案,还包括锁紧螺母10,用于锁紧调节螺钉9。
[0047]
作为本发明的一种优选方案,还包括调整垫片12,安装于主阀芯2和主弹簧3之间。
[0048]
作为本发明的一种优选方案,还包括密封圈(15、16、17、18),密封圈15用于溢流阀与外部结构密封;密封圈16用于导阀座4和阀体1密封;密封圈17用于导阀体7和阀体1密封;密封圈18用于滑动轴8和导阀体7密封。
[0049]
作为本发明的一种优选方案,所述阀体1上设有进口和出口;油液经进口进入阀体1的内腔,然后通过阻尼塞13进入主阀芯2的内腔,然后流入导阀座4与阀体1之间的腔体,最
后通过进油通道达到导阀5;导阀5开启后,油液经回油通道、回油孔后,从阀体1的出口流出。
[0050]
作为本发明的一种优选方案,所述主阀芯2的尾部和分体阀口11将进口和出口隔离。
[0051]
实施例:
[0052]
一种插装型分体阀口内流式高压溢流阀,包括阀体1、主阀芯2、主弹簧3、导阀座4、导阀5、导弹簧6、导阀体7、滑动轴8、调节螺钉9、锁紧螺母10、分体阀口11、调整垫片12、阻尼塞13、螺母14、密封圈(15、16、17、18)。主要技术方案包括如下内容:
[0053]
主阀芯2设计:
[0054]
本发明主阀芯2中心设计为中心通孔,导阀座4交错设置进油通道(即进口孔)与回油通道(即进回油孔),主弹簧腔油液通过导阀座4上导阀进口孔道进入导阀5前端;导阀5开启后先导阀出口油液通过导阀座4上导阀回油孔进入主阀芯2中心孔道,最终回流至溢流阀低压出口,此种将先导阀回油与主阀芯2中心孔结合的方式有效的减小了溢流阀体积与重量。
[0055]
分体阀设计:
[0056]
主阀口采用分体阀口11形式,通过过盈压入与阀体形成整体,分体阀口11通过工装从右端过盈压入至阀口位置,再通过双螺母14进行锁紧,防止进口高压将过盈压入的分体阀口11挤出。此种分体形式可有效提高机加工艺性,防止一体式阀口机加不便,阀口尺寸不易保证等问题。
[0057]
可变阻尼设计:
[0058]
主阀芯2偏置一侧设置螺纹孔,阻尼塞13为外螺纹形式。阻尼塞13中阻尼孔大小在0.2mm-0.3mm之间,阻尼塞13通过螺纹连接与主阀芯2形成整体。本发明可通过安装不同阻尼塞13来调整阻尼孔大小,从而调整启闭特性,从而使不同尺寸公差及弹簧的溢流阀可通过调整阻尼孔满足技术要求。
[0059]
间隙动密封设计:
[0060]
主阀芯2为运动件,其包括两处动密封,为减小摩擦力,动密封采用均牙槽间隙密封形式,均牙槽,为深0.5mm,宽0.5mm的沟槽,油液由于粘性在均牙槽形成环形油膜,起到密封作用。直径小于10mm时采用双均牙槽动密封,直径大于10mm时采用三均牙槽动密封形式。
[0061]
防卡滞弹簧调节装置设计:
[0062]
防卡滞弹簧调节装置,包括带锥角滑动轴8和圆头调节螺钉9,滑动轴8右端作为弹簧座支撑导弹簧6,滑动轴8左端为120
°
锥角,调节螺钉9头部为圆头结构,圆头部分与滑动轴120
°
锥角相接触,从而使调节滑动轴8时防止出现同轴度误差导致滑动轴8偏置使导弹簧6卡滞的问题。
[0063]
长回油腔设计:
[0064]
主阀芯2中心回油孔延长过双螺母14至出口轴向口中心位置,且主阀芯2尾端设计有60
°
+120
°
双倒角,使出油成放射状,防止回油腔压力不稳导致导阀启闭不畅,同时主阀芯2尾端外部设计有内槽,使主阀口开启后高压油液冲击作用在阀芯尾端内槽上,以改善流场,防止高压下出口压力波动导致阀口开启不畅。。
[0065]
主阀芯尾端防压力波动设计
[0066]
主阀芯尾端设置包含内角为α的内槽,使主阀口开启后高压油液冲击作用在主阀芯尾端内角上,以改善流场,防止高压下出口压力波动导致阀口开启不畅。
[0067]
更具体的,一种插装型分体阀口内流式高压溢流阀,如图1所示。
[0068]
主阀芯2结构如图2所示,其尾端放大图如图3所示,主阀芯2中心设计有回油孔,阀芯2中心回油孔延长过螺母14至出口轴向口中心位置,且阀芯2尾端设计有双倒角,出油口尾端设置60
°
+120
°
双倒角。
[0069]
导阀结构如图4所示,导阀进油示意图如图5所示,导阀回油示意图如图6所示,导阀座4交错设置进油通道与回油通道,主弹簧腔油液通过导阀座4上导阀进口孔道进入导阀前端;导阀开启后先导阀出口油液通过导阀座上导阀回油孔进入主阀芯中心孔道,最终回流至溢流阀低压出口。
[0070]
如图7、8所示,分体阀口11通过过盈压入阀体1中,之后通过双螺母14进行锁紧。
[0071]
阻尼塞结构如图9所示,其通过螺纹与主阀芯2相连,装配后效果如图10所示,阻尼塞与主阀芯并通过涂胶紧固。
[0072]
滑动轴结构如图11,调节螺钉结构如图12所示,滑动轴8与调节螺钉9组成防卡滞弹簧调节装置,滑动轴8右端作为弹簧座支撑导弹簧,滑动轴8左端为120
°
锥角,调节螺钉9头部为圆头结构,其圆头部分与滑动轴8的120
°
锥角相接触,从而使调节滑动轴8时防止出现同轴度误差导致滑动轴8偏置使导弹簧卡滞的问题。
[0073]
本发明为内流式先导高压溢流阀,在伺服系统工作过程中将系统多余的液压油溢流回油箱,进而保证系统压力的稳定,也可用作安全阀,限制系统的最大压力,在系统压力过高时实现卸荷,防止压力过载。其工作原理为:进口压力通过阻尼孔进入主弹簧腔,主弹簧腔压力作用在导阀上,当进口压力大于导弹簧6设定值时导阀开启,主弹簧腔油液通过主阀中心孔流向低压区,使主弹簧腔压力降低,在阻尼孔作用下,主阀芯2前后形成压力差,最终使主阀芯2开启。当进口压力小于导弹簧6设定值时,导阀关闭,主弹簧腔重新建立起压力,主阀芯2两端压力相同,主阀芯2在主弹簧3作用下关闭。
[0074]
本发明说明书中未作详细描述的内容属本领域技术人员的公知技术。
[0075]
本发明虽然已以较佳实施例公开如上,但其并不是用来限定本发明,任何本领域技术人员在不脱离本发明的精神和范围内,都可以利用上述揭示的方法和技术内容对本发明技术方案做出可能的变动和修改,因此,凡是未脱离本发明技术方案的内容,依据本发明的技术实质对以上实施例所作的任何简单修改、等同变化及修饰,均属于本发明技术方案的保护范围。