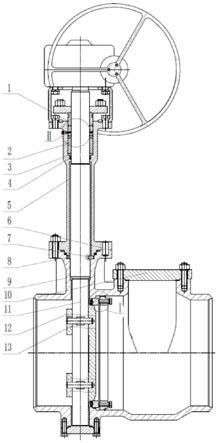
1.本发明涉及蝶阀技术领域,特别涉及一种超低温双偏心硬密封结构。
背景技术:2.lng液化天然气储运装备国产化的展开,使得lng离不开一个关键的词:超低温。液化天然气(lng)的储存和运输温度为
‑
162℃;空气分离中氧的沸点为
‑
183℃,氮为
‑
196℃,氢为
‑
253℃;在深冷技术方面有些要求温度可能更低,并且低温介质有其特殊性,通常为易燃、易爆物质,或者是稀有物质,所以对于它们的泄漏要求都非常高。于是对超低温蝶阀的需求不断增加,密封性能也提出了更高要求。
3.传统的硬密封蝶阀其密封形式大多采用传统的三偏心密封结构,但三偏心蝶阀的加工工装多,加工工艺较为复杂,装配及检修难度相对较高,加工成本较高。而双偏心蝶阀加工、装配工艺较为简单,成本更低,现场检修方便,因此使得国内外企业选择采用双偏心蝶阀居多。
4.但目前国内外双偏心硬密封蝶阀的压力有pn系列pn10、pn16、pn25,class 150等几个规格,却鲜有压力为class 300、class 600、pn63、pn100的双偏心硬密封蝶阀,为此,需要设计或提供新的密封结构来有效解决现有技术中蝶阀不适用中高压力的问题。
技术实现要素:5.本发明目的之一是解决现有技术中超低温双偏心硬密封蝶阀不适用中高压力的问题。
6.本发明目的之二是提供一种具有超低温双偏心硬密封结构的蝶阀。
7.本发明目的之三是提供一种超低温双偏心硬密封方法。
8.为达到上述目的之一,本发明采用以下技术方案:一种超低温双偏心硬密封结构,其中,包括:阀体、阀杆、蝶板、金属阀座、阀座压环。
9.所述阀体内开设有空腔,所述阀杆与所述蝶板设置在所述阀体的空腔中,所述阀杆与所述蝶板相连。
10.所述金属阀座置于所述阀体与所述蝶板之间,所述金属阀座包括有:c形圈、环形弹簧、支撑环、软态板(软态铜板)。所述环形弹簧安装在所述c形圈的内侧面,所述支撑环与所述阀体相连或紧密接触。所述软态板(软态铜板)以包裹所述支撑环头端的一端为起点,延伸并包裹内外的两c形圈外侧面,使得外侧面的软态板形成一整体。
11.所述c形圈、环形弹簧和所述软态板形成内外层两密封圈,所述支撑环设置在该内外层的密封圈之间。
12.所述阀座压环设置在所述阀体的空腔中,所述阀座压环置于所述金属阀座的一侧,通过所述阀座压环对所述金属阀座施加预紧压力。
13.在上述技术方案中,本发明实施例在低温工作时,当金属阀座中的支撑环受阀体内压力的挤压后,c型圈、环形弹簧、软态板构成的密封圈产生形变,同时支撑环会靠近深入
金属阀座内部,而包裹在支撑环上的铜板随着支撑环的深入而被进一步收紧;
14.其中,c型圈的变形空间由c型圈自身结构形成的开口补偿,从而使密封位置金属密封面的变形是平顺的,可自行吸收的,可预期的,有效地保证了在中高压下蝶阀的密封性能;
15.并且金属阀座外密封圈与阀体进行台阶配合,台阶高度控制外密封圈的最大压缩量,有效地避免了外密封圈受力过大而产生破坏,内密封圈处在由阀座压环、阀体和支撑环共同限定密封位置,使得密封位置可靠,受力均匀,保证了中高压下蝶阀的密封性能。
16.进一步地,在本发明实施例中,所述软态板为铜制,所述金属阀座包括有环形弹簧、c形圈、支撑环及软态板共同复合加工而成。
17.进一步地,在本发明实施例中,所述环形弹簧为密圈弹簧,c形圈开口均向支撑环方向,两c形圈之间的软态板具有凸起,所述支撑环头端为进入所述阀座压环凹槽的挤入端,该挤入端具有导入斜面和/或圆角,所述支撑环经挤压嵌入所述阀座,并对所述环形弹簧施加有预紧力,且所述支撑环未挤入端高于c形圈端面,所述支撑环挤入端被所述软态板包裹。通过软态板凸起与支撑环、阀座压环凹槽的配合,使得在压力下时,三者能够靠近嵌合,防止外力作用下金属阀座中的部件发生侧位移动,影响密封性能。
18.更进一步地,在本发明实施例中,所述阀座压环的凹槽与所述金属阀座上的凸起软态板配合且预留有间隙,该间隙为密封时的所述金属阀座受挤压变形而产生较大凸起而预留的空间。
19.更进一步地,在本发明实施例中,所述环形弹簧材质为inconel x750,所述c形圈材质为奥氏体不锈钢或inconel x750,所述支撑环为高强度合金,且所述支撑环线收缩系数大于等于所述环形弹簧材料的线收缩系数。在低温条件下支撑环提供的预紧力不会变小,并且能限制高压状态下环形弹簧的径向变形,使弹簧提供更大的密封比压,实现高压力下的密封。
20.进一步地,在本发明实施例中,所述阀杆与所述蝶板用滑动销连接,所述滑动销由圆锥销加工而成,大端部为圆锥面,所述滑动销与所述阀杆接触部位均为机加工光滑平面,所述蝶板销孔为圆锥孔。滑动销即可传递扭矩,也可依靠滑动销配合过盈量来定位蝶阀密封位置,在低温状态下,阀杆与蝶阀的相对位置可微量滑动,补偿低温下各零部件收缩量的不均匀性,确保低温下金属阀座的密封性能。
21.进一步地,在本发明实施例中,所述阀座压环侧设有调整环,所述调整环上配合有螺栓,所述阀座压环通过卡圈在所述阀体空腔内进行固定定位。
22.进一步地,在本发明实施例中,所述阀体空腔上开口处设置有检修盖板,通过打开所述检修盖板,使得所述金属阀座可实现在线检修和更换。
23.本发明的有益效果是:
24.本发明在阀体与蝶板之间安置金属阀座,使得金属阀座受到阀体内压力作用后,其中的c型圈、环形弹簧、软态板构成的密封圈能够产生形变,在形变时发生的变形空间由c型圈自身结构形成的开口补偿,从而使密封位置金属密封面的变形是平顺的,可自行吸收的,可预期的,有效地保证了在中高压下蝶阀的密封性能。并且金属阀座与阀体进行的台阶配合,一方面有效地避免了外密封圈受力过大而产生破坏,另一方面限定密封位置,使得密封位置可靠,受力均匀,保证了中高压下蝶阀的密封性能。
25.本发明提供了一种密封可靠,成本较低,加工、装配、检修较为方便的中高压超低温双偏心硬密封结构(超低温双偏心硬密封蝶阀)。
26.为达到上述目的之二,本发明采用以下技术方案:一种蝶阀,其中,具有上述发明目的之一中所述的超低温双偏心硬密封结构。
27.进一步地,在本发明实施例中,所述阀体上连接有填料盖,所述填料盖与所述阀体之间通过圆柱销连接,所述阀杆上端穿入至所述填料盖。
28.更进一步地,在本发明实施例中,所述阀杆上开设有卡槽,所述限位块为90
°
扇形块,所述限位块安装在所述阀杆卡槽内,与填料盖上90
°
的扇形块配合作用。确保阀杆在90
°
范围内旋转,即防止由于蝶板开关造成的金属阀座过度挤压而产生永久变形,又确保蝶板始终在正确的密封位置,密封可靠,填料盖与阀体连接处设计有圆柱销定位,确保限位牢靠,不相对滑动。
29.更进一步地,在本发明实施例中,所述阀杆的密封采用蓄能圈、石墨填料、填料垫与o形圈进行组合密封,所述的填料压套内外表面即分别设有两道o形圈和紧急密封槽,内外所述紧急密封槽通过小圆孔连通,内外所述紧急密封槽分别设在两道所述o形圈密封的中间位置。紧急情况下,可通过填料盖上的螺纹孔注入液体密封材料,作紧急密封处理。
30.为达到上述目的之三,本发明采用以下技术方案:一种超低温双偏心硬密封方法,应用于上述发明目的之一中所述的超低温双偏心硬密封结构,或上述发明目的之二中所述的蝶阀,其中,包括以下步骤:
31.在低温工作时,当金属阀座中的支撑环受阀体内压力的挤压后,c型圈、环形弹簧、软态板构成的密封圈产生形变,同时支撑环会靠近深入金属阀座内部,而包裹在支撑环上的铜板随着支撑环的深入而被进一步收紧;
32.其中,c型圈的变形空间由c型圈自身结构形成的开口补偿,从而使密封位置金属密封面的变形是平顺的,可自行吸收的,可预期的,有效地保证了在中高压下蝶阀的密封性能;
33.并且金属阀座外密封圈与阀体进行台阶配合,台阶高度控制外密封圈的最大压缩量,有效地避免了外密封圈受力过大而产生破坏,内密封圈处在由阀座压环、阀体和支撑环共同限定密封位置,使得密封位置可靠,受力均匀,保证了中高压下蝶阀的密封性能。
34.进一步地,在本发明实施例中,将环形弹簧材质采用为inconel x750,c形圈材质采用为奥氏体不锈钢或inconel x750,支撑环采用为高强度合金,使得支撑环线收缩系数大于等于环形弹簧材料的线收缩系数,进而在低温条件下支撑环提供的预紧力不会变小,并且能限制高压状态下环形弹簧的径向变形,使弹簧提供更大的密封比压,实现高压力下的密封。
35.进一步地,在本发明实施例中,阀杆与蝶板用滑动销连接,滑动销大端部为圆锥面,滑动销与阀杆接触部位均为机加工光滑平面,蝶板销孔为圆锥孔,在力作用下,滑动销即可传递扭矩,也可依靠滑动销配合过盈量来定位蝶阀密封位置,在低温状态下,阀杆与蝶阀的相对位置可微量滑动,补偿低温下各零部件收缩量的不均匀性,确保低温下金属阀座的密封性能。
附图说明
36.图1为本发明实施例具有超低温双偏心硬密封结构的蝶阀结构示意图。
37.图2为本发明实施例蝶阀的ⅰ部结构放大示意图。
38.图3为图2的ⅲ部结构放大示意图。
39.图4为本发明实施例滑动销的平面示意图。
40.图5为本发明实施例限位块的俯视示意图。
41.图6为本发明实施例蝶阀的ⅱ部结构放大示意图。
42.附图中
43.1、填料压套
ꢀꢀꢀꢀꢀꢀꢀꢀꢀꢀꢀꢀꢀꢀꢀ
2、石墨填料
ꢀꢀꢀꢀꢀꢀꢀꢀꢀꢀꢀꢀꢀꢀꢀ
3、填料垫
44.4、蓄能圈
ꢀꢀꢀꢀꢀꢀꢀꢀꢀꢀꢀꢀꢀꢀꢀꢀꢀꢀ
5、填料盖
ꢀꢀꢀꢀꢀꢀꢀꢀꢀꢀꢀꢀꢀꢀꢀꢀꢀꢀ
6、圆柱销
45.7、限位块
ꢀꢀꢀꢀꢀꢀꢀꢀꢀꢀꢀꢀꢀꢀꢀꢀꢀꢀ
8、扇形块
ꢀꢀꢀꢀꢀꢀꢀꢀꢀꢀꢀꢀꢀꢀꢀꢀꢀꢀ
9、阀体
46.10、检修盖板
ꢀꢀꢀꢀꢀꢀꢀꢀꢀꢀꢀꢀꢀꢀꢀ
11、阀杆
ꢀꢀꢀꢀꢀꢀꢀꢀꢀꢀꢀꢀꢀꢀꢀꢀꢀꢀꢀ
12、蝶板
47.13、滑动销
ꢀꢀꢀꢀꢀꢀꢀꢀꢀꢀꢀꢀꢀꢀꢀꢀꢀ
14、卡圈
ꢀꢀꢀꢀꢀꢀꢀꢀꢀꢀꢀꢀꢀꢀꢀꢀꢀꢀꢀ
15、调整环
48.16、螺栓
ꢀꢀꢀꢀꢀꢀꢀꢀꢀꢀꢀꢀꢀꢀꢀꢀꢀꢀꢀ
17、阀座压环
ꢀꢀꢀꢀꢀꢀꢀꢀꢀꢀꢀꢀꢀꢀꢀ
18、金属阀座
49.19、c形圈
ꢀꢀꢀꢀꢀꢀꢀꢀꢀꢀꢀꢀꢀꢀꢀꢀꢀꢀ
20、环形弹簧
ꢀꢀꢀꢀꢀꢀꢀꢀꢀꢀꢀꢀꢀꢀꢀ
21、软态板
50.22、支撑环
ꢀꢀꢀꢀꢀꢀꢀꢀꢀꢀꢀꢀꢀꢀꢀꢀꢀ
23、o形圈
ꢀꢀꢀꢀꢀꢀꢀꢀꢀꢀꢀꢀꢀꢀꢀꢀꢀꢀ
24、螺纹孔
51.25、紧急密封槽
具体实施方式
52.为了使本发明的目的、技术方案进行清楚、完整地描述,及优点更加清楚明白,以下结合附图对本发明实施例进行进一步详细说明。应当理解,此处所描述的具体实施例是本发明一部分实施例,而不是全部的实施例,仅仅用以解释本发明实施例,并不用于限定本发明实施例,本领域普通技术人员在没有做出创造性劳动前提下所获得的所有其他实施例,都属于本发明保护的范围。
53.在本发明的描述中,需要说明的是,术语“中心”、“中”“上”、“下”、“左”、“右”、“内”、“外”、“顶”、“底”、“侧”、“竖直”、“水平”等指示的方位或位置关系为基于附图所示的方位或位置关系,仅是为了便于描述本发明和简化描述,而不是指示或暗示所指的装置或元件必须具有特定的方位、以特定的方位构造和操作,因此不能理解为对本发明的限制。此外,术语“一”、“第一”、“第二”、“第三”、“第四”、“第五”、“第六”仅用于描述目的,而不能理解为指示或暗示相对重要性。
54.在本发明的描述中,需要说明的是,除非另有明确的规定和限定,术语“安装”、“相连”、“连接”应做广义理解,例如,可以是固定连接,也可以是可拆卸连接,或一体地连接;可以是机械连接,也可以是电连接;可以是直接相连,也可以通过中间媒介间接相连,可以是两个元件内部的连通。对于本领域的普通技术人员而言,可以具体情况理解上述术语在本发明中的具体含义。
55.出于简明和说明的目的,实施例的原理主要通过参考例子来描述。在以下描述中,很多具体细节被提出用以提供对实施例的彻底理解。然而明显的是。对于本领域普通技术人员,这些实施例在实践中可以不限于这些具体细节。在一些实例中,没有详细地描述公知超低温双偏心硬密封方法和结构,以避免无必要地使这些实施例变得难以理解。另外,所有
实施例可以互相结合使用。
56.实施例一:
57.一种超低温双偏心硬密封结构,其中,如图1、2所示,包括:阀体9、阀杆11、蝶板12、金属阀座18、阀座压环17。
58.如图1所示,阀体9内开设有空腔,阀杆11与蝶板12设置在阀体9的空腔中,阀杆11与蝶板12相连。
59.如图2、3所示,金属阀座18置于阀体9与蝶板12之间,金属阀座18包括有:c形圈19、环形弹簧20、支撑环22、软态板21(软态铜板)。环形弹簧20安装在c形圈19的内侧面,支撑环22与阀体9相连或紧密接触。软态板21(软态铜板)以包裹支撑环22头端的一端为起点,延伸并包裹内外的两c形圈19外侧面,使得外侧面的软态板21形成一整体。
60.c形圈19、环形弹簧20和软态板21形成内外层两密封圈,支撑环22设置在该内外层的密封圈之间。
61.阀座压环17设置在阀体9的空腔中,阀座压环17置于金属阀座18的一侧,通过阀座压环17对金属阀座18施加预紧压力。
62.本实施例在低温工作时,当金属阀座18中的支撑环22受阀体9内压力的挤压后,c型圈、环形弹簧20、软态板21构成的密封圈产生形变,同时支撑环22会靠近深入金属阀座18内部,而包裹在支撑环22上的铜板随着支撑环22的深入而被进一步收紧。
63.其中,c型圈的变形空间由c型圈自身结构形成的开口补偿,从而使密封位置金属密封面的变形是平顺的,可自行吸收的,可预期的,有效地保证了在中高压下蝶阀的密封性能。
64.并且金属阀座18外密封圈与阀体9进行台阶配合,台阶高度控制外密封圈的最大压缩量,有效地避免了外密封圈受力过大而产生破坏,内密封圈处在由阀座压环17、阀体9和支撑环22共同限定密封位置,使得密封位置可靠,受力均匀,保证了中高压下蝶阀的密封性能。
65.如图3所示,软态板21为铜制,金属阀座18包括有环形弹簧20、c形圈19、支撑环22及软态板21共同复合加工而成。
66.如图3所示,环形弹簧20为密圈弹簧,c形圈19开口均向支撑环22方向,两c形圈19之间的软态板21具有凸起,支撑环22头端为进入阀座压环17凹槽的挤入端,该挤入端具有导入斜面和/或圆角,支撑环22经挤压嵌入阀座,并对环形弹簧20施加有预紧力,且支撑环22未挤入端高于c形圈19端面,支撑环22挤入端被软态板21包裹。通过软态板21凸起与支撑环22、阀座压环17凹槽的配合,使得在压力下时,三者能够靠近嵌合,防止外力作用下金属阀座18中的部件发生侧位移动,影响密封性能。
67.如图3所示,阀座压环17的凹槽与金属阀座18上的凸起软态板21配合且预留有间隙,该间隙为密封时的金属阀座18受挤压变形而产生较大凸起而预留的空间。
68.环形弹簧20材质为inconel x750,c形圈19材质为奥氏体不锈钢或inconel x750,支撑环22为高强度合金,且支撑环22线收缩系数大于等于环形弹簧20材料的线收缩系数。在低温条件下支撑环22提供的预紧力不会变小,并且能限制高压状态下环形弹簧20的径向变形,使弹簧提供更大的密封比压,实现高压力下的密封。
69.如图1、4所示,阀杆11与蝶板12用滑动销13连接,滑动销13由圆锥销加工而成,大
端部为圆锥面,滑动销13与阀杆11接触部位均为机加工光滑平面,蝶板12销孔为圆锥孔。滑动销13即可传递扭矩,也可依靠滑动销13配合过盈量来定位蝶阀密封位置,在低温状态下,阀杆11与蝶阀的相对位置可微量滑动,补偿低温下各零部件收缩量的不均匀性,确保低温下金属阀座18的密封性能。
70.如图2所示,阀座压环17侧设有调整环15,调整环15上配合有螺栓16,阀座压环17通过卡圈14在阀体9空腔内进行固定定位。
71.如图1所示,阀体9空腔上开口处设置有检修盖板10,通过打开检修盖板10,使得金属阀座18可实现在线检修和更换。
72.实施例二:
73.一种蝶阀,其中,如图1所示,具有上述实施例一中的超低温双偏心硬密封结构。
74.阀体9上连接有填料盖5,填料盖5与阀体9之间通过圆柱销6连接,阀杆11上端穿入至填料盖5。
75.如图1、5所示,阀杆11上开设有卡槽,限位块7为90
°
扇形块8,限位块7安装在阀杆11卡槽内,与填料盖5上90
°
的扇形块8配合作用。确保阀杆11在90
°
范围内旋转,即防止由于蝶板12开关造成的金属阀座18过度挤压而产生永久变形,又确保蝶板12始终在正确的密封位置,密封可靠,填料盖5与阀体9连接处设计有圆柱销6定位,确保限位牢靠,不相对滑动。
76.如图1、6所示,阀杆11的密封采用蓄能圈4、石墨填料2、填料垫3与o形圈23进行组合密封,的填料压套1内外表面即分别设有两道o形圈23和紧急密封槽25,内外紧急密封槽25通过小圆孔连通,内外紧急密封槽25分别设在两道o形圈23密封的中间位置。紧急情况下,可通过填料盖5上的螺纹孔24注入液体密封材料,作紧急密封处理。
77.实施例三:
78.一种超低温双偏心硬密封方法,应用于实施例一中的超低温双偏心硬密封结构,或实施例二中的蝶阀,其中,包括以下步骤:
79.在低温工作时,当金属阀座18中的支撑环22受阀体9内压力的挤压后,c型圈、环形弹簧20、软态板21构成的密封圈产生形变,同时支撑环22会靠近深入金属阀座18内部,而包裹在支撑环22上的铜板随着支撑环22的深入而被进一步收紧。
80.其中,c型圈的变形空间由c型圈自身结构形成的开口补偿,从而使密封位置金属密封面的变形是平顺的,可自行吸收的,可预期的,有效地保证了在中高压下蝶阀的密封性能。
81.并且金属阀座18外密封圈与阀体9进行台阶配合,台阶高度控制外密封圈的最大压缩量,有效地避免了外密封圈受力过大而产生破坏,内密封圈处在由阀座压环17、阀体9和支撑环22共同限定密封位置,使得密封位置可靠,受力均匀,保证了中高压下蝶阀的密封性能。
82.将环形弹簧20材质采用为inconel x750,c形圈19材质采用为奥氏体不锈钢或inconel x750,支撑环22采用为高强度合金,使得支撑环22线收缩系数大于等于环形弹簧20材料的线收缩系数,进而在低温条件下支撑环22提供的预紧力不会变小,并且能限制高压状态下环形弹簧20的径向变形,使弹簧提供更大的密封比压,实现高压力下的密封。
83.阀杆11与蝶板12用滑动销13连接,滑动销13大端部为圆锥面,滑动销13与阀杆11接触部位均为机加工光滑平面,蝶板12销孔为圆锥孔,在力作用下,滑动销13即可传递扭
矩,也可依靠滑动销13配合过盈量来定位蝶阀密封位置,在低温状态下,阀杆11与蝶阀的相对位置可微量滑动,补偿低温下各零部件收缩量的不均匀性,确保低温下金属阀座18的密封性能。
84.尽管上面对本发明说明性的具体实施方式进行了描述,以便于本技术领域的技术人员能够理解本发明,但是本发明不仅限于具体实施方式的范围,对本技术领域的普通技术人员而言,只要各种变化只要在所附的权利要求限定和确定的本发明精神和范围内,一切利用本发明构思的发明创造均在保护之列。