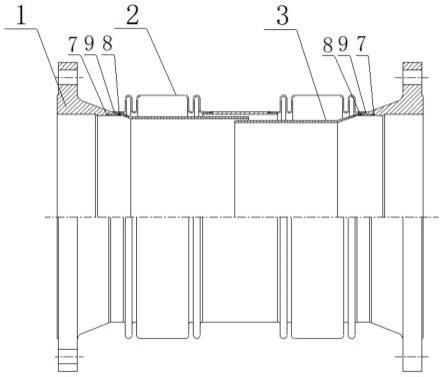
1.本发明涉及一种导流筒连接结构及其连接方法。
背景技术:2.金属波纹管膨胀节是lng运输领域低温管路系统中的重要柔性补偿装备,目前,金属波纹管膨胀节基本上以法兰连接方式为主。考虑到管路内部高流速介质导流,以及双流向的要求,膨胀节多设置双导流筒,且导流筒与法兰采用搭接角焊缝的连接结构,如图1所示。由于搭接角焊缝沿轴向方向的抗拉强度高,而沿径向方向的抗弯强度低。而导流筒属于悬臂梁结构,当有高速介质持续冲击导流筒尾部时,容易造成导流筒尾部振动。导流筒尾部振动产生的力叠加导流筒的长度,会在搭接角焊缝位置产生弯矩,容易造成导流筒环向焊缝沿径向折断开裂。
3.公开号为cn110985800a的中国专利,公开了一种防阻畅流膨胀节,该专利提供了一种将导流筒翻边改为扩口结构,并增设垫环(长度需≥100mm)的新型烟气轮机进出口膨胀节导流筒。
4.公开号为cn201462308u的中国专利,公开了一种新型烟气轮机进出口膨胀节导流筒,该专利提供了一种采用柔性组合导流管,进而提供了一种较大轴向、横向和角向位移的防阻畅流膨胀节。
5.公开号为cn209800957u的中国专利,公开了一种耐强气流冲刷的金属膨胀节,对常规导流筒结构进行了改进,设置进口导流筒和出口导流筒,进口导流筒的内径与进口接管内径等直径,两者共面有效提高导流筒的通流面积,大大减小了高强度通流介质对导流筒的冲刷,在保持金属膨胀节良好补偿性能的同时,提高金属膨胀节使用安全性和寿命。
6.公开号为cn209800957u的中国专利,公开了一种用于高温膨胀节的分段式导流密封筒,包括导流筒a和导流筒b,导流筒a的一端和导流筒b的一端均与对应侧的膨胀节的筒节焊接,导流筒a的另一端和导流筒b的另一端在膨胀节的内腔中部交错,导流筒a包括低热力隔热筒和分段导流筒,低热力隔热筒的一端焊接在筒节的内壁上,另一端与分段导流筒的筒面平齐焊接,分段导流筒的一端焊接在筒节的内壁上,低热力隔热筒、筒节内壁与分段导流筒围成的空间内填充有隔热材料,在分段导流筒和导流筒b交错位置设有将间隙进行密封的密封补偿波纹管,防止介质进入导流筒与波纹管之间的腔体,产生结焦,导致导流筒开裂;另一方面可以防止导流筒受高温热膨胀而产生扭曲变形,造成导流筒与筒节连接处焊缝开裂。
7.上述现有技术分别针对导流筒焊缝防冲击或防振动,提出了解决方法,但均需要对导流筒结构进行改造,并未从根源解决高流速介质冲击下,导流筒焊缝直接受介质冲刷以及振动脱落的问题。
技术实现要素:8.为解决上述技术问题,本发明提供一种导流筒连接结构及其连接方法,有效消除
导流筒因高速介质冲刷及振动导致的环向焊缝开裂隐患,避免因导流筒脱落现象造成管路系统附近设备的失效,增强金属波纹管膨胀节作为管路系统重要柔性补偿装备的安全服役周期。
9.本发明的目的是通过以下方案实现的:一种导流筒连接结构,包括:连接法兰、波纹管和导流筒。
10.其中,连接法兰内径处设置有与导流筒同壁厚的防焊缝冲击凸台和塞焊盲孔。
11.导流筒为端部翻边带直段结构,且沿圆周均布有多个排液孔。
12.多个塞焊通孔沿导流筒圆周间隔布置,其数量与塞焊盲孔相同。
13.进一步的,连接法兰与导流筒环向焊接,连接法兰的塞焊盲孔和导流筒上的塞焊通孔通过塞焊的方式连接。
14.连接法兰与波纹管通过环向焊接连接。
15.优选的,连接法兰与导流筒之间的环向焊接方式为锁底对接焊。
16.优选的,连接法兰与波纹管之间的环向焊接方式为锁底对接焊。
17.优选的,防焊缝冲击凸台设置在导流筒与连接法兰环向焊缝前端15mm-25mm的范围内。
18.优选的,防焊缝冲击凸台的宽度为10mm-15mm。
19.优选的,导流筒上的塞焊通孔为“v”型。
20.优选的,塞焊通孔沿导流筒圆周弧长200mm-250mm的间隔进行设置。
21.优选的,塞焊盲孔深入连接法兰母材基体3mm-5mm深。
22.本发明除了提供一种导流筒连接结构以外,还进一步提供一种波纹管膨胀节的连接方法,具体包括以下步骤:
23.将连接法兰与导流筒,塞焊通孔与塞焊盲孔,连接法兰与波纹管施焊到位,完成波纹管膨胀节的连接。
24.优选的,当波纹管膨胀节为外套型波纹管膨胀节时,连接方法具体如下:
25.将连接法兰与导流筒环向焊接的第一环焊缝施焊到位,再将塞焊通孔与塞焊盲孔塞焊的塞焊缝施焊到位,最后将连接法兰与波纹管环向焊接的第二环焊缝施焊到位,完成防冲击振动脱落的导流筒连接结构在外套型波纹管膨胀节上的连接。
26.当波纹管膨胀节为内插型波纹管膨胀节时,连接方法具体如下:
27.将连接法兰与波纹管环向焊接的第二环焊缝施焊到位,再将连接法兰与导流筒环向焊接的第一环焊缝施焊到位,最后将塞焊通孔与塞焊盲孔塞焊的塞焊缝施焊到位,完成防冲击振动脱落的导流筒连接结构在内插型波纹管膨胀节上的连接。
28.与现有技术相比,本发明具备以下优点:
29.本发明提供的一种导流筒连接结构及其连接方法,通过设置塞焊缝使得导流筒尾部振动产生的力叠加导流筒的长度而形成的弯矩,将首先由塞焊缝吸收,使得传递到导流筒环向焊缝的力矩变小。
30.通过设置防冲击凸台使得高速流体介质将直接冲刷凸台本体,而对导流筒焊缝产生一定遮挡和缓冲效果。由于凸台本体为锻制法兰或轧制钢板,材料的均匀性较好,整体力学性能且优于焊缝本体,可以解决原来搭接角焊缝冲蚀失效的问题。
31.此外,防冲击凸台还使得导流筒与凸台的连接环向焊缝,由原先的角焊缝变为对
接焊缝,对接焊缝的抗弯性能要优于角焊缝,因此,即使在塞焊缝全部失效的极端情况下,该导流筒的环向焊缝性能依然比现有结构有所提升。
附图说明
32.图1为本发明背景技术中低温膨胀节示意图;
33.图2为本发明中采用防冲击振动脱落的导流筒连接结构的膨胀节连接示意图;
34.图3为本发明中连接法兰的局部示意图;
35.图4为本发明中导流筒局部结构示意图;
36.图5为本发明实施例中连接结构在外套型波纹管膨胀节上的连接局部示意图;
37.图6为本发明实施例中连接结构在内插型波纹管膨胀节上的连接局部示意图。
38.图中,1为连接法兰;2为波纹管;3为导流筒;4为防焊缝冲击凸台;5为塞焊盲孔;6为塞焊通孔;7为第一环焊缝;8为塞焊缝;9为第二环焊缝。
具体实施方式
39.下面结合附图和实施例对本发明作进一步的详细说明。可以理解的是,此处所描述的具体实施例仅仅用于解释本发明,而非对本发明的限定。另外还需要说明的是,为了便于描述,附图中仅示出了与本发明相关的部分而非全部结构。
40.如图2至图4所示,本发明的技术方案中提供一种导流筒连接结构,包括:连接法兰1、波纹管2和导流筒3。
41.其中,连接法兰1内径处设置有与导流筒3同壁厚的防焊缝冲击凸台4和塞焊盲孔5。
42.导流筒3为端部翻边带直段结构,且沿圆周均布有多个排液孔。
43.多个塞焊通孔6沿导流筒3圆周间隔布置,其数量与塞焊盲孔5相同。
44.进一步的,连接法兰1与导流筒3环向焊接,连接法兰1的塞焊盲孔5和导流筒3上的塞焊通孔6通过塞焊的方式连接。
45.连接法兰1与波纹管2通过环向焊接连接。
46.在本发明的一些实施例中,连接法兰1与导流筒3之间的环向焊接方式为锁底对接焊,连接法兰1与波纹管2之间的环向焊接方式为锁底对接焊。
47.在这些实施例中,采用锁底对接焊的方式代替传统的搭接角焊缝,在提高该焊缝成形质量的同时,可有效降低高流速介质造成的冲刷减薄风险。
48.在本发明的一些实施例中,防焊缝冲击凸台4设置在导流筒3与连接法兰1环向焊缝前端15mm-25mm的范围内,防焊缝冲击凸台4的宽度为10mm-15mm。
49.在本发明的一些实施例中,导流筒3上的塞焊通孔6为“v”型。
50.在本发明的一些实施例中,塞焊通孔6沿导流筒3圆周弧长200mm-250mm的间隔进行设置,塞焊盲孔5深入连接法兰1母材基体3mm-5mm深。在这些实施例中,设置深入连接法兰1母材基体的塞焊结构,能够进一步降低因导流筒3悬臂结构产生的振动开裂问题。
51.本发明的技术方案中,除了提供一种导流筒连接结构以外,还进一步提供一种波纹管膨胀节的连接方法,具体包括以下步骤:
52.将连接法兰1与导流筒3,塞焊通孔6与塞焊盲孔5,连接法兰1与波纹管2施焊到位,
完成波纹管膨胀节的连接。
53.如图5所示,在本发明的一些实施例中,当波纹管膨胀节为外套型波纹管膨胀节时,连接方法具体如下:
54.将防焊缝冲击凸台4设置在导流筒3与连接法兰1环向焊缝前端15mm,防焊缝冲击凸台4的宽度为10mm。塞焊通孔6沿导流筒3圆周弧长200mm的间隔进行设置,塞焊盲孔5深入连接法兰1母材基体3mm。
55.将连接法兰1与导流筒3环向焊接的第一环焊缝7施焊到位,再将塞焊通孔6与塞焊盲孔5塞焊的塞焊缝8施焊到位,最后将连接法兰1与波纹管2环向焊接的第二环焊缝9施焊到位,完成防冲击振动脱落的导流筒连接结构在外套型波纹管膨胀节上的连接。
56.如图6所示,在本发明的一些实施例中,当波纹管膨胀节为内插型波纹管膨胀节时,连接方法具体如下:
57.将防焊缝冲击凸台4设置在导流筒3与连接法兰1环向焊缝前端25mm的范围内,防焊缝冲击凸台4的宽度为15mm。塞焊通孔6沿导流筒3圆周弧长250mm的间隔进行设置,塞焊盲孔5深入连接法兰1母材基体5mm。
58.将连接法兰1与波纹管2环向焊接的第二环焊缝9施焊到位,再将连接法兰1与导流筒3环向焊接的第一环焊缝7施焊到位,最后将塞焊通孔6与塞焊盲孔5塞焊的塞焊缝8施焊到位,完成防冲击振动脱落的导流筒连接结构在内插型波纹管膨胀节上的连接。
59.以上是本发明的优选实施方式,应当指出,对于本技术领域的普通技术人员来说,在不脱离本发明原理的前提下,还可以作出若干改进和润饰,这些改进和润饰也应视为本发明的保护范围。