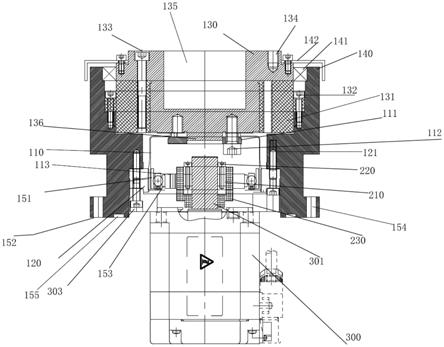
[0001]
本申请涉及数控机械技术领域,尤其涉及一种伺服电机直联输入谐波减速机。
背景技术:[0002]
谐波减速机经过几十年的发展,现应用十分广泛。经过几代人的技术改革创新品种也多样化,但主要还应用在多关节机械手上,在机床领域的发展和应用存在很多的不足。
[0003]
在现有已公开的专利技术来看到有几个方法:最常用的是用键槽联接诸如苏州绿的谐波传动科技股份有限公司的cn201220466990.4、cn201920329935.2等专利,通过伺服电机的轴上健与波发生器的内孔键进行装,缺点很明显,键如公差大则没有精度,但容易装入,如公差小则精度会好一点,但不容易装入,而且无论是通过敲入还是压入都会对伺服电机轴有所影响,如拆装维修则无法保证精度使用。日本哈默纳科还有一种方法也是键槽式,但加入一个十字联轴器,虽然在波生器高速旋转时与电机轴的同心度得到了调整,但十字联轴器的配合间隙无法消除,定位精度大大下降。在现有技术中,还有一种中空轴的联接方法,是通过同步带轮来传动,这是一种二级传动,虽然传动的震动可以调节,安装也比较简单,但传递精度会有所下降。
[0004]
在现有已公开的专利技术看到cn207715679u的专利,其存在很多的技术问题,这种电机轴与波发生器硬联接方式,不适合正常的伺服电机,轴端的联接只是用套刚性胀入并无弹性收与缩,精度及稳定不能得到良好的应证,另外如能实现其所述技术也只能用于帽檐型的柔轮,因柔轮与波发生器的装入只能从柔轮带齿面一端装入,如是杯型的柔轮则固定端为杯底所以无法实现安装,另外帽檐型的柔轮结构是帽檐处圆孔内径小,而柔轮带齿这一端大,故而波发生器根本无法从帽檐处圆孔端穿入。另外就算这种联接方式能使用,也只能实现钢轮端输出,不能实柔轮端输出,综合实际应用发现其存在许多不足及技术问题。
技术实现要素:[0005]
为了解决上述技术问题,本申请实施例提供一种伺服电机直联输入谐波减速机,包括谐波减速机、波发生器组件电机轴联接装置和伺服电机;所述伺服电机的输入轴与谐波减速机的波发生器组件的轴心孔通过波发生器组件电机轴联接装置的联接形成精密套入式结构装配;所述波发生器组件电机轴联接装置包括胀紧套、胀紧套锁紧螺栓和波发生器组件轴心孔伺服电机输入直联联接套;所述波发生器组件轴心孔伺服电机输入直联联接套的外侧与波发生器轴承内圈的套接面为一体加工而成;所述波发生器组件轴心孔伺服电机输入直联联接套的内侧安装所述胀紧套;所述胀紧套外径通过紧固锁紧力胀紧固定在波发生器组件的轴心孔上;所述胀紧套内径固定在电机轴的输出轴轴径上;所述胀紧套与电机轴的输出轴同步运动;
[0006]
所述波发生器组件轴心孔伺服电机输入直联联接套的纵截面为垂直的z字形,分成上下分布的大圆环孔和小圆环孔,其中,大圆环孔内部用于放置所述胀紧套;所述电机轴
的输出轴自下而上穿过小圆环孔后与胀紧套连接;所述小圆环孔的内径与电机轴的输出轴外径一致,精密公差配合,实现精定位;
[0007]
所述胀紧套包括胀紧外套和胀紧内套,且胀紧外套和胀紧内套沿母线上均开有收缩槽;所述胀紧外套的内壁和胀紧内套的外壁均为台阶状,且每级台阶均为圆锥面;所述胀紧内套的端面四周设置有顶丝孔,用于将胀紧外套和胀紧内套分离;所述胀紧套设置有贯穿胀紧外套和胀紧内套的锁紧孔;所述锁紧孔匹配有锁紧螺栓,用于调节胀紧外套和胀紧内套之间的距离从而改变胀紧程度。
[0008]
进一步地,所述谐波减速机包括减速机柔轮、减速机刚轮、波发生器、输出端轴和减速机壳体;所述减速机柔轮采用杯型柔轮;所述减速机的减速输出方式是钢轮固定不动,通过波发生器高速旋转带动柔轮减速输出;
[0009]
所述减速机柔轮的内圈与波发生器轴承外圈采用插入直联套接;
[0010]
所述减速机柔轮的输出端面内设置有柔轮锁紧压块;所述减速机柔轮锁紧压块为平面圆形无止口凸台;所述减速机柔轮的端面通过螺栓连接输出端轴;所述螺栓将柔轮锁紧压块与柔轮的输出端面叠压一起锁紧;
[0011]
所述输出端轴的输入端设置有精定位轴头凸台,轴头凸台的同心度、垂直度与输出断面与减速机柔轮的端面相接且保持高精度一致性;所述输出端轴固定在径轴向转盘轴承的内孔;所述径轴向转盘轴承的外圈固定在减速机壳体内,所述径轴向转盘轴承以内圈转动,外圈不动的方式承载;所述输出端轴的输出面设置有盘面通孔和盘面螺孔;所述输出端轴通过盘面通孔与转盘轴承内圈螺孔联接;所述输出端轴盘面螺孔用联接外工件或夹具;
[0012]
所述减速机壳体的输出面内孔,位于径轴向转盘轴承固定轴圈螺丝顶部,设置有骨架油封,使输出轴与减速机壳体的内腔口形成密封;所述减速机壳体在谐波减速机的输出轴头下沉处设有防尘罩;
[0013]
所述减速机壳体安装底位也设有密封槽,用于加入密封,实现全封闭高级双重防护。
[0014]
进一步地,所述径轴向转盘轴承采用高精度p4以上级的转盘轴承,跳动精度控制在5um以下;所述径轴向转盘轴承输出内圈顶面设有圆周均布通孔、螺孔用于固定输出端轴。
[0015]
进一步地,所述减速机壳体为圆筒型,安装底面设有法兰盘式台阶面,底面与内孔垂直精度小于0.01mm;所述减速机壳体为整体精加工,内孔轴承定位面、谐波刚轮定位面及伺服电机定位皆采用精加工;所述减速机壳体的内孔定位面为内孔壁与垂直于孔壁的凸台面。
[0016]
进一步地,所述伺服电机的电机板为圆形;所述电机板外圆与内孔均用于精度定位;所述伺服电机先穿过电机板有精度的内孔,用伺服电机输出端止口定位,通过螺栓固定在电机机板上,再装入波发生器,通过胀紧套与伺服电机轴固定后,再装入减速机壳体内腔同时也把波发生器一起插入到柔轮中,再用螺栓锁紧电机板完成整个动力输入装配。
[0017]
进一步地,所述谐波减速机输出端轴的外形为法兰形,并采用整体加工件。
[0018]
在本申请实施例中,伺服电机输入轴与谐波减速机的波发生器通过精密套入式结构装配,再用胀紧套把波发生器与伺服电机轴高刚性固定,将电机与谐波发生器的联接结
构采用上述结构之后,普通的操作者就可以实现精准地把伺服电机与谐波减速机的波发生器装配好,改变了以往以键槽作为主要联接方式的措施。
附图说明
[0019]
为了更清楚地说明本申请实施例或现有技术中的技术方案,下面将对实施例或现有技术描述中所需要使用的附图作简单地介绍,显而易见地,下面描述中的附图仅仅是本申请的一些实施例,对于本领域普通技术人员来讲,在不付出创造性劳动的前提下,还可以根据这些附图获得其他的附图。
[0020]
图1是本申请实施例提供的整机剖面结构示意图;
[0021]
图2是减速机柔轮与波发生器组件电机轴联接装置的示意图;
[0022]
图3是柔轮的剖面结构示意图;
[0023]
图4是图3的左视图;
[0024]
图5是柔轮锁紧压块的结构示意图;
[0025]
图6是图2的局部放大示意图;
[0026]
图7是图6的右视图;
[0027]
图8是胀紧套的横截面结构示意图;
[0028]
图9是胀紧套的纵截面结构示意图;
[0029]
图10是胀紧外套的截面结构示意图;
[0030]
图11是胀紧内套的截面结构示意图;
[0031]
图12是减速机外壳的剖面结构示意图;
[0032]
图13是输出端面的结构示意图;
[0033]
图14是径轴向转盘轴承的俯视图;
[0034]
图15是径轴向转盘轴承的截面图;
[0035]
图16是径轴向转盘轴承的立体图。
[0036]
图中附图标记的含义:
[0037]
100-谐波减速机,110-减速机柔轮,110a-柔轮齿面,110b-柔轮固定面及输出端,111-柔轮锁紧压块,111b-柔轮高精度中心定位孔,112-柔轮锁紧压块螺栓,113-波发生器顶丝孔,114-刚轮与伺服电机板精定凸台,120-减速机刚轮,121-固定螺栓,130-输出端轴,131-径轴向转盘轴承,132-径轴向转盘轴承固定轴圈螺丝,133-盘面通孔,134-盘面螺孔,135-避空位,136-精定位轴头凸台,137-轴承固定精定位面,140-减速机壳体,141-骨架油封,141b-油封位,142-防尘罩,142b-防尘罩螺孔,150-波发生器,1501-波发生器轴承,151-波发生器轴承外圈,152-减速机安装底座,153-波发生器轴承内圈,154-减速机安装孔,155-密封圈卡入槽,156-轴承旋转的内圈螺孔,157-轴承旋转的内圈,158-径轴向转盘轴承固定外圈,159-真圆形滚柱,200-波发生器组件电机轴联接装置,210-胀紧套,211-收缩槽,212-顶丝孔,213-胀紧外套,214-胀紧内套,220-胀紧套锁紧螺栓,230-波发生器组件轴心孔伺服电机输入直联联接套,300-伺服电机,301-输出轴头,303-伺服电机板安装孔。
具体实施方式
[0038]
为使得本申请的申请目的、特征、优点能够更加的明显和易懂,下面将结合本申请
实施例中的附图,对本申请实施例中的技术方案进行清楚、完整地描述,显然,下面所描述的实施例仅仅是本申请一部分实施例,而非全部的实施例。基于本申请中的实施例,本领域普通技术人员在没有做出创造性劳动前提下所获得的所有其它实施例,都属于本申请保护的范围。
[0039]
下面结合附图和具体实施例,进一步阐明本发明。
[0040]
在本申请的描述中,需要理解的是,术语“上”、“下”、“顶”、“底”、“内”、“外”等指示的方位或位置关系为基于附图所示的方位或位置关系,仅是为了便于描述本申请和简化描述,而不是指示或暗示所指的装置或元件必须具有特定的方位、以特定的方位构造和操作,因此不能理解为对本申请的限制。
[0041]
本申请所涉及的一种伺服电机直联输入谐波减速机,主要的创新之处在于伺服电机输入轴与谐波减速机的波发生器通过精密套入式结构装配,再用胀紧套把波发生器与伺服电机轴高刚性固定。这种创新的方法有利只要有一点机械知识的人就能精准地把伺服电机与谐波减速机的波发生器装配好。
[0042]
具体地,结构上如图1所示,包括谐波减速机100、波发生器组件电机轴联接装置200和伺服电机300。如图2所示,谐波减速机100包括减速机柔轮110、减速机刚轮120、输出端轴130和减速机壳体140。
[0043]
本申请中,减速机柔轮110采用杯型柔轮。已公开的专利中,专利cn207715679u所涉及到的一种新型谐波减速器,其采用的是礼帽型柔轮,礼帽型减速机的特点是输入轴和输出端面是同向,该礼帽型减速机以波发生器作为输入,刚轮作为输出,柔轮作为固定并由十字交叉轴承作为保持承载,在本领域中刚轮输出传动比一般为51/81/101/121/161等,且该申请中所采用的结构无法在礼帽型柔轮下实现柔轮的输出。该机构的安装过程方式是与本方案完全不同的。此外在该申请中,胀紧套的加入是为了使得降低对输入轴的长度要求,使得短一点的输入轴也能够使用,这一点与本方案是完全不同的。本方案中所采用的杯型柔轮,其无法使用该申请中的结构,且安装方式也不同,本方案是以波发生器作为输入,柔轮作为输出,刚轮作为固定,在本领域中柔轮输出常用传动比为50/80/100/120/160等整数速比。虽然在传动比上两者相差1,但是对于精度上的计算是影响非常大的,在数控系统的计算中会出现更多的小数点,刚轮作为输出时,由于其传动比的数字比较特殊,在编程上的难度加大。本申请采用的柔轮输出方式能够对精度有更大的保证。
[0044]
本申请中谐波减速机包括减速机柔轮110、减速机刚轮、输出端轴和减速机壳体。减速机柔轮110采用且只能采用杯型柔轮,减速机的减速输出方式是钢轮固定不动,通过波发生器高速旋转带动柔轮减速输出。
[0045]
减速机柔轮110的输出端面内设置有柔轮锁紧压块111,减速机柔轮110的端面通过螺栓连接输出端轴,螺栓将柔轮锁紧压块111与柔轮的输出端面叠压一起锁紧。
[0046]
输出端轴130的输入端设置有精定位轴头凸台136,轴头凸台136的同心度、垂直度与输出断面与减速机柔轮的端面相接且保持高精度一致性,输出端轴固定在径轴向转盘轴,131的内孔,径轴向转盘轴131的外圈固定在减速机壳体内,径轴向转盘轴承131以内圈转动,外圈不动的方式承载。径轴向转盘轴承131输出内圈顶面设有圆周均布通孔、螺孔用于固定输出端轴。
[0047]
输出端轴130的输出面(图中为顶面)设置有盘面通孔133和盘面螺孔134,输出端
轴通过盘面通孔与转盘轴承内圈螺孔联接,输出端轴盘面螺孔用联接外工件或夹具。本申请中盘面通孔133采用沉孔式结构,用于联接轴承内圈。盘面螺孔134用于联接外部其他部件。整个输出端轴130的输出侧中心处设置避空位135。
[0048]
传统的谐波减速机体积虽小,但轴承也用得小,故无论是外壳,还是输出轴承刚性都比较小,为了提高轴承的刚性,保障输出时的径轴向跳动精度,采用了高精度p4以上级径轴向转盘轴承131,跳动精度可以控制在5um以下,提高刚性及达到超精密旋转。此外本申请为了提高输出轴端的刚性及精度,采用了大盘面输出轴心。
[0049]
本申请中,谐波减速机应用的是径向转盘轴承,转盘轴承如图14-16所示,其具备结构紧凑、引导旋转方便、安装简便和维护容易的特点。
[0050]
转盘轴承的内圈由上下两层夹持而成,转盘轴承的外圈位于两个内圈连接处的外部,且,转盘轴承的外圈的上下面均设置有真圆形滚柱,用于承载上下方向的力,转盘轴承的外圈内侧面设置有真圆形滚柱,用于承载左右方向的力。现有技术中的专利都是十字交叉滚子轴承,多为相互垂直且以斜向45度分布的两列滚子,无法实现本申请中转盘轴承在径向和轴向上的精度要求。在本申请中改用转盘轴承,可以提高刚性以及精度,相比于滚子轴承,转盘轴承的优势在于能够加工出更高的精度,从而在实际的使用过程中,大幅提高并且保障精度的要求。
[0051]
本结构中,轴心与减速机柔轮110的联接方法式进行了创新,通过输出轴端面、轴承靠接面,柔轮定位端与面进行一体化精磨加工,使其达到更高旋转精度,而传统的谐波减速机,都是通过多层套接,损失精度。
[0052]
作为一个具体的实施例,减速机壳体140的输出面内,位于径轴向转盘轴承固定轴圈螺丝132顶部,设置有骨架油封141,以形成密封。减速机壳体140在谐波减速机100的输出轴头下沉处设有防尘罩142。减速机壳体安装底位也设有密封槽,用于加入密封,实现全封闭高级双重防护。同时,减速机壳体140内壁上设置有多个精定位凸台,包括刚轮与伺服电机板精定凸台114、轴承固定精定位面137,以实现精定位。
[0053]
如图所示,波发生器组件电机轴联接装置200包括胀紧套210、胀紧套锁紧螺栓220和波发生器组件轴心孔伺服电机输入直联联接套230。
[0054]
波发生器组件轴心孔伺服电机输入直联联接套230的外侧与波发生器轴承内圈153采用一体加工成型,通过波发生器顶丝孔113进行波发生器组件轴心孔伺服电机输入直联联接套230与电机外壳的分离。
[0055]
波发生器组件轴心孔伺服电机输入直联联接套230的纵截面为z字形,分成上下分布的大圆环孔和小圆环孔,其中大圆环孔内部用于安装胀紧套210,电机轴的输出轴头301自下而上穿过小圆环孔后与胀紧套210连接。胀紧套210内径固定在电机轴的输出轴头301轴径上实现同步运动。此外,整个大圆环孔用于胀紧套210的胀紧安装,小圆环孔用于对电机轴的输出轴进行精定位,本实施例中小圆环孔用磨床精加工,使得小圆环孔的内径与电机轴的输出轴的外径一致,最优选的情况是等同,从而实现完美的精定位。
[0056]
此外,本申请中为了进一步地提高整个加工的进度,减速机壳体采用圆筒型,安装底面设有法兰盘台阶面,底面与内孔垂直精度小于0.01mm。减速机壳体为整体精加工,内孔轴承定位面、谐波刚轮定位面及伺服电机定位皆采用精加工。减速机壳体的内孔定位面为内孔壁与垂直于孔壁的凸台面。伺服电机的电机板为圆形,电机板外圆与内孔均用于精度
定位。
[0057]
上述整个波发生器的联接方式,可以提高电机安装精度,使电机在高速旋转时,动平衡更稳定,震动更小,同比旋速可以提得更高,伺服电机的“增益"值可以设置得更高,从而使伺服电机自身的刚性发挥调校到最佳态,伺服电机静态、动态锁定力增加,从而实现减速机刚性增加。
[0058]
如图所示,胀紧套210包括胀紧外套213和胀紧内套214,且胀紧外套213和胀紧内套214沿母线上均开有收缩槽211。胀紧外套213的内壁和胀紧内套214的外壁均为台阶状,且每级台阶均为圆锥面,当胀紧内套214向胀紧外套213移动时,两者之间的胀紧力会增大。胀紧内套214的端面四周设置有顶丝孔212,用于将胀紧外套213和胀紧内套214分离。胀紧套210设置有贯穿胀紧外套213和胀紧内套214的锁紧孔,匹配有锁紧螺栓220,用于调节胀紧外套213和胀紧内套214之间的距离从而改变胀紧程度。
[0059]
在使用时,胀紧外套213与电机轴的输出轴连接,收缩槽211可以使得胀紧套210自身可有一定的膨胀,利用锁紧锁紧螺栓230的动作将胀紧内套214向胀紧外套213移动,随着胀紧内套214与胀紧外套213之间的相对距离越来越小,胀紧内套214与胀紧外套213之间的胀紧力增大,胀紧内套214受到胀紧力与内部的电机轴的输出轴紧密连接,胀紧外套213受到胀紧力向外膨胀,与波发生器组件轴心孔伺服电机输入直联联接套230紧密连接。
[0060]
本创新的目的是通过直联的方式提高伺服电机的传递精度,做到装配简单实用的目的。伺服电机输入轴与谐波减速机的波发生器通过精密套入式结构装配,再用胀紧套把波发生器与伺服电机轴高刚性固定,将电机与谐波发生器的联接结构采用上述结构之后,普通的操作者就可以实现精准地把伺服电机与谐波减速机的波发生器装配好,改变了以往以键槽作为主要联接方式的措施。
[0061]
在进行本装置的安装时,伺服电机先穿过电机板有精度的内孔,用伺服电机输出端止口定位,通过螺栓固定在电机机板上,再装入波发生器,通过胀紧套与伺服电机轴固定后,再装入减速机壳体内孔。进行拆卸时,将波发生器和伺服电机先从减速机壳体内取出,在利用胀紧套的拆卸方式,将波发生器与伺服电机进行拆卸。这种创新的方法使得普通的操作者就可以实现精准地把伺服电机与谐波减速机的波发生器装配好,改变了以往以键槽作为主要联接方式的措施,通过加入了高精度转盘轴承,配合高精度安装壳体,实现了既能达到高精度的减速定位,又能实现高精度径轴向跳动精度。
[0062]
以上详细描述了本发明的优选实施方式,但是本发明并不限于上述实施方式中的具体细节,在本发明的技术构思范围内,可以对本发明的技术方案进行多种等同变换(如数量、形状、位置等),这些等同变换均属于本发明的保护。