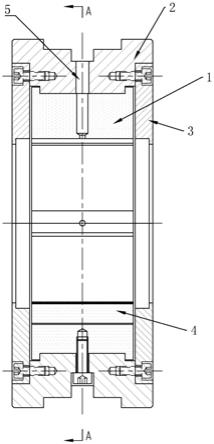
1.本实用新型属于可倾瓦轴承技术领域,特指一种径向轴承。
背景技术:2.可倾瓦轴承通常由3~5个或更多个能在支点上自由倾斜的弧形瓦块组成,所以又叫活支多瓦形支持轴承,也叫摆动轴瓦式轴承。由于其瓦块能随着转速、载荷及轴承温度的不同而自由摆动,在轴颈周围形成多油楔。且各个油膜压力总是指向中心,具有较高的稳定性。
3.然而由于传统的可倾瓦轴承的减振效果不理想,从而降低了轴承整体的使用寿命。
技术实现要素:4.针对现有技术存在的不足,本实用新型的目的在于提供一种结构简单且减振效果良好的径向可倾瓦轴承。
5.为实现上述目的,本实用新型提供了如下技术方案:一种径向轴承,包括径向瓦块体;在径向瓦块体的外侧设置有轴承壳体,在轴承壳体的两端设置有用于控制泄油量的端盖,在所述的径向瓦块体的内侧一体成型有若干按圆周均匀分布可倾瓦块,且在可倾瓦块与径向瓦块体之间阻尼减振结构;并在所述轴承壳体的外壁上设置有若干按圆周均匀分布且贯穿至径向瓦块体内侧的注油孔。
6.通过采用上述的技术方案,在可倾瓦块与径向瓦块体设置阻尼减振结构,从而能起到良好的减振的效果,以确保轴承的使用寿命。
7.本实用新型进一步设置为:所述的径向瓦块体有若干个按圆周均匀分布的轴承块拼接而成,每个所述的轴承块均通过若干紧固螺栓与轴承壳体固定连接,且相邻的轴承块间形成有间隙。
8.通过采用上述的技术方案,径向瓦块体径向瓦块体有若干个按圆周均匀分布的轴承块拼接而成,一旦某个瓦块损坏,可仅更换损坏瓦块,无需更换整个轴承,可大幅节约成本。
9.本实用新型进一步设置为:每个所述的轴承块上均形成有一个可倾瓦块,且每个所述的轴承块上均带有贯穿至其内侧的注油孔。
10.通过采用上述的技术方案,每个轴承块上均形成有一个可倾瓦块,且每个所述的轴承块上均带有贯穿至其内侧的注油孔,使得各个轴承块的结构统一,具备良好的工艺性和互换性。
11.本实用新型进一步设置为:所述的阻尼减振结构为贯穿轴承块的槽状结构,包括自可倾瓦块径向的两侧向可倾瓦块中部延伸的第一阻尼减振槽、及设置在两个第一阻尼减振槽之间的第二阻尼减振槽,所述的第一阻尼减振槽及第二阻尼减振槽均不切断可倾瓦块与轴承块之间一体成型的连接关系。
12.通过采用上述的技术方案,通过两个尼减振槽的设置能确保阻尼减振结构整体的减振效果。
13.本实用新型进一步设置为:所述的第一阻尼减振槽包括从轴承块内侧端切入的第一槽部、与第一槽部连接的且沿径向向可倾瓦块中部延伸的第二槽部及设置在第二槽部的一侧且向轴承块外侧面方向延伸的呈s状的第三槽部,所述的第二槽部与第三槽部的连接处形成有承接部,且轴承块其中一侧的第一槽部与间隙重合。
14.通过采用上述的技术方案,在第一槽部、第二槽部及第三槽部的配合下,使轴承整体具有自动调整性能。
15.本实用新型进一步设置为:所述的第二阻尼减振槽包括与第一槽部同轴设置的第四槽部及设置在靠近第四槽部两侧并向承接部延伸且呈钩状的第五槽部,并在第四槽部的两侧设置有向轴承块内侧面方向延伸的延伸部。
16.通过采用上述的技术方案,在第一槽部、第二槽部及第三槽部、第四槽部、第五槽部及延伸部的配合下,使轴承整体不仅具有自动调整性能,还具有优异的减振性能。
附图说明
17.图1是本实用新型的结构示意图;
18.图2是图1中a
‑
a处的剖视图;
19.图3只图2中ⅰ处的局部放大图;
20.附图中标记及相应的部件名称:1
‑
径向瓦块体、1a
‑
轴承块、2
‑
轴承壳体、3
‑
端盖、4
‑
可倾瓦块、5
‑
注油孔、6
‑
间隙、7
‑
第一阻尼减振槽、7a
‑
第一槽部、7b
‑
第二槽部、7c
‑
第三槽部、8
‑
第二阻尼减振槽、8a
‑
第四槽部、8b
‑
第五槽部、9
‑
承接部、10
‑
延伸部。
具体实施方式
21.参照图1至图3对本实用新型的一个实施例做进一步说明。
22.一种径向轴承,包括径向瓦块体1;在径向瓦块体1的外侧设置有轴承壳体2,在轴承壳体2的两侧设置有用于控制泄油量的端盖3,在所述的径向瓦块体1的内侧一体成型有若干按圆周均匀分布可倾瓦块4,且在可倾瓦块4与径向瓦块体1之间阻尼减振结构;并在所述轴承壳体2的外壁上设置有若干按圆周均匀分布且贯穿至径向瓦块体1内侧的注油孔5。
23.通过在可倾瓦块4与径向瓦块体1设置阻尼减振结构,从而能起到良好的减振的效果,以确保轴承的使用寿命。
24.进一步:所述的径向瓦块体1有若干个按圆周均匀分布的轴承块1a拼接而成,每个所述的轴承块1a均通过若干紧固螺栓与轴承壳体2固定连接,且相邻的轴承块1a间形成有间隙6。
25.通过径向瓦块体1径向瓦块体1有若干个按圆周均匀分布的轴承块1a拼接而成,一旦某个瓦块损坏,可仅更换损坏瓦块,无需更换整个轴承,可大幅节约成本。
26.进一步:每个所述的轴承块1a上均形成有一个可倾瓦块4,且每个所述的轴承块1a上均带有贯穿至其内侧的注油孔5。
27.通过每个轴承块1a上均形成有一个可倾瓦块4,且每个所述的轴承块1a上均带有贯穿至其内侧的注油孔5,使得各个轴承块1a的结构统一,具备良好的工艺性和互换性。
28.进一:所述的阻尼减振结构为贯穿轴承块1a的槽状结构,包括自可倾瓦块4径向的两侧向可倾瓦块4中部延伸的第一阻尼减振槽7、及设置在两个阻尼减振槽之间的第二阻尼减振槽8,所述的第一阻尼减振槽7及第二阻尼减振槽8均不切断可倾瓦块4与轴承块1a之间一体成型的连接关系。
29.通过两个尼减振槽的设置能确保阻尼减振结构整体的减振效果。
30.进一步:所述的第一阻尼减振槽7包括从轴承块1a内侧端切入的第一槽部7a、与第一槽部7a连接的且沿径向向可倾瓦块4中部延伸的第二槽部7b及设置在第二槽部7b的一侧且向轴承块1a外侧面方向延伸的呈s状的第三槽部7c,所述的第二槽部7b与第三槽部7c的连接处形成有承接部9,且轴承块1a其中一侧的第一槽部7a与间隙6重合。
31.通过采用上述的技术方案,在第一槽部7a、第二槽部7b及第三槽部7c的配合下,使轴承整体具有自动调整性能。
32.进一步:所述的第二阻尼减振槽8包括与第一槽部7a同轴设置的第四槽部8a及设置在靠近第四槽部8a两侧并向承接部9延伸且呈钩状的第五槽部8b,并在第四槽部8a的两侧设置有向轴承块1a内侧面方向延伸的延伸部10。
33.通过在第一槽部7a、第二槽部7b及第三槽部7c、第四槽部8a、第五槽部8b及延伸部10的配合下,使轴承整体不仅具有自动调整性能,还具有优异的减振性能。
34.上述实施例仅为本实用新型的较佳实施例,并非依此限制本实用新型的保护范围,故:凡依本实用新型的结构、形状、原理所做的等效变化,均应涵盖于本实用新型的保护范围之内。