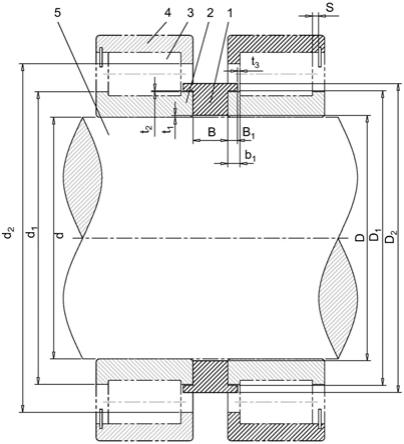
1.本实用新型属于轴承技术领域,具体涉及一种单列满装圆柱滚子轴承内隔圈及组合轴承,适用于两个或以上单列满装圆柱滚子轴承串联安装的内圈轴向定位,主要用于陆上或海上起重机主副钩缠绕系统、变幅缠绕系统和绞吸式挖泥船桥架起升滑轮系统的动滑轮组和定滑轮组。
背景技术:2.单列满装圆柱滚子轴承由内圈、外圈以及挡边引导的圆柱滚子组成。该类轴承的滚子没有配备滚子保持架;由于具有尽可能多的滚动体,因此该类轴承具有极高的径向承载能力和刚性,特别适用于紧凑的结构设计;目前单列满装圆柱滚子轴承的内隔圈设计和其它轴承的内隔圈设计没有差别,其结构特征为矩形横截面的简单回转体;由于单列满装圆柱滚子轴承属于半定位轴承,其内圈和外圈之间存在一定的轴向游隙,因此,在安装的过程中,内圈在轴的摩檫力作用下会产生相对外圈的轴向位移,导致现有的内隔圈侧面脱离内隔圈的接触,失去摩檫力支撑的内隔圈在重力或其它作用力的作用下,滑入轴的安装空间,阻挡轴的顺利安装。
3.鉴于上述情况,亟待研发一种单列满装圆柱滚子轴承内隔圈及组合轴承,能利用单列满装圆柱滚子轴承的内圈对内隔圈进行径向的定位,阻止其意外径向位移并影响轴的安装。
技术实现要素:4.针对现有技术中存在的上述缺陷,本实用新型的目的是提供一种单列满装圆柱滚子轴承内隔圈及组合轴承,充分利用了单列满装圆柱滚子轴承没有滚子保持架的结构特点,将单列满装圆柱滚子轴承内隔圈设计成端面带轴向外突缘的端面形状,对单列满装圆柱滚子轴承的内圈挡边进行了深度较小的包围,利用单列满装圆柱滚子轴承的内圈对内隔圈进行径向的定位,阻止内隔圈意外径向位移并影响轴的安装。
5.为实现上述目的,本实用新型采用如下技术方案:
6.本实用新型的第一方面提供了一种单列满装圆柱滚子轴承内隔圈,设于单列满装圆柱滚子轴承之间,套设于所述单列满装圆柱滚子轴承的轴上,所述单列满装圆柱滚子轴承内隔圈为圆环状,该单列满装圆柱滚子轴承内隔圈的边缘设有轴向外突缘;
7.所述轴向外突缘与所述单列满装圆柱滚子轴承的内圈挡边之间采用间隙配合;
8.所述单列满装圆柱滚子轴承内隔圈与所述单列满装圆柱滚子轴承的轴之间采用间隙配合。
9.优选地,所述单列满装圆柱滚子轴承内隔圈与所述单列满装圆柱滚子轴承的轴之间的间隙t1大于所述轴向外突缘与所述内圈挡边之间的间隙t2。
10.优选地,所述单列满装圆柱滚子轴承内隔圈与所述单列满装圆柱滚子轴承的轴之间的间隙t1为1~2mm。
11.优选地,所述轴向外突缘与所述内圈挡边之间的间隙t2为0.5~1mm。
12.优选地,所述轴向外突缘的外径d2小于所述单列满装圆柱滚子轴承的外圈挡边内径d2。
13.优选地,所述轴向外突缘的外径d2为:
14.d2=d1+(d2‑
d1)/6;
15.其中,d2为轴向外突缘的外径,单位为mm;
16.d1为轴向外突缘的内径,单位为mm;
17.d2为单列满装圆柱滚子轴承的外圈挡边内径,单位为mm;
18.d1为单列满装圆柱滚子轴承的内圈挡边内径,单位为mm。
19.优选地,所述轴向外突缘的轴向高度b1小于所述单列满装圆柱滚子轴承的内圈挡边的宽度b1。
20.优选地,所述轴向外突缘的轴向高度b1大于所述单列满装圆柱滚子轴承的内圈相对于所述单列满装圆柱滚子轴承的外圈的轴向位移s。
21.优选地,所述轴向外突缘的轴向高度b1为:
22.b1=0.8b1;
23.其中,b1为轴向外突缘的轴向高度,单位为mm;
24.b1为单列满装圆柱滚子轴承的内圈挡边的宽度,单位为mm。
25.本实用新型的第二方面提供一种组合轴承,包括套设在轴上的多个串联的单列满装圆柱滚子轴承以及设于所述单列满装圆柱滚子轴承之间的内隔圈;
26.所述内隔圈采用如本实用新型第一方面所述的单列满装圆柱滚子轴承内隔圈。
27.本实用新型的有益效果:
28.1、本实用新型的单列满装圆柱滚子轴承内隔圈及组合轴承,充分利用了单列满装圆柱滚子轴承没有滚子保持架的结构特点,将单列满装圆柱滚子轴承内隔圈设计成端面带外突缘的端面形状,对单列满装圆柱滚子轴承的内圈挡边进行了深度较小的包围,利用单列满装圆柱滚子轴承的内圈对内隔圈进行径向的定位,阻止内隔圈意外径向位移并影响轴的安装;
29.2、本实用新型的单列满装圆柱滚子轴承内隔圈适用于ina品牌的sl1818、 sl1829、sl1830、sl1822和sl1923系列型号,以及skf品牌的ncf和njg系列型号,或其它品牌具有相同或类似设计的单列满装圆柱滚子轴承。
附图说明
30.通过阅读参照以下附图对非限制性实施例所作的详细描述,本实用新型的其它特征、目的和优点将会变得更明显:
31.图1为本实用新型的组合轴承的结构示意图。
具体实施方式
32.为了能更好地理解本实用新型的上述技术方案,下面结合附图和实施例进一步说明本实用新型的技术方案。
33.结合图1所示,本实用新型所提供的单列满装圆柱滚子轴承内隔圈1,用于将单列
满装圆柱滚子轴承隔开;该单列满装圆柱滚子轴承内隔圈1设于单列满装圆柱滚子轴承之间,套设于单列满装圆柱滚子轴承的轴5上,其中单列满装圆柱滚子轴承内隔圈1为圆环状,该单列满装圆柱滚子轴承内隔圈1的边缘设有轴向外突缘;轴向外突缘与单列满装圆柱滚子轴承的内圈2挡边之间采用间隙配合;单列满装圆柱滚子轴承内隔圈1与单列满装圆柱滚子轴承的轴5之间采用间隙配合。
34.结合图1所示,其中单列满装圆柱滚子轴承内隔圈1的内径为d,单列满装圆柱滚子轴承内隔圈1的宽度为b,轴向外突缘的内径为d1,轴向外突缘的内径为d2,轴向外突缘的轴向高度为b1。轴的外径为d。单列满装圆柱滚子轴承的内圈2挡边外径d1,单列满装圆柱滚子轴承的外圈4挡边内径d2;单列满装圆柱滚子轴承的内圈2挡边的宽度为b1。单列满装圆柱滚子轴承内隔圈1与轴之间的间隙为t1,轴向外突缘与单列满装圆柱滚子轴承的内圈2挡边之间的间隙为t2,轴向外突缘的端面与单列满装圆柱滚子轴承的圆柱滚子3之间的间隙为t3。单列满装圆柱滚子轴承的内圈2相对于单列满装圆柱滚子轴承的外圈4的轴向位移为s。
35.结合图1所示,在一个具体的实施例中,单列满装圆柱滚子轴承内隔圈1的宽度b,按具体设计要求由单列满装圆柱滚子轴承的内圈2、圆柱滚子3以及内圈2 组成的单列满装圆柱滚子轴承之间的距离确定;
36.结合图1所示,在一个具体的实施例中,单列满装圆柱滚子轴承内隔圈1与单列满装圆柱滚子轴承的轴5之间的间隙t1大于轴向外突缘与内圈2挡边之间的间隙 t2,即t1>t2,能够保证单列满装圆柱滚子轴承内隔圈1相对单列满装圆柱滚子轴承的内圈2存在径向位移值达到t2的情况下,单列满装圆柱滚子轴承内隔圈1与轴之间存在间隙,从而不影响轴的安装。
37.结合图1所示,在一个具体的实施例中,单列满装圆柱滚子轴承内隔圈1与单列满装圆柱滚子轴承的轴5之间的间隙t1为1~2mm。
38.在一个具体的实施例中,轴向外突缘与单列满装圆柱滚子轴承的内圈2挡边之间的间隙t2为0.5~1mm。
39.结合图1所示,在一个实施例中,理论上只需要轴向外突缘的外径d2小于单列满装圆柱滚子轴承的外圈4挡边内径d2即可,但是考虑到需要为润滑油脂提供足够的通道,因此在具体的实施例中轴向外突缘的外径d2满足下述公式:
40.d2=d1+(d2‑
d1)/6;
41.其中,d2为轴向外突缘的外径,单位为mm;
42.d1为轴向外突缘的内径,单位为mm;
43.d2为单列满装圆柱滚子轴承的外圈4挡边内径,单位为mm;
44.d1为单列满装圆柱滚子轴承的内圈2挡边内径,单位为mm。
45.结合图1所示,在一个实施例中,轴向外突缘的轴向高度b1需要小于单列满装圆柱滚子轴承的内圈2挡边的宽度b1,以确保轴向外突缘端面与单列满装圆柱滚子轴承的圆柱滚子3之间的间隙t3大于零,保证两者之间不产生滑动摩擦;除此之外,轴向外突缘的轴向高度b1需要大于单列满装圆柱滚子轴承的内圈2相对于单列满装圆柱滚子轴承的外圈4的轴向位移s,以确保即使在轴的安装过程中,单列满装圆柱滚子轴承内隔圈1跟随单列满装圆柱滚子轴承的内圈2存在的轴向位移值达到轴向位移s的情况下,单列满装圆柱滚子轴承内隔圈1的轴向外突缘仍然受到单列满装圆柱滚子轴承的内圈2挡边的径向位移限制,不至
于产生超过数值超过t2 的径向位移;因此,在一个优选的实施例中,要达到上述情况,轴向外突缘的轴向高度b1需要满足下述公式:
46.b1=0.8b1;
47.其中,b1为轴向外突缘的轴向高度,单位为mm;
48.b1为单列满装圆柱滚子轴承的内圈2挡边的宽度,单位为mm。
49.结合图1所示,将上述的单列满装圆柱滚子轴承内隔圈1应用到组合轴承中,该组合轴承包括套设在轴上的多个串联的单列满装圆柱滚子轴承以及设于单列满装圆柱滚子轴承之间的内隔圈,其中内隔圈采用上述的单列满装圆柱滚子轴承内隔圈1,其具体安装在单列满装圆柱滚子轴承之间,套设于单列满装圆柱滚子轴承的轴5上。
50.综上所述,本实用新型的单列满装圆柱滚子轴承内隔圈及组合轴承,充分利用了单列满装圆柱滚子轴承没有滚子保持架的结构特点,将单列满装圆柱滚子轴承内隔圈设计成端面带外突缘的端面形状,对单列满装圆柱滚子轴承的内圈挡边进行了深度较浅的包围,利用单列满装圆柱滚子轴承的内圈对内隔圈进行径向的定位,阻止内隔圈意外径向位移并影响轴的安装;该单列满装圆柱滚子轴承内隔圈适用于 ina品牌的sl1818、sl1829、sl1830、sl1822和sl1923系列型号,以及skf品牌的ncf和njg系列型号,或其它品牌具有相同或类似设计的单列满装圆柱滚子轴承。
51.本技术领域中的普通技术人员应当认识到,以上的实施例仅是用来说明本实用新型,而并非用作为对本实用新型的限定,只要在本实用新型的实质精神范围内,对以上所述实施例的变化、变型都将落在本实用新型的权利要求书范围内。