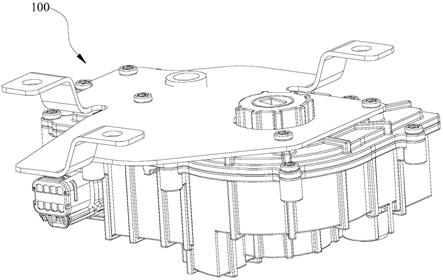
1.本实用新型属于汽车自动变速器换挡控制技术领域,尤其涉及线控换挡执行器。
背景技术:2.随着电子科技和汽车行业的高速发展,汽车电子化已经是大势所趋,其中汽车换挡信号采用电信号通过can总线进行传输的方式也是发展的趋势所在,这就要求汽车换挡器和换挡执行器之间不能再采用传统式的通过机械拉索软轴连接的方式。而且传统式的拉索软轴需穿过整车的相关区域来实现汽车换挡器与换挡执行器之间的连接,对空间区域有一定要求。同时传统的拉索软轴控制方式,需要将换挡器的体积做的比较大,以至于提供足够大的换挡力及换挡行程。拉索软轴控制方式便会带来以下的缺点:(1)占用布置空间;(2)需要在车身上穿孔,降低了密封性能;(3)为了匹配变速器的力与行程,换挡器需要做成比较大体积的形状;(4)拉索软轴由于本身的特性,会有摩擦力、间隙产生,影响操作手感;(5)变速器产生的振动,会通过拉索软轴、换挡器传递给驾驶员,影响舒适性。
3.为解决上述问题,急需研制一种无需采用机械拉索软轴连接的换挡执行器。
技术实现要素:4.为了克服现有技术的不足,本实用新型的目的在于提供线控换挡执行器,包括齿轮箱体、用于与变速箱双d轴连接的连接轴、电机、用于将电机转动的动力传动至连接轴的行星齿轮传动结构以及换挡检测结构,行星齿轮传动结构包括固定设置于电机输出轴上的蜗杆、与蜗杆啮合的斜齿轮、固定设置于斜齿轮圆心处的太阳轮、若干与太阳轮啮合的行星齿轮以及内侧齿牙与若干行星齿轮啮合的内齿圈,连接轴底部对应行星齿轮的圆心处设有销轴,行星齿轮装配于销轴。本方案通过上述设置,可实现独立于自动变速器之外,在针对不同的车型,只需要保证自动变速器与本方案中的线控换挡执行器连接即可,能够实现汽车换挡执行器的平台化设计,同时换挡器与执行器之间无机械连接,节约了整车布置空间。
5.本实用新型的目的采用如下技术方案实现:
6.线控换挡执行器,包括齿轮箱体、用于与变速箱双d轴连接的连接轴、电机、用于将所述电机转动的动力传动至所述连接轴的行星齿轮传动结构以及换挡检测结构,所述行星齿轮传动结构包括固定设置于所述电机输出轴上的蜗杆、与所述蜗杆啮合的斜齿轮、固定设置于所述斜齿轮圆心处的太阳轮、若干与所述太阳轮啮合的行星齿轮以及内侧齿牙与若干所述行星齿轮啮合的内齿圈,所述连接轴底部对应所述行星齿轮的圆心处设有销轴,所述行星齿轮装配于所述销轴。
7.进一步地,所述内齿圈的外侧壁上设有若干用于防止所述内齿圈周向转动的凸出部,所述内齿圈通过所述凸出部卡固于所述齿轮箱体内。
8.进一步地,所述蜗杆的导程角大于所述蜗杆齿面与斜齿轮齿面之间的当量摩擦角,所述行星齿轮采用直齿圆柱齿轮。
9.进一步地,所述换挡检测结构包括与所述连接轴同轴设置且位于所述行星齿轮传
动结构底部的磁铁支架,嵌套设置于所述磁铁支架的磁铁、固定于所述齿轮箱体内的旋转支架以及与所述电机电性连接的控制主板,所述磁铁支架通过无油轴承可转动的嵌套设置于所述旋转支架内,所述连接轴还设有用于与所述磁铁支架连接的芯轴,所述芯轴一端与所述连接轴过盈连接,另一端穿过太阳轮中心孔与所述磁铁支架过盈连接以实现连接轴和磁铁支架同步转动。
10.进一步地,所述控制主板包括用于检测磁铁所在位置的芯片以及用于与换挡控制器连接的插头。
11.进一步地,所述磁铁采用湿式铁氧体永磁材料制成,且充磁方向为径向充磁。
12.进一步地,所述磁铁支架的底部设有两沿着轴向突出的凸块,两所述凸块环绕着所述磁铁支架的圆心间隔设置,所述旋转支架的内侧壁沿径向突出有限位块,安装时,所述限位块位于两所述凸块中间以实现限制所述磁铁支架的转动。
13.进一步地,齿轮箱体包括下壳体以及齿轮箱盖,所述连接轴、电机、控制主板以及行星齿轮传动结构均设置于所述下壳体内,所述下壳体对应所述插头设有电源插头位;所述下壳体设有透气孔,所述透气孔设有透气塞。
14.进一步地,所述连接轴通过第二含油轴承与所述齿轮箱盖配合,所述连接轴与所述第二含油轴承之间设有用于防水的o型圈。
15.进一步地,所述下壳体设有用于定位所述齿轮箱盖的十字定位柱,所述下壳体和齿轮箱盖通过螺钉连接,所述下壳体和齿轮箱盖的连接处设置有用于防水的密封圈。
16.相比现有技术,本实用新型的有益效果在于:
17.本实用新型的线控换挡执行器,包括齿轮箱体、用于与变速箱双d轴连接的连接轴、电机、用于将电机转动的动力传动至连接轴的行星齿轮传动结构以及换挡检测结构,行星齿轮传动结构包括固定设置于电机输出轴上的蜗杆、与蜗杆啮合的斜齿轮、固定设置于斜齿轮圆心处的太阳轮、若干与太阳轮啮合的行星齿轮以及内侧齿牙与若干行星齿轮啮合的内齿圈,连接轴底部对应行星齿轮的圆心处设有销轴,行星齿轮装配于销轴。本方案通过上述设置,可实现独立于自动变速器之外,在针对不同的车型,只需要保证自动变速器与本方案中的线控换挡执行器连接即可,能够实现汽车换挡执行器的平台化设计,同时换挡器与执行器之间无机械连接,节约了整车布置空间。
附图说明
18.图1是本实用新型线控换挡执行器优选实施方式的结构示意图;
19.图2是本实用新型线控换挡执行器优选实施方式的实际应用示意图;
20.图3是本实用新型线控换挡执行器优选实施方式的爆炸视图;
21.图4是本实用新型线控换挡执行器沿连接轴轴向的剖视图;
22.图5是本实用新型下壳体优选实施方式的结构示意图;
23.图6是本实用新型下壳体优选实施方式另一视角的结构示意图;
24.图7是本实用新型连接轴优选实施方式的结构示意图;
25.图8是本实用新型内齿圈优选实施方式的结构示意图;
26.图9是本实用新型磁铁支架优选实施方式的结构示意图;
27.图10是本实用新型磁铁支架优选实施方式另一视角的结构示意图;
28.图11是本实用新型旋转支架优选实施方式的结构示意图。
29.图中:100、线控换挡执行器;1、齿轮箱体;11、下壳体;111、电源插头位;112、透气孔;113、十字定位柱;114、透气塞;12、齿轮箱盖;13、密封圈;2、连接轴;21、销轴;22、第二含油轴承;23、o型圈;3、电机;31、电机支架;311、peek垫片;312、橡胶柱;313、第一含油轴承;4、行星齿轮传动结构;41、蜗杆;42、斜齿轮;43、太阳轮;44、行星齿轮;45、内齿圈;451、凸出部;5、换挡检测结构;51、磁铁支架;511、凸块;512、磁铁槽位;513、透气槽位;514、油槽;52、磁铁;53、旋转支架;531、限位块;532、固定凸起;54、无油轴承;55、控制主板;551、芯片;552、插头;6、芯轴;7、支架;8、双d轴。
具体实施方式
30.下面,结合附图以及具体实施方式,对本实用新型做进一步描述,需要说明的是,在不相冲突的前提下,以下描述的各实施例之间或各技术特征之间可以任意组合形成新的实施例。
31.本实用新型线控换挡执行器100如图1
‑
图11所示,包括齿轮箱体1、用于与变速箱双d轴8连接的连接轴2、电机3、与电机3电性连接的控制主板55以及用于将电机3转动的动力传动至连接轴2的行星齿轮传动结构4,行星齿轮传动结构4包括固定设置于电机3输出轴上的蜗杆41、与蜗杆41啮合的斜齿轮42、固定设置于斜齿轮42圆心处的太阳轮43、若干与太阳轮43啮合的行星齿轮44以及内侧齿牙与若干行星齿轮44啮合的内齿圈45,连接轴2底部对应行星齿轮44的圆心处设有销轴21,行星齿轮44装配于销轴21。本方案通过上述设置,可实现线控换挡执行器100独立于自动变速器之外,在针对不同的车型,只需要保证自动变速器与本方案中的线控换挡执行器100连接即可,能够实现汽车换挡执行器的平台化设计,同时换挡器与执行器之间无机械连接,节约了整车布置空间。
32.优选的,为了消除电机3的轴向窜动,本实施例中还设置了固定设置于齿轮箱体1内的电机支架31,在电机支架31中装有peek垫片311和橡胶柱312;其中peek垫片311主要解决耐磨性问题,橡胶柱312提供可变性压缩,且橡胶柱312采用耐高温橡胶材料制作。同时电机支架31位于电机3的输出轴处设有用于支撑电机3输出轴的第一含油轴承313。
33.本实施例中的换挡流程为(如图2):驾驶员操作换挡器将换挡意图通过电信号传输给换挡控制器,换挡控制器将上述信号转换为控制信号并发送给该换挡执行器中的控制主板55,控制主板55经过分析判断将上述控制信号转换为电信号发送给该换挡执行器中的电机3,控制电机3的正反转,从而驱动该换挡执行器中的其它传动部件,最终将动力通过连接轴2传递给变速箱的tcu双d轴8,实现换挡的过程。
34.其中具体传动过程为:换挡执行器的动力由电机3输入,动力首先由电机3输出轴传输到蜗杆41上;通过蜗杆41与斜齿轮42的一级传动将电机3的动力传到执行器的输入端,蜗杆41带动斜齿轮42转动,与斜齿轮42固定的所述太阳轮43也绕着斜齿轮42的轴线同步转动;在太阳轮43与内齿圈45的共同作用下,若干行星齿轮44均绕太阳轮43轴线旋转同时行星齿轮44还绕着自身轴线旋转,若干行星齿轮44带动连接轴2绕自身轴线旋转,将动力传输到自动变速箱的tcu双d轴8,驱动自动变速箱换挡。
35.优选的,本实施例中的斜齿轮42采用工程塑料注塑成型,且太阳轮43和斜齿轮42一体注塑成型。
36.本实施例中行星齿轮传动结构4的二级传动是由太阳轮43、行星齿轮44和内齿圈45组成,是通过三者的协同运作才实现驱使连接轴2绕自身轴线旋转,在该传动过程中,若内齿圈45也是可转动的设置于齿轮箱体1内,则当行星齿轮44在太阳轮43的带动下仅会发生自转,同时行星齿轮44的自转还会带动内齿圈45的转动,在该种情况下行星齿轮44便无法带动连接轴2发生转动。因此,本实施例中在所述内齿圈45的外侧壁上设有若干用于防止所述内齿圈45周向转动的凸出部451,所述内齿圈45通过所述凸出部451卡固于所述齿轮箱体1内。即是内齿圈45在安装到齿轮箱体1后便固定设置在箱体上,行星齿轮44在自转的过程中便同时沿着内齿圈45旋转带动整个连接轴2绕着自身轴线发生转动。
37.本实施例中采用两级齿轮传动,第一级为蜗杆41斜齿轮42传动,第二级为行星齿轮44结构传动,其中所述蜗杆41为双头大导程角蜗杆41(导程角大于蜗杆齿面与斜齿轮齿面之间的当量摩擦角),所述行星齿轮44采用直齿圆柱齿轮。通过上述两者的设置均能实现非自锁功能。
38.本实施例中,蜗杆41参数如下:模数1mm,齿数为2,压力角14.5
°
,导程角15
°
,变位系数为
‑
0.5,齿顶圆直径为10.979mm,齿根圆直径为5.784mm,齿厚1.312mm。斜齿轮42参数如下:模数1mm,齿数为54,压力角14.5
°
,螺旋角13.617
°
,变位系数为1.0795,齿顶圆直径为57.373mm,齿根圆直径为51.830mm,齿厚2.129mm。太阳轮43参数如下:模数1.1mm,齿数为11,压力角20
°
,变位系数为0.6306,齿顶圆直径为15.217mm,齿根圆直径为10.737mm,齿厚2.233mm。行星齿轮44参数如下:模数1.1mm,齿数为21,压力角20
°
,变位系数为0.6288,齿顶圆直径为26.213mm,齿根圆直径为21.513mm,齿厚2.231mm。内齿圈45参数如下:模数1.1mm,齿数为55,压力角20
°
,变位系数为0.6748,齿顶圆直径为59.784mm,齿根圆直径为64.734mm,齿厚1.188mm。
39.本实施例中的所述换挡检测结构5包括与所述连接轴2同轴设置且设置于所述行星齿轮传动结构4底部的磁铁支架51,嵌套设置于所述磁铁支架51的磁铁52、固定于所述齿轮箱体1内的旋转支架53以及与所述电机3电性连接的控制主板55,所述磁铁支架51通过无油轴承54可转动的嵌套设置于所述旋转支架53内,其中所述连接轴2还设有用于与所述磁铁支架51连接的芯轴6,芯轴6两端切削成扁平状,所述芯轴6一端与所述连接轴2过盈连接,另一端穿过太阳轮43中心孔与所述磁铁支架51过盈连接以实现连接轴2和磁铁支架51同步转动。
40.优选的,本实施例中的磁铁支架51的底部端面上设置有磁铁槽位512,磁铁52通过3m胶过盈压入磁铁槽位512中,其中具有耐高温性能。除此之外环绕着磁铁槽位512的四周设置还有若干透气槽位513,以方便磁铁52压装。同时磁铁支架51顶端面还设置有若干油槽514,若干油槽514环绕着顶端面的圆心环形间隔设置,油槽514内涂有润滑脂,以减小磁铁支架51与斜齿轮42之间的摩擦。
41.优选的,所述磁铁52采用湿式铁氧体永磁材料制成,且充磁方向为径向充磁。且所述控制主板55包括用于检测磁铁52所在位置的芯片551以及用于与换挡控制器55连接的插头552。通过上述的设置,当行星齿轮传动结构4带动连接轴2转动后,其下方的磁铁支架51也会随之同步转动,此时磁铁支架51上的磁铁52在发生转动后,其磁感线方向也发生改变,芯片551通过检测磁铁52的磁感线方向便能够检测此时换挡执行器的档位位置。同时控制主板55也与电机3电性连接,能够传递电信号至电机3控制电机3的正反转。以此实现信号的
线性变化检测,换挡检测精度高,可控性好。
42.本实施例中的所述磁铁支架51的底部设有两沿着轴向突出的凸块511,两所述凸块511环绕着所述磁铁支架51的圆心间隔设置,所述旋转支架53的内侧壁沿径向突出有限位块531,安装时,磁铁支架51可转动的嵌套旋转支架53内侧,且所述限位块531位于两所述凸块511中间以实现限制所述磁铁支架51的转动。以此保证磁铁支架51在正确的角度范围内旋转。
43.同样的,为了防止旋转支架53在齿轮箱体1内发生转动,本实施例中在旋转支架53的外侧壁上设置了若干固定凸起532,通过若干固定凸起532和齿轮箱体1内的槽位配合以此限制旋转支架53转动。
44.本方案中齿轮箱体1包括下壳体11以及齿轮箱盖12,所述连接轴2、电机3、控制主板55以及行星齿轮传动结构4均设置于所述下壳体11内,所述下壳体11对应所述插头552设有电源插头位111,通过该设置使得插头552能够漏出在箱体外部,换挡控制器能够直接连接到插头552。所述下壳体11设有透气孔112,所述透气孔112设有透气塞114。
45.优选的,所述下壳体11设有用于定位所述齿轮箱盖12的十字定位柱113,所述下壳体11和齿轮箱盖12通过螺钉连接,使得两者的安装更加快捷牢固。同时所述下壳体11和齿轮箱盖12的连接处设置有用于防水的密封圈13,密封圈13具体结构形式依据下壳体11和齿轮箱盖12的配合边界结构确定。
46.优选的,所述连接轴2通过第二含油轴承22与所述齿轮箱盖12配合,使得减小连接轴2和齿轮箱盖12之间的摩擦。所述连接轴2与所述第二含油轴承22之间设有用于防水的o型圈23。连接轴2的顶部对应所述o型圈23设有环状o型圈23槽位,o型圈23装入o型圈23槽位中,并与第二含油轴承22过盈配合。其中密封圈13和o型圈23均采用耐高温橡胶材料制成,使得连接更加紧密牢固,防水性能佳。
47.本方案的线控换挡执行器100是独立于自动变速箱之外,但是为了信号线的接通方便,两者安装位置不会相差太远。对此,本实施例中还设置用于连接自动变速箱的支架7。支架7固定设置在齿轮箱盖12上;同时支架7上设置有螺栓孔位,用于支架7与自动变速箱之间的紧固连接。
48.本实用新型的上述实施例并不是对本实用新型保护范围的限定,本实用新型的实施方式不限于此,凡此种种根据本实用新型的上述内容,按照本领域的普通技术知识和惯用手段,在不脱离本实用新型上述基本技术思想前提下,对本实用新型上述结构做出的其它多种形式的修改、替换或变更,均应落在本实用新型的保护范围之内。