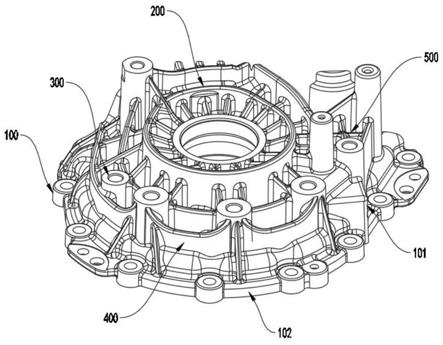
1.本发明属于新能源汽车变速器技术领域,具体涉及一种抑制形变的变速器壳体、变速器及车辆。
背景技术:2.随着新能源汽车的市场保有量大幅上涨,关于新能源汽车的要求也越来越高,目前新能源汽车中的减速器普遍存在产生啸叫的噪音问题,而解决这个问题最经济、最有效的方案就是提高齿轮副传动时的重合度,提高重合度最直接的方案就是增大螺旋角,但增大螺旋角会相应地出现壳体变形量增大,传动时,整个变速器系统的传递误差都会增大。
3.对于上述问题,大部分厂家采用的方式是增厚变速器壳体的厚度,以达到增强变速器壳体的强度,继而控制形变量,但该种方式成效并不显著,即要想较好地控制形变量,就需要大幅度增厚壳体厚度,导致变速器壳体重量过重,完全不符合目前新能源汽车轻量化的趋势。
技术实现要素:4.有鉴于此,本发明提供了一种抑制形变的变速器壳体、变速器及车辆,用以解决现有技术中存在的变速器壳体形变量过大,导致传递误差增大的问题。
5.本发明采用的技术方案是:
6.第一方面,本发明提供了一种抑制形变的变速器壳体,所述变速器壳体包括:壳本体、设置在所述壳本体上并贯通所述壳本体的轴承孔以及用于传递轴向力的第一加强部;
7.所述第一加强部包括:首尾相连呈环形的高环筋、多个加强筋以及多个支撑筋,所述高环筋与所述轴承孔同轴设置,所述加强筋设置在所述高环筋与所述轴承孔之间,所述支撑筋设置在所述高环筋背离所述加强筋的一侧边沿上,用于支撑所述高环筋;
8.在所述壳本体的外围边缘上设有多个圆柱形的安装台,在所述安装台上开设有用于安装变速器壳体的安装孔。
9.作为上述抑制形变的变速器壳体的优选方案,所述加强筋与所述高环筋连接处以及所述加强筋与所述轴承孔连接处均为弧形。
10.作为上述抑制形变的变速器壳体的优选方案,所述变速器壳体还包括:第二加强部和第三加强部,所述第二加强部设在所述第一加强部的外围上,所述第三加强部设在所述第二加强部的外围上。
11.作为上述抑制形变的变速器壳体的优选方案,所述第二加强部包括:加强环以及加强柱,所述加强环朝向所述高环筋的一侧与所述支撑筋连接,所述加强柱设置在与所述支撑筋位置对应的所述加强环上。
12.作为上述抑制形变的变速器壳体的优选方案,所述第三加强部包括:支撑墙体、凸起以及斜拉筋,所述支撑墙体设置在相邻所述加强柱之间,所述斜拉筋则倾斜设置在所述加强柱表面或者所述支撑墙体表面,所述凸起围绕在所述支撑墙体背离所述加强柱的外表
面上。
13.作为上述抑制形变的变速器壳体的优选方案,所述高环筋的高度大于所述加强环的高度,所述加强环的高度大于所述支撑墙体的高度。
14.作为上述抑制形变的变速器壳体的优选方案,所述壳本体上还开设有注油孔。
15.作为上述抑制形变的变速器壳体的优选方案,所述壳本体上还设有副轴安装部,所述副轴安装部与所述注油孔之间设有用于传递轴向力和径向力的衔接部。
16.第二方面,本发明提供了一种变速器,所述变速器包括上述任意一种抑制形变的变速器壳体。
17.第三方面,本发明提供了一种车辆,所述车辆包括上述任意一种抑制形变的变速器壳体或者包括上述的变速器。
18.综上所述,本发明的有益效果如下:
19.本发明提供的抑制形变的变速器壳体、变速器及车辆通过设置第一加强部,第一加强部包括高环筋、支撑筋以及加强筋,利用高环筋与所述轴承孔同轴设置,所述加强筋又设置在所述高环筋与所述轴承孔之间,所述支撑筋设置在所述高环筋背离所述加强筋的一侧边沿上,用于支撑所述高环筋,通过高环筋、支撑筋以及加强筋三者的配合,将轴承孔处受到的轴向力分散至壳本体的周围,使一些受力较小的部位能够分担一部分轴向力,一部分受力较大,可能变形的部位受到的轴向力减小,达到增强壳本体强度,抑制壳本体发生变形的效果。
附图说明
20.为了更清楚地说明本发明实施例的技术方案,下面将对本发明实施例中所需要使用的附图作简单地介绍,对于本领域普通技术人员来讲,在不付出创造性劳动的前提下,还可以根据这些附图获得其他的附图,这些均在本发明的保护范围内。
21.图1为本发明中抑制形变的变速器壳体的结构示意图;
22.图2为本发明中体现衔接部的视角的结构示意图;
23.图3为本发明的变速器四挡换挡装置的三维结构图;
24.图4为本发明的换挡鼓的换挡区与第一驱动机构和第二驱动机构的角位置关系图;
25.图5为本发明的换挡鼓的三维结构图;
26.图6为本发明的第一驱动机构与换挡鼓配合的三维结构图;
27.图7为本发明的第一驱动机构与换挡鼓配合的三维结构图;
28.图8为本发明的第一驱动机构与第一同步器配合的三维结构图;
29.图9为本发明的可使转动带随同步器转动的结构的俯视图;
30.图10为本发明的可使转动带随同步器转动的结构的侧视图;
31.图11为本发明的四个转动件的位置关系图;
32.图12为本发明的传动法兰的三维结构图;
33.图13为本发明的传动法兰的另一个视角的三维结构图;
34.图14为本发明的传动法兰用于和传动轴连接的结构的三维视图;
35.图15为本发明的传动法兰的侧视图;
36.图16为本发明的传动法兰的主视图;
37.图17为本发明的三组子传动结构组断开设置的结构示意图;
38.图18为本发明的传动法兰的两组子传动结构在周向方向上错开设置的结构示意图;
39.图19为本发明多功能减速器的结构示意图;
40.图20为本发明多功能减速器的油路示意图;
41.图21为本发明多功能减速器的控制方法的流程示意图;
42.图22为本发明多功能减速器的控制方法进一步细化的流程示意图
43.图23为本发明中车辆的结构示意图。
44.图中零件部件及编号:
45.100、壳本体;101、注油孔;102、底座102;
46.200、第一加强部;201、高环筋;202、加强筋;203、支撑筋;
47.300、第二加强部;301、加强柱;302、加强环;
48.400、第三加强部;401、支撑墙体;402、凸起;403、斜拉筋;
49.500、衔接部;501、加强板;502、连接柱;503、十字筋;504、多个矩形筋;505、衔接环;506、衔接筋;
50.600、动力系统;700、传动系统;800、车身;
51.1、换挡鼓;11、导引槽;111、换挡区;113、第一导引段;114、第二导引段;115、第三导引段;12、第一角位置;13、第二角位置;
52.2、第一同步器;21、限位槽21;
53.3、第一驱动机构;31、第一滑动件;32、第一拨叉;33、第一连接件;321、第一转动件;322、第二转动件;323、第三转动件;324、第四转动件;325、拨动件;326、转动带;
54.4、第二同步器;5、第二驱动机构;51、第二滑动件;52、第二拨叉;53、第二连接件;6、电机;7、转轴;
55.410、法兰主体;411、第一连接部;412、第二连接部;4121、限位孔;4122、止口;420、第一传动结构;430、第一连接结构;440、第二传动结构;441、第一子传动结构组;442、第二子传动结构组;443、第三子传动结构组;444、第四子传动结构组;445、第五子传动结构组;
56.10、供油系统;20、润滑系统;30、驻车系统;40、油路通断装置;110、驱动电机;120、电机控制器;130、润滑油泵;41、电磁阀;41a、第一阀门;41b、第二阀门;310、液压杆;320、液压缸;330、位移传感器。
具体实施方式
57.为使本发明实施例的目的、技术方案和优点更加清楚,下面将结合本发明实施例中的附图,对本发明实施例中的技术方案进行清楚、完整地描述。需要说明的是,在本文中,诸如第一和第二等之类的关系术语仅仅用来将一个实体或者操作与另一个实体或操作区分开来,而不一定要求或者暗示这些实体或操作之间存在任何这种实际的关系或者顺序。在本发明的描述中,需要理解的是,术语“中心”、“上”、“下”、“前”、“后”、“左”、“右”、“竖直”、“水平”、“顶”、“底”、“内”、“外”等指示的方位或位置关系为基于附图所示的方位或位置关系,仅是为了便于描述本技术和简化描述,而不是指示或暗示所指的装置或元件必须
具有特定的方位、以特定的方位构造和操作,因此不能理解为对本发明的限制。而且,术语“包括”、“包含”或者其任何其他变体意在涵盖非排他性的包含,从而使得包括一系列要素的过程、方法、物品或者设备不仅包括那些要素,而且还包括没有明确列出的其他要素,或者是还包括为这种过程、方法、物品或者设备所固有的要素。在没有更多限制的情况下,由语句“包括
……”
限定的要素,并不排除在包括所述要素的过程、方法、物品或者设备中还存在另外的相同要素。如果不冲突,本发明实施例以及实施例中的各个特征可以相互结合,均在本发明的保护范围之内。
58.请参见图23,车辆是一种常用的交通工具,主要由动力系统600、传动系统700、车身800、底盘等组成。其中传动系统700又包括了变速器、变速器四挡换挡装置、传动轴、差速器以及传动法兰等。车辆行驶时动力系统600的动力传动给变速器,变速器将动力系统600的动力进行转换后输出具有合适的扭矩和转速的动力,转换后的动力再传递给传动轴,传动轴将动力传动给差速器后,由差速器将动力分别传递给两侧的车轮,转换后的动力也可以传递给差速器。为了实现驻车和换挡,变速器还设置有换挡装置和驻车装置。为了给变速器、差速器等装置润滑,还为变速器、差速器等装置配置了润滑系统。
59.实施例1
60.请参见图1和图2,本发明实施例1公开了一种抑制形变的变速器壳体。变速器啸叫是目前新能源变速器普遍存在的一个问题,针对啸叫也提出了一些有效的方案,最常见,也最有效的方案便是提高齿轮副传动时的重合度。因为变速器之所以产生啸叫就是因为齿轮之间不能做到完全啮合,齿与齿之间会发生碰撞,从而产生啸叫,所以提高齿轮副传动重合度便是最直接有效的方法。而提高传动重合度,最直接的方法就是增大齿轮和轴的螺旋角,但随着螺旋角的增大,变速器壳体受到的轴向力也会越来越大,导致变速器壳体产生过大的变形,降低传递精度,而本实施例提出的变速器壳体则能够在满足增大螺旋角的情况下,其壳体变形量相较于现有技术还能减小。
61.本变速器壳体包括:壳本体100、第一加强部200、第二加强部300以及第三加强部400。在壳本体100上还开设有贯通壳本体100的轴承孔,用于安装轴承。在轴承孔内壁上还开设有呈螺旋状的凹槽,用于轴承的安装以及对进入轴承孔内的润滑油进行导流,使润滑油能够充分润滑到轴承。而第一加强部200则套设在轴承孔的外围,将轴承孔包围,且第一加强部200与轴承孔是同轴设置,用于分散和传递轴承作用于壳本体100上的轴向力和径向力。第二加强部300则设置在第一加强部200的外围,用于传递第一加强部200上的轴向力和径向力;第三加强部400设置在第二加强部300的外围,用于传递第二加强部300上的轴向力和径向力,使壳本体100受到的轴向力与径向力分布在壳本体100的各个部位。在壳本体100的最外围边缘上还设有多个用于安装变速器壳体的安装孔,安装孔并非直接在壳体上开孔,而是在壳本体100边缘上设置多个圆柱形的安装台,安装孔则开设在安装台上,以此增强壳本体100边缘的强度,而不会因为开孔影响壳本体100的强度。安装台与壳本体100连接的部分均设置为圆弧形,避免壳本体100边缘直接与其他零部件发生碰撞。
62.为便于理解抑制形变的变速器壳体的结构,现将第一加强部200、第二加强部300以及第三加强部400分别进行描述,如下:
63.第一加强部200:该第一加强部200包括首尾相连呈环形的高环筋201、多个加强筋202以及多个支撑筋203。其中,高环筋201与轴承孔同轴设置,且高环筋201的直径大于轴承
孔的直径,使高环筋201将轴承孔包围。高环筋201在轴承孔轴向方向上的长度大于轴承孔在轴向方向上的长度,使高环筋201能够传递更多的轴向力。加强筋202则设置在高环筋201与轴承孔之间,且加强筋202的一端固定在高环筋201朝向轴承孔方向的内壁上,另一端则固定在轴承孔的外表面上。加强筋202的横截面呈梯形状,且加强筋202位于背离变速器壳体内腔的一侧边呈倾斜设置,从径向方向看,加强筋202成倾斜设置的边在位于高环筋201上的一端高于位于轴承孔上的一端,这样更有利于加强筋202将轴承孔上的轴向力传递至高环筋201上,且高环筋201高度相较于轴承孔更高,更有利于将传递至高环筋201上的轴向力进一步传递扩散。加强筋202与高环筋201连接处以及加强筋202与轴承孔外表面连接处均为弧形的连接面,加强筋202在背离壳本体100内腔方向的端面也呈弧形,能够避免加强筋202直接受到来自垂直于加强筋202端面的冲击力。多个加强筋202围绕轴承孔呈环形布置,且多个加强筋202围成的环形与轴承孔同轴设置,以此将轴向力和径向力传递至高环筋201上。
64.支撑筋203的横截面也为梯形状,设置在高环筋201的外围表面上。支撑筋203与高环筋201连接处呈弧形的连接面,支撑筋203在背离壳本体100内腔的一端面也呈弧形状,与加强筋202连接面呈弧形是同一作用,均能够避免冲击力直接垂直作用于支撑筋203上。支撑筋203在背离壳本体100内腔的一端端面呈倾斜设置,其倾斜方向与加强筋202的倾斜方向相对,即支撑筋203该端面中与高环筋201连接的一端在轴向方向上的高度高于该端面中与第二加强部300连接的一端在轴向方向上的高度。加强筋202与支撑筋203呈倾斜相对设置,共同对高环筋201起到支撑稳固作用。
65.通过支撑筋203、高环筋201以及加强筋202之间的配合,将轴向力和径向力传递至壳本体100各处,使壳本体100受力过大的部分受力减小,受力较小的部分因为分担传递过来的轴向力或径向力而增大,以此减小壳本体100因某部位受力过大而产生的形变量。
66.第二加强部300:该第二加强部300包括加强柱301以及加强环302。加强柱301设有多个,且加强柱301的大小、高度根据壳本体100与外部设备(未示出)连接的具体情况各不相同。加强环302呈未封口的环形,设置在高环筋201的外围,将高环筋201的一部分包围,加强环302在轴向方向上的长度小于高环筋201在轴向方向上的长度。其中,多个加强柱301沿加强环302的环形路径进行设置,固定在加强环302上。在加强环302上具有多个连接部位,其每一个连接部位处均具有加强柱301和支撑筋203。一部分加强柱301对应与两根支撑筋203连接,一部分加强柱301对应与一根支撑筋203连接,根据加强柱301的体积大小决定。在加强柱301的中心轴上开设有轴心孔,用于减轻变速器壳体的重量以及用于配合外部设备进行安装。
67.第三加强部400:该第三加强部400包括支撑墙体401、凸起402以及斜拉筋403。支撑墙体401设有多个,其围绕加强环302的外围进行设置,支撑墙体401的两端固定在加强柱301的表面上。凸起402则设置在支撑墙体401背离加强环302的一侧,且凸起402呈不规则的弧面形状,贴附在支撑墙体401表面,对支撑墙体401起到固定的作用。对于斜拉筋403,也设置在支撑墙体401背离加强环302的一侧,一部分斜拉筋403的一端固定在支撑墙体401上,一部分斜拉筋403的一端则直接固定在支撑柱上。斜拉筋403靠近支撑墙体401或者加强柱301的部分是完全贴附在支撑墙体401或者加强柱301上,斜拉筋403背离支撑墙体401或者加强柱301的部分则是完全贴附在凸起402上,与凸起402成一体设置。在斜拉筋403位于凸
起402上的部分的端头还与壳本体100的底座102连接,以此使斜拉筋403找到支撑点。斜拉筋403因为凸起402的缘故,所以斜拉筋403呈朝向支撑墙体401倾斜的状态,对支撑墙体401起到支撑和稳固的作用。
68.其中,高环筋201轴向方向上的长度大于加强环302轴向方向上的长度,加强环302轴向方向上的长度大于支撑墙体401轴向方向上的长度,利用水波纹遇障碍物进行传播的原理,使得变速器内发出啸叫的声音得到减小。
69.在壳本体100上还设有一个或者多个副轴安装部(未示出),用于安装副传动轴。在壳本体100上还开设有注油孔101,注油孔101和副轴安装部均位于支撑墙体401沿其路径末端的同一侧。在注油孔101与副轴安装部之间还设有衔接部500,用于将副轴安装部与第三加强部400衔接起来。
70.衔接部500包括:加强板501、连接柱502、十字筋503、多个矩形筋504、衔接环505以及多根衔接筋506。506其中连接柱502至少有两个,设置在壳本体100的底座102上。加强板501设有三个,形状根据其位置的不同而均不相同,一个加强板501设置在两个连接柱502之间,将相邻两根连接柱502连接起来,一个加强板501将其中一个连接柱502与衔接环505表面连接,最后一个加强板501将另一个连接柱502与衔接环505表面连接,三个加强板501与衔接环505以及两个连接柱502共同围成一个空腔。十字筋503则设置在该空腔内,十字筋503的四个端部分别与空腔的四面内壁固定接触,即十字筋503的一端固定在衔接环505表面,一端固定在其中一个加强板501上,一端固定在另一个加强板501上,一端固定在一个连接柱502上,对连接柱502、连接板以及衔接环505均起到固定支撑作用,也能将轴向力和径向力传递至各个部位。衔接环505呈开口设置,围绕在高环筋201的外侧,与高环筋201同轴设置。而多个矩形筋504则设置在高环筋201与衔接环505之间,多个矩形筋504沿高环筋201的外围路径依次排列,将高环筋201上的轴向力和径向力传递至衔接环505上,同时也对高环筋201起到支撑作用,采用矩形也是为了能够尽可能多地增加与高环筋201和衔接环505之间的接触面积,增大力的传递以及支撑强度。多根衔接筋506均呈三角形状,但多根衔接筋506之间的面积、高度均各不相同,以适应其不同的安装位置。其一部分衔接筋506设置在靠近副轴安装部一端的加强板501上,另一部分衔接筋506则设置在衔接环505表面上。而衔接筋506背离衔接环505或者加强板501的一端则均设置在底座102上,起到支撑作用。通过衔接部500的设置,可以进一步将轴承孔上受到的轴向力以及径向力传递至副轴安装部,扩大轴向力与径向力的扩散范围,使变速器壳体的各个部分均受到一定的轴向力和径向力,从而为一些受力较大的部位减轻负担,减小甚至消除变速器壳体的变形量。
71.本发明的工作原理:
72.本实施例中抑制形变的变速器壳体在工作时,齿轮以及轴承均进行转动,对变速器壳体产生轴向力、径向力以及扭矩,又由于增大螺旋角,减少啸叫的缘故,变速器壳体受到的轴向力以及径向力都会增加。在变速器壳体产生轴向力和径向力时,通过第一加强部200将轴向力以及径向力传递至第一加强部200自身以及第一加强部200周围的壳本体100上;再通过第二加强部300又将一部分轴向力以及径向力传递至第二加强部300自身以及第二加强部300周围的壳本体100上;再通过第三加强部400又将一部分轴向力以及径向力传递至第三加强部400自身以及第三加强部400周围的壳本体100上;最后,一部分轴向力和径向力还会通过衔接部500,被传递至衔接部500自身上以及传递至副轴安装部上。通过上述
一系列力的传递,达到将轴向力和径向力分散至壳本体100的各个部分,尽可能使壳本体100受力变得相对平衡,受力较大且易发生变形的部位受力得到减小,实现变速器壳体形变量减小甚至消除的效果。
73.实施例2
74.本发明实施例2公开了一种变速器,该变速器包括实施例1中的一种抑制形变的变速器壳体。
75.发明实施例2中变速器采用上述结构,在工作时,齿轮以及轴承均进行转动,对变速器壳体产生轴向力、径向力以及扭矩,又由于增大螺旋角,减少啸叫的缘故,变速器壳体受到的轴向力以及径向力都会增加。在变速器壳体产生轴向力和径向力时,通过第一加强部200将轴向力以及径向力传递至第一加强部200自身以及第一加强部200周围的壳本体100上;再通过第二加强部300又将一部分轴向力以及径向力传递至第二加强部300自身以及第二加强部300周围的壳本体100上;再通过第三加强部400又将一部分轴向力以及径向力传递至第三加强部400自身以及第三加强部400周围的壳本体100上;最后,一部分轴向力和径向力还会通过衔接部500,被传递至衔接部500自身上以及传递至副轴安装部上。通过上述一系列力的传递,达到将轴向力和径向力分散至壳本体100的各个部分,尽可能使壳本体100受力变得相对平衡,受力较大且易发生变形的部位受力得到减小,实现变速器壳体形变量减小甚至消除的效果。
76.除此以外,该变速器还包括四挡换挡装置,该装置用于进行四个档位的挂挡操作。为了便于描述,本文将这四个档位分为两组,分别为第一组档位和第二组档位,每组档位包括两个档位。本实施例的变速器四挡换挡装置包括换挡鼓1、电机6、第一同步器、第一驱动机构3、第二同步器4和第二驱动机构5。
77.如图4和图5所示,其中换挡鼓1设置有沿其周向方向延伸的导引槽11,所述导引槽11包括随换挡鼓1转动至不同角位置的换挡区111;
78.如图3所示,换挡鼓1可以设置为圆柱状,前述导引槽11则可以设置在换挡鼓1的圆柱形的周壁上,换挡区111为整个导引槽11的其中一部分区域,换挡鼓1可以绕自身的轴线旋转,换挡区111也随换挡鼓1的旋转而转动到不同的位置。
79.如图6所示,其中第一同步器用于参与第一组档位的挂挡操作。第一同步器可以与输入轴或者输出轴同步转动连接;第一同步器上设置有挂挡部件,挂挡部件在外力作用下(例如在拨叉的拨动下)可沿第一同步器的轴向方向移动,当第一同步器的挂挡部件移动至与某个挡位的齿轮完全结合时,第一同步器与该齿轮同步转动,这时输入轴的动力可以通过第一同步器传递给该齿轮,或者该齿轮的动力可以传递给输出轴。前述同步传动连接,是指可以使第一同步器和输入轴或者输出轴同步转动的连接方式。
80.其中所述第一驱动机构3在换挡鼓1的第一角位置12与导引槽11滑动连接,所述第一驱动机构3用于在换挡区111的驱动下推动第一同步器的挂挡部件沿第一同步器的轴向方向移动至第一轴向位置挂挡,或推动第一同步器的挂挡部件沿第一同步器的轴向方向移动至第二轴向位置挂挡,其中第一轴向位置与第二轴向位置不相同;
81.其中第一轴向位置是指第一同步器的挂挡部件与第一组档位中的其中一个档位的齿轮完全结合并使该齿轮与其同步转动时所处的位置。其中第二轴向位置是指第一同步器的挂挡部件与第一组档位中的另一个档位的齿轮完全结合并使该齿轮与其同步转动时
所处的位置。前述挂挡部件可以是第一同步器的同步环。
82.随着换挡鼓1的转动,换挡区111域可以转动到与第一驱动机构3滑动连接的角位置范围。在该角位置范围内,随着换挡鼓1的转动,换挡区111域与第一驱动连接的位置也不断变化。由于换挡区111域各个位置沿轴向方向与第一同步器的距离有差异,因此换挡区111在转动过程中可以驱动第一驱动机构3沿轴向方向移动,第一驱动机构3沿轴向方向移动的同时又推动第一同步器的挂挡部件沿轴向方向移动。
83.在本实施例中所述第一驱动机构3包括第一滑动件31、第一拨叉32和第一连接件33,所述第一连接件33分别与所述第一滑动件31和第一拨叉32连接,所述第一滑动件31沿所述导引槽11滑动。
84.其中引导槽的宽度略大于第一滑动件31的宽度,第一连接件33的运动方向受到约束,其只能沿轴向方向移动。沿换挡鼓1的轴向方向看去,在一些区域导引槽11在不同的周向位置距离第一同步器或者第二同步器4的距离有所不同。当换挡鼓1转动时,导引槽11的不同位置与第一滑动件31接触,滑动件一边相对导引槽11沿周向方向滑动,一边也在导引槽11的驱动下沿着轴向方向来回移动。由于第一连接件33将第一滑动件31、第一拨叉32连接在了一起,因此,第一拨叉32也随第一滑动件31同步沿轴向方向移动。其中第一连接件33可以设置在换挡鼓1径向方向的侧面,第一滑动件31沿换挡鼓1的径向方向设置,第一滑动件31的一端与第一连接件33相连,相对的另一端嵌入到导引槽11中。
85.如图3和图7所示,其中第二同步器4用于参与第二组挡位的挂挡操作,第二同步器4可以与输入轴或者输出轴同步转动连接;第二同步器4上设置有挂挡部件,挂挡部件在外力作用下(例如在拨叉的拨动下)可沿第二同步器4的轴向方向移动,当第二同步器4的挂挡部件移动至与某个挡位的齿轮完全结合时,第二同步器4与该齿轮同步转动,这时输入轴的动力可以通过第二同步器4传递给该齿轮,或者该齿轮的动力可以传递给输出轴。前述同步传动连接,是指可以使第二同步器4和输入轴或者输出轴同步转动的连接方式。
86.其中所述第二驱动机构5在换挡鼓1的第二角位置13与导引槽11滑动连接,所述第二驱动机构5用于在换挡区111的驱动下推动第二同步器4的挂挡部件沿第二同步器4的轴向方向移动至第三轴向位置挂挡,或推动第二同步器4的挂挡部件沿第二同步器4的轴向方向移动至第四轴向位置挂挡,其中第三轴向位置与第四轴向位置不相同,所述第二角位置13不同于第一角位置12;
87.其中第三轴向位置是指第二同步器4的挂挡部件与第二组档位中的其中一个档位的齿轮完全结合并使该齿轮与其同步转动时所处的位置。其中第四轴向位置是指第二同步器4的挂挡部件与第二组档位中的另一个档位的齿轮完全结合并使该齿轮与其同步转动时所处的位置。前述挂挡部件可以是第二同步器4的同步环。
88.随着换挡鼓1的转动,换挡区111域可以转动到与第二驱动机构5滑动连接的角位置范围。在该角位置范围内,随着换挡鼓1的转动,换挡区111域与第二驱动连接的位置也不断变化。由于换挡区111域各个位置沿轴向方向与第二同步器4的距离有差异,因此换挡区111在转动过程中可以驱动第二驱动机构5沿轴向方向移动,第二驱动机构5沿轴向方向移动的同时又推动第二同步器4的挂挡部件沿轴向方向移动。
89.在本实施例中所述第二驱动机构5包括第二滑动件51、第二拨叉52和第二连接件53,所述第二连接件53分别与所述第二滑动件51和第二拨叉52连接,所述第二滑动件51沿
所述导引槽11滑动。
90.其中引导槽的宽度略大于第二滑动件51的宽度,第二连接件53的运动方向受到约束,其只能沿轴向方向移动。沿换挡鼓1的轴向方向看去,在一些区域导引槽11在不同的周向位置距离第一同步器或者第二同步器4的距离有所不同。当换挡鼓1转动时,导引槽11的不同位置与第二滑动件51接触,滑动件一边相对导引槽11沿周向方向滑动,一边也在导引槽11的驱动下沿着轴向方向来回移动。由于第二连接件53将第二滑动件51、第二拨叉52连接在了一起,因此,第二拨叉52也随第二滑动件51同步沿轴向方向移动。其中第二连接件53可以设置在换挡鼓1径向方向的侧面,第二滑动件51沿换挡鼓1的径向方向设置,第二滑动件51的一端与第二连接件53相连,相对的另一端嵌入到导引槽11中。
91.如图3所示,其中电机6用于驱动所述换挡鼓1转动以使换挡区111驱动第一驱动机构3和第二驱动机构5沿换挡鼓1的轴向方向来回移动。所述电机6位和第一同步器以及第二同步器4位于换挡鼓1的轴向方向的两侧,所述电机6与所述换挡鼓1同轴设置。
92.本实施例将电机6和两个驱动机构沿轴向方向分开设置,使其位于换挡鼓1的两侧,这样电机6和驱动机构的动作可以互不影响,并且将电机6与所述换挡鼓1同轴设置可以使结构更加紧凑,也利用电机6和换挡鼓1之间动力的传递。
93.作为一种优选的实施方式,在本实施例中,所述变速器四挡换挡装置还包括转轴7,所述换挡鼓1与所述转轴7过盈配合,所述电机6驱动所述转轴7转动以带动所述换挡鼓1转动。通过转动轴与换挡鼓1直接采用过盈配合的方式进行传动,传动过程更加简单可靠。其中电机6安装在总成箱体上,换挡鼓1通过转轴7在箱体上定位,换挡鼓1和换挡鼓1轴转轴7相对固定,转轴7在箱体上可以转动。
94.如图8所示,在本实施例中,所述第一同步器和/或第二同步器4的周壁上设置有环形的限位槽21,所述述第一拨叉32和/或第二拨叉52的端部设置有拨动件325,所述拨动件325通过拨动所述限位槽21的侧壁来拨动第一同步器和/或第二同步器4的挂挡部件。
95.在本实施例中,所述限位槽21的宽度大于拨动件325宽度的1.1倍,第一轴向位置和第二轴向位置之间的距离大于拨动件325和限位槽21之间的轴向间隙的2倍。采用前述结构,拨动件325插入限位槽21中并将同步器的挂挡部件拨动至挂挡位置后,拨动件325的一侧与限位槽21的一个侧壁接触,拨动件325的另一侧与限位槽21的另一个侧壁之间留有足够的间隙。这样当出现意外小幅振动导致拨动件325与限位槽21之间产生相对位移后,拨动件325的另一侧也不会与限位槽21的另一个侧壁接触,这样避免了因为意外振动而导致拨动件325拨动限位槽21,使挂挡部件从当前的档位脱出,从而使挂挡更加可靠。而正常挂挡时,拨动件325沿轴向方向移动的距离要超过拨动件325和限位槽21之间的轴向间隙,因此拨动移动过程中拨动件325的另一侧也可以通过与限位槽21的另一个侧壁接触来推动挂挡部件移动。
96.当拨动件325拨动同步器换挡时,拨动件325与同步器接触,而同步器处于高速转动中,拨动件325和同步器之间产生相对运动,因此拨动件325与同步器之间存在持续性的滑动摩擦,拨动件325和同步器都容易磨损变形,且摩擦产生的热量也会对变速箱产生影响。对此可以在拨动件325上设置可以更换的耐磨件,让耐磨件与同步器接触。当耐磨件磨损到一定程度后再更换新的耐磨件。当是采用这种方式需要拆装变速箱,才能更换耐磨件,因此实际使用过程中十分不方便。
97.对此可以在第一拨叉32上设置导油槽,并将导油槽的出口设置在拨动件325与同步器接触的表面,润滑油沿导油槽流到拨动件325表面,在拨动件325与同步器之间形成油膜以减小两者之间的摩擦。
98.此外也可以在拨动件325上设置滚子或者滚针,来减少摩擦,但是由于滚子与同步器接触时为点接触,滚针与同步器接触时为线接触,这两种接触方式的接触面积都很小,容易造成同步器和拨叉受力过于集中。
99.对此,本实施例采用可以使拨动件325随同步器同步转动结构的来避免摩擦。如9至图11所示,本实施例的第一拨叉32还包括圆柱形的第一转动件321、第二转动件322、第三转动件323和第四转动件324,所述第一转动件321、第二转动件322、第三转动件323和第四转动件324与所述第一拨叉32转动连接,所述第一转动件321、第二转动件322、第三转动件323和第四转动件324的转动轴线的延长线相交于同一交点,所述同一交点位于第一同步器的转动轴线上,所述第一转动件321的转动轴线和所述第二转动件322的转动轴线位于第一平面,所述第三转动件323的转动轴线和所述第四转动件324的转动轴线位于与第一平面不同的第二平面,所述第一平面和第二平面沿第一同步器的轴向方向排布。所述拨动件325为转动带326,所述转动带326的一端依次绕过第一转动件321、第二转动件322、第三转动件323和第四转动件324的外壁后与相对的另一端相接。前述转动带326可以是钢带或者皮带。具体实施时将转动带326绷紧后绕在前述四个转动件的外壁上,并使转动带326首尾相接形成一个环形。所述转动带326展开后为圆弧形。当第一转动件321和第二转动件322之间距离过长时还可以在第一转动件321和第二转动件322之间设置第五转动件,利用第五转动件在中部为转动带326提供支撑;当第三转动件323和第四转动件324之间距离过长时还可以在第一转动件321和第二转动件322之间设置第五转动件,利用第六转动件在中部为转动带326提供支撑。其中第五转动件和第六转动件可以设置多个,其数量可以根据第一转动件321和第二转动件322之间的距离或者第三转动件323和第四转动件324之间的距离来确定。前述各个转动将可以通过表面光滑的转轴与第一拨叉32转动连接。
100.采用前述结构后,当转动带326随第一拨叉32移动到与同步器接触的位置时,转动带326在同步器的带动下转动,转动带326的转动方向如图8至图10中的箭头方向所示。当转动带326刚与同步器接触的初期,转动带326和同步器之间会有滑动摩擦,当转动带326与同步器转速相同后,转动带326和同步器之间没有相对滑动,不会产生滑动摩擦而导致转动带326和同步器磨损,这时转动带326在同步器的带动下依次绕四个转动件循环转动,而转动带326与同步器接触的方式为面接触,不易出现受力过于集中的情况,且转动带326则始终能与同步器同步转动。
101.本实施例还提供另外一种解决前述滑动摩擦问题的实施方式。所述第一拨叉32还包括多组转动组件,每组转动组件包括第七转动件、第八转动件和转动带326、所述第七转动件、第八转动件与所述第一拨叉32转动连接,所述转动带326的一端依次绕过第七转动件、第八转动件的外壁后与相对的另一端相接。其中第七转动件、第八转动件转轴7相互平行。所述第八转动件和第九转动件为轴对称设置,其对称轴作为转动组件的对称轴,各组转动组件的对称轴的延长线相较于同一个交点,所述交点位于第一同步器的转动轴线上。
102.每组转动组件形成一个小的转动单元,每组转动组件的转动带326可以绕四个转动件循环转动。由于转动组件的对称轴的延长线位于第一同步器的转动轴线上,因此当转
动带326随第一拨叉32移动到与同步器接触的位置时,各个转动组件的转动带326的转动方向与同步器上对应位置的转动方向几乎相同,各个转组件的转动带326的与同步器的滑动摩擦很小。采用前述方式,结构简单,各个转动组件之间可以平行设置,方便安装,既实现了面接触,又减小的滑动摩擦。
103.本实施例的变速器四挡换挡装置可以利用电机6驱动换挡鼓1转动,当换挡鼓1的换挡区111转动至与第一驱动机构3连接的位置时,换挡区111可以随换挡鼓1转动而通过第一驱动机构3推动第一同步器进行其中两个档位的挂挡操作;当换挡鼓1的换挡区111转动至与第二驱动机构5连接的位置时,换挡区111可以随换挡鼓1转动而通过第二驱动机构5推动第二同步器4进行另外两个档位的挂挡操作;由于第一驱动机构3和第二驱动机构5与换挡鼓1连接的区域处于不同的角位置,因此只需要一个换挡鼓1两个驱动机构就可以分别进行两个挡位的挂挡,前述四个挡位的挂挡操作只需要一个电机6驱动一个换挡鼓1转动就可以完成,因此换挡的执行机构少,挂挡动作简单,操作更加可靠。
104.实施例3
105.请参见图12至图18,本发明实施例3还公开了一种位于车辆传动系统内的传动法兰,该传动法兰主要包括法兰主体410、第一传动结构420、第一连接结构430和第二传动结构440;
106.其中所述第一传动结构420设置在所述法兰主体410上,所述第一传动结构420用于与变速器输出轴连接并将变速器输出轴的扭矩传递给法兰主体410;
107.如图13和图15所示,变速器的输出轴通过第一传动结构420与法兰主体410形成连接,当变速器的输出轴转动时,变速器的输出轴的扭矩作用在第一传动结构420上,并通过第一传动结构420带动法兰主体410一同转动,是输出轴的转动和扭矩都传递到法兰主体410上。
108.其中所述第一连接结构430设置在所述法兰主体410上,所述第一连接结构430用于使法兰主体410与传动轴形成连接;
109.在本实施例中第一连接结构430至起到连接作用,第一连接结构430通过将法兰主体410与传动轴连接,避免传动轴与法兰主体410松脱。
110.第二传动结构440,所述第二传动结构440设置在法兰主体410朝向传动轴的一端,所述第二传动结构440用于将法兰主体410的扭矩传递给所述传动轴,并防止扭矩传递至所述第一连接结构430。
111.当法兰主体410在变速箱输出轴的驱动下转动时,法兰主体410的扭矩通过第二传动结构440传递给所述传动轴。在法兰主体410驱动传动轴转动的过程中,第二传动结构440负责承受传动的扭矩。并且第二传动结构440还用于防止扭矩被传递至第一连接结构430,这样在法兰将扭矩传递给传递轴的过程中,第一连接结构430不会受到扭矩的作用,因此不容易损坏,可以保证第一连接结构430始终能够将法兰主体410和传动轴进行连接,从而提高了法兰连接的安全性,并且可以适少第一连接结构430的数量从而简化结构降低成本。
112.作为一种优选的实施方式,在本实施例中,所述第二传动结构440为矩形齿,所述矩形齿设置在法兰主体410与传动轴连接的端面上,所述法兰主体410上的矩形齿用于与所述传动轴上的矩形齿配合传递扭矩。
113.其中矩形齿为长条形,矩形齿的截面为矩形。在本实施例中,传动轴上可以设置与
法兰主体410上的矩形齿向配合的矩形齿。法兰主体410与传动轴安装连接后,法兰主体410的端面与传动轴配合,法兰主体410上的矩形齿与传动轴上的矩形齿嵌合在一起。当法兰主体410转动时,法兰主体410上的矩形齿与其相邻的传动轴上的矩形齿相接触,法兰主体410上的矩形齿推动与其相邻的传动轴上的矩形齿,使所述传动轴与所述法兰主体410一起转动。可以直接通过铣削直接在法兰主体410的端面加工出矩形齿。为了在实现矩形齿承受扭矩的同时,使法兰结构更加简单,所述矩形齿由相邻的两条齿槽形成,所述齿槽由法兰主体410端面朝远离传动轴的方向凹陷形成。采用前述结构来形成矩形齿可以使矩形齿的顶部与法兰主体410的端面平齐,因此不会占用多余的空间,并且只需要在原有法兰主体410直接去除材料形成齿槽即可。这样形成的矩形齿与法兰主体410为一体式结构,对原来的法兰主体410影响小。整体结构简单,承载能力强。
114.在本实施例中,所述第一连接结构430通过第一连接件与所述传动轴连接;在法兰转动方向上,所述第一连接件与所述第一连接结构430之间的配合间隙大于所述法兰主体410上的矩形齿和所述传动轴上的矩形齿之间的配合间隙。
115.由于在法兰转动方向上,所述第一连接件与所述第一连接结构430之间的配合间隙大于所述法兰主体410上的矩形齿和所述传动轴上的矩形齿之间的配合间隙,法兰传动时,在第一连接件与所述第一连接结构430接触受力前,法兰主体410上的矩形齿就先与所述传动轴上的矩形齿接触,由于传动轴上的矩形齿的阻挡,第一连接件与所述第一连接结构430始终留有配合的间隙,这样就可以很好的避免第一连接结构430和第一连接件在传动时扭矩作用。前述第一连接件可以采用螺栓,第一连接结构430可以采用螺栓孔,在法兰主体410与所述传动轴连接时,所述螺栓穿过螺栓孔。
116.在本实施例中,所述法兰主体410上设置有多组传动结构组,每组传动结构组包括若干个相互平行设置的第一传动结构420,所述第一连接结构430的数量与所述传动结构组的数量相同,且第一连接结构430与所述传动结构组一一对应,所述传动结构组用于防止扭矩传递至与其相对应的第一连接结构430上。
117.如图16所示,本实施例可以沿法兰主体410的周向方向设置多个第一连接结构430,以提高连接的可靠性。此外,本实施例采用传动结构组与第一连接结构430一一对应的设置方式。使每一个第一连接结构430均有相应的传动结构组进行保护,保证相对应的第一连接结构430和传动结构组中,传动结构组优选于第一连接结构430承受扭矩,避免了设置多个第一连接结构430时,无法保证所有第一连接结构430均不会受到扭矩作用的问题。其中每一组传动结构组可以设置多个相互平行设置的第一传动结构420。在传动时,同一组中的各个第一传动结构420可以共同承受扭矩。这样作用在法兰上的扭矩被分散到各个传动结构组后又进一步被分散到各个第一传动结构420上,使每个第一传动机构所承受的扭矩变小,而整体所能承受的扭矩则变大。
118.此外,在转动方向上,第一连接结构430位于其所对应的传动结构组的中心位置。采用前述方式可以使法兰主体410无论正转还是反转,传动结构组中的每一个第一传动结构420均能在第一连接结构430与第一连接件接触之前受到扭矩作用,从而保证扭矩不会传递给第一连接结构430。
119.例如可以在法兰主体410上设置6组传动结构组,每一组传动结构组设置4个矩形齿。这4个矩形齿相互平行,且以与这四个矩形齿相平行的法兰主体410的直径为对称轴对
称设置。而与该组矩形齿相对应的第一传动结构420则设置在该组对称轴上。其中6组传动结构组沿法兰主体410的周向方向均匀分布,即6组传动结构组中任意相邻两组传动结构组之间的间隔的角度相同,相邻两组之间间隔60度。可以理解的是前述传动组的数量和每组传动结构组中第一连接结构430的数量也可以采用其它的数量,在此不做限制。
120.本实施例可以在一组传动结构组中采用多个相互平行的矩形齿,且每个矩形齿的长度与法兰主体410端面的径向尺寸相同。采用前述方式可以在不增加每组矩形齿数量的情况下,进一步增加每一组传动结构组所能承受扭矩的能力。
121.如图15所示,在本实施例中,所述法兰主体410包括圆柱形的第一连接部411和圆盘形的第二连接部412,所述第一连接部411和第二连接部412沿法兰主体410的轴向方向排布,所述第一连接部411上设置有贯穿所述连接部的通孔,所述第一传动结构420为花键,所述花键设置在第一连接部411的通孔上,所述第一连接结构430设置在第二连接部412上。
122.当第一连接结构430采用矩形齿时,矩形齿设置在第二连接部412朝向传动轴的圆盘面上。
123.在本实施例中,第一连接部411用于实现法兰主体410与变速器输出轴的连接,而第二连接部412用于实现法兰主体410与传动轴的连接。本实施例通过采用第一连接部411和第二连接部412沿法兰主体410的轴向方向排布的方式,使变速器输出轴传动轴紧凑地分布在法兰轴向方向的两侧,这样可以避免动力输入侧和动力输出侧之间相互影响。
124.本实施例在动力输入侧采用花键进行传动,传动的承载能力强。可以先在第一连接部411加工出通孔,然后在通过内壁上加工出花键。
125.在本实施例中,所述第二传动结构440沿第二连接部412的径向方向由通孔内壁位置延伸至第二连接部412的外壁位置。采用这种方式可以充分利用第二连接部412圆盘的径向尺寸,使可以承受扭矩的矩形齿的长度最长。
126.当矩形齿长度较长时,矩形齿在扭矩作用下的形变量会增加,当形变量超过一定程度后,同一个矩形齿与其配合的矩形齿接触不充分是会使矩形齿的承载能力下降。对此,在本实施例中,每个矩形齿由多个长度较小的子矩形齿组成,相邻两个子矩形齿之间断开。采用前述方式后各个子矩形齿的变形不会累累加到其它子矩形齿上,从而使矩形齿的变形量可以分散到各个子矩形齿,则各个子矩形齿的变形量都很小,不会超过可以引起矩形齿接触不充分的程度。相邻子矩形齿断开的间隙可以很小,因此采用前述结构也不会明显减少矩形齿可以承受扭矩的部位的长度。
127.如图18所示,在本实施例中,每组传动结构组由两组子传动结构组组成,分别为第一子传动结构组441和第二子传动结构组442。两组子传动结构组中矩形齿的数量,截面形状,排布间隔均相等,只是两组子传动结构组在周向方向上相互错开,每个矩形齿也被分成了两个相互断开的部分,且分属于两组子传动结构组。采用前述方式可以在不减少矩形齿用于承载扭矩部分的总长度的情况下,减少矩形齿的变形量。两组子传动结构组在周向方向上相互错开后,法兰主体410的受力不会集中在法兰主体410的同一周向位置,法兰主体410的形变也被分散到了法兰主体410周向方向的各个位置上。
128.其中第一子传动结构组441中每个矩形齿的一端均延伸至法兰主体410的外壁位置,这样铣刀可以有法兰主体410的外侧向内侧一次性去除材料完成对矩形齿的加工,这样可以显著提高加工效率。
129.在周向方向上第一子传动结构组441和第二子传动结构组442可以完全错开,也可以不完全错开。在采用完全错开的方式时,第一子传动结构组441和第二子传动结构组442在径向方向上部分交叠。法兰主体410上第一子传动结构组441和第二子传动结构组442断开的部位无法承受扭矩,第一子传动结构组441和第二子传动结构组442靠近断开位置的部位受力也会发生陡变,这些都会对法兰的使用寿命造成影响。而第一子传动结构组441和第二子传动结构组442在径向方向上部分交叠后,消除了原来法兰主体410在径向方向上由于径向齿断开而产生的不能承受扭矩的部分,避免的第一子传动结构组441和第二子传动结构组442靠近断开位置的部位受力发生陡变。
130.采用不完全错开的方式时,可以使第一子传动结构组441中矩形齿的齿槽和第二子传动结构组442中矩形齿的齿顶对齐。采用前述方式可以使同一组传动结构组中,法兰主体410周向方向上用于承载扭矩的部分最多,这样可以使法兰主体410所能承受的扭矩更多。
131.如图17所示,在本实施例中同一个传动结构组由三组子传动结构组组成,由法兰主体410的外壁向内分别依次为第三子传动结构组443、第四子传动结构组444和第五子传动结构组445。每组传动结构组的矩形齿之间相互断开,且第三子传动结构组443的矩形齿的长度小于第四子传动结构组444,第四子传动结构组444的矩形齿的长度小于和第五子传动结构组445的矩形齿长度。在承受相同扭矩的情况下,法兰主体410外侧变形量比其内侧大,本实施例采用前述由内至外矩形齿长度变短的结构,可以使法兰主体410各个径向位置的矩形齿的变形量的方差减小,避免法兰主体410径向方向上局部位置矩形齿的变形量过大而影响法兰的使用寿命。
132.如图14所示,在本实施例中,所述第二连接部412上设置有与所述传动轴配合的限位孔4121,所述限位孔4121朝向第一连接部411的一端设置有用于限制传动轴轴向位置的止口4122,所述花键延伸至所述止口4122的位置。
133.在安装时,传动轴的端部可以插入第二连接部412的限位孔4121中,直至传动轴的端部与所述止口4122抵接。而变速箱的输出轴则可以插入到通孔中。由于通孔中的花键延伸到止口4122位置,因此输入端传递扭矩的位置与传动轴端部距离较短。采用前述方式可以使输入端传递扭矩的位置和输出端的传动扭矩的位置之间的距离缩短,从而减少输入端和输出端之间传动部件在扭矩作用下的变形量。
134.实施例4
135.请参考图19至图22,作为本发明的一个目的,在车辆内还包括一种多功能减速器,其包括供油系统10、润滑系统20、驻车系统30和油路通断装置40,其中,供油系统10用于可调节地供应润滑油,润滑系统20与供油系统10相连接并通过接收润滑油以实施润滑模式,驻车系统30与供油系统10相连接并通过接收或排出润滑油以对应地实施或解除驻车模式,油路通断装置40设置于供油系统10分别与润滑系统20和驻车系统30的两者之间,相当于,润滑系统20和驻车系统30并列地与油路通断装置40相连接,从而使供油系统10选择性地向润滑系统20或者驻车系统30供油,也就是说,在多功能减速器通过例如用户对汽车控制台手动操控或者汽车驾驶软件自动运行来对油路通断装置40进行控制下,当执行实施润滑模式时,润滑油供应至润滑系统20更进一步来说可以是供应至润滑系统20的流经传动机构的润滑油管道(以下将作进一步说明),当执行实施驻车模式或者解除驻车模式时,润滑油通
过供应至驻车系统30从而为驻车系统30提供液压力来实现驻车模式或者通过将部分的润滑油从驻车系统30排出从而撤销对驻车系统30提供的液压力来解除驻车模式。这样的话,由于在多功能减速器中,只需设置一个供油系统10就可对其中的驻车系统30和润滑系统20选择性地供应润滑油,从而实现多功能减速器集成了驻车、解除驻车和润滑多种功能,并且,利用对供油系统10中润滑油供应至驻车系统30的排出即可解除驻车功能,因此,多功能减速器为具有高整合度的整体系统,不仅成本降低、整体系统简化,还制造和安装方便,并且,利用对油路通断装置40的控制来选择润滑油的流向可以简化控制方式且提高智能化。
136.请进一步参考图19和图20,在一种实施例中,供油系统10包括存储润滑油的润滑油腔(未图示)、驱动电机110、控制驱动电机110工作的电机控制器120和接收驱动电机110驱动力以将润滑油腔中的润滑油进行循环泵油的润滑油泵130,因此,利用电机控制器120接收的控制指令来控制润滑油泵130的例如转动方向、转速、转动时长等,该控制指令可以是来自外部处理器也可以是电机控制器120自身接收传感器信号所生成,以下对于阀控制器等也作同样理解。可知的是,润滑油泵130可以通过泵体的正反转来改变泵油的方向和通过泵体的转速快慢来改变泵油的单位时间油量,达到所预期的润滑功能、驻车功能及解除驻车功能,以下如无特别说明,泵油量均指单位时间内流经或流出润滑油泵130的油量。
137.在一种实施例中,油路通断装置40包括阀控制器(未图示)和电磁阀41,电磁阀41具体可为两位两通电磁阀,电磁阀41包括第一阀门41a和第二阀门41b,阀控制器控制第一阀门41a和第二阀门41b分别与润滑系统20和驻车系统30的通断,这样的话,对于润滑系统20和驻车系统30分别与供油系统10之间的两油路,在阀控制器控制第一阀门41a和第二阀门41b开启和关闭下,相应油路连通或者阻断,并且在控制开启时还可以通过周期性地开启和关闭,能够精准控制油路中润滑油的流速和流量,从而确保润滑系统20和驻车系统30均准确获得预设值的润滑油。
138.在一种实施例中,润滑系统20包括润滑油管道和传动机构(未图示),润滑油经润滑油管道流经传动机构,传动机构包括传递动力电机驱动输出轴的驱动力的各个齿轮及轴承。驻车系统30包括设有液压杆310的液压缸320、用于探测液压杆310位移的位移传感器330和接收液压杆310的驻车力的驻车机构(未图示),该位移传感器330可探测液压杆310在液压缸320中位移的方向及距离从而准确确定液压杆310在液压缸320中的位置,驻车机构包括例如可在液压杆310的作用力作用下相互啮合以及在作用力撤除后相互脱离的棘轮和齿槽,关于驻车机构的具体结构为本领域技术人员所知晓,在此不再赘述,由上所述,利用对润滑油流经传动机构的油量控制能够确保在各种工况下传动机构均获得良好的润滑和导热的技术效果,且相对于液压缸320,利用控制润滑油的流入或者流出的润滑油量从而相应地使液压杆310移出或者移入相应距离,确保了驻车机构接收来自液压杆310的足够作用力而锁定或者无法获得液压杆310的作用力而解锁,从而获得可靠的驻车状态和非驻车状态。
139.在一种实施例中,驻车系统30包括动力电机,多功能减速器还包括用于探测动力电机的工作温度的温度传感器(未图示),在润滑模式下,阀控制器控制开启第一阀门41a且关闭第二阀门41b,则润滑系统20与供油系统10的循环油路处于连通状态且驻车系统30与供油系统10的循环油路处于非连通状态,且电机控制器120根据温度传感器探测到的温度数值控制驱动电机110的转速,从而驱动润滑油泵130以第一泵油量向润滑系统20供油,从
而在润滑油泵130的泵油工作下,润滑油被循环供应至传动机构,并且经过传动机构后起到了润滑和吸热的润滑油进一步流至润滑油腔从而得到冷却。在驻车模式下,阀控制器控制开启第二阀门41b且关闭第一阀门41a,则驻车系统30与供油系统10的循环油路处于连通状态且润滑系统20与供油系统10的循环油路处于非连通状态,且电机控制器120根据位移传感器330探测到的位移数值控制驱动电机110在第一方向转动的转速,从而驱动润滑油泵130以第二泵油量向液压缸320供油,并且,当位移数值等于位移阈值时,位移阈值可以根据实际情况而设定并存储于例如与电机控制器120和阀控制器相连接的cpu、plc等处理器的存储模块中,另外,以下将描述的转速阈值可作同样的理解。阀控制器控制关闭第二阀门41b且电机控制器120控制驱动电机110关停,也就是液压杆310运动至预设位置以施加足够作用力即驻车力于驻车机构来完成驻车操作后,第二阀门41b关闭以保持液压缸320中的润滑油填充量从而维持提供给液压杆310的液压力,并且润滑油泵130停止工作,润滑系统20在驻车状态下无需工作。因此,多功能减速器能在高可靠及高智能化的控制下实现润滑功能和驻车功能。
140.在一种实施例中,位移数值为位移传感器330所探测到液压杆310向着移出液压缸320方向移动的距离,第一泵油量随着温度数值的增减而增减,具体来说,第一泵油量=温度数值
×
温度系数,其中,温度系数大小与润滑系统20的润滑油管道的尺寸、传动机构中需润滑部件的多少、驱动电机110的功率等参数有关,本领域技术人员可以根据实际情况而选择合适的温度系数,在本实施例中,第一泵油量的最大值为18l/min,驱动电机110的最大转速为6000rpm/min,第二泵油量随着位移数值的增大而减小,这样的话,由于动力电机的工作温度随传动机构的各传动部件间摩擦力的增减而升降,因此,第一泵油量针对温度数值而调整,确保了润滑系统20的传动机构获得良好润滑并且动力电机的工作温度不会过热从而保证动力电机的正常工作和长寿命;第二泵油量设置为随着液压杆310向着移出液压缸320方向移动而持续施加驻车力的过程而递减,实现了根据驻车距离大小来控制驱动电机110,驻车距离越远则第二泵油量越大从而液压杆310移动越快,驻车距离越近则第二泵油量越小从而液压杆310移动越慢,这样既在一定程度上减少了驻车时长又避免了在驻车过程中接近驻车点时由于司乘人员的行驶惯性所带来的身体前倾或摇晃的不适。
141.在一种实施例中,多功能减速器还具有解除驻车模式,在解除驻车模式下,液压杆310向着移入液压缸320方向移动,移入的停止位置根据实际情况而设定,可知的是,该停止位置即为液压杆310的初始位置也对应于位移数值的零点值,阀控制器控制开启第二阀门41b且关闭第一阀门41a,且电机控制器120根据位移传感器330探测到的位移数值控制驱动电机110在与第一方向相反的第二方向上的转速,从而驱动润滑油泵130以第三泵油量将液压缸320中润滑油排出并向润滑油腔回流润滑油,第三泵油量随着位移数值的减小而增大,根据以上对驻车模式的相关描述,在解除驻车模式过程中,液压杆310受外力作用向着移入液压缸320方向移动并且随着液压杆310的移动距离越大即位移数值越小则第三泵油量越大从而液压杆310的移动速度越快,因此,在解除驻车模式的初始阶段,对驻车机构缓慢解除驻车力,既确保可靠地解除驻车又避免了驻车机构受到突变的作用力而影响刚性强度,而在初始阶段之后,液压杆310的移动速度逐步加快,从而一定程度上减少了解除驻车模式的耗时。
142.在一种实施例中,多功能减速器还包括用于探测动力电机的工作转速的转速传感
器,当工作转速达到转速阈值时,阀控制器始终控制关闭第二阀门41b,当工作转速低于转速阈值时,驻车模式才可实施。这样的话,当装配了多功能减速器的汽车接受动力电机的驱动力使得车速大于某一阈值时,关闭的第二阀门41b阻止润滑油进入液压缸320,驻车机构无法获得液压杆310的驻车力,驻车模式无法实施,从而确保多功能减速器及装配其的汽车的安全运行。
143.请进一步参考图21和图22,作为本发明的又一个目的,提供了一种多功能减速器的控制方法,对于该多功能减速器,请参照上文的具体描述,在此不再赘述,以下重点对控制方法进行描述。
144.该多功能减速器具有润滑模式和驻车模式,控制方法包括:
145.s10:判断多功能减速器是否进入润滑模式或者驻车模式?
146.s20:判断进入润滑模式,则控制油路通断装置40开启润滑系统20与供油系统10之间的油路并关闭驻车系统30与供油系统10之间的油路;
147.s30:判断进入驻车模式,则控制油路通断装置40关闭润滑系统20与供油系统10之间的油路并开启驻车系统30与供油系统10之间的油路。
148.由上所述,多功能减速器的控制方法利用对一个供油系统10和一个油路通断装置40的控制,就能使供油系统10选择性地向润滑系统20供油从而实现润滑模式以及对于驻车系统30供油和排油来分别实现驻车模式和解除驻车模式,因此,控制方法具有控制方式简化及智能化高的优点。
149.在一种实施例中,控制方法还包括:
150.判断进入润滑模式步骤s20进一步包括:控制阀控制器开启第一阀门41a且关闭第二阀门41b,且电机控制器120根据温度传感器所探测到的温度数值计算得出转速并按此控制驱动电机110的转动,从而驱动润滑油泵130以第一油量向润滑系统20供油,优选的,第一泵油量随着温度数值的增减而增减;
151.在判断进入驻车模式步骤s30后进一步包括:控制阀控制器开启第二阀门41b且关闭第一阀门41a,且电机控制器120根据位移传感器330所探测到的位移数值控制驱动电机110在第一方向转动的转速,从而驱动润滑油泵130以第二泵油量向液压缸320供油,优选的,第二泵油量随着位移数值的增大而减小,当位移数值达到位移数值时,控制阀控制器关闭第一阀门41a和第二阀门41b且控制电机控制器120关停驱动电机110。
152.由上所述,多功能减速器的控制方法控制阀控制器对第一阀门41a和第二阀门41b的开启和关闭进行控制,确保了润滑系统20和驻车系统30的其中一个与供油系统10相连通并准确获得预设值的润滑油和在完成驻车模式后润滑系统20和驻车系统30均不与供油系统10相连通,并且,多功能减速器控制方法还根据温度数值控制驱动电机110的转动来使润滑系统20获得所需的润滑油量,以及根据位移数值控制驱动电机110的转动来使驻车系统30获得优选为变流速的流入或排出的润滑油量,从而保障了润滑功能和驻车功能的可靠实现。
153.在一种实施例中,多功能减速器还包括用于探测动力电机的工作转速的转速传感器,判断进入驻车模式步骤s30还进一步包括:步骤s31:判断是否允许实施驻车模式,比较工作转速与转速阈值,步骤s31
‑
1:当工作转速大于等于转速阈值时,则不允许实施驻车模式,且阀控制器始终控制关闭第二阀门41b;步骤s31
‑
2:当工作转速低于转速阈值时,则允
许实施驻车模式,多功能减速器还具有解除驻车模式,多功能减速器的控制方法还进一步包括:步骤s40:判断进入解除驻车模式,且进一步的,步骤s41:判断是否允许实施解除驻车模式,比较位移数值与位移阈值,步骤s41
‑
1:当位移数值小于位移数值时,则不允许实施解除驻车模式,步骤s41
‑
2:当位移数值达到位移数值时,则允许实施解除驻车模式,并且在实施解除驻车模式时,在液压杆310的向着移入液压缸320方向移动下,控制阀控制器开启第二阀门41b且关闭第一阀门41a,且控制电机控制器120根据位移传感器330探测到的位移数值对驱动电机110施加在与第一方向相反的第二方向上的转速,从而驱动润滑油泵130以第三泵油量将液压缸320中润滑油排出并向润滑油腔回流润滑油,优选的,该第三泵油量随着位移数值的减小而增大。
154.由上所述,多功能减速器控制方法还根据工作转速与转速阈值的比较结果确定是否允许进入驻车模式并进行相应控制以及根据位移数值与位移阈值的比较结果确定是否允许进入解除驻车模式驻车模式并进行相应控制,因此,既能够避免车速较快时进行驻车而给安全行车带来的隐患,还确保了解除驻车模式在驻车模式实施后才能进行且解除过程可靠和准确。
155.实施例5
156.本发明实施例5公开了一种车辆,该车辆包括上述的抑制形变的变速器壳体和/或变速器和/或变速器四挡换挡装置和/或传动法兰和/或多功能减速器。
157.发明实施例5中车辆可以是传统燃油汽车例如汽油车,柴油车等,也可以是新能源汽车。其中新能源汽车包括但不限于纯电(bev/ev)车、混合动力(hev、phev和reev)车、燃料电池车(fcev)、太阳能电池车。
158.最后应说明的是:以上各实施例仅用以说明本发明的技术方案,而非对其限制;尽管参照前述各实施例对本发明进行了详细的说明,本领域的普通技术人员应当理解:其依然可以对前述各实施例所记载的技术方案进行修改,或者对其中部分或者全部技术特征进行等同替换;而这些修改或者替换,并不使相应技术方案的本质脱离本发明各实施例技术方案的范围。