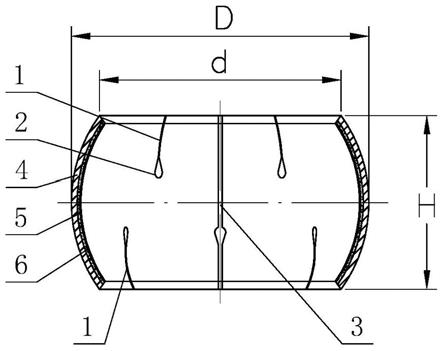
1.本发明涉及滑动轴承,尤其是一种鼓状形的无油润滑轴承及制造方法。
背景技术:2.通常的无油润滑轴承为圆环形的轴套,但对于一些球型关键上用的无油润滑的滑动轴承,现有的常规做法是根据球面滑动轴承的规格用复合材料的板材,下料成扇形的配料,再卷制成带开口缝的圆台形,再冲压、整形加工成有拼接缝的半球面滑动轴承,这种球面滑动轴承尺寸精度不高,材料利用率低。也有用复合材料的板材下料成圆环形的无油润滑轴承的坯料,再在冲床上加工成碗状形的(半圆球形)无油润滑轴承,如专利cn200710156848.3无接缝球面滑动复合轴承及其制造方法。以上这些滑动轴承都是先制成两个半圆球形,在使用时,需要将两件碗状形的(半圆球形)无油润滑轴承对合,而组成两端有孔的球型无油润滑轴承,这些传统结构的加工方法,虽然使用比较方便,但缺点是必须要有两件半圆球形的无油润滑轴承组合而成,它们的共同缺点都是整体性差,而且在摩擦副表面还经常需要添加润滑油脂,使用寿命较短,维护也很麻烦。
技术实现要素:3.本发明的目的在于提供一种整体性好、安装和维护方便,使用寿命长,制作成本低的一种鼓状形的无油润滑轴承及制造方法。
4.为了达到上述目的,本发明所采用的技术方案是:其特征它是一上下两端内缩的球形滑动轴承,在所述两端内缩的位置上,分别开有6
‑
8条均匀分布的收缩槽,上下两端的收缩槽相互错开,且每条收缩槽的末端不超过滑动轴承高度的1/2位置,在滑动轴承的外表面设有拼接缝,滑动轴承的外表面为钢材基层,在钢材基层的内表面上烧结一铜粉层,在铜粉层上附着烧结有一层聚甲醛或改性聚甲醛层。
5.所述收缩槽的末端设有圆弧。
6.所述钢材基层的厚度为1.80
‑
1.90毫米。
7.所述铜粉层的厚度为0.3毫米。
8.所述聚甲醛或改性聚甲醛层的厚度为0.20
‑
0.30毫米。
9.所述的拼接缝为其中一条收缩槽的延伸。
10.所述的改性聚甲醛层为聚甲醛与纤维的混合物层。
11.鼓状形的无油润滑轴承的制造方法:其特征依次是以下步骤:(1)制作复合板材:根据需要以常规方法制作出钢材基层——铜粉层——聚甲醛或改性聚甲醛层的复合材料的板材;(2)根据鼓状形的无油润滑轴承的外径d、小端外径d和高度h,计算出直桶形滑动轴承的展开长度l=πd和高度h=(πd/180)sinh/d;(3)根据收缩槽的数量和鼓状形的无油润滑轴承小口端的直径d,计算每一条v形收缩槽上口宽的尺寸s,所述s的计算方法:根据无油润滑轴承的直径d和无油润滑轴承小端
外径d,计算出它们的圆周长差再除以一端的收缩槽条数k,求得v形收缩槽上口宽的尺寸s,即s=(d
‑
d)π/k;(4)根据展开长度l和高度h,裁切直桶形滑动轴承的坯料;(5)根据每一条v形收缩槽的几何尺寸,冲制出坯料两端的各v形收缩槽;(6)将直桶形滑动轴承的坯料卷圆,形成直桶形的滑动轴承;(7)将直桶形的滑动轴承放入成形模具中加压,使各v形收缩槽两侧的材料向内弯曲,各收缩槽合拢、成鼓形,脱模后,制成成品。
12.所述的步骤(4)和(5)合并,在直桶形滑动轴承的坯料裁切时,将坯料的长度l、高度h和各v形收缩槽一起冲制出。
13.根据上述技术方案设计的一种鼓状形的无油润滑轴承及制造方法,在制造中先根据滑动轴承的尺寸和要求以钢板或钢带为基材,在基材表面烧结一铜粉层,在铜粉层上附着烧结有一层聚甲醛(pom)或改性聚甲醛材料的复合材料板材,pom强度、刚度高,弹性好,减磨、耐磨性好。其力学性能优异,比强度可达50.5mpa,比刚度可达2650mpa,与金属十分接近。经落料、卷圆、成形制成每端具有6
‑
8条带有圆弧收缩槽的鼓状形无油润滑轴承。它具有结构新颖、整体新好,安装和维护方便,使用更耐久。特殊的鼓状形使它能实现将需要组合使用的两件碗状形轴承变为一件鼓状形轴承的优点。产品在使用时也无需经常加注润滑油或润滑油脂。该产品主要应用于旋转和摇摆运动的摩擦副中,高度、长度等调节的机构中。
附图说明
14.图1是鼓状形无油润滑轴承的主视图;图2是图1的俯视图;图3是钢基材表面烧结铜粉层并附着聚甲醛或改性聚甲醛层材料的复合板材剖视图;图4是鼓状形无油润滑轴承的展开图;图5是用图4材料卷制成有12条带有圆弧收缩槽的直桶滑动轴承主视图;图6是图5的俯视图。
15.图中:1、收缩槽;2、圆弧;3、拼接缝;4、钢材基层;5、铜粉层;6、聚甲醛或改性聚甲醛层。
具体实施方式
16.下面结合附图和具体实施例对本发明作进一步的描述。
17.图1、图2是鼓状形的无油润滑轴承的结构图。从图中看出它是一上下两端内缩的球形滑动轴承,在所述两端内缩的位置上,分别开有6条均匀分布的收缩槽1,为了减小收缩槽1末端的应力集中、加强冲制收缩槽1末端的冲模强度和便于成形,在收缩槽1的末端制有圆弧2,并使上端的收缩槽1与下两端的收缩槽1相互错开,且收缩槽1的末端不超过滑动轴承高度h的1/2位置,在滑动轴承的外表面设有拼接缝3,所述的拼接缝3为其中一条收缩槽1的延伸。滑动轴承的外表面为钢材基层4,钢材基层4的厚度为1.80
‑
1.90毫米,在钢材基层4的内表面上烧结一铜粉层5,铜粉层5的厚度为0.3毫米,在铜粉层5上附着烧结有一层聚甲醛或改性聚甲醛层6,所述的改性聚甲醛层为聚甲醛与纤维的混合物层,聚甲醛或改性聚甲
醛层6的厚度为0.20
‑
0.30毫米。
18.所述鼓状形的无油润滑轴承的制造方法依次是:(1)制作复合板材:根据需要以常规方法制作出钢材基层4——铜粉层5——聚甲醛或改性聚甲醛层6的三层复合材料的板材如图3所示;(2)根据鼓状形的无油润滑轴承的外径d、小端外径d和高度h,计算出直桶形滑动轴承的展开长度l=πd和高度h=(πd/180)sinh/d;(3)根据收缩槽1的数量和鼓状形的无油润滑轴承小口端的直径d,计算每一条v形收缩槽1上口宽的尺寸s,收缩槽1的长度b小于h/2,所述s的计算方法:根据无油润滑轴承的直径d和无油润滑轴承小端直径d,计算出它们的圆周长差,再除以一端的收缩槽1的条数k,求得v形收缩槽1上口宽的尺寸s,即s=(d
‑
d)π/k;(4)根据展开长度l和高度h,裁切直桶形滑动轴承的坯料;(5)根据每一条v形收缩槽的几何尺寸,冲制出坯料两端的各v形收缩槽1如图4所示;(6)将直桶形滑动轴承的坯料卷圆,形成直桶形的滑动轴承如图5、图6所示;(7)将直桶形的滑动轴承放入成形模具中加压,使各v形收缩槽1两侧的材料向内弯曲,各收缩槽合拢、成鼓形,脱模后,制成成品如图1、图2所示。
19.对于以上方法也可以将步骤(4)和(5)合并,在直桶形滑动轴承的坯料裁切时,将坯料的长度l、高度h和各v形收缩槽1一起冲制出如图4所示。在制作试模时,由于材料的厚度、刚度等因素,s、l、h等的实际尺寸,还需要根据实际的试模结果进行适当的调整。
20.当然,以上所举的例子仅为本发明的较佳实施例而已,但并不限定本发明实施的范围。凡依本技术范围所作的均等变化与修饰仍属本发明所涵盖的保护范围。