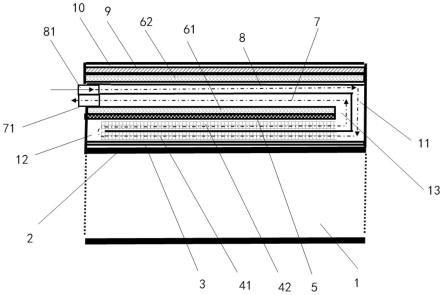
1.本发明涉及光热发电和熔盐储能技术领域,具体涉及一种熔盐管道加热单元、装置及方法。
背景技术:2.太阳能热发电系统主要由太阳岛、储热岛和常规岛等三部分组成,光热发电系统的热电转化效率主要取决于进口蒸汽参数,而进口蒸汽参数又取决于传热工质的传热性能。与传统的传热工质导热油、水或空气相比,熔融盐是最具前途的太阳能热电站的传热工质之一。目前国际上有三种流行的熔盐储热介质,分别是二元熔融盐、hitec和hitec xl三种,其中二元熔融盐为60%nano3和40%kno3的混合盐,在550℃具有非常好的稳定性、成本低、对普通材质管道及阀门具有较好的兼容性和较好的出热性能而被广泛应用于太阳能热发电储热系统中。
3.由于熔盐在管道内会不停的对外散热,为了避免熔盐在不同的运行模式下出现凝固,管道外需要设置电伴热带及保温材料,对其进行加热和保温。
4.然而,现有的熔盐系统管道及设备的加热方式主要以电热方式为主,这种加热方式存在以下缺点:加热功率密度较小,最大约为165w/m,不能满足快速升温和解冻的需求,加热效率低;且伴热电缆只能以一定的方式局部缠绕或者贴在管道外壁,加热不均匀。
技术实现要素:5.为解决背景技术中现有熔盐管道的加热方式加热功率密度较小、加热不均匀的问题,本发明提供了一种熔盐管道加热单元,具体技术方案如下。
6.一种熔盐管道加热单元,包括设于熔盐管道本体外壁上的电加热层;还包括设于电加热层外的催化燃烧加热层,所述催化燃烧加热层包括由内至外依次设置的第一催化燃烧层、第二催化燃烧层、烟气层和燃料层;所述燃料层的一端设有燃料入口,所述燃料层的另一端通过第一通道与所述第一催化燃烧层的一端连通,所述第一催化燃烧层的另一端通过第二通道与所述第二催化燃烧层的一端连通,所述第二催化燃烧层的另一端通过第三通道与所述烟气层的一端连通,所述烟气层的另一端设有烟气出口;所述燃料入口外接燃料喷射装置;所述第一催化燃烧层、第二催化燃烧层内填充有催化剂。
7.本发明中的电加热层的加热方式可以是阻抗加热方式或伴热电缆加热方式。本发明中电加热层用于使第一催化燃烧层、第二催化燃烧层内的催化剂达到燃料的起燃温度。
8.本发明中的燃料为碳氢小分子(分子含有碳原子个数小于5)的气体或者易挥发液体燃料,包括但不限于天然气、丁烷、甲醇、co、h2、合成气等。
9.本发明中的燃料在整个熔盐管道加热单元的流通顺序或者燃料通道依次为:燃料入口
→
燃料层
→
第一通道
→
第一催化燃烧层
→
第二通道
→
第二催化燃烧层
→
第三通道
→
烟气层,燃料催化燃烧产生的废气最终通过烟气出口排出。
10.本发明中烟气层与燃料层相邻设置,从而可以利用烟气层内废气的热量为燃料层
预热。
11.本发明中催化剂的形状为蜂窝状或者不规则的孔状结构。催化剂包含载体和活性组分,其中载体为含有硅铝氧化物的硅酸盐,或者是含铁、镍的泡沫金属,活性组分为pt、pd、ce、mn的金属单质或者氧化物。
12.优选地,所述第二催化燃烧层与所述烟气层之间还设有第一蓄热层,所述燃料层的外侧还设有第二蓄热层。由此,通过蓄热层来储存烟气层内废气中的废热,从而更好地为燃料层预热。蓄热层内填充有氧化铝蜂窝蓄热体。
13.为防止第一催化燃烧层、第二催化燃烧层产生的热量通过接触导热直接传递到烟气层被排出,优选地,所述第二催化燃烧层与所述第一蓄热层之间还设有隔热层。隔热层内填充有隔热材料,隔热材料包括岩棉、硅酸铝纤维等。
14.优选地,所述熔盐管道本体与所述第一催化燃烧层之间还设有导热层;所述第二蓄热层外还设有保温层;所述保温层外还设有保护层。导热层用于使电加热层的加热效果更加均匀。保温层用于包裹住整个燃料通道,防止热量散发。保护层用于保护和固定加热单元(保护层为一个铝皮外壳,起到固定和包裹保温层的作用)。
15.优选地,所述烟气层、燃料层、第一通道、第二通道和第三通道均为空腔。
16.第一通道作为燃料层与第一催化燃烧层之间的连接通道,其作用是将预热后的燃料和氧化剂引入到第一催化燃烧层中进行催化燃烧。第二通道作为第一催化燃烧层和第二催化燃烧层之间的连接通道,其作用是保证从第一催化燃烧层出来的未燃尽的燃料、氧化剂与烟气混合物能够进入第二催化燃烧层继续发生催化氧化燃烧,延长停留时间,提高燃烧效率。第三通道作为第二催化燃烧层与烟气层之间的连接通道,其作用是将第二催化燃烧层尾部排出的已经完全燃烧的烟气引入到烟气层中去。
17.优选地,所述燃料喷射装置上设有用于调节燃料流量的调节阀和用于测量燃料实际流量的计量阀。由此,可调节燃料催化燃烧的加热功率。
18.基于相同的发明构思,本发明还提供一种熔盐管道加热装置,包括多个上述的熔盐管道加热单元,多个所述熔盐管道加热单元首尾相接地安装在一条完整的熔盐管道本体上。每个加热单元独立加热,且加热单元的形状与对应熔盐管道的形状匹配,例如可以是直线、曲线或直线与曲线的组合。
19.基于相同的发明构思,本发明还提供一种利用上述熔盐管道加热单元实现的熔盐管道加热方法,包括如下步骤:
20.当熔盐管道本体内无熔盐且熔盐管道本体外壁温度低于t1时,启动电加热层对熔盐管道本体进行加热;
21.当熔盐管道本体外壁温度等于或高于t1时,电加热层停止工作,启动燃料喷射装置对熔盐管道本体进行加热;其中,t1高于燃料的起燃温度,取值范围为150≤t1≤200℃;
22.当熔盐管道本体外壁温度等于或高于t2时,向熔盐管道本体内泵入熔盐并将燃料喷射装置的燃料流量调节为fcg;其中,fcg=105%*qsr/qnet;qsr为熔盐管道加热单元的散热损失,qnet为燃料的低位发热值,270≤t2≤290℃。
23.上述加热方法为熔盐管道加热单元的预加热模式。由于熔盐温度过低会凝固,因此需要对熔盐管道进行预加热。上述方法首先通过电加热使温度达到燃料的起燃点,然后切换为燃料加热,为熔盐提供更大的加热功率密度和更好的加热均匀性。当熔盐管道本体
外壁温度达到目标温度t2时,加热单元进入保温模式,即根据散热损失来控制燃料流量,以提供跟散热损失等同的热量,从而将熔盐温度保持在目标温度t2附近。
24.优选地,当熔盐管道本体外壁温度等于或高于t1且小于t2时,燃料喷射装置的燃料流量为fjz;其中fjz=(t2-t1)*cpgd*mgd*120%/tjr;cpgd为熔盐管道本体的比热容,mgd为熔盐管道本体的质量,tjr为预热加热时间。在预加热模式中,为保证熔盐管道本体的温度在预热加热时间内达到t2,将燃料喷射装置的燃料流量设定为fjz。
25.优选地,当熔盐管道本体内有熔盐且熔盐管道本体外壁温度低于t3时,将燃料喷射装置的燃料流量调节为fmax;当熔盐管道本体外壁温度等于或高于t4时,关闭燃料喷射装置;其中,fmax为料喷射装置的最大燃料流量,210≤t3≤230℃,300≤t4≤350℃。
26.上述加热方法为熔盐管道加热单元的快速解冻模式。当因检修或其它原因导致熔盐管道本体外壁温度低于t3时,熔盐管道本体内的熔盐有凝固的风险,因此需启动解冻模式以最大燃料流量进行加热,防止熔盐凝固。
27.由于采用了以上技术方案,与现有技术相比较,本发明具有如下优点:
28.1)本发明采用电加热、催化燃烧加热相结合的方式,采用低品位的燃料作为热源,可以节约高品位电能。
29.2)相对于电加热,燃料催化燃烧的加热方式不仅加热功率密度更大,而且加热均匀,将其用于预热和解冻时,可以提升加热效率,缩短加热和解冻时间,同时加热和解冻过程温升更加均匀。
30.3)采用燃气明火加热虽然可以解决电加热方式的加热功率密度小的问题,但是存在局部火焰温度远高于熔盐,加热不均匀,对管道本体材料也容易造成损伤、氧化和变形等一系列安全问题。本发明采用催化燃烧加热,其与明火加热相比,反应过程温和,峰值温度低,燃烧反应区扩大,燃烧不产生有害的氮氧化物;同时在催化剂的作用下,燃烧完全,未燃尽co含量很低,是一种清洁高效的燃烧方式。
31.4)本发明采用催化燃烧加热方式,其工作反应温度位于150-500℃,与熔盐管道的外壁面温度工作需求范围接近,同时,催化燃烧在整个反应区域发生,反应区可以覆盖整个熔盐管道本体的外部壁面区域,可以实现均匀加热。
32.5)本发明采用催化燃烧和燃料为主要热源的方式,可以通过调节燃料的流量实现加热功率的改变,可以有效提升加热效率,缩短加热时间,更加快速的实现升温、保温和解冻,减少了熔盐温度下降和冻堵的风险。
33.6)本发明提出根据热损失的计算获得所需要的燃料供应量,做到按需加热,温度波动范围小,加热更加精准,系统运行更加稳定;同时可以节约燃料,降低能耗。
34.7)本发明通过烟气、空气与燃料逆流换热,回收烟气的余热,同时采用蓄热层将烟气的热量进行存储,降低了排烟温度,减小了热损失,同时强化了催化燃烧。
附图说明
35.图1为本发明熔盐管道加热单元的结构示意图;
36.图2为图1的a-a剖视图;
37.图3为本发明燃料喷射装置的结构示意图;
38.图4为本发明烟气出口和燃料入口的位置示意图;
39.图5为本发明熔盐管道加热装置的结构示意图。
具体实施方式
40.下面结合附图对本发明作进一步详细描述。
41.实施例1
42.如图1所示,一种熔盐管道加热单元,包括设于熔盐管道本体1外壁上的电加热层2,以及从电加热层2由内向外依次设置的导热层3、第一催化燃烧层41、第二催化燃烧层42、隔热层5、第一蓄热层61、烟气层7、燃料层8、第二蓄热层62、保温层9和保护层10。
43.如图2所示,所述燃料层8的一端设有燃料入口81,所述燃料层8的另一端通过第一通道11与所述第一催化燃烧层41的一端连通,所述第一催化燃烧层41的另一端通过第二通道12与所述第二催化燃烧层42的一端连通,所述第二催化燃烧层42的另一端通过第三通道13与所述烟气层7的一端连通,所述烟气层7的另一端设有烟气出口71。如图2箭头所示,燃料通道为燃料入口81
→
燃料层8
→
第一通道11
→
第一催化燃烧层41
→
第二通道12
→
第二催化燃烧层42
→
第三通道13
→
烟气层7,燃料催化燃烧产生的废气最终通过烟气出口71排出。所述烟气层7、燃料层8、第一通道11、第二通道12和第三通道13均为空腔。
44.导热层3由导热性能良好的铝片或铜片制成。第一催化燃烧层41和第二催化燃烧层42内填充有催化剂,催化剂的形状为蜂窝状或者不规则的孔状结构。催化剂包含载体和活性组分,其中载体为含有硅铝氧化物的硅酸盐,或者是含铁、镍的泡沫金属,活性组分为pt、pd、ce、mn的金属单质或者氧化物。隔热层5和保温层9内填充有隔热材料,隔热材料包括岩棉、硅酸铝纤维等。第一蓄热层61和第二蓄热层62内均填充有氧化铝蜂窝蓄热体。
45.如图3所示,燃料入口81外接有燃料喷射装置,燃料喷射装置包括依次连接的燃料罐14、计量阀15、调节阀16和喷射装置17,喷射装置17与燃料入口81连接。
46.如图2和图4所示,烟气出口71和燃料入口81即可以开设于熔盐管道加热单元的端部(如图2所示),也可以开设在熔盐管道加热单元的侧部(如图4所示)。
47.实施例2
48.如图5所示,一种熔盐管道加热装置,包括多个上述的熔盐管道加热单元18,多个所述熔盐管道加热单元18(实线)首尾相接地安装在一条完整的熔盐管道本体1(虚线)上。每个加热单元18独立加热,且加热单元的形状与对应熔盐管道的形状匹配,例如可以是直线,也可以是曲线。
49.实施例3
50.一种利用实施例1中的熔盐管道加热单元实现的熔盐管道加热方法。
51.本实施例中的电加热层采用伴热电缆的加热方式,采用丁烷作为催化燃烧的燃料,其储存于丁烷罐中,采用堇青石蜂窝体作为催化剂载体,并通过浸渍法负载催化剂pt,pt的负载量为5%。燃料的催化起燃温度(tqr)为150℃。
52.预加热模式:
53.预热阶段,当熔盐管道本体内无熔盐且熔盐管道本体外壁温度低于t1(170℃)时,启动电加热层对熔盐管道本体进行加热。
54.具体地,冷启动时,熔盐管道的本体温度为环境温度,环境温度为15℃。此时启动电加热,电加热目标温度为170℃,即比燃料的催化起燃温度高20℃。在预热阶段,当熔盐管
道的本体温度低于170℃时,对于熔盐管道装置单元,电加热电压为380v,安装的伴热电缆的发热功率为160w/m,以该功率进行持续加热,当熔盐管道的本体温度等于或者高于170℃,切断电源,电伴热关闭。
55.加热阶段,当熔盐管道本体外壁温度等于或高于t1时,电加热层停止工作,启动燃料喷射装置对熔盐管道本体进行加热。本阶段中燃料喷射装置的燃料流量为fjz;其中fjz=(t2-t1)*cpgd*mgd*120%/tjr;cpgd为熔盐管道本体的比热容,mgd为熔盐管道本体的质量,tjr为预热加热时间。
56.具体地,当熔盐管道本体外壁温度等于或高于170℃时,此时已达到燃料的最低起燃温度值,意味着燃料进入催化燃烧层后可以实现稳定燃烧,当电加热电源切断时,开启燃料喷射装置,液体丁烷燃料经过计量泵、喷射装置进入燃料层,然后进入第一催化燃烧层,接着从第一催化燃烧层出来,经过u形折返进入第二催化燃烧层继续反应直至燃尽,燃尽后的烟气经烟气层后最终通过烟气出口排出。同时,由于烟气层与燃料层相邻设置,从而可以利用烟气层内废气的热量为燃料层预热。
57.本实施例中,t2为280℃,t1为170℃;熔盐管道本体的比热容cpgd为0.5kj/(kg
·
℃);熔盐管道本体的长度为5m,管道本体外径为600mm,厚度为5mm,钢的密度为8g/cm3;加热时间tjr设定为1小时,计算得到加热阶段燃料喷射装置的流量应设定为fjz=0.2m3/h。
58.保温阶段,当熔盐管道本体外壁温度等于或高于t2(280℃)时,向熔盐管道本体内泵入熔盐并将燃料喷射装置的燃料流量调节为fcg;其中,fcg=105%*qsr/qnet;qsr为熔盐管道加热单元的散热损失,qnet为燃料的低位发热值。
59.具体地,在保温模式条件下,环境温度测定为9.5℃,风速为2m/s,保温层外壁平均温度为14.5℃,熔盐管道装置单元的保温层壳体的长度为5m;直径为1m;表面积为15.7m2;根据经典传热学计算公式,可以计算出熔盐管道装置单元的保温层壳体的散热损失(qsr),
60.其中,已知气流速度v(m/s),可根据周围环境与保温层表面之间的对流换热系数计算公式可先求得
[0061][0062]
忽略保温层外壁面的低温辐射作用,根据牛顿冷却公式q=ha(tw-tf),其中,q为周围环境与壁面的对流换热量,tw为壁面温度,tf为流体温度,a为壁面表面积,代入上述h,可计算出
[0063]
熔盐管道装置单元的保温层壳体与周围环境之间的对流换热量为
[0064]
qsr=21.5
×
15.7
×
(14.5-9.5)=1687.75w
[0065]
已知丁烷的低位发热量(qnet)为:123.56mj/nm3.
[0066]
考虑到熔盐管道装置单元具有散热损失,故供给的热量为散热损失的105%;依据如下公式求得燃料流量(fcg):
[0067]
fcg=105%qsr/qnet=105%
×
1687.75/(123.56
×
10^6)
×
3600=0.0516m3/h
[0068]
此外,在天气突变之后,在保温模式条件下,环境温度测定为2℃,风速为10m/s,保温层外壁平均温度为13℃;根据经典传热学计算公式,可以计算出熔盐管道装置单元的保温层壳体的散热损失(qsr),
[0069]
其中,已知气流速度v(m/s),可根据周围环境与保温层表面之间的对流换热系数
计算公式可先求得
[0070][0071]
忽略保温层外壁面的低温辐射作用,根据牛顿冷却公式q=ha(tw-tf),其中,q为周围环境与壁面的对流换热量,tw为壁面温度,tf为流体温度,a为壁面表面积,代入上述h,可计算出
[0072]
熔盐管道装置单元的保温层壳体与周围环境之间的对流换热量为
[0073]
qsr=33.8
×
15.7
×
(13-2)=5837.26w
[0074]
已知丁烷的低位发热量(qnet)为:123.56mj/nm3.
[0075]
考虑到熔盐管道装置单元具有散热损失,故供给的热量为散热损失的105%;依据如下公式求得燃料流量(fcg),
[0076]
fcg=105%qsr/qnet=105%
×
5837.26/(123.56
×
10^6)
×
3600=0.1786m3/h。
[0077]
由于熔盐温度过低会凝固,因此需要对熔盐管道进行预加热。上述方法首先通过电加热使温度达到燃料的起燃点,然后切换为燃料加热,为熔盐提供更大的加热功率密度和更好的加热均匀性。当熔盐管道本体外壁温度达到目标温度280℃时,加热单元进入保温模式,即根据散热损失来控制燃料流量,以提供跟散热损失等同的热量,从而将熔盐温度保持在目标温度280℃附近。
[0078]
快速解冻模式:
[0079]
当熔盐管道本体内有熔盐且熔盐管道本体外壁温度低于t3(220℃)时,将燃料喷射装置的燃料流量调节为fmax;当熔盐管道本体外壁温度等于或高于t4(320℃)时,关闭燃料喷射装置;其中,fmax为料喷射装置的最大燃料流量,具体值为1m3/h。
[0080]
当因检修或其它原因导致熔盐管道本体外壁温度低于220℃时,熔盐管道本体内的熔盐有凝固的风险,因此需启动解冻模式以最大燃料流量进行加热,防止熔盐凝固。
[0081]
最后应说明的是:以上实施例仅用以说明本发明的技术方案,而非对其限制;尽管参照前述实施例对本发明进行了详细的说明,本领域的普通技术人员应当理解:其依然可以对前述各实施例所记载的技术方案进行修改,或者对其中部分技术特征进行等同替换;而这些修改或者替换,并不使相应技术方案的本质脱离本发明各实施例技术方案的精神和范围。