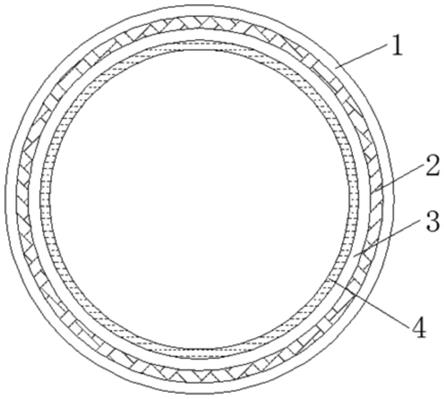
1.本发明涉及防腐蚀管道技术领域,具体涉及一种可防腐耐化学性软管。本发明的可防腐耐化学性软管主要应用在应急救援、工矿排水、农用拖拽输水/粪和野外输送含化学物质液体等场景,相对应于硬质管线来说,本发明的软管铺设和收卷、储存方便,软管主要应用在环境多变的场合中,其耐腐蚀性好,并可应用于管道修复。
背景技术:2.目前输送耐腐蚀性流体一般采用的是金属管道或硬质管道,但金属或硬质管道相对重量比较重,在管道铺设上难度较大,并且只适合短距离的安装,同时属或硬质管道的施工也比较复杂,工期较长。因此,需要采用具备耐腐蚀性的软管进行长距离的铺设,软管的施工周期短且铺设简单,易于操作。
3.然而,现有的软管生产工艺,一般是采用涤纶工业丝作为编织增强层,其内胶层和外胶层分别作为防渗漏层和耐磨保护层。内胶层作为防渗漏层通常不具备耐腐蚀性能,若要内胶层满足耐腐蚀功能,则使得成本较高;并且通过现有的技术使内胶层具备耐腐蚀功能时,还会导致内胶层与编织增强层的粘连存在困难。
技术实现要素:4.针对现有软管生产工艺中存在的内胶层不满足耐腐蚀功能,如若要内胶层满足耐腐蚀功能则会导致生产成本升高,还会导致内胶层与编织增强层之间的粘连存在一定的困难,上述的缺陷会导致现有的防腐软管存在生产成本高以及软管中功能层之间存在粘接困难等问题;针对上述的缺陷和不足,本发明提供了一种可防腐耐化学性软管,本发明所提供的可防腐耐化学性软管其成本低,且防腐蚀性好,同时还不影响管内各功能层之间的粘连。
5.本发明是通过如下技术方案实现的:
6.一种可防腐耐化学性软管,其特征在于,所述的软管由外向内依次包括外胶层,编织增强层,内胶层和耐高温、耐腐蚀特种涂层;所述的耐高温、耐腐蚀特种涂层包括如下重量份的组分:乙烯基树脂100份、功能性填料10
‑
20份、促进剂0.5
‑
1份和助剂4
‑
8份。
7.具体的,所述的功能性填料的加入可以增加耐高温、耐腐蚀特种涂层的亲和力和柔韧性,同时还有助于提升耐高温、耐腐蚀特种涂层与内胶层之间的粘连效果。具体的,本发明所提供的可防腐耐化学性软管的设计思路是通过在原有软管内部增加一层耐高温、耐腐蚀的特种涂层,并通过对特种涂层的配方优选,使得该涂层具备优异的耐腐蚀性能;本发明的工艺并不需要内胶层具备耐腐蚀功能,因此解决了现有技术所面临的:若要内胶层满足耐腐蚀功能时,则会导致生产成本较高以及会使得内胶层与编织增强层之间粘连存在困难的难题。将本发明的可防腐耐化学性软管用于输送具有腐蚀性的流体介质时,通过管内设置的耐高温、耐腐蚀特种涂层即可实现对腐蚀性流体的介质安全输送,有效保护软管不被腐蚀;并且经过长期的使用证明本发明的可防腐耐化学性软管经久耐用,防腐性能优异;同时由于管内设置的耐高温、耐腐蚀特种涂层还进一步提升了整个软管的耐高温性能。
8.本发明的可防腐耐化学性软管通过选用耐高温、耐腐蚀的乙烯基树脂与其它功能性填料(水性pu)、促进剂以及助剂(聚硅氧烷)等组分,并严格控制各组分之间的比例调配,从而配置出厚膜型复合物作为软管内部的耐高温、耐腐蚀特种涂层;本发明通过对耐高温、耐腐蚀特种涂层的配方调配使得涂层均匀、光滑,可降低远距离输送的压力损失,柔韧性好,环保经济,选配适合不同救援或应用场所,扩大使用范围,成为多功能多用途的特种产品,有效提高了产品价值。本发明软管中设置的耐高温、耐腐蚀特种涂层通过对配方和配方比例的优选,使得该涂层不仅满足耐高温和耐腐蚀的功能,还使得该涂层与原有管道中的内胶层具备较强的粘接能力。
9.进一步的,所述的耐高温、耐腐蚀特种涂层包括如下重量份的组分:乙烯基树脂100份、功能性填料15
‑
20份、促进剂0.5
‑
0.8份和助剂5
‑
7份。
10.进一步的,所述耐高温、耐腐蚀特种涂层包括如下重量份的组分:乙烯基树脂100份、功能性填料15份、促进剂0.6份和助剂6份。
11.进一步的,所述的功能性填料为水性pu。该功能性填料的引入能够增加涂层的粘连效果以及柔韧性。
12.进一步的,所述的促进剂选自异辛酸钴。本发明所用的促进剂为低钴环保型异辛酸钴促进剂。
13.进一步的,所述的助剂为聚硅氧烷。
14.进一步的,所述的耐高温、耐腐蚀特种涂层的厚度为650
‑
850μm。优选的,将所述耐高温、耐腐蚀特种涂层的厚度设置为650
‑
850μm,在此厚度范围内即能充分保证耐高温和防腐性能,同时又能满足对生产成本的控制。
15.一种可防腐耐化学性软管的制备方法,其特征在于,该方法包括如下步骤:具体的,本发明的可防腐耐化学性软管的制备方法,是在原有软管的基础之上再复合一层耐高温、耐腐蚀的特种涂层,具体是将耐高温、耐腐蚀的特种涂层粘连在内胶层的内壁上,从而形成本发明的可防腐耐化学性软管;其具体的生产工艺如下(这里原有的软管生产工艺不做赘述,直接用现成的原有软管即可):
16.s1、按重量份比将所述乙烯基树脂、所述功能性填料和所述促进剂混合并搅拌均匀,得到混合物料;
17.s2、向所述混合物料中加入所述助剂并搅拌均匀,得到喷涂浆料;
18.s3、采用管内离心喷涂的方式,将所述喷涂浆料喷涂在所述内胶层的内壁上,固化形成所述耐高温、耐腐蚀特种涂层,即得到可防腐耐化学性软管。
19.进一步的,步骤s1中所述的搅拌速度为800
‑
1000rpm,搅拌10
‑
20分钟;步骤s2中所述的搅拌速度为1100
‑
1200rpm,搅拌15
‑
30分钟。优选的,步骤s1中其搅拌速度优选为800
‑
1000rpm;若搅拌速度低于该范围则不利于组分之间的分散,若高于该搅拌速度范围则搅拌时物料所受剪切力较大会影响物料分之间结构,从而影响最终所形成的耐高温、耐腐蚀特种涂层的性能,给耐高温和耐腐蚀性能带来不利影响,同时也会影响该涂层与原管道内胶层之间的粘接能力。
20.进一步的,步骤s3选用航空级高速风机作为离心喷涂的动力源,喷涂速度为8
‑
10米/分钟,喷涂温度为15
‑
35℃。具体的,在本发明的制备工艺中选用航空级高速风机作为动力源驱动,喷涂速度最高可达10米/分钟,喷枪流量根据plc流量控制阀调整,涂料高度雾
化,雾化微粒均匀,线速度高;涂层均匀、光滑、无气泡和针孔;涂层附着力好,一次喷涂即可达到所要求的厚度;施工速度快、效率高。
21.本发明的有益效果:
22.(1)本发明所提供的可防腐耐化学性软管其结构简单,生产成本较低;本发明软管的设计思路是通过在原有软管内部增加一层耐高温、耐腐蚀的特种涂层,并通过对特种涂层的配方优选,使得该涂层具备优异的耐腐蚀性能;本发明的软管由于设计了特种的耐高温、耐腐蚀涂层,因此并不需要原有管道中的内胶层具备耐腐蚀功能,因此本发明的软管解决了现有技术所面临的:若要内胶层满足耐腐蚀功能时,则会导致生产成本较高以及会使得内胶层与编织增强层之间粘连存在困难的难题。
23.(2)本发明的可防腐耐化学性软管通过选用耐高温、耐腐蚀的乙烯基树脂与水性pu、促进剂以及聚硅氧烷等组分,并严格控制各组分之间的比例调配,从而配置出厚膜型复合物作为软管内部的耐高温、耐腐蚀特种涂层,因此本发明的软管相对于现有技术改进内胶层使软管具备防腐功能来说是一种全新的防腐管道制备思路。本发明通过对耐高温、耐腐蚀特种涂层的配方调配使得该涂层均匀、光滑,可降低远距离输送的压力损失,柔韧性好,环保经济,选配适合不同救援或应用场所,扩大使用范围,成为多功能多用途的特种产品,有效提高了产品价值。
24.(3)本发明软管中设置的耐高温、耐腐蚀特种涂层通过对配方和配方比例的优选,使得该涂层不仅满足耐高温和耐腐蚀的功能,还使得该涂层与原有管道中的内胶层具备较强的粘接能力。
附图说明
25.为了更清楚地说明本发明实施例的技术方案,下面将对实施例描述中所需要使用的附图作简单地介绍,显而易见地,下面描述中的附图仅仅是本发明的一些实施例,对于本领域的技术人员来讲,在不付出创造性劳动的前提下,还可以根据这些附图获得其他附图。
26.图1为现有软管的结构示意图;
27.图2为本发明制备的可防腐耐化学性软管的结构示意图。
28.图中:1外胶层、2编织增强层、3内胶层、4耐高温、耐腐蚀特种涂层。
具体实施方式
29.下面将结合本发明实施例中的附图,对本发明实施例中的技术方案进行清楚、完整地描述,显然,所描述的实施例仅仅是本发明的一部分实施例,而不是全部的实施例。以下对至少一个示例性实施例的描述实际上仅仅是说明性的,决不作为对本发明及其应用或使用的任何限制。基于本发明中的实施例,本领域普通技术人员在没有作出创造性劳动前提下所获得的所有其他实施例,都属于本发明保护的范围。
30.实施例1
31.一种可防腐耐化学性软管,所述的软管由外向内依次包括外胶层1,编织增强层2,内胶层3和耐高温、耐腐蚀特种涂层4(该可防腐耐化学性软管的结构图如图2所示);所述的耐高温、耐腐蚀特种涂层4包括如下重量份的组分:乙烯基树脂100份、功能性填料15份、促进剂0.6份和助剂6份。所述的功能性填料为水性pu;所述的促进剂为低钴环保型异辛酸钴;
所述的助剂为聚硅氧烷。
32.实施例2
33.一种可防腐耐化学性软管,所述的软管由外向内依次包括外胶层1,编织增强层2,内胶层3和耐高温、耐腐蚀特种涂层4(该可防腐耐化学性软管的结构图如图2所示);所述的耐高温、耐腐蚀特种涂层4包括如下重量份的组分:乙烯基树脂100份、功能性填料10份、促进剂1份和助剂8份。所述的功能性填料为水性pu;所述的促进剂为为低钴环保型异辛酸钴;所述的助剂为聚硅氧烷。
34.实施例3
35.一种可防腐耐化学性软管,所述的软管由外向内依次包括外胶层1,编织增强层2,内胶层3和耐高温、耐腐蚀特种涂层4(该可防腐耐化学性软管的结构图如图2所示);所述的耐高温、耐腐蚀特种涂层4包括如下重量份的组分:乙烯基树脂100份、功能性填料20份、促进剂0.8份和助剂5份。所述的功能性填料为水性pu;所述的促进剂为为低钴环保型异辛酸钴;所述的助剂为聚硅氧烷。
36.实施例4
37.一种可防腐耐化学性软管,所述的软管由外向内依次包括外胶层1,编织增强层2,内胶层3和耐高温、耐腐蚀特种涂层4(该可防腐耐化学性软管的结构图如图2所示);所述的耐高温、耐腐蚀特种涂层4包括如下重量份的组分:乙烯基树脂100份、功能性填料12份、促进剂0.6份和助剂7份。所述的功能性填料为水性pu;所述的促进剂为为低钴环保型异辛酸钴;所述的助剂为聚硅氧烷。
38.实施例5
39.一种可防腐耐化学性软管,所述的软管由外向内依次包括外胶层1,编织增强层2,内胶层3和耐高温、耐腐蚀特种涂层4(该可防腐耐化学性软管的结构图如图2所示);所述的耐高温、耐腐蚀特种涂层4包括如下重量份的组分:乙烯基树脂100份、功能性填料18份、促进剂0.7份和助剂8份。所述的功能性填料为水性pu;所述的促进剂为为低钴环保型异辛酸钴;所述的助剂为聚硅氧烷。
40.上述实施1
‑
5的区别在于耐高温、耐腐蚀特种涂层4中的组分含量不同,其余均相同。
41.实施例6
42.上述实施l的可防腐耐化学性软管的制备方法,包括如下步骤:该可防腐耐化学性软管的制备方法,是在原有软管的基础之上,在软管内部的内胶层3上再复合一层耐高温、耐腐蚀的特种涂层4,从而形成实施例1所述的可防腐耐化学性软管;其具体的生产工艺如下(这里原有的软管生产工艺不做赘述,直接用现成的原有软管即可,原有软管的结构如图1所示):
43.s1、按重量份比将100份的乙烯基树脂、15份的功能性填料(即15份的水性pu)和0.6份的促进剂混合,并在900rpm下机械搅拌15分钟,使之混合均匀,得到混合物料;
44.s2、向上述的混合物料中加入6份的助剂(即6份聚硅氧烷)并在1100rpm下机械搅拌20分钟,使之混合均匀,得到喷涂浆料;
45.s3、选用航空级高速风机作为离心喷涂的动力源,采用管内离心喷涂的方式,将上述的喷涂浆料喷涂在内胶层3的内壁上(其中喷涂速度为8米/分钟,喷涂温度为15℃),固化
形成780μm厚的耐高温、耐腐蚀特种涂层4;最终得到可防腐耐化学性软管。
46.实施例7
47.上述实施例2的可防腐耐化学性软管的制备方法,包括如下步骤:
48.s1、按重量份比将100份的乙烯基树脂、10份的功能性填料(即10份的水性pu)和1份的促进剂混合,并在800rpm下机械搅拌20分钟,使之混合均匀,得到混合物料;
49.s2、向上述的混合物料中加入8份的助剂(即8份聚硅氧烷)并在1200rpm下机械搅拌15分钟,使之混合均匀,得到喷涂浆料;
50.s3、选用航空级高速风机作为离心喷涂的动力源,采用管内离心喷涂的方式,将上述的喷涂浆料喷涂在内胶层3的内壁上(其中喷涂速度为9米/分钟,喷涂温度为20℃),固化形成760μm厚的耐高温、耐腐蚀特种涂层4;最终得到可防腐耐化学性软管。
51.实施例8
52.上述实施例3的可防腐耐化学性软管的制备方法,包括如下步骤:
53.s1、按重量份比将100份的乙烯基树脂、20份的功能性填料(即20份的水性pu)和0.8份的促进剂混合,并在1000rpm下机械搅拌10分钟,使之混合均匀,得到混合物料;
54.s2、向上述的混合物料中加入5份的助剂(即5份聚硅氧烷)并在1100rpm下机械搅拌20分钟,使之混合均匀,得到喷涂浆料;
55.s3、选用航空级高速风机作为离心喷涂的动力源,采用管内离心喷涂的方式,将上述的喷涂浆料喷涂在内胶层3的内壁上(其中喷涂速度为8米/分钟,喷涂温度为25℃),固化形成760μm厚的耐高温、耐腐蚀特种涂层4;最终得到可防腐耐化学性软管。
56.实施例9
57.上述实施例4的可防腐耐化学性软管的制备方法,包括如下步骤:
58.s1、按重量份比将100份的乙烯基树脂、12份的功能性填料(即12份的水性pu)和0.6份的促进剂混合,并在850rpm下机械搅拌15分钟,使之混合均匀,得到混合物料;
59.s2、向上述的混合物料中加入7份的助剂(即7份聚硅氧烷)并在1150rpm下机械搅拌25分钟,使之混合均匀,得到喷涂浆料;
60.s3、选用航空级高速风机作为离心喷涂的动力源,采用管内离心喷涂的方式,将上述的喷涂浆料喷涂在内胶层3的内壁上(其中喷涂速度为8米/分钟,喷涂温度为30℃),固化形成720μm厚的耐高温、耐腐蚀特种涂层4;最终得到可防腐耐化学性软管。
61.实施例10
62.上述实施例5的可防腐耐化学性软管的制备方法,包括如下步骤:
63.s1、按重量份比将100份的乙烯基树脂、18份的功能性填料(即18份的水性pu)和0.7份的促进剂混合,并在950rpm下机械搅拌15分钟,使之混合均匀,得到混合物料;
64.s2、向上述的混合物料中加入8份的助剂(即8份聚硅氧烷)并在1100rpm下机械搅拌20分钟,使之混合均匀,得到喷涂浆料;
65.s3、选用航空级高速风机作为离心喷涂的动力源,采用管内离心喷涂的方式,将上述的喷涂浆料喷涂在内胶层3的内壁上(其中喷涂速度为8米/分钟,喷涂温度为35℃),固化形成720μm厚的耐高温、耐腐蚀特种涂层4;最终得到可防腐耐化学性软管。
66.测试:将上述实施例6
‑
10中制得的可防腐耐化学性软管的制备参数汇总并测试其与内胶层的附着力,将其制成下表:
[0067][0068]
由表中的测试数据可以看出在可控的速度和不同的生产环境温度下,通过耐腐蚀涂层达到有效的设计厚度,并验证涂层的与内胶层的附着力,达到附着要求。
[0069]
上述为本发明的较佳实施例仅用于解释本发明,并不用于限定本发明。凡由本发明的技术方案所引伸出的显而易见的变化或变动仍处于本发明的保护范围之中。