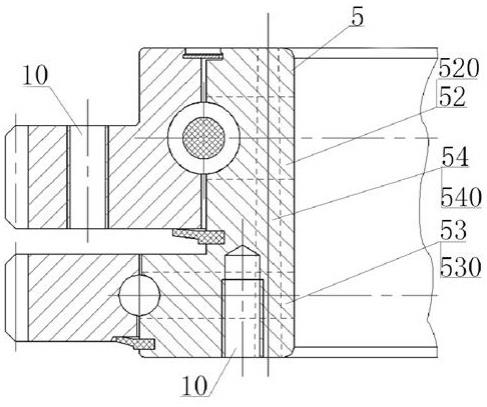
1.本发明涉及轴承领域,具体涉及一种双排异径外圈分体式回转轴承。
背景技术:2.回转轴承是近四十年在世界范围内逐渐兴起的新型机械零部件,它有内外圈、滚动体等构成,我国定型生产的回转支承,主要是80年代初由机械工业部指定天津工程机械研究所组织引进原联邦德国rothe erde公司的设计和制造技术。1984年12月20日发布了中华人民共和国机械工业部标准:jb/2300-84《回转支承型式、基本参数和技术要求》,主要由机械电子工业部天津工程机械研究所、徐州海林回转支承厂负责起草,后来国家又在1991年发布了建筑机械标准:jb36.1-36.3-91,在1999年和2011年先后发布新的机械行业标准jb/2300-1999及jb/2300-2011。回转支承,是一种能够承受综合载荷的大型轴承,可以同时承受较大的轴向、径向负荷和倾覆力矩。
3.回转轴承一般用于回转机构中实现单一的转向运动,遇到复杂的使用环境需要同时实现多个转向运动时常规回转轴承就无法满足。
4.针对特殊场合使用的移动机器人其转向机构增加多类辅助设施,需要在同一时间实现多个不同向的转向运动,根据这一工况特点,我们所设计的双层异径球外齿式双向回转轴承可满足此类工况需求。
技术实现要素:5.为了解决上述技术问题,本发明提出一种双排异径外圈分体式回转轴承,设计合理巧妙,使用方便,能够同一时间实现多个不同向的转向运动。
6.本发明的技术方案:一种双排异径外圈分体式回转轴承,它包括上层外圈、下层外圈、第一钢球、第二钢球和内圈,内圈是圆环且下端一周设计有向外凸起的环形凸台,上层外圈设计在内圈上端外侧且上层外圈内侧的滚道与内圈上端外侧的滚道之间安装有若干第一钢球,下层外圈设计在内圈的环形凸台外侧且下层外圈内侧的滚道与内圈的环形凸台外侧的滚道之间安装有若干第二钢球,所述上层外圈外侧下端设计有环形凸边,环形凸边一周设计有啮合齿,下层外圈外侧一周也设计有啮合齿。
7.所述的内圈靠近上端设计有上层柱塞孔,内圈靠近下端设计有下层柱塞孔;上层柱塞孔一端联通内圈的内孔,上层柱塞孔另一端联通内圈外侧上端的滚道;下层柱塞孔一端联通内圈的内孔,下层柱塞孔另一端联通内圈外侧下端环形凸台外侧的滚道;所述内圈还设计圆锥孔,圆锥孔从上往下依次贯通上层柱塞孔和下层柱塞孔,圆锥孔的上端联通内圈的上端面,圆锥孔的下端联通内圈的下端面;所述上层柱塞孔内安装有上层柱塞销,下层柱塞孔安装有下层柱塞销,上层柱塞销上开有上锥形孔,下层柱塞销上开有下锥形孔,所述圆锥孔内插入圆锥销,圆锥销插入圆锥孔中且从上层柱塞销的上层锥形孔以及下层柱塞销的下锥形孔中穿过。
8.所述的内圈轴向靠近中心位置设计有竖向油孔,竖向油孔上端联通内圈的上端面,内圈还分别设计上横向油孔和下横向油孔,上横向油孔一端联通竖向油孔靠近中间位置,上横向油孔另一端联通内圈上端外侧的滚道,下横向油孔一端联通竖向油孔的下端,下横向油孔另一端联通内圈下端的环形凸台外侧的滚道;所述竖向油孔的上端口部还装有压配式压注油杯。
9.所述的内圈上端外侧一周设计外环形台阶,上层外圈的内侧一周设计内环形台阶,外环形台阶和内环形台阶形成环形凹槽,环形凹槽内安装有防尘盖;内圈的圆环外侧下端根部设计上环形矩形槽,上环形矩形槽内安装有上密封圈,上密封圈包括矩形状圈和斜圈,矩形状圈外侧连接有斜圈,矩形状圈内侧安装在上环形矩形槽内,斜圈倾斜压在上层外圈的下端;内圈的环形凸台外侧下端设计下环形矩形槽,下环形矩形槽内安装有下密封圈,下密封圈包括矩形状圈和斜圈,矩形状圈外侧连接有斜圈,矩形状圈内侧安装在下环形矩形槽内,斜圈倾斜压在下层外圈的下端。
10.所述的环形凸边的轴向上一周设计有若干的安装孔;内圈下端一周靠近内侧位置也设计有若干安装孔。
11.所述的上层外圈加工方法:步骤一:锻加工圆钢锻打,用锻压设备把圆钢锻打成环形工件后正火处理改善切削功能。
12.步骤二:调质前荒车将环形工件放在数控车床上进行车削;荒车环形工件的两平面、外圆、内孔及内外倒角,车削参数为线速度40-50r/min,进刀量:粗车0.4-0.5mm/r,精车0.3-0.4 mm/r;车削后工件粗糙度为ra6.3以下。
13.步骤三:调质处理调质处理就是淬火加高温回火的双重热处理方法;淬火温度为820-870℃,高温回火在500-650℃之间回火;调质硬度hb270-310。
14.步骤四:精车套圈将工件用三爪卡盘固定数控车床上加工两平面、外圆、l型台阶、内孔、滚道及各处倒角;车削参数为线速度40-50r/min,进刀量:0.20mm/r;精车后工件粗糙度为ra3.2以下。
15.步骤五:滚道淬火滚道淬火使用设备中频扫描淬火机床,工件运转速度137mm/min,加工频率为15hz;工艺要求:hrc洛氏硬度55-62,ds淬硬层≥2.2mm,无裂纹缺陷,软带总长不大于40mm。
16.步骤六:半硬车l型台阶将工件用三爪卡盘固定数控车床上加工l型台阶;车削参数为线速度40-50r/min,进刀量:0.20mm/r;精车后工件粗糙度为ra3.2以下。
17.步骤七:附加回火将工件放进回火炉里,附加回火为120-150℃;保温时间3-4h。
18.步骤八:硬车套圈将工件用三爪卡盘固定数控车床上加工两平面、外圆l型台阶、密封槽;车削参数为线速度40-50r/min,进刀量:0.10mm/r;精车后工件粗糙度为ra3.2以下。
19.步骤九:加工安装孔
将工件固定在数控铣床上加工安装孔;钻铣参数为线速度50-60r/min,进刀量:0.16mm/r;精车后工件粗糙度为ra3.2以下。
20.步骤十:齿加工采用盘形模数铣刀或指状铣刀铣齿,铣刀刀齿截面形状与齿轮齿间形状相对应。
21.步骤十一:配车滚道将工件固定在数控立车上加工;车削参数为线速度40-50r/min,进刀量:0.10mm/r;精车后工件粗糙度为ra1.0以下。
22.步骤十二:磷化处理防止工件工作环境比较恶劣,容易腐蚀生锈,表面做磷化处理。
23.所述的下层外圈的加工方法步骤一:锻加工圆钢锻打;用锻压设备把圆钢锻打成环形工件后正火处理改善切削功能。
24.步骤二:调质前荒车将环形工件放在数控车床上进行车削,荒车环形工件的两平面、外圆、内孔及内外倒角;车削参数为线速度40-50r/min,进刀量:粗车0.4-0.5mm/r,精车0.3-0.4 mm/r;车削后工件粗糙度为ra6.3以下。
25.步骤三:调质处理调质处理就是淬火加高温回火的双重热处理方法淬火温度为820-870℃,高温回火在500-650℃之间回火;调质硬度hb270-310。
26.步骤四:粗车套圈将工件用三爪卡盘固定数控车床上加工两平面、外圆及台阶、内孔及滚道;车削参数为线速度40-50r/min,进刀量:0.20mm/r;精车后工件粗糙度为ra3.2以下。
27.步骤五:齿加工采用盘形模数铣刀或指状铣刀铣齿,铣刀刀齿截面形状与齿轮齿间形状相对应。
28.步骤六:精光两平面将工件固定在数控立车上加工;车削参数为线速度40-50r/min,进刀量:0.10mm/r;精车后工件粗糙度为ra1.0以下。
29.步骤七:精车滚道将工件固定在数控立车上加工;车削参数为线速度40-50r/min,进刀量:0.10mm/r;精车后工件粗糙度为ra1.0以下。
30.步骤八:氮化处理将工件治愈渗氮炉中,并将炉盖密封后加热,但在加热至150℃以前需排除炉内空气;将加热炉的自动温度控制在150℃并开始加热,在炉内空气排除至10%以下,将炉温升高至渗氮温度,渗氮所需厚度至少保持4-10小时,处理温度即保持在520℃左右;通过氮化处理使工件表面形成一层硬化层,提高齿面硬度增强其耐磨性以提高外齿圈的使用寿命。
31.步骤九:磷化处理防止工件工作环境比较恶劣,容易腐蚀生锈,表面做磷化处理。
32.所述的内圈的加工方法步骤一:锻加工
圆钢锻打;用锻压设备把圆钢锻打成环形工件后正火处理改善切削功能。
33.步骤二:调质前荒车将环形工件放在数控车床上进行车削两平面、外圆、内孔;车削参数为线速度40-50r/min,进刀量:粗车0.4-0.5mm/r,精车0.3-0.4 mm/r;车削后工件粗糙度为ra6.3以下。
34.步骤三:调质处理调质处理就是淬火加高温回火的双重热处理方法;淬火温度为820-870℃,高温回火在500-650℃之间回火;调质硬度hb270-310。
35.步骤四:加工柱塞/锥销孔将工件通过工装装夹固定在摇臂钻上钻孔,铰孔;钻削参数为线速度40-50r/min,进刀量:0.16mm/r;铰孔后工件粗糙度为ra1.6以下。
36.步骤五:精车套圈将工件用三爪卡盘固定数控车床上加工两平面、外圆、内孔、两滚道及倒角;车削参数为线速度40-50r/min,进刀量:0.20mm/r;精车后工件粗糙度为ra3.2以下。
37.步骤六:钻油孔将工件固定在摇臂钻上加工油孔;钻孔参数为线速度40-50r/min,进刀量:0.16mm/r;精车后工件粗糙度为ra3.2以下。
38.步骤七:滚道淬火滚道淬火使用设备中频扫描淬火机床,工件运转速度137mm/min,加工频率为15hz;工艺要求:hrc洛氏硬度55-62,ds淬硬层上滚道ds:2.0-2.5mm, 下滚道ds≥2.2mm,无裂纹缺陷,软带总长不大于40mm。
39.步骤八:硬车套圈将工件用三爪卡盘固定数控车床上加工两平面、内孔、密封槽、倒角;车削参数为线速度40-50r/min,进刀量:0.20mm/r;精车后工件粗糙度为ra3.2以下。
40.步骤九:加工安装孔/油杯孔将工件固定在数控铣床上加工安装孔;钻铣参数为线速度50-60r/min,进刀量:0.16mm/r;精车后工件粗糙度为ra3.2以下。
41.步骤十:硬车滚道将工件固定在数控立车上加工;车削参数为线速度40-50r/min,进刀量:0.10mm/r;精车后工件粗糙度为ra1.0以下。
42.步骤十一:磷化处理防止工件工作环境比较恶劣,容易腐蚀生锈,表面做磷化处理。
43.本发明的优点:1、设计合理巧妙,使用方便,设计成两层独立外圈结合一个内圈方式,能够同一时间实现多个不同向的转向运动。
44.2、通过柱塞孔方式装填钢球,效率高,同时通过一个圆锥销同时固定两个柱塞,安全可靠,固定牢固。
45.3、调质前荒车目的是为了提高毛坯工件的形状精度和减少工件的精加工余量。
46.4、调质处理就是淬火加高温回火的双重热处理方法,其目的是使工件具有良好的综合性能;调质硬度hb270-310,执行的高于正常设计标准的调质硬度,以提高套圈在受倾
覆力矩下的抗拉与屈服强度。
47.5、滚道淬火保证承受载荷的滚道具备一定深度的淬硬层来满足工况需要。
48.6、配车滚道是根据上层轴承的游隙值计算出上层外圈滚道所需加工的直径,然后编程加工到计算尺寸后进行使装配并检查成品精度(游隙与跳动)。
49.7、氮化处理是通过氮化处理使工件表面形成一层硬化层,提高齿面硬度增强其耐磨性以提高外齿圈的使用寿命。
附图说明
50.图1是本发明的示意图。
51.图2是图1中左侧放大示意图。
52.图3是图1中右侧放大示意图。
53.图4是图1的俯视图。
具体实施方式
54.参照附图1-4,一种双排异径外圈分体式回转轴承,它包括上层外圈1、下层外圈2、第一钢球3、第二钢球4和内圈5,内圈5是圆环且下端一周设计有向外凸起的环形凸台51,上层外圈1设计在内圈5上端外侧且上层外圈1内侧的滚道与内圈5上端外侧的滚道之间安装有若干第一钢球3,下层外圈2设计在内圈5的环形凸台51外侧且下层外圈2内侧的滚道与内圈5的环形凸台51外侧的滚道之间安装有若干第二钢球4,所述上层外圈1外侧下端设计有环形凸边11,环形凸边11一周设计有啮合齿6,下层外圈2外侧一周也设计有啮合齿6。所述上层外圈与下层外圈之间间距5mm。
55.如图2,所述的内圈5靠近上端设计有上层柱塞孔52,内圈5靠近下端设计有下层柱塞孔53;上层柱塞孔52一端联通内圈5的内孔,上层柱塞孔52另一端联通内圈5外侧上端的滚道;下层柱塞孔53一端联通内圈5的内孔,下层柱塞孔53另一端联通内圈5外侧下端环形凸台51外侧的滚道;所述内圈5还设计圆锥孔54,圆锥孔54从上往下依次贯通上层柱塞孔52和下层柱塞孔53,圆锥孔54的上端联通内圈5的上端面,圆锥孔54的下端联通内圈5的下端面;所述上层柱塞孔52内安装有上层柱塞销520,下层柱塞孔53安装有下层柱塞销530,上层柱塞销520上开有上锥形孔,下层柱塞销530上开有下锥形孔,所述圆锥孔54内插入圆锥销540,圆锥销540插入圆锥孔54中且从上层柱塞销520的上层锥形孔以及下层柱塞销530的下锥形孔中穿过。
56.如图3,所述的内圈5轴向靠近中心位置设计有竖向油孔55,竖向油孔55上端联通内圈5的上端面,内圈5还分别设计上横向油孔56和下横向油孔57,上横向油孔56一端联通竖向油孔55靠近中间位置,上横向油孔56另一端联通内圈5上端外侧的滚道,下横向油孔57一端联通竖向油孔55的下端,下横向油孔57另一端联通内圈5下端的环形凸台51外侧的滚道;所述竖向油孔55的上端口部还装有压配式压注油杯。
57.如图2、3,所述的内圈5上端外侧一周设计外环形台阶,上层外圈1的内侧一周设计内环形台阶,外环形台阶和内环形台阶形成环形凹槽,环形凹槽内安装有防尘盖7;内圈5的圆环外侧下端根部设计上环形矩形槽,上环形矩形槽内安装有上密封圈8,上密封圈8包括矩形状圈和斜圈,矩形状圈外侧连接有斜圈,矩形状圈内侧安装在上环形矩形槽内,斜圈倾
斜压在上层外圈1的下端;内圈5的环形凸台51外侧下端设计下环形矩形槽,下环形矩形槽内安装有下密封圈9,下密封圈9包括矩形状圈和斜圈,矩形状圈外侧连接有斜圈,矩形状圈内侧安装在下环形矩形槽内,斜圈倾斜压在下层外圈2的下端。
58.如图1-3,所述的环形凸边11的轴向上一周设计有若干的安装孔10;内圈5下端一周靠近内侧位置也设计有若干安装孔10。
59.所述的上层外圈1加工方法:步骤一:锻加工圆钢锻打,用锻压设备把圆钢锻打成环形工件后正火处理改善切削功能。
60.步骤二:调质前荒车将环形工件放在数控车床上进行车削;荒车环形工件的两平面、外圆、内孔及内外倒角,车削参数为线速度40-50r/min,进刀量:粗车0.4-0.5mm/r,精车0.3-0.4 mm/r;车削后工件粗糙度为ra6.3以下。
61.步骤三:调质处理 执行的高于正常设计标准的调质硬度,以提高套圈在受倾覆力矩下的抗拉与屈服强度。
62.调质处理就是淬火加高温回火的双重热处理方法,其目的是使工件具有良好的综合性能;淬火温度为820-870℃,高温回火在500-650℃之间回火;调质硬度hb270-310。
63.步骤四:精车套圈将工件用三爪卡盘固定数控车床上加工两平面、外圆、l型台阶、内孔、滚道及各处倒角;车削参数为线速度40-50r/min,进刀量:0.20mm/r;精车后工件粗糙度为ra3.2以下。
64.步骤五:滚道淬火 保证承受载荷的滚道具备一定深度的淬硬层来满足工况需要。
65.滚道淬火使用设备中频扫描淬火机床,工件运转速度137mm/min,加工频率为15hz;工艺要求:hrc洛氏硬度55-62,ds淬硬层≥2.2mm,无裂纹缺陷,软带总长不大于40mm。
66.步骤六:半硬车l型台阶将工件用三爪卡盘固定数控车床上加工l型台阶;车削参数为线速度40-50r/min,进刀量:0.20mm/r;精车后工件粗糙度为ra3.2以下。
67.步骤七:附加回火将工件放进回火炉里,附加回火为120-150℃;保温时间3-4h。
68.步骤八:硬车套圈将工件用三爪卡盘固定数控车床上加工两平面、外圆l型台阶、密封槽;车削参数为线速度40-50r/min,进刀量:0.10mm/r;精车后工件粗糙度为ra3.2以下。
69.步骤九:加工安装孔将工件固定在数控铣床上加工安装孔;钻铣参数为线速度50-60r/min,进刀量:0.16mm/r;精车后工件粗糙度为ra3.2以下。
70.步骤十:齿加工采用盘形模数铣刀或指状铣刀铣齿,铣刀刀齿截面形状与齿轮齿间形状相对应。
71.步骤十一:配车滚道 根据上层轴承的游隙值计算出上层外圈1滚道所需加工的直径,然后编程加工到计算尺寸后进行使装配并检查成品精度(游隙与跳动)。
72.将工件固定在数控立车上加工;车削参数为线速度40-50r/min,进刀量:0.10mm/r;精车后工件粗糙度为ra1.0以下。
50r/min,进刀量:粗车0.4-0.5mm/r,精车0.3-0.4 mm/r;车削后工件粗糙度为ra6.3以下。
88.步骤三:调质处理 执行的高于正常设计标准的调质硬度,以提高套圈在受倾覆力矩下的抗拉与屈服强度。
89.调质处理就是淬火加高温回火的双重热处理方法,其目的是使工件具有良好的综合性能;淬火温度为820-870℃,高温回火在500-650℃之间回火。
90.步骤四:加工柱塞/锥销孔将工件通过工装装夹固定在摇臂钻上钻孔,铰孔;钻削参数为线速度40-50r/min,进刀量:0.16mm/r;铰孔后工件粗糙度为ra1.6以下。
91.步骤五:精车套圈将工件用三爪卡盘固定数控车床上加工两平面、外圆、内孔、两滚道及倒角;车削参数为线速度40-50r/min,进刀量:0.20mm/r;精车后工件粗糙度为ra3.2以下。
92.步骤六:钻油孔将工件固定在摇臂钻上加工油孔;钻孔参数为线速度40-50r/min,进刀量:0.16mm/r;精车后工件粗糙度为ra3.2以下。
93.步骤七:滚道淬火 保证承受载荷的滚道具备一定深度的淬硬层来满足工况需要。
94.滚道淬火使用设备中频扫描淬火机床,工件运转速度137mm/min,加工频率为15hz;工艺要求:hrc洛氏硬度55-62,ds淬硬层上滚道ds:2.0-2.5mm, 下滚道ds≥2.2mm,无裂纹缺陷,软带总长不大于40mm。
95.步骤八:硬车套圈将工件用三爪卡盘固定数控车床上加工两平面、内孔、密封槽、倒角;车削参数为线速度40-50r/min,进刀量:0.20mm/r;精车后工件粗糙度为ra3.2以下。
96.步骤九:加工安装孔/油杯孔将工件固定在数控铣床上加工安装孔;钻铣参数为线速度50-60r/min,进刀量:0.16mm/r;精车后工件粗糙度为ra3.2以下。
97.步骤十:硬车滚道将工件固定在数控立车上加工;车削参数为线速度40-50r/min,进刀量:0.10mm/r;精车后工件粗糙度为ra1.0以下。
98.步骤十一:磷化处理防止工件工作环境比较恶劣,容易腐蚀生锈,表面做磷化处理;包括除油防锈-水洗-磷化-水洗-磷化后处理五道基本步骤。