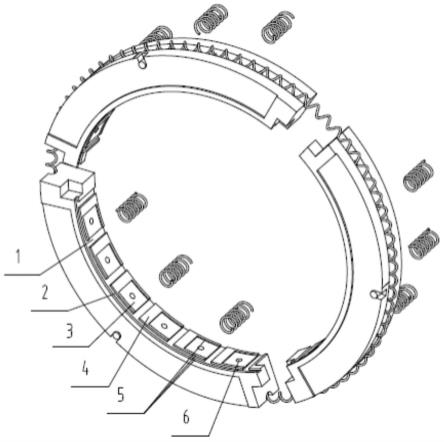
1.本发明涉及一种开有节流小孔的环瓣式浮环密封,属于非接触式流体密封技术领域,适用于多种旋转机械的轴封。
背景技术:2.浮环密封最早应用于航空发动机主轴承腔的密封中,因其具有结构紧凑、易装配、泄漏率低等优点,随后也被应用于火箭发动机的涡轮泵系统中。其中,在环瓣密封环内表面上开动静压槽,提高承载力,从而实现环瓣密封的长寿命运行,是行之有效的办法。再在浮环上开有节流小孔,利用流体动压效应和流体静压效应,来进一步改善整体结构的润滑与密封情况。
3.根据浮环内表面上开设的槽区可以分析出,由于静压槽的深度较大,起到了引流作用,进而保持较好的润滑效应;同时在内表面开有动压槽,动压槽槽根处在动压效应下能够显著提升气膜开启力,形成较好的承载作用。但当转轴启动或处于低转速时会与浮环发生磨损,尤其是动压槽磨损严重,此缺点会影响整体的密封效果。
4.总的来说,单纯地开有动静压槽并基于动压效应的密封技术,虽然可以有效提高承载力,减小泄漏率,但开启前浮环与转轴的磨损问题无法解决。所以在此基础上添加节流小孔,通过小孔引入静压承载力,变成基于动静压混合润滑效应,从而避免此问题。
技术实现要素:5.本发明提供了一种开有节流小孔的环瓣式浮环密封,通过巧妙地设计节流小孔与动压槽、静压槽配合构建了多段密封段依次连接后首尾连接的新型环瓣式浮环密封。
6.本发明的技术方案是:一种开有节流小孔的环瓣式浮环密封,包括多个分瓣密封段,多个分瓣密封段依次连接成环瓣式浮环密封本体,环瓣式浮环密封本体端面一侧为介质高压侧,环瓣式浮环密封本体端面另一侧为介质低压侧,每段分瓣密封段的结构相同,具体为:每段分瓣密封段内表面开有轴向静压槽1和周向静压槽2且二者相连;每两个相邻轴向静压槽1之间开有动压槽3,相邻轴向静压槽1中的一个轴向静压槽1与动压槽3入口处连接且形成台阶,相邻轴向静压槽1中的另一个轴向静压槽1与动压槽3出口处之间存在密封脊4;周向静压槽2与介质低压侧、动压槽3与周向静压槽2、动压槽3与介质高压侧之间形成密封凸台5;节流小孔6开在动压槽3中间位置且与辅助孔7共同贯穿分瓣密封段。
7.每个分瓣密封段均匀分布的轴向静压槽1为4-7个,周向静压槽2为1个;动压槽3的数量为轴向静压槽1的数量减1。
8.每个轴向静压槽1的宽度l3为0.7~1.7mm,每个周向静压槽2的宽度b2为0.7~1.7mm;每个动压槽3的周向宽度l1为8~10mm,每个动压槽3的轴向宽度b3为2~5mm。
9.每个轴向静压槽1和周向静压槽2的槽深h1均为0.03-0.05mm,每个动压槽3的槽深h2为7-15μm。
10.所述动压槽3出口与相隔轴向静压槽1间密封脊4的宽度l2为3-5mm。
11.所述周向静压槽2与介质低压侧,动压槽3与介质高压侧,动压槽3与周向静压槽2所形成的三处密封凸台5的宽度b1、b4、b5均为0.3~0.7mm。
12.所述节流小孔6靠近环瓣式浮环密封内圈,辅助孔7靠近环瓣式浮环密封外圈;辅助孔7的孔径大于节流小孔6,节流小孔6的深度大于辅助孔7的深度。
13.所述节流小孔6的直径d为0.2~0.3mm。
14.本发明的有益效果是:本发明采用环瓣搭接头进行拼接组装,便于加工和安装。本发明在环瓣浮环内表面开有动静压槽,静压槽可以将高压侧介质压力引入,起到较好的润滑效果;与密封脊相连的动压槽的槽根处会形成雷利台阶,气体在转轴转速和偏心率共同作用下,产生较强的动压效应,起到很好的承载作用。本发明开有节流小孔,这样在环瓣浮环处于启动前或者低转速的情况下,气体流经小孔起到很好的静压润滑效果,产生承载力,使环瓣浮环浮起,从而避免环瓣浮环在开启或者低转速的情况下所产生的磨损现象。
附图说明
15.图1是本发明一种开有节流小孔的环瓣式浮环密封的结构示意图;
16.图2是本发明一种开有节流小孔的环瓣式浮环密封三维结构主视示意图;
17.图3是本发明一种开有节流小孔的环瓣式浮环密封三维结构侧视示意图;
18.图4是一个分瓣密封段的三维结构示意图;
19.图5是本发明节流小孔、辅助孔示意图;
20.图6是两种节流小孔位置示意图;
21.图7本发明一个分瓣密封段的平面投影意图;
22.图8是本发明浮环密封的平面槽深示意图;
23.图9是本发明浮环密封槽区的结构参数示意图;
24.图10是本发明一种浮环密封的受力分析图;
25.图中各标号为:1-轴向静压槽,2-周向静压槽,3-动压槽,4-密封脊,5-密封凸台,6-节流小孔,7-辅助孔,b
1-周向静压槽与压力出口处密封凸台的宽度,b
2-周向静压槽宽度,b
3-动压槽轴向宽度,b
4-动压槽与压力入口处密封凸台的宽度,b
5-周向静压槽与动压槽之间的密封凸台宽度,b
t-浮环轴向宽度,l
1-动压槽周向宽度,l
2-密封脊宽度,l
3-轴向静压槽宽度,h
1-静压槽深度,h
2-动压槽深度,h
m-浮环内表面其它坝区气膜厚度,d-节流小孔直径,p
up-高压侧介质压力,p
down-低压侧介质压力,f
rad-周向弹簧力,f
s-压缩弹簧力,f
n-次密封面支撑力,f-次密封面与密封座的摩擦力,f-气膜承载力。
具体实施方式
26.下面结合附图和实施例,对发明做进一步的说明,但本发明的内容并不限于所述范围。
27.实施例1:如图1-10所示,一种开有节流小孔的环瓣式浮环密封,包括多个分瓣密封段,多个分瓣密封段依次连接成环瓣式浮环密封本体,环瓣式浮环密封本体端面一侧为介质高压侧,环瓣式浮环密封本体端面另一侧为介质低压侧且介质低压侧开有周向凹槽,每段分瓣密封段的结构相同,具体为:每段分瓣密封段内表面开有轴向静压槽1和周向静压槽2且二者相连通,起到引流槽作用,将高压侧介质压力引入槽内,保持较好润滑效应;每两
个相邻轴向静压槽1之间开有动压槽3,相邻轴向静压槽1中的一个轴向静压槽1与动压槽3入口处连通且形成雷利台阶,相邻轴向静压槽1中的另一个轴向静压槽1与动压槽3出口处之间存在密封脊4;周向静压槽2与介质低压侧、动压槽3与周向静压槽2、动压槽3与介质高压侧之间形成密封凸台5;节流小孔6开在动压槽3中间位置且与辅助孔7共同贯穿分瓣密封段。其中,轴向静压槽1入口处位于介质高压侧且与周向静压槽2相连通,即起到了引流槽作用,因此静压槽((轴向静压槽和周向静压槽)内的气体压力均为高压侧介质压力,在相邻轴向静压槽1之间开有动压槽3,其中动压槽3入口处与轴向静压槽1一端相连通,从而将高压侧介质压力在动压槽3入口处引入。对于同一个环瓣式浮环密封的所有分瓣密封段各设计参数尺寸、数量相同。
28.可选地,每个分瓣密封段均匀分布的轴向静压槽1为4-7个(如可以为4个、5个、7个等),周向静压槽2为1个;动压槽3的数量为轴向静压槽1的数量减1。
29.可选地,每个轴向静压槽1的宽度l3为0.7-1.7mm(如可以取0.7mm、1.1mm、1.2mm、1.7mm等),每个周向静压槽2的宽度b2为0.7-1.7mm(如可以取0.7mm、1.0mm、1.35mm、1.7mm等);每个动压槽3的周向宽度l1为8-10mm(如可以取8mm、8.5mm、9mm、10mm等),每个动压槽3的轴向宽度b3为2-5mm(如可以取2mm、3mm、4.5mm、5mm等)。
30.可选地,每个轴向静压槽1和周向静压槽2的槽深h1为0.03-0.05mm且取值相同(如可以取0.03mm、0.04mm、0.05mm等),每个动压槽3的槽深h2为7-15μm(如可以取7μm、9μm、10μm、15μm等)。
31.可选地,所述动压槽3出口与相隔轴向静压槽1间密封脊4的宽度l2为3-5mm(如可以取3mm、4mm、5mm等)。
32.可选地,所述周向静压槽2与介质低压侧,动压槽3与介质高压侧,动压槽3与周向静压槽2所形成的三处密封凸台5的宽度b1、b4、b5均为0.3-0.7mm(如可以取0.3mm、0.45mm、0.6mm、0.7mm等)。
33.可选地,所述节流小孔6靠近环瓣式浮环密封内圈,辅助孔7靠近环瓣式浮环密封外圈;辅助孔7的孔径大于节流小孔6(孔径可以根据实际节流需求来进行调整),节流小孔6的深度大于辅助孔7的深度。通过该辅助孔的设计,可以起到高低压转换,降压作用,控制气体流速,使节流小孔达到节流效果。
34.可选地,所述节流小孔6的直径d为0.2~0.3mm(如可以取0.2mm、0.25mm、0.3mm等);所述节流小孔6的深度比辅助孔7深度长3-5mm左右(如可以取节流小孔6的深度比辅助孔7深度长3mm、4.5mm、5mm等)。
35.本发明的工作原理是:启动前,环瓣浮环在周向弹簧的箍紧力作用下,与转轴贴紧,处于静止状态,此时浮环楔形效应最强,偏心率最大。此情况下,润滑气体流经节流小孔,并在静压槽(轴向静压槽和周向静压槽)作用下将高压处介质压力引入,形成气膜力,以支撑负载,防止转轴在启动时或转轴处于低转速时与浮环发生磨损。然后当浮环浮起后,由于动压槽入口与轴向静压槽相通,从而引入高压侧介质压力,在动压槽与密封脊接触的槽根处,由于转速剪切和偏心率的作用,动压槽根的雷利台阶结构形成流动阻力,气体被挤压,形成动压效应,压力明显升高。至此在动静压混合润滑效应作用下,浮环与转轴间形成一层刚度非常大的气膜,隔离介质,从而形成密封。
36.具体而言,如图1-4所示,本发明由个分瓣密封段组成,其中每段之间由单搭接头
进行搭接,整体再由外界周向弹簧进行箍紧,减小密封环与转轴初始气膜间隙(通过周向弹簧的调节,当改变工况参数时,可以使浮环在始终保持在稳定状态,且能保证在稳定状态时气膜间隙最小,从而降低泄漏率)。轴向方向的轴向弹簧产生弹簧压缩力使浮环次密封面与密封座压紧,防止气体在次密封面的泄漏。防转销限制浮环旋转运动,只能让其进行竖直方向运动。
37.在每段分瓣密封段内表面开有轴向静压槽和周向静压槽,其中轴向静压槽1与周向静压槽2相连通,周向静压槽与介质低压侧间存在密封凸台5。静压槽相当于引流槽,起到将入口高压侧介质压力引入槽内的作用,有较好的润滑效应,形成气膜力,以支撑负载,防止转轴与浮环发生磨损。如图中所示,在每段分瓣密封段内表面开有相同个数的轴向静压槽和周向静压槽,即7个轴向静压槽和1个周向静压槽。
38.在每段分瓣密封段内表面开有动压槽3,动压槽3与周向静压槽2、动压槽3和介质高压侧间分别存在密封凸台5。由于动压槽3入口与轴向静压槽1相连通,从而在入口处将高压侧介质压力引入,在动压槽3与密封脊4接触的槽根处,由于转速剪切和偏心率的作用,动压槽根的台阶结构形成流动阻力,气体被挤压,形成动压效应,承载力明显升高。从而提高整体密封效果。所有动压槽的入口方向保持一致(即入口都朝左,或都朝右,以图7示意,入口朝左)。
39.如图5至6所示,在每段环瓣浮环内表面开有节流小孔6。节流小孔6设置在动压槽3的中间处,其分布规律为;将浮环展开,可以在每个动压槽上开节流小孔,也可以隔着开,也可以隔两个开。对于图中示意下,将浮环展开,就变成一个开有18个动压槽的矩形,图6中展示了每个动压槽上开节流小孔还展示了隔两个动压槽上开节流小孔。对于每个环瓣来说,开节流小孔数量均相同。小孔位置也一样,都在动压槽中间,而且都在每个浮环密封段相同位置。
40.如图7至9所示,对于开有节流小孔的环瓣式浮环密封环的每个轴向静压槽1的宽度l3为0.7~1.7mm,每个周向静压槽2的宽度b2为0.7~1.7mm;每个静压槽(轴向静压槽和周向静压槽)的深度h1为0.03~0.05mm。每个动压槽3的周向宽度l1为8~10mm,每个动压槽3的轴向宽度b3为2~5mm;每个动压槽3的深度h2为7~15μm。每个动压槽3出口处与另一个相隔轴向静压槽1之间的密封脊4的周向宽度l2为3~5mm。所述周向静压槽2与介质低压侧,动压槽3与介质高压侧,动压槽3与周向静压槽2所形成的密封凸台5的宽度依次为b1、b4、b5,取值均为0.3~0.7mm。每个节流小孔直径6的直径d为0.2~0.3mm。
41.如图10所示,为开有节流小孔的环瓣式浮环受力分析图,其中:p
up
为高压侧介质压力,p
down
为低压侧介质压力,f
rad
为周向弹簧力,fs为压缩弹簧力,fn为次密封面支撑力,f为次密封面与密封座的摩擦力,f为气膜承载力。当浮环处于稳定状态时,各方向均受力平衡,合力为零。对其进行轴向方向的受力分析,列出力平衡方程就可以求出次密封面支撑力fn,再乘以摩擦系数μ,即可进而求出次密封面摩擦力f。对其进行竖直方向受力分析,竖直方向的力分别为:周向弹簧力f
rad
,次密封面摩擦力f,气膜承载力f,那么通过受力分析图可以看出,在竖直方向上,当气膜承载力f等于周向弹簧力f
rad
加上次密封面摩擦力f时,此时浮环竖直方向受力平衡,达到稳定状态。
42.将本实施例开有节流小孔的环瓣式浮环密封与不开有节流小孔的环瓣式浮环密封的进行数值对比(开孔指的是每个动压槽上都开有节流小孔)。工况参数:高压侧介质压
力p
up
=0.4mpa,低压侧介质压力p
down
=0.1mpa,转速an=20000r/min,偏心率ε=0.4,初始气膜间隙h0=2.8μm,工作温度t=293k。数值结果如表1所示:
43.表1
44.密封形式唇口处泄漏率g/s气膜承载力n有节流小孔0.06133无节流小孔0.058129
45.从表1可以看出,本实施例开有节流小孔的环瓣式浮环在唇口处的泄漏率要略大于无节流小孔的环瓣式浮环,但是本发明采用多段式设计,可以跟随转轴自动对心,根据这一特点就可以适当减小气膜间隙,从而减小由于较大气膜间隙所带来的泄漏率较大问题。再通过气膜承载力的对比,可以看出,开有节流小孔的环瓣浮环的气膜承载力要大于不开有节流小孔的环瓣浮环,说明开有节流小孔的环瓣浮环有更好的承载效果。
46.上面结合附图对本发明的具体实施方式作了详细说明,但是本发明并不限于上述实施方式,在本领域普通技术人员所具备的知识范围内,还可以在不脱离本发明宗旨的前提下做出各种变化。