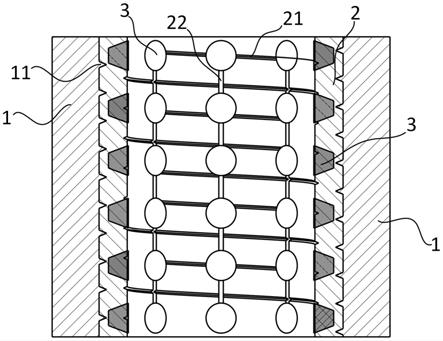
1.本公开涉及一种双金属自润滑复合轴套及其制备方法以及工程机械设备。
背景技术:2.这里的陈述仅提供与本公开有关的背景信息,而不必然地构成现有技术。
3.工程机械、矿业机械等大型重载设备在矿山、工地等恶劣环境施工作业,其主要动作依靠液压系统驱动、工作部件运动来实现,高载荷、大频率对挖斗、铲斗、箱体等工作部位运动、转动寿命的影响重大,其零部件长期存在难维护、易磨损、寿命短等技术难题。其中,轴套是此类重型机械完成不同部件连接并形成转动的常用零件,也是首当其冲最先受到恶劣工况的影响。当出现润滑状态恶化时,轴套及轴类件表面均会发生金属啃蚀、拉伤、严重磨损甚至烧伤,使得作业效率受到影响,机械噪声与震动明显加剧。最终导致维护成本提升、劳动强增加度、工作效率降低。因此,改善轴套零件的性能,对于延长轴类零件寿命、降低其磨损、减小整机作业抖动等方面具有重要作用。
4.目前常用的滑动轴套按材质分类主要有四大类:合金钢轴套、粉末冶金含油轴套、铜合金轴套与复合材料轴套。合金钢轴套主要通过在内壁机加工复杂的油槽或油穴,通过存储加注的润滑油脂来达到延长润滑周期的效果,其优点是整体材料成本低、钢材强度高,但通常存在加工复杂、材料浪费、润滑周期不够长等缺点;粉末冶金含油轴套通常采用含铜合金粉末高温烧结制备,内部残留孔隙用于后期浸油储油,其优点是在工作过程中可以通过释放润滑油形成自润滑免润滑效果,但由于孔隙和油液的存在,会大大降低粉末冶金含油轴套的强度并显著增强其脆性开裂的风险;铜合金轴套通常采用高力黄铜、铝青铜、锡青铜等通过机加工方式制备,其优点是铜合金具有较好的摩擦学性能,但会大量使用有色金属,存在成本高、强度不足等缺点,尤其在重载条件下容易发生微变形而影响轴与轴套的配合间隙,从而导致偏磨损、异常磨损的发生;另有镶嵌固体润滑剂铜套,最常见的为镶嵌石墨铜套,其优点是石墨与铜材质均可以显著提升润滑效果,但通常需要在铜套内壁机加工大量镶嵌孔位,同时需要对石墨进行镶嵌,由于石墨镶嵌层较浅且强度不高,在恶劣工况下极易发生快速磨损或脱落,导致使用后期润滑效果大打折扣;复合材料轴套通常有双金属复合轴套、非金属与金属复合轴套,双金属复合轴套通常采用固体压制方法结合,存在结合强度不高,自润滑效果不佳等问题。而非金属与金属复合轴套一般承载力不足,难以在重载工况下进行推广应用。
5.传统的钢套或合金材料轴套,因不具备自润滑特性,其注脂周期间隔较短。粉末冶金含油轴套存在压溃强度较低,无法承受重载使用工况的缺陷。固体镶嵌自润滑轴套以石墨铜套为主,通常整体采用高力黄铜结构,导致成本居高不下,并且由于镶嵌石墨槽较浅,长期恶劣磨损工况下镶嵌式石墨磨损后,其自润滑效果将大打折扣,后期磨损加速。
技术实现要素:6.本公开所要解决的一个技术问题是:提供一种双金属自润滑复合轴套及其制备方
法以及工程机械设备,能够提高轴套的自润滑性能及抗压溃性能,达到节能减材、降低成本与延长寿命的目的。
7.本公开的一些实施例提供了一种双金属自润滑复合轴套,包括:轴套基体,由合金钢制成;和复合自润滑耐磨层,制备于轴套基体的内表面;其中,复合自润滑耐磨层由纳米-微米双尺度颗粒增强铜基复合材料制成。
8.在一些实施例中,纳米-微米双尺度颗粒增强铜基复合材料包括富铁纳米颗粒-al3ti微米颗粒协同增强锡青铜合金。
9.在一些实施例中,富铁纳米颗粒-al3ti微米颗粒协同增强锡青铜合金中各组分的质量成分被配置为:sn:4%~10%wt,zn:1.5%~4.5%wt,ni:0.8%~2.8%wt,fe:0.5%~3.5%wt,co:0.1%~0.9%wt,al3ti:1.5%~4.0%wt。
10.在一些实施例中,还包括预埋在复合自润滑耐磨层内表面上的多个固体润滑剂预制件,固体润滑剂预制件由氟化石墨制成。
11.在一些实施例中,多个固体润滑剂预制件在复合自润滑耐磨层的内表面上呈等间隔布置。
12.在一些实施例中,固体润滑剂预制件相对于复合自润滑耐磨层的内表面呈凸台状。
13.在一些实施例中,固体润滑剂预制件呈梯形圆柱体状,固体润滑剂预制件的小径部埋入复合自润滑耐磨层,固体润滑剂预制件的大径部相对于复合自润滑耐磨层的内表面凸出设置。
14.在一些实施例中,复合自润滑耐磨层的内表面上形成有呈螺旋状的排屑储油槽。
15.在一些实施例中,复合自润滑耐磨层的内表面上形成有连通排屑储油槽的纵向贯通槽。
16.在一些实施例中,轴套基体的内表面上设有螺旋状的基体凸台。
17.本公开的一些实施例提供了一种制备方法,用于制备前述双金属自润滑复合轴套,包括:利用负压消失模铸造工艺将复合自润滑耐磨层制备于轴套基体的内表面。
18.本公开的一些实施例提供了一种工程机械设备,包括前述双金属自润滑复合轴套。
19.因此,本公开双金属自润滑复合轴套通过在其轴套基体的内表面制备由纳米-微米双尺度颗粒增强铜基复合材料制成的复合自润滑耐磨层,在减少铜材料使用的同时可以实现高耐磨性能与自润滑性能,具有较高的强度与韧性,提高了轴套的自润滑性能及抗压溃性能,达到节能减材、降低成本与延长寿命的目的。
附图说明
20.为了更清楚地说明本公开实施例或现有技术中的技术方案,下面将对实施例或现有技术描述中所需要使用的附图作简单地介绍,显而易见地,下面描述中的附图仅仅是本公开的一些实施例,对于本领域普通技术人员来讲,在不付出创造性劳动的前提下,还可以根据这些附图获得其他的附图。
21.图1是本公开双金属自润滑复合轴套的剖视结构示意图。
22.附图标记说明
23.1、轴套基体;2、复合自润滑耐磨层;3、固体润滑剂预制件;11、基体凸台;21、排屑储油槽;22、纵向贯通槽。
具体实施方式
24.现在将参照附图来详细描述本公开的各种示例性实施例。对示例性实施例的描述仅仅是说明性的,决不作为对本公开及其应用或使用的任何限制。本公开可以以许多不同的形式实现,不限于这里的实施例。提供这些实施例是为了使本公开透彻且完整,并且向本领域技术人员充分表达本公开的范围。应注意到:除非另外具体说明,否则在这些实施例中阐述的部件和步骤的相对布置、材料的组分、数字表达式和数值应被解释为仅仅是示例性的,而不是作为限制。
25.本公开中使用的“第一”、“第二”以及类似的词语并不表示任何顺序、数量或者重要性,而只是用来区分不同的部分。“包括”或者“包含”等类似的词语意指在该词前的要素涵盖在该词后列举的要素,并不排除也涵盖其他要素的可能。“上”、“下”、“左”、“右”等仅用于表示相对位置关系,当被描述对象的绝对位置改变后,则该相对位置关系也可能相应地改变。
26.在本公开中,当描述到特定器件位于第一器件和第二器件之间时,在该特定器件与第一器件或第二器件之间可以存在居间器件,也可以不存在居间器件。当描述到特定器件连接其它器件时,该特定器件可以与其它器件直接连接而不具有居间器件,也可以不与其它器件直接连接而具有居间器件。
27.本公开使用的所有术语与本公开所属领域的普通技术人员理解的含义相同,除非另外特别定义。还应当理解,在诸如通用字典中定义的术语应当被解释为具有与它们在相关技术的上下文中的含义相一致的含义,而不应用理想化或极度形式化的意义来解释,除非这里明确地这样定义。
28.对于相关领域普通技术人员已知的技术、方法和设备可能不作详细讨论,但在适当情况下,技术、方法和设备应当被视为说明书的一部分。
29.如图1所示,本公开的一些实施例提供了一种双金属自润滑复合轴套,包括:轴套基体1和复合自润滑耐磨层2,其中,轴套基体1由合金钢制成;复合自润滑耐磨层2制备于轴套基体1的内表面,复合自润滑耐磨层2由纳米-微米双尺度颗粒增强铜基复合材料制成。
30.在该示意性的实施例中,通过在其轴套基体1的内表面制备由纳米-微米双尺度颗粒增强铜基复合材料制成的复合自润滑耐磨层2,在减少合金钢材料使用的同时可以实现高耐磨性能与自润滑性能,具有较高的强度与韧性,提高了轴套的自润滑性能及抗压溃性能,大幅节约铜材料用量,达到节能减材、降低成本与延长寿命的目的。
31.本公开利用纳米颗粒(nanoparticles,np)-微米颗粒(microparticles,mp)双尺度协同强化效应,制备出np-mp结构材料,在铜基体组织内部弥散分布大量的纳米第二相颗粒与微米第二相颗粒,使得构成np-mp结构的细晶材料、晶粒内部弥散分布的共格或半共格纳米颗粒与组织内部弥散分布的微米颗粒相互协同配合,在提高铜基体强度的同时,显著提高其耐磨性能。
32.如图1所示,在一些实施例中,轴套基体1的内表面上设有螺旋状的基体凸台11。轴套基体1的内表面与复合自润滑耐磨层2通过消失模铸造并带有螺旋的基体凸台11结合,冶
金结合效果更佳,具有更高的结合强度。
33.在一些实施例中,纳米-微米双尺度颗粒增强铜基复合材料包括富铁纳米颗粒-al3ti微米颗粒协同增强锡青铜合金,从而获得更好的高耐磨性能与自润滑性能。
34.如图1所示,轴套基体1以常用合金钢为基体材料,通过消失模负压铸造工艺在其内层制备出由富铁纳米颗粒-al3ti微米颗粒协同增强锡青铜合金制成的复合自润滑耐磨层2,通过al3ti微米颗粒的不相溶特性,作为变质剂达到显著细化铜基体晶粒尺寸的目的,起到细晶强化效果,显著增强内层铜基体层的强度与硬度,有助于提高其整体抗压溃强度与耐磨性能。而不相溶al3ti微米颗粒作为高硬度第二相弥散分布在铜基体晶粒周围,同时可以阻碍磨粒磨损过程中磨粒的划过,减轻材料表面的磨损,起到提高耐磨性的效果。弥散分布的富铁纳米颗粒可以协同al3ti微米颗粒起到第二相形核并抑制铜基体晶粒长大的倾向,协同细晶强化。在铜基体中存在的富铁纳米颗粒-al3ti微米颗粒,以双尺度第二相颗粒形式弥散分布,从而阻碍位错运动,提升铜基体强度,进一步达到弥散强化。al3ti微米颗粒尺寸相对比较大,且与铜基体的浸润性不好,第二相与铜基体界面是非共格存在,位错运动过程中,由于不能穿过al3ti微米第二相颗粒而在界面出发生塞积,导致应力集中,强度提升。而富铁纳米颗粒尺寸细小,且与铜基体的浸润性较好,第二相与铜基体形成完美晶格匹配,在铜包铁纳米颗粒的高形核潜力与自发捕捉机制下,进一步提升细晶粒强度,位错切过共格晶粒的难度大幅增强,铜基体材料强度进一步提升。同时起到富锡相消除作用,在凝固过程中形成富铁纳米墙阻碍锡的偏析并打破锡的团聚,有利于铜基体材料的综合性能提升。
35.在一些实施例中,富铁纳米颗粒-al3ti微米颗粒协同增强锡青铜合金中各组分的质量成分被配置为:sn:4%~10%wt,zn:1.5%~4.5%wt,ni:0.8%~2.8%wt,fe:0.5%~3.5%wt,co:0.1%~0.9%wt,al3ti:1.5%~4.0%wt,余量为cu。通过合金成分设计,优化铸造锡青铜合金内层的组织性能,并且与外层钢基体进行强冶金结合。在该数值范围内,轴套的耐磨性能提升效果显著。
36.如图1所示,在一些实施例中,双金属自润滑复合轴套还包括预埋在复合自润滑耐磨层2内表面上的多个固体润滑剂预制件3,固体润滑剂预制件3由氟化石墨制成。在内层铸造锡青铜合金上预埋氟化石墨固体润滑剂预制件,可以起到面润滑效果。
37.在轴套基体1的材料选择上,可以是普通合金钢也可以是有色金属,复合固体润滑剂可以是镶嵌的氟化石墨也可以是其他mos2等单独或复合的带润滑性能的固体材料,复合固体润滑剂的形状与排布形式也可以是多种多样的。
38.如图1所示,在一些实施例中,多个固体润滑剂预制件3在复合自润滑耐磨层2的内表面上呈等间隔布置,从而保证润滑均匀性。在一些实施例中,固体润滑剂预制件3相对于复合自润滑耐磨层2的内表面呈凸台状。在磨损过程中,一方面可以起到越磨越润滑,另一方面可以起到稳固不脱落的效果。在一些实施例中,如图1所示,固体润滑剂预制件3呈梯形圆柱体状,固体润滑剂预制件3的小径部埋入复合自润滑耐磨层2,固体润滑剂预制件3的大径部相对于复合自润滑耐磨层2的内表面凸出设置,固体润滑剂预制件3梯形圆柱体设计可以使其与内层复合自润滑层牢固浇注成一体,自润滑效果越好,从而进一步提升润滑和稳固不脱落的效果。
39.如图1所示,在一些实施例中,复合自润滑耐磨层2的内表面上形成有呈螺旋状的
排屑储油槽21。排屑储油槽21可以存储首次注脂润滑脂并不断吸收磨损过程中的异质颗粒物与粉尘颗粒物,减少磨损加剧。在一些实施例中,复合自润滑耐磨层2的内表面上形成有连通排屑储油槽21的纵向贯通槽22,一方面可以存储润滑脂,加强润滑效果,另一方面可以存储因磨损产生的磨屑或因密封问题带入的灰尘异物颗粒,避免摩擦表面因异物存在而导致磨损加剧。
40.本公开的一些实施例提供了一种制备方法,用于制备前述双金属自润滑复合轴套,包括:利用负压消失模铸造工艺将复合自润滑耐磨层2制备于轴套基体1的内表面。负压消失模铸造工艺(又称实型铸造)是将与铸件尺寸形状相似的石蜡或泡沫模型粘结组合成模型簇,刷涂耐火涂料并烘干后,埋在干石英砂中振动造型,在负压下浇注,使模型气化,液体金属占据模型位置,凝固冷却后形成铸件的新型铸造方法。实验表明,通过负压消失模铸造工艺将将复合自润滑耐磨层2制备于轴套基体1的内表面,显著增强内层铜基体层的强度与硬度,有助于提高其整体抗压溃强度与耐磨性能,轴套的耐磨性能与自润滑性能得到显著提升,具有较高的可实施性。
41.下面结合附图1来说明本公开双金属自润滑复合轴套的制备过程如下:
42.首先采用20crmnti钢材为轴套基体1的材料,并在轴套基体1的内表面加工螺旋状的基体凸台11,节距8mm;然后制备由氟化石墨制成的固体润滑剂预制件3;继而制备内层复合自润滑层eps模型,并在内层复合自润滑层eps模型预埋多个呈点阵状离散分布的固体润滑剂预制件3。其中,固体润滑剂预制件3外形为梯形圆柱体,在消失模铸造过程中,直接与内层复合自润滑层浇注一体成型。
43.准备各成分比例的组分:sn:9.3%wt,zn:2.1%wt,ni:1.0%wt,fe:1.1%wt,co:0.4%,al3ti:1.4%wt,余量为cu。
44.(1)熔炼铜合金液,按质量比例熔炼84.7份的电解铜、9.3份的锡,熔炼温度控制在1380℃,加入1.1份的铁与0.4份的钴,石墨棒搅拌均匀,保温15min。
45.(2)保温结束后,及时降低加热频率,控制温度在1140℃,加入2.1份的锌与1.4份的al3ti(平均粒径500μm),石墨棒搅拌均匀,并快速升温至1300℃,保温10min。
46.(3)保温结束后,及时降低加热频率,控制温度在1200℃准备消失模浇注成型。
47.(4)同时将组装好的轴套基体1、镶嵌有氟化石墨固体润滑剂梯形圆柱体的内层复合自润滑层eps模型置于消失模砂箱中,均匀加入干砂微振紧实;振幅小于1.5mm,振频75hz,在砂箱上部覆盖塑料布密封,抽真空负压,浇入高温合金液;负压控制在0.01mpa~0.04mpa,完成内层复合自润滑层的铸造成型。
48.(5)在保压20min后排气泄压,制备双金属自润滑复合轴套。
49.与现有的自润滑轴套相比,本公开双金属自润滑复合轴套在轴套基体1的内表面通过消失模铸造工艺制备出复合自润滑层,并镶嵌有复合固体润滑剂,通过成分优化设计,在内层铜合金层铸造过程中,通过引入富铁纳米增强颗粒,一方面通过抑制晶粒长大达到显著细化基体晶粒尺寸的效果,另一方面通过“铜包铁”纳米颗粒的异质形核与自发捕捉机制,在提升基体铜合金强度硬度的同时,减少韧性与塑性的损失。同时,微米级晶粒细化剂al3ti一方面可以配合富铁纳米增强颗粒抑制晶粒长大进一步达到细化基体晶粒尺寸的效果,另一方面微米级al3ti弥散分布在铜合金基体内,可以起到多重的耐磨效果。相比镶嵌固体润滑剂铜套可以明显节约有色金属铜的使用量,进而显著降低成本。同时,由于钢材基
体的强度与硬度保证,可以获得更佳的抗压溃性能。相比粉末冶金自润滑轴套,本公开中复合自润滑耐磨层不仅自身具有自润滑性能与耐磨效果,镶嵌有氟化石墨更能提供优异的自润滑性能,并且由于钢材基体的强度与硬度保证,可以获得更佳的抗压溃性能。
50.本公开的一些实施例提供了一种工程机械设备,包括前述双金属自润滑复合轴套。工程机械设备相应地具有上述有益技术效果。
51.至此,已经详细描述了本公开的各实施例。为了避免遮蔽本公开的构思,没有描述本领域所公知的一些细节。本领域技术人员根据上面的描述,完全可以明白如何实施这里公开的技术方案。
52.虽然已经通过示例对本公开的一些特定实施例进行了详细说明,但是本领域的技术人员应该理解,以上示例仅是为了进行说明,而不是为了限制本公开的范围。本领域的技术人员应该理解,可在不脱离本公开的范围和精神的情况下,对以上实施例进行修改或者对部分技术特征进行等同替换。本公开的范围由所附权利要求来限定。