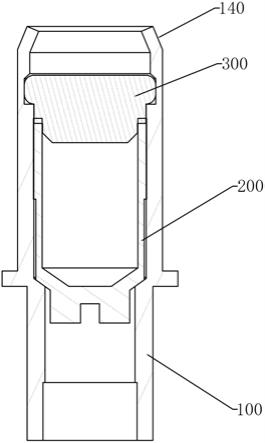
1.本实用新型涉及医疗配件单向阀技术领域,具体涉及一种医用单向阀。
背景技术:2.医用单向阀的运用范围非常广泛,留置针、麻醉面罩等医疗产品上均需要使用医用单向阀。现有的医疗单向阀一般使用弹簧提供预压缩力实现单向功能,但是弹簧在加工过程中轴向高度一般很难控制,这就造成了单向阀开启压力的不稳定。另外,现有的一部分医疗单向阀会使用压盖进行预压缩,但现有压盖的紧固方式不牢靠,当受力过大时,容易出现压盖崩开,功能失效造成安全隐患。
技术实现要素:3.本实用新型是为了解决背景技术中存在的至少一种缺陷或问题,提供一种医用单向阀,该医疗单向阀无需使用弹簧,单向阀开启压力的稳定。
4.为达成上述目的,本实用新型采用如下的技术方案:
5.一种医用单向阀,包括阀体、压紧件和弹性密封件,阀体为中空结构的部件,压紧件和弹性密封件装设于阀体内,阀体内腔壁设有第一密封面,弹性密封件设有第二密封面,弹性密封件顶抵在压紧件和第一密封面之间,其特征在于,阀体上端部向内倾斜形成缩口,密封状态下,第二密封面与第一密封面紧密贴合形成密封,阀体的上下腔之间不导通;工作状态下,弹性密封件受力发生形变,第二密封面与第一密封面脱离形成导通间隙,阀体的上下腔之间导通;弹性密封件不受力时,回复至密封状态。
6.优选的,所述压紧件为设有通孔的圆环型压盖,阀体内腔壁设有用于容纳压盖的凹槽,所述凹槽的上槽壁倾斜设置,压盖装设于凹槽内。
7.优选的,所述弹性密封件为上端设有开口的u型杯体状的弹性阀芯,弹性阀芯包括底壁和侧壁,侧壁具有弹性受力可发生形变;所述压盖设有向下延伸的凸筋;凸筋嵌入所述弹性阀芯的上端开口中。
8.优选的,所述弹性阀芯上部外侧壁与所述阀体中部腔壁之间间隙设置形成导通通道;导通通道与所述压盖的通孔连通;所述阀体中部腔壁底端倾斜设置形成第一密封面,所述弹性阀芯底壁外周倾斜设置形成第二密封面。
9.优选的,所述阀体中部腔壁设有若干间隔设置的第一筋条,所述弹性阀芯上部外侧壁贴紧所述第一筋条端面,两两相邻第一筋条之间的凹部形成所述导通通道。
10.优选的,所述弹性阀芯外侧壁设有少于所述第一筋条数量的第二筋条,第二筋条嵌入两相邻所述第一筋条之间。
11.优选的,所述阀体为透明塑料件。
12.优选的,所述阀体为圆柱型状,所述缩口为锥状缩口。
13.本实用新型的技术方案与背景技术相比,具有如下优点:
14.1、阀体上端形成缩口,无需使用螺纹也能实现和面罩等的过盈连接,安装方便;并
且可防止压紧件受力过大而脱离阀体。
15.2、本实用新型的医用单向阀的凹槽与缩口对压盖形成双重限制,防止压盖受力过大而脱离阀体。
16.3、本实用新型的弹性内芯可采用硅胶或其他弹性体制备,加工精度高,尺寸稳定,单向阀开启压力稳定。半成品阀体的可以设计成单独一个零件一次性注塑成型,精度高,注塑模具简单,制造成本低。
附图说明
17.为了更清楚地说明实施例的技术方案,下面简要介绍所需要使用的附图:
18.图1为单向阀剖面的立体示意图;
19.图2为阀体剖面的立体示意图;
20.图3为弹性阀芯的剖面示意图;
21.图4为弹性阀芯的侧面示意图;
22.图5为压盖的立体示意图;
23.图6为单向阀的安装过程示意图1;
24.图7为单向阀的安装过程示意图2;
25.图8为实施例二加工的示意图;
26.图9为实施例三加工的示意图;
27.图10为单向阀的剖面示意图;
28.附图标记:100、阀体;110、凹槽;111、上槽壁;120、第一密封面;130、第一筋条;131、导通通道;140、缩口;200、弹性阀芯;210、底壁;211、第二密封面;220、侧壁;221、第二筋条;300、压盖;310、圆环;320、凸筋;330、通孔;400、模具。
具体实施方式
29.在本实用新型的描述中,采用了“上”、“下”等指示的方位或位置关系为基于附图所示的方位或位置关系,仅是为了便于描述本实用新型,而不是指示或暗示所指的装置必须具有特定的方位、以特定的方位构造和操作,因此不能理解为对本实用新型保护范围的限制。
30.本实用新型公开了一种医用单向阀,包括阀体100、压紧件和弹性密封件,阀体100为中空结构的部件,压紧件和弹性密封件装设于阀体100内,阀体100内腔壁设有第一密封面,弹性密封件设有第二密封面,弹性密封件顶抵在压紧件和第一密封面之间,阀体100上端部向内倾斜形成缩口。具体的实施方式如:
31.实施例一:
32.如图1
‑
10所示,一种医用单向阀,包括阀体100、弹性阀芯200和设有通孔330的圆环型压盖300,阀体100为中空结构的部件,阀体100内腔壁设有用于容纳压盖300的凹槽110,压盖300装设于凹槽110内,凹槽110上下槽壁起到限位作用,防止压盖300受力后脱离阀体100;阀体100上端部向内倾斜形成缩口140,缩口140直径小于压盖300,可限制压盖300脱离阀体100;阀体100内腔壁设有第一密封面120;弹性阀芯200设有第二密封面211;弹性阀芯200顶抵在压盖300和第一密封面120之间;密封状态下,第二密封面211与第一密封面
120紧密贴合形成密封,阀体100的上下腔之间不导通;工作状态下,弹性阀芯200受力发生形变,第二密封面211与第一密封面120脱离形成导通间隙,阀体100的上下腔之间导通;弹性阀芯200不受力时,依靠自身弹性回复至密封状态。
33.具体的,本实施例的凹槽110的上槽壁111倾斜设置。在生产制造阀体100时凹槽110的上槽壁111倾斜可以方便模具脱模。
34.具体的,本实施例的弹性阀芯200呈u型杯体状,上端设有开口,包括底壁210和侧壁220,侧壁220具有弹性受力可发生形变。
35.具体的,本实施例的压盖300包括一中空的圆环310,圆环310中间设有向下延伸的“十字交叉”凸筋320,凸筋320与圆环310之间形成通孔330;凸筋320嵌入弹性阀芯200的上端开口中。
36.具体的,本实施例的弹性阀芯200上部外侧壁220与阀体100中部腔壁之间间隙设置形成导通通道131;导通通道131与压盖300的通孔330连通;阀体100中部腔壁底端倾斜设置形成第一密封面120,弹性阀芯200底壁210外周倾斜设置形成第二密封面211。
37.具体的,本实施例的阀体100中部腔壁设有若干间隔设置的第一筋条130,弹性阀芯200上部外侧壁220贴紧第一筋条130端面,两两相邻第一筋条130之间的凹部形成导通通道131。
38.具体的,本实施例的弹性阀芯200外侧壁220设有少于筋条数量的第二筋条221,第二筋条221嵌入两相邻第一筋条130之间且与阀体100的腔壁之间具有一定间隙。第二筋条221定位在第一筋条130中间,防止转动,弹性阀芯200发生形变时也不会贴死阀体100的腔壁堵住导通通道131。
39.具体的,本实施例的阀体100为透明塑料件,可以方便观察注射液体或者气体的走向;压盖300为塑料件,弹性阀芯200为硅胶件。
40.具体的,本实施例的阀体100为圆柱型状,缩口140为锥状缩口140。
41.具体的本实施例的单向阀在初始密封状态下时,弹性阀芯200下部外侧壁220上的第二密封面211与阀体100内腔的第一密封面120紧密贴合形成密封,阀体100的上下腔之间不导通;工作状态下,弹性阀芯200受到向上的力,弹性阀芯200的侧壁220发生形变,第二密封面211脱离第一密封面120形成导通间隙,此时气体或液体可通过该导通间隙进入弹性阀芯200外侧壁220与阀体100内腔壁形成的导通通道131中,经导通通道131流向压盖300的通孔330,最终流出阀体100的上端出口;使用完毕后,弹性阀芯200不再受力,此时弹性阀芯200依靠自身的弹性回复至密封状态,以防止气体或液体倒流。
42.本实用新型的医用单向阀的一种生产制造方法为:
43.步骤一:分别生产制造出成品弹性阀芯200、压盖300以及阀体100上端部还未向内倾斜形成缩口140的半成品阀体100’,其中半成品阀体100’为注塑一体成型;
44.步骤二:将弹性阀芯200和压盖300依次装入半成品阀体100’内;
45.步骤三:加热安装有弹性阀芯200和阀盖的半成品阀体100’的上端部,使半成品阀体100’的上端部使其变软,以易于整形;
46.步骤四:将半成品阀体100’固定,使用模具400挤压半成品阀体100’的上端部使其被挤压成向内倾斜的缩口140;或者旋转半成品阀体100’并向半成品阀体100’的上端部施加向内的压力f1使其倾斜形成向内倾斜的缩口140。
47.本实用新型的医用单向阀的凹槽与缩口对压盖形成双重限制,防止压盖受力过大而脱离阀体。
48.本实用新型的弹性内芯可采用硅胶或其他弹性体制备,加工精度高,尺寸稳定,单向阀开启压力稳定。半成品阀体的可以设计成单独一个零件一次性注塑成型,精度高,注塑模具简单,制造成本低。
49.上述说明书和实施例的描述,用于解释本实用新型保护范围,但并不构成对本实用新型保护范围的限定。