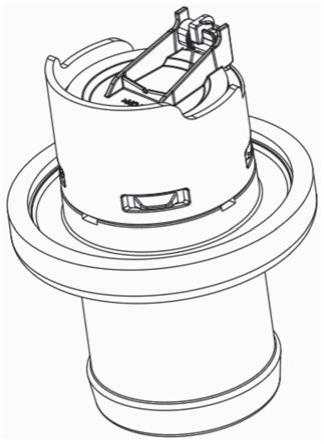
[0001]
本发明涉及一种汽车零部件,尤其涉及一种高效率的和油箱总成、注油系统总成相连接的加油单向阀。
背景技术:[0002]
加油单向阀装配在汽车上,他的工作原理是:连接油箱总成与注油系统总成,注油时,汽油路径注油管,通过加油单向阀自适应打开阀门,持续流入油箱内部,当油箱加满油跳枪,系统停止供油,加油单向阀阀门自适应闭合,阻止汽油反向溢出。
[0003]
专利号2015800443695、2017210476390以及2018106892975都公开了加油单向阀的关系技术,但是这些现有技术的加油单向阀在实际使用中会存在以下缺陷:
[0004]
1、接头与阀体并不相连接,而是通过连接管和o形圈将两者密封连接;
[0005]
2、采用橡胶与阀门本体注塑成型,密封性好,但工艺繁琐难度大,产量限制;
[0006]
3、挡板转轴采用金属轴作为枢轴连接,阀体侧边设有旋转用的孔,挡板侧边设有旋转用的孔,扭簧,以上三个零件通过金属轴穿入,因扭簧受力需要拨动固定,金属轴穿入后需要铆压金属轴两端锁住,此工艺需要工装夹具实现,工艺繁琐,零件多,成本高。
[0007]
其中专利号2015800443695,挡板注塑时,熔融塑料流经枢轴孔一侧,形成分叉,流经枢轴孔对向侧时,又汇合,因不能完全融合而产生接缝,俗称熔接线,熔接线处的强度会大幅减弱。
[0008]
因此,现有技术还有提升的地方。
技术实现要素:[0009]
针对上述缺陷,本发明的目的是提供一种加油单向阀成本低、安装便捷、产量高、不良率降低,以解决现有技术的技术问题。
[0010]
为实现上述目的,本发明采用了以下的技术方案:
[0011]
一种加油单向阀,所述加油单向阀包括一挡板和一阀体,所述阀体包括一阀本体和一轴孔柱,所述轴孔柱的一侧柱体连接所述阀本体,所述轴孔柱的两端面各开设一轴孔;所述挡板包括一板本体、两连接片和两枢轴,两所述连接片连接所述板本体,两所述枢轴分别连接两所述连接片,所述枢轴的位置对应所述轴孔的位置,所述枢轴插入连接所述轴孔。
[0012]
依照本申请较佳实施例所述的加油单向阀,所述挡板还包括两加强片,两所述加强片分别连接两所述连接片。
[0013]
依照本申请较佳实施例所述的加油单向阀,所述挡板还包括一压槽片,所述压槽片轴向凸出于所述挡板,所述压槽片开设一压槽。
[0014]
依照本申请较佳实施例所述的加油单向阀,所述轴孔柱连接所述阀本体的一侧开设一导向槽,所述导向槽包括两槽板和一槽底面,所述槽底面为一倾斜面。
[0015]
依照本申请较佳实施例所述的加油单向阀,所述轴孔柱包括一中间隔片,所述中间隔片的一侧的所述轴孔柱的表面为光滑面,所述中间隔片的另外一侧为所述导向槽。
[0016]
依照本申请较佳实施例所述的加油单向阀,所述加油单向阀还包括一扭簧,所述扭簧的固定臂连接所述阀体;所述扭簧的活动臂连接所述压槽。
[0017]
依照本申请较佳实施例所述的加油单向阀,所述加油单向阀还包括一接头和一密封圈,所述密封圈设置在所述接头和所述阀体之间。
[0018]
本申请的技术方案对现有系列加油单向阀进行改进方案:
[0019]
1、本申请取消连接管和o形圈,通过优化零件结构,实现阀体与接头直接卡扣连接,并利用密封圈结构设定解决密封性能;
[0020]
2、工艺简化方面:本申请采用通过优化零件结构实现了密封圈与挡板分离,密封圈不用二次包胶与挡板上,直接以单体零件预装套入接头与阀体连接部的端面台阶上,再通过阀体套入接头,经卡扣结构锁紧密封圈;此工艺成本低,效率高,安装方便,不良率降低;
[0021]
3、减少零件方面:本申请取消金属轴零件,旋转枢轴集成在挡板侧边枢轴上,直接与阀体侧边轴孔连接;
[0022]
4、组装方面:本申请采用扭簧预装于阀体侧边轴孔外周面,扭簧固定臂抵住阀体最大外圆周面,并拨动活动臂挂入阀体侧边轴孔相邻挡块上,此时扭簧就可以固定,挡板组装时就不会干涉,挡板其中一侧枢轴可以先穿入阀体侧边其中一侧轴孔,挡板另一侧枢轴通过阀体轴孔柱上的导向槽滑入轴孔中,此时扭簧活动臂受挡板滑入动作会自动滑出挡块,压住挡板,受力使挡板复位至安装状态;
[0023]
5、本申请将挡板改为轴,可以有效解决注塑风险,现有技术挡板及扭簧安装时,因没有安装所需的导向及固定机构,使零件组装效率减低;本申请优化结构,将中间隔片的中间增加有阶梯的隔板,用于扭簧安装过程中临时固定,有效避免对挡板安装的干扰,同时挡板安装后转到最大角度时,又能自动将扭簧推出隔板,滑入挡板的压槽中,本申请优化结构,将中间隔片的外圈增加导向槽,用于挡板安装时,能准确滑入轴孔柱孔中。
[0024]
由于采用了以上的技术特征,使得本发明相比于现有技术,具有如下的优点和积极效果:
[0025]
第一、本申请零件结构简单、所需零件数减少,成本低;
[0026]
第二、本申请工艺步骤减少组装效率高,工装治具设计简单。
[0027]
当然,实施本发明内容的任何一个具体实施例,并不一定同时具有以上全部的技术效果。
附图说明
[0028]
图1为本申请加油单向阀外观示意图;
[0029]
图2为本申请加油单向阀炸开示意图;
[0030]
图3为本申请阀体示意图;
[0031]
图4为本申请挡板和扭簧示意图;
[0032]
图5为本申请加油单向阀的俯视示意图;
[0033]
图6为本申请阀体、挡板和扭簧连接示意图;
[0034]
图7为图5的主视示意图;
[0035]
图8为本申请扭簧安装示意图;
[0036]
图9为本申请挡板安装示意图;
[0037]
图10为图9部份放大示意图;
[0038]
图11为本申请加油单向阀剖开示意图。
具体实施方式
[0039]
以下结合附图对本发明的几个优选实施例进行详细描述,但本发明并不仅仅限于这些实施例。本发明涵盖任何在本发明的精髓和范围上做的替代、修改、等效方法以及方案。为了使公众对本发明有彻底的了解,在以下本发明优选实施例中详细说明了具体的细节,而对本领域技术人员来说没有这些细节的描述也可以完全理解本发明。另外,为了避免对本发明的实质造成不必要的混淆,并没有详细说明众所周知的方法、过程、流程、元件等。请参阅图1和图2本申请加油单向阀外观示意图以及炸开示意图,本申请的加油单向阀装配在汽车上,连接油箱总成(图未示)与注油系统总成(图未示),注油时,汽油路径注油管,通过加油单向阀自适应打开阀门,持续流入油箱内部,当油箱加满油跳枪,系统停止供油,加油单向阀阀门自适应闭合,阻止汽油反向溢出,所述加油单向阀包括一接头10、一密封圈20、一阀体30、一挡板40和一扭簧50。
[0040]
请参考图3,所述阀体30包括一阀本体31和一轴孔柱32,所述轴孔柱32的一侧柱体连接所述阀本体31,图3中,所述轴孔柱32的一侧柱体是通过有加强底座的片体连接所述阀本体31,所述轴孔柱32的另外一侧柱体则是和所述阀本体31保持距离,便于扭簧50连接,所述轴孔柱32的两端面各开设一轴孔33,本申请实施例中,两所述轴孔33之间是没有贯通的,但是不能用来限制本申请,将两所述轴孔33之间贯通形成一个通孔,只要能够稳定连接所述挡板40,都应该是本申请的保护范围。
[0041]
请参考图4本申请挡板40和扭簧50示意图,所述挡板40受到所述扭簧50的压力覆盖在所述阀体30的开口处,所述挡板40包括一板本体41、两连接片42和两枢轴43,两所述连接片42连接所述板本体41,如图所示,所述连接片42的一侧连接所述板本体41,所述连接片42的另外一侧则是在所述板本体41的直径范围外侧,两所述枢轴43分别连接两所述连接片42,所述枢轴43的位置对应所述轴孔33的位置,装配时,所述枢轴43插入连接所述轴孔33。为了增加连接强度,所述挡板40还包括两加强片44,两所述加强片44分别连接两所述连接片42,图4中两所述加强片44平行设置在所述挡板40上,所述加强片44的一侧连接所述连接片42。
[0042]
如图4所示,所述挡板40还包括一压槽片45,所述压槽片45轴向凸出于所述挡板40,所述压槽片45开设一压槽46,所述压槽46是片体上的一个缺口,请参考图5,所述压槽46的设置目的在于连接所述扭簧50,所述扭簧50进入所述压槽46中不会乱动,本申请实施例中,所述压槽片45的两端分别连接两所述加强片44,这样的设计方便所述扭簧50进入所述压槽46中,但是不能用来限制本申请,即使所述压槽片45的两端不触碰所述加强片44,只要方便所述扭簧50进入所述压槽46中都应该是本申请的保护范围,此外,本申请所述板本体41、两连接片42、两枢轴43、两加强片44、压槽片45和压槽46一体成型制成,这种一体成型的设计使得所述枢轴43在插入连接所述轴孔33后不会变形,而且所述连接片42和加强片44的整体结构强度强,不会有内应力,不会受力翻转,所述枢轴43插入连接所述轴孔33中得到强力的支撑。挡板注塑时,熔融塑料流经枢轴孔一侧,形成分叉,流经枢轴孔对向侧时,又汇
合,因不能完全融合而产生接缝,俗称熔接线,熔接线处的强度会大幅减弱。本申请将挡板改为轴,就可以有效解决注塑风险。
[0043]
请同时参考图3和图6,所述轴孔柱32连接所述阀本体31的一侧开设一导向槽34,所述导向槽34包括两槽板和一槽底面,所述槽底面为一倾斜面,在装配时,首先插入另外一侧的所述枢轴43进入所述轴孔33,在这之前所述扭簧50已经先套设在所述轴孔柱32,接着将这一侧的所述枢轴43放入所述导向槽34中,所述枢轴43在两所述槽板的限位下,沿着倾斜面的所述槽底面逐步滑向所述轴孔33中,完成所述阀体30、挡板40和扭簧50的连接。
[0044]
如图6所示,所述轴孔柱32包括一中间隔片35,所述中间隔片35的一侧的所述轴孔柱32的表面为光滑面,所述中间隔片35的另外一侧为所述导向槽34;所述轴孔柱32的表面为光滑面的一侧,也就是所述轴孔柱32和所述阀本体31之间保持距离的一侧,所述扭簧50套设连接所述轴孔柱32的表面为光滑面的一侧,装配后,所述扭簧50的固定臂连接所述阀体30,如图7所示,所述扭簧50的固定臂抵住所述阀体30最大外圆周面;另外,如图5所示,所述扭簧50的活动臂连接所述压槽46。
[0045]
请同时参考图6、图8、图9和图10扭簧50和挡板40安装示意图,所述扭簧50预装于所述阀体30侧边所述轴孔33外周面,所述扭簧50的固定臂抵住所述阀体30最大外圆周面,如图6所示,所述中间隔片35的一侧为一缺口阶梯351,所述缺口阶梯351就像是一个挡块,如图8所示,如箭头方向所示,拨动所述扭簧50的活动臂将所述扭簧50的固定臂挂入所述中间隔片35的一侧的所述缺口阶梯351上,如图9和图10所示,所述缺口阶梯351将所述扭簧50的活动臂挡住不至于滑动,图10所述扭簧50的活动臂是示意图,用来显示活动臂和所述缺口阶梯351的位置,此时所述扭簧50已固定,所述挡板40组装时就不会干涉,所述挡板40其中一侧所述枢轴43先穿入所述阀体30侧边其中一侧所述轴孔33,所述挡板40另一侧所述枢轴43通过所述阀体30的所述轴孔柱32上的所述导向槽34滑入所述轴孔33中,此时所述扭簧50的活动臂受所述挡板40滑入动作会自动脱离所述缺口阶梯351的阻挡滑入所述压槽46,如图5中压住所述挡板40,受力使所述挡板40复位至安装状态。
[0046]
请同时参考图11本申请加油单向阀剖开示意图;图中所述密封圈20的剖开面呈y字型,y字型的外侧的短的部份在装配时被挤压保证密封的强度效果,所述密封圈20设置在所述接头10和所述阀体30之间。所述密封圈20预装套入所述接头10连接部的端面台阶上,再通过组装好后所述阀体30套入所述接头10,经卡扣结构锁紧密封圈20,如图2所示,所述接头10均匀分布多数个卡凸11,相对的,所述阀体30均匀分布多数个卡槽36,装配时,所述卡凸11卡入所述卡槽36中,将所述接头10和所述阀体30紧密结合。
[0047]
综上所述,由于采用了以上的技术特征,使得本发明相比于现有技术,具有如下的优点和积极效果:
[0048]
第一、本申请零件结构简单、所需零件数减少,成本低;
[0049]
第二、本申请工艺步骤减少组装效率高,工装治具设计简单。
[0050]
发明优选实施例只是用于帮助阐述本发明。优选实施例并没有详尽叙述所有的细节,也不限制该发明仅为所述的具体实施方式。显然,根据本说明书的内容,可作很多的修改和变化。本说明书选取并具体描述这些实施例,是为了更好地解释本发明的原理和实际应用,从而使所属技术领域技术人员能很好地利用本发明。本发明仅受权利要求书及其全部范围和等效物的限制。以上公开的仅仅是本发明的较佳实施例,但并非用来限制其本身,
任何熟习本领域的技术人员在不违背本发明精神内涵的情况下,所做的均等变化和更动,均应落在本发明的保护范围内。