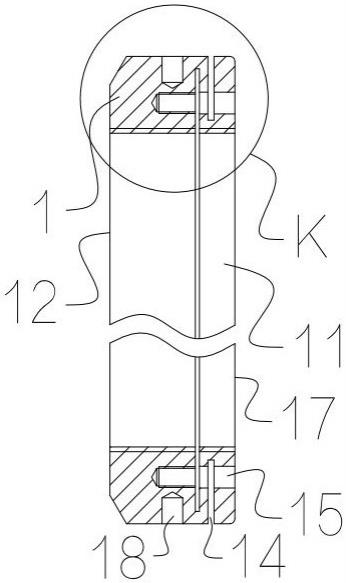
[0001]
本实用新型涉及紧固件技术领域,更具体地是涉及一种大型内外槽自锁螺母。
背景技术:[0002]
螺母是一种常见的紧固件。对于标准螺母通常配合弹性垫圈或止动垫圈一起使用来进行防松保护。但是对大型螺母,由于空间位置、垫圈的加工装配、螺母的装配、防松效果等原因,基本无法采用弹性垫圈或止动垫圈进行防松保护。
[0003]
现有技术中针对一些非标准螺母采用各种各样的防松方法。例如名称为一种自锁的圆螺母,申请号为201821469749.0的中国实用新型专利公开了一种自锁式的螺母。该专利方案的主要改进结构是贯穿螺母的侧壁开设一个弧形的自锁缺口,并在自锁缺口的位置锁紧螺钉,利用螺钉的外螺牙补偿螺母自锁缺口处的内螺纹,进而改变螺母的自锁缺口处的局部螺距,从而解决螺母容易出现松动的问题。但是,该专利方案针对且只适用于小型螺母,对于大型螺母而言,这种改进结构的防松效果不理想。另外贯穿螺母的侧壁的缺口结构对螺母自身的强度影响较大。此外改变螺母的自锁缺口处的局部螺距,也就是使这种缺口结构处产生足够大的变形量需要对螺钉施加的扭矩也较大,对于大型螺母而言有时即使拧断螺钉也无法提供足够大的变形量。
技术实现要素:[0004]
本实用新型为克服上述现有技术中的不足,提供了一种大型内外槽自锁螺母。
[0005]
本实用新型通过以下技术方案来实现上述目的。
[0006]
一种大型内外槽自锁螺母,包括本体,所述的本体上设有绕着螺母的轴心布置的整圈的内侧开口槽和整圈的外侧开口槽,内侧开口槽的开口朝向螺母的轴心,外侧开口槽的开口背离螺母的轴心,内侧开口槽和外侧开口槽在螺母的轴心方向上错位布置,本体上绕着螺母的轴心布置有若干个螺丝过孔,螺丝过孔从螺母的轴向一端开始并贯穿内侧开口槽和外侧开口槽,本体上设有用于和穿过螺丝过孔的螺栓螺纹配合的内螺纹孔。
[0007]
对于大型螺母来说,像现有技术一样只在局部开设自锁缺口然后锁紧螺钉所能提供的防松作用力十分有限,而且需要对螺钉施加足够大的扭矩才能使螺母产生足够大的刚性变形,所以基本无法提供有效的防松作用力。为此,本方案考虑利用整圈的内侧开口槽和整圈的外侧开口槽,并开设若干个螺丝过孔和内螺纹孔,从而可以采用螺栓穿过螺丝过孔并锁紧到内螺纹孔中来提供防松作用力。整圈的内侧开口槽和整圈的外侧开口槽在保证螺母具有足够强度的前提下锁紧螺栓时更容易产生刚性变形,产生的变形效果更好,而且内侧开口槽和外侧开口槽错位布置可以形成耦合效应,防松效果更有效。沿螺母周向锁紧多个螺栓后,螺母沿周向提供的防松作用力的大小分布接近波浪形,也就是说螺母和与之螺纹配合的零件之间的相互作用力在周向上更加均衡,使自锁防松效果更好。
[0008]
上述的内侧开口槽和外侧开口槽分别包括两个相互平行的内壁面,这些内壁面都和螺母的轴心垂直。例如内侧开口槽和外侧开口槽在螺母轴向上的截面为矩形或者u形,这
样加工更加简单,而且可以和螺母的中心内螺纹通孔在同一机台上加工,相对来说省去拆卸搬运过程,对于大型螺母的拆卸和搬运是很费时费力的,本结构自然就降低了工艺成本,缩短了工艺时间。
[0009]
上述的本体上绕着螺母的轴心布置有若干个用于插接柱销的装配工艺孔,装配工艺孔的轴心都指向螺母的轴心,且装配工艺孔的孔口都外露于本体。装配工艺孔可以是圆柱孔,也可以是内螺纹孔,可以是通孔,也可以是盲孔。大型螺母不同于标准螺母等可以用扳手或钳子等直接拧动,该结构在本体上布置装配工艺孔,装配时可以用大型柱销插入装配工艺孔中,这样可以扳着大型柱销来拧动螺母。
[0010]
本实用新型与现有技术相比还具有如下有益效果:锁紧螺栓后螺母整体上多点受力,受力更加均衡,受力点多自锁防松效果好,采用整圈的开口槽所提供的可变形量更大,本体上没有贯穿螺母的侧壁的结构,对螺母整体结构强度影响较小,节省加工工艺成本,加工效率更高。
附图说明
[0011]
图1为本实用新型实施例的圆螺母带折断线的剖面结构示意图。
[0012]
图2为图1中k处的局部放大图。
[0013]
图3为本实用新型实施例的圆螺母使用状态参考示意图。
具体实施方式
[0014]
下面结合附图对本实用新型做进一步说明。附图仅用于示例性说明,不能理解为对本专利的限制。
[0015]
为了更简洁的说明本实施例,附图或说明中某些本领域技术人员公知的、但与本实用新型的主要内容不相关的零部件会有所省略。另外为便于表述,附图中某些零部件会有所省略、放大或缩小,但并不代表实际产品的尺寸或全部结构。
[0016]
实施例:
[0017]
如图1和图2所示,一种大型内外槽自锁圆螺母,包括圆环形的本体1,本体1的轴心处为中心内螺纹通孔11,对于大型螺母的中心内螺纹通孔通常采用梯形螺纹。如图3所示,本实施例的大型内外槽自锁圆螺母用于压紧一大型滚动轴承2,圆螺母的左端面12用于抵着轴承2的右端面。
[0018]
再如图1和图2所示,本体1上设有绕着圆螺母的轴心布置的整圈的内侧开口槽13和整圈的外侧开口槽14,其中内侧开口槽13的开口朝向圆螺母的轴心,外侧开口槽14的开口背离圆螺母的轴心。本实施例中的内侧开口槽13和外侧开口槽14在圆螺母轴向上的截面都是矩形,也可以说内侧开口槽13和外侧开口槽14分别是矩形截面绕着圆螺母的轴心旋转形成的圆环槽。在其它实施例中内侧开口槽13和外侧开口槽14可以都采用u形截面,或者一个开口槽采用矩形截面,另一个开口槽采用u形截面。无论采用矩形截面还是采用u形截面,内侧开口槽13和外侧开口槽14都会分别形成两个相互平行的内壁面,这些内壁面都和圆螺母的轴心垂直,这样加工更加简单,而且可以和圆螺母的中心内螺纹通孔11在同一机台上加工,相对来说省去拆卸搬运过程,对于大型圆螺母的拆卸和搬运是很费时费力的,本实施例自然就降低了工艺成本,缩短了工艺时间。
[0019]
本实施例中的内侧开口槽13和外侧开口槽14沿着圆螺母的轴心方向错位布置,如图1和图2所示,内侧开口槽13和外侧开口槽14是平行交错的,外侧开口槽14位于内侧开口槽13的右侧。
[0020]
本体1上绕着圆螺母的轴心均匀布置有十个螺丝过孔15和十个锁紧用内螺纹盲孔16,这十个螺丝过孔15和十个内螺纹盲孔16的轴心都和圆螺母的轴心平行。每个螺丝过孔15从圆螺母轴向上靠近外侧开口槽14的一端开始并贯穿外侧开口槽14和内侧开口槽13,也就是从图1和图2中圆螺母的右端面17开始依次贯穿外侧开口槽14和内侧开口槽13。本实施例中的十个锁紧用内螺纹盲孔16分别和十个螺丝过孔15同轴布置,每个锁紧用内螺纹盲孔16从图1和图2中内侧开口槽13的左侧内壁面开始向圆螺母的左侧延伸。锁紧用内螺纹盲孔16用于和穿过螺丝过孔15的螺栓螺纹配合,从而引起螺母自身产生变形,尤其是使圆螺母的中心内螺纹通孔11处产生变形,也就是圆螺母的内螺牙产生变形,从而提供自锁防松作用力。在其它实施例中,可以将锁紧用内螺纹盲孔16贯通至圆螺母的左端面12,但是对于圆螺母的整体强度和端面平整度等的影响明显超过本实施例采用的盲孔结构。螺丝过孔15和锁紧用内螺纹盲孔16的数量相同,具体数量和具体尺寸本领域技术人员可以根据圆螺母的尺寸进行合理设计,还可以利用三维软件或者力学分析软件等进行受力分析和优化设计。
[0021]
本体1上绕着圆螺母的轴心均匀布置有八个用于插接柱销的圆柱形装配工艺孔18,本实施例中的装配工艺孔18的轴心都指向圆螺母的轴心,且都和圆螺母的轴心垂直,装配工艺孔18的孔口都位于本体的径向外轮廓面上,也就是圆螺母的外圆面上。其它实施例中也可以采用工艺螺纹孔。大型圆螺母不同于标准螺母等可以用扳手或钳子等直接拧动,本实施例在本体1上布置装配工艺孔18,装配时可以用大型柱销插入装配工艺孔18中,这样可以扳着大型柱销来拧动圆螺母。
[0022]
为了便于理解,此处列出本实施例的大型内外槽自锁圆螺母的一些相关尺寸,外侧直径为1470mm,内侧最小直径为1310mm,厚度为116mm。内侧开口槽13的截面尺寸为:长是61mm,宽是4mm。外侧开口槽14的截面尺寸为:长是61mm,宽是5.8mm。内侧开口槽13和外侧开口槽14之间的距离为8mm。外侧开口槽14的右侧内壁面到圆螺母的右端面17之间的距离为19.6mm。螺丝过孔15的直径为20.8mm,内螺纹盲孔为m20的螺纹孔。螺丝过孔15均布在直径为1382mm的圆上。这些参数只是为了举例说明,本实用新型所要求的保护范围不局限于此。
[0023]
本实施例使用时,将大型柱销插入装配工艺孔18中,然后将圆螺母对准与之螺纹配合的零件,扳动大型柱销来拧动圆螺母,直至圆螺母的左端面12贴紧轴承2,然后将十根螺栓分别穿过十个螺丝过孔15并分别锁紧到十个锁紧用内螺纹盲孔16中。
[0024]
本实施例利用整圈的内侧开口槽13和整圈的外侧开口槽14,并利用多根螺栓穿过螺丝过孔15并锁紧到内螺纹盲孔16中来提供防松作用力。整圈的内侧开口槽13和整圈的外侧开口槽14在保证圆螺母具有足够强度的前提下锁紧螺栓时更容易产生刚性变形,产生的变形效果更好,而且内侧开口槽13和外侧开口槽14错位布置可以形成耦合效应,防松效果更有效。沿圆螺母周向锁紧多个螺栓后,圆螺母沿周向提供的防松作用力的大小分布接近波浪形,也就是说圆螺母和与之螺纹配合的零件之间的相互作用力在周向上更加均衡,自锁防松效果更好。
[0025]
以上仅为本实用新型的一个具体实施例,但本实用新型的设计构思并不局限于此,凡利用本实用新型的构思对本实用新型做出的非实质性修改,均落入本实用新型的保
护范围之内。