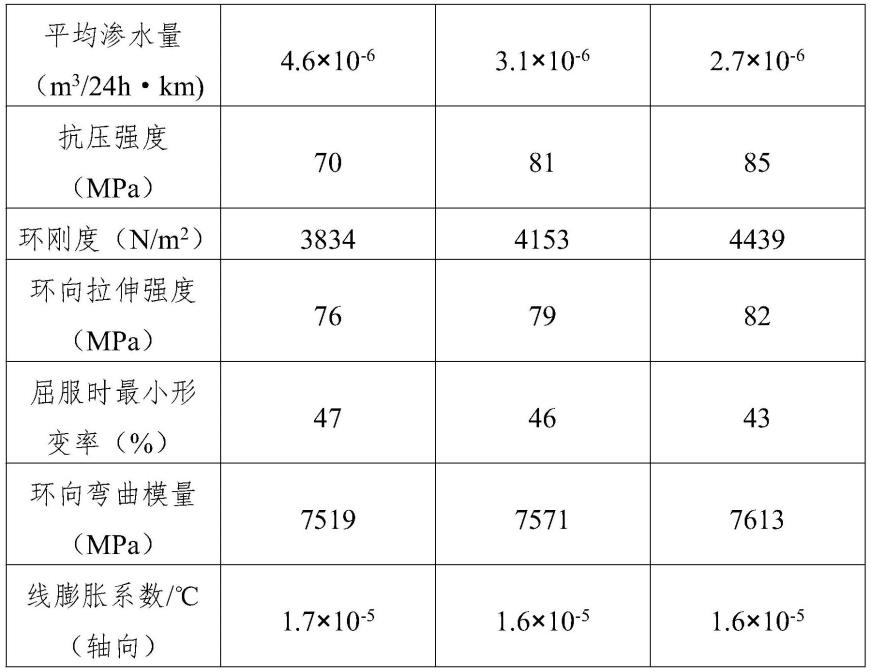
1.本发明属于管道施工技术领域,尤其涉及一种竹缠绕复合管的连接装置及方法。
背景技术:2.在竹缠绕复合管现场施工过程中,由于竹缠绕复合管长度平均,在遇到拐弯、水泥井处,工人习惯将竹缠绕复合管现场切割进行安装作业,且切口处不做防护处理,对管道的使用耐久性以及管材强度都会产生较大的影响。目前使用的竹缠绕复合管连接方式为承插式的柔性连接方式,插口处采用双胶圈型密封,而承口处是表面光滑的内台阶式,现场一旦发生切割,原有插口消失管身就无法与承口形成连接。
3.原有的竹缠绕复合管承在插口处均采用玻璃钢类型的制作材料,切割后管身作为插口就不再是原有的玻璃钢材质,且承口也要做成球墨铸铁管样式的。而且,竹缠绕复合管由于主体材料使用的是竹材,切割后端面的防护处理也是需要解决的问题。竹缠绕复合管的管身不同于球磨铸铁管,球磨铸铁管采用旋转熔铸的工艺,管道外径可以做到一致,竹缠绕复合管由于制作工艺不同,脱模过程中采用抽拔方式,所以管道制作模由承口向插口模具外径不断缩小,大小端差值在一公分左右,承口内径有限。
4.申请号为cn2015210309810的专利公开了一种适用于竹缠绕复合管的法兰连接结构,包括法兰和法兰连接所依附的竹缠绕复合管,法兰套在竹缠绕复合管上,竹缠绕复合管端部的外表面的周向上设置有凸台,法兰抵靠在凸台上,该凸台与竹缠绕复合管外表面相接触的闭合面上设置有装胶槽,该装胶槽由位于凸台上的凸台凹槽与位于竹缠绕复合管外表面上的管凹槽相对形成;在凸台上还设置有与装胶槽连通的注胶口,用于向装胶槽内注入胶黏剂。但该结构在竹缠绕复合管切割后承口直径改变,从而导致在两侧管道端口直径不一致的情况下不适用。
5.因此,需要一种连接装置与防护处理材料,以便能够在管道切割后对直径不统一的两端管道进行连接,并在端口形成相关的防护层。
技术实现要素:6.为解决上述技术问题,本发明提供了一种竹缠绕复合管的连接装置及方法,可以解决竹缠绕复合管切割后连接不便,切割处防护处理难的问题。
7.本发明通过以下技术方案得以实现。
8.本发明提供的一种竹缠绕复合管的连接装置,包括连接管,密封环,所述连接管的一端设置有承口端a,连接管的另一端设置有插入端a,所述连接管通过模具组件制备而成,所述密封环置于连接管内形成连接。
9.优选地,所述连接管上设置有台阶a,台阶b,所述台阶a靠承口端a一侧设置,所述台阶b靠插入端a一侧设置,所述连接管内设置有滑槽。
10.优选地,所述密封环,包括基座环a,凸台环a,所述基座环a一端与凸台环a同轴连接,所述凸台环a的外径大于基座环a的外径,密封环置于滑槽内形成滑动连接。
11.优选地,所述模具组件,包括模具a,模具b,所述模具a上设置有台阶c,台阶d,所述台阶c与台阶d连接处呈斜面设置,模具a的一端设置有承口端b,模具a的另一端设置有插入端b,所述模具b呈环状,模具b置于台阶c上与模具a形成滑动连接。
12.优选地,所述模具b包括基座环b,凸台环b,所述基座环b的一端与凸台环b同轴连接。
13.一种竹缠绕复合管连接装置的制备方法,包括以下步骤:
14.s1:将模具b上基座环b与凸台环b的连接处打磨呈垂直状态,使用测量工具测量模具b的尺寸是否符合需求,然后将模具a贯穿模具b,使得模具b置于台阶c上,然后在模具a、模具b上缠绕一层薄膜,
15.s2:在完成步骤s1的薄膜缠绕后,依次缠绕竹纤维无纺布,针织毡,网格布,完成内衬层的制备,然后使用玻璃纤维从模具a的承口端b、台阶c至台阶d位置上进行缠绕,每缠绕一层玻璃纤维,就在该层玻璃纤维的表面刷一层不饱和树脂,待不饱和树脂固化后,将模具组件脱模即完成制备;
16.s3:使用内腔与密封环形状对应的模具进行浇筑制备,成型后脱模,对成型件进行整平,修边,即完成密封环的制备。
17.优选地,所述步骤s1中,模具b的基座环b端部距离台阶c远离承口端b一侧的端部50-300mm,模具b的凸台环b靠承口端b一侧设置。
18.优选地,所述步骤s2中,玻璃纤维缠绕厚度为3-10mm;所述步骤s2中,玻璃纤维缠绕范围延伸至台阶d上100-400mm即可;所述步骤s2中,不饱和树脂为191c型树脂。
19.一种竹缠绕复合管连接装置的连接方法,包括以下步骤:
20.s1:使用连接装置连通管道a和管道b,将密封环分别设置于连接管与管道b的滑槽内,使用防护剂对管道a和管道b的切割面进行涂抹,然后将管道a的一端从连接管的承口端a插入,将连接管的插入端a插入管道b内,待防护剂固化后,进行闭水试验,试验合格后即完成连接。
21.优选地,所述防护剂,以质量份计算,其组分包括胶衣树脂93-110份,环烷酸钴0.2-0.8份,过氧化钾乙酮0.6-1.5份;所述防护剂的制备方法,包括以下步骤:将环烷酸钴加入到胶衣树脂中,搅拌均匀后加入过氧化钾乙酮,再搅拌均匀即可。
22.本发明的有益效果在于:
23.本发明中,实施例1-3的连接装置力学性能均达到规定值,其中,作为重要指标之一的平均渗水量最大允许值为13.8
×
10-6
,实施例1-3的平均渗水量均远低于最大允许值。因此,使用实施例1-3的方法制备的,并进行连接的连接装置符合竹缠绕复合管在管段连接时的施工需求。通过防护剂的使用,极大的提高了施工过程中固化速度,减少施工时间的浪费,防护剂还具有调配方式简单,使用方便的特点。本发明的连接装置及连接方法,解决了竹缠绕管道在连接过程中的缺陷问题,给管道施工极大的增加了便利性,也为竹缠绕管道工程质量做出了更进一步的保障。
附图说明
24.图1是本发明的连接结构示意图;
25.图2是本发明模具组件的结构示意图;
26.图中:1-连接管,2-密封环,3-承口端a,4-插入端a,5-台阶a,6-台阶b,7-滑槽,8-基座环a,9-凸台环a,10-模具a,11-模具b,12-台阶c,13-台阶d,14-承口端b,15-插入端b,16-基座环b,17-凸台环b,18-管道a,19-管道b。
具体实施方式
27.下面进一步描述本发明的技术方案,但要求保护的范围并不局限于所述。
28.实施例1:
29.如图1、2所示,一种竹缠绕复合管的连接装置,包括连接管1,密封环2,所述连接管1的一端设置有承口端a3,连接管1的另一端设置有插入端a4,所述连接管1通过模具组件制备而成,所述密封环2置于连接管1内形成连接。密封环2对连接处起到密封作用,防止液体漏出。
30.所述连接管1上设置有台阶a5,台阶b6,所述台阶a5靠承口端a3一侧设置,所述台阶b6靠插入端a4一侧设置,所述连接管1内设置有滑槽7。
31.所述密封环2,包括基座环a8,凸台环a9,密封环2材质为三元乙丙橡胶,所述基座环a8一端与凸台环a9同轴连接,所述凸台环a9的外径大于基座环a8的外径,密封环2置于滑槽7内形成滑动连接。
32.所述模具组件,包括模具a10,模具b11,所述模具a10上设置有台阶c12,台阶d13,所述台阶c12与台阶d13连接处呈斜面设置,模具a10的一端设置有承口端b14,模具a10的另一端设置有插入端b15,所述模具b11呈环状,模具b11置于台阶c12上与模具a10形成滑动连接。
33.所述模具b11材质为三元乙丙橡胶,模具b11包括基座环b16,凸台环b17,所述基座环b16的一端与凸台环b17同轴连接,基座环b16的宽度为25mm,所述凸台环b17的外径大于基座环b16的外径6mm,凸台环b17的宽度为4mm。
34.一种竹缠绕复合管连接装置的制备方法,包括以下步骤:
35.s1:将模具b11上基座环b16与凸台环b17的连接处打磨呈垂直状态,使用测量工具测量模具b11的尺寸是否符合需求,然后将模具a10贯穿模具b11,使得模具b11置于台阶c12上,然后在模具a10、模具b11上缠绕一层薄膜,
36.s2:在完成步骤s1的薄膜缠绕后,依次缠绕竹纤维无纺布,针织毡,网格布,完成内衬层的制备,然后使用玻璃纤维从模具a10的承口端b14、台阶c12至台阶d13位置上进行缠绕,每缠绕一层玻璃纤维,就在该层玻璃纤维的表面刷一层不饱和树脂,待不饱和树脂固化后,将模具组件脱模即完成制备;
37.s3:使用内腔与密封环2形状对应的模具进行浇筑制备,成型后脱模,对成型件进行整平,修边,即完成密封环2的制备。
38.所述步骤s1中,模具b11的基座环b16端部距离台阶c12远离承口端b14一侧的端部50mm,模具b11的凸台环b17靠承口端b14一侧设置。
39.所述步骤s2中,玻璃纤维缠绕厚度为3mm;所述步骤s2中,玻璃纤维缠绕范围延伸至台阶d13上100mm即可;所述步骤s2中,不饱和树脂为191c型树脂。
40.一种竹缠绕复合管连接装置的连接方法,包括以下步骤:
41.s1:使用连接装置连通管道a18和管道b19,管道a18和管道b19均为竹缠绕复合管,
将密封环2分别设置于连接管1与管道b19的滑槽7内(若管道b19无滑槽7,则将密封环2卡至管道b19上对应台阶a5,台阶b6设置的两处台阶连接处的内壁),使用防护剂对管道a18和管道b19的切割面(管道可根据实际情况决定是否需要切割)进行涂抹,然后将管道a18的一端从连接管1的承口端a3插入,将连接管1的插入端a4插入管道b19内,待防护剂固化(固化时间15-20min,具体视温度情况而定)后,进行闭水试验,试验合格后即完成连接。
42.所述防护剂,以质量份计算,其组分包括胶衣树脂93份,环烷酸钴0.2份,过氧化钾乙酮0.6份;所述防护剂的制备方法,包括以下步骤:将环烷酸钴加入到胶衣树脂中,搅拌均匀后加入过氧化钾乙酮,再搅拌均匀即可;所述胶衣树脂的黏度在750mpa.s,该黏度下便于防护剂附着在竹缠绕复合管上。
43.防护剂能够对竹缠绕复合管的切割面起到保护作用,具有耐腐蚀、防水、耐候性强的特点,从而提高竹缠绕复合管切割面的使用耐久性及管材强度。防护剂能够在施工现场根据需求量制备。
44.实施例2:
45.如图1、2所示,一种竹缠绕复合管的连接装置,包括连接管1,密封环2,所述连接管1的一端设置有承口端a3,连接管1的另一端设置有插入端a4,所述连接管1通过模具组件制备而成,所述密封环2置于连接管1内形成连接。密封环2对连接处起到密封作用,防止液体漏出。
46.所述连接管1上设置有台阶a5,台阶b6,所述台阶a5靠承口端a3一侧设置,所述台阶b6靠插入端a4一侧设置,所述连接管1内设置有滑槽7。
47.所述密封环2,包括基座环a8,凸台环a9,密封环2材质为三元乙丙橡胶,所述基座环a8一端与凸台环a9同轴连接,所述凸台环a9的外径大于基座环a8的外径,密封环2置于滑槽7内形成滑动连接。
48.所述模具组件,包括模具a10,模具b11,所述模具a10上设置有台阶c12,台阶d13,所述台阶c12与台阶d13连接处呈斜面设置,模具a10的一端设置有承口端b14,模具a10的另一端设置有插入端b15,所述模具b11呈环状,模具b11置于台阶c12上与模具a10形成滑动连接。
49.所述模具b11材质为三元乙丙橡胶,模具b11包括基座环b16,凸台环b17,所述基座环b16的一端与凸台环b17同轴连接,基座环b16的宽度为50mm,所述凸台环b17的外径大于基座环b16的外径15mm,凸台环b17的宽度为15mm。
50.一种竹缠绕复合管连接装置的制备方法,包括以下步骤:
51.s1:将模具b11上基座环b16与凸台环b17的连接处打磨呈垂直状态,使用测量工具测量模具b11的尺寸是否符合需求,然后将模具a10贯穿模具b11,使得模具b11置于台阶c12上,然后在模具a10、模具b11上缠绕一层薄膜,
52.s2:在完成步骤s1的薄膜缠绕后,依次缠绕竹纤维无纺布,针织毡,网格布,完成内衬层的制备,然后使用玻璃纤维从模具a10的承口端b14、台阶c12至台阶d13位置上进行缠绕,每缠绕一层玻璃纤维,就在该层玻璃纤维的表面刷一层不饱和树脂,待不饱和树脂固化后,将模具组件脱模即完成制备;
53.s3:使用内腔与密封环2形状对应的模具进行浇筑制备,成型后脱模,对成型件进行整平,修边,即完成密封环2的制备。
54.所述步骤s1中,模具b11的基座环b16端部距离台阶c12远离承口端b14一侧的端部300mm,模具b11的凸台环b17靠承口端b14一侧设置。
55.所述步骤s2中,玻璃纤维缠绕厚度为10mm;所述步骤s2中,玻璃纤维缠绕范围延伸至台阶d13上400mm即可;所述步骤s2中,不饱和树脂为191c型树脂。
56.一种竹缠绕复合管连接装置的连接方法,包括以下步骤:
57.s1:使用连接装置连通管道a18和管道b19,管道a18和管道b19均为竹缠绕复合管,将密封环2分别设置于连接管1与管道b19的滑槽7内(若管道b19无滑槽7,则将密封环2卡至管道b19上对应台阶a5,台阶b6设置的两处台阶连接处的内壁上),使用防护剂对管道a18和管道b19的切割面(管道可根据实际情况决定是否需要切割)进行涂抹,然后将管道a18的一端从连接管1的承口端a3插入,将连接管1的插入端a4插入管道b19内,待防护剂固化(固化时间15-20min,具体视温度情况而定)后,进行闭水试验,试验合格后即完成连接。
58.所述防护剂,以质量份计算,其组分包括胶衣树脂110份,环烷酸钴0.8份,过氧化钾乙酮1.5份;所述防护剂的制备方法,包括以下步骤:将环烷酸钴加入到胶衣树脂中,搅拌均匀后加入过氧化钾乙酮,再搅拌均匀即可;所述胶衣树脂的黏度在900mpa.s,该黏度下便于防护剂附着在竹缠绕复合管上。
59.防护剂能够对竹缠绕复合管的切割面起到保护作用,具有耐腐蚀、防水、耐候性强的特点,从而提高竹缠绕复合管切割面的使用耐久性及管材强度。防护剂能够在施工现场根据需求量制备。
60.实施例3:
61.如图1、2所示,一种竹缠绕复合管的连接装置,包括连接管1,密封环2,所述连接管1的一端设置有承口端a3,连接管1的另一端设置有插入端a4,所述连接管1通过模具组件制备而成,所述密封环2置于连接管1内形成连接。密封环2对连接处起到密封作用,防止液体漏出。
62.所述连接管1上设置有台阶a5,台阶b6,所述台阶a5靠承口端a3一侧设置,所述台阶b6靠插入端a4一侧设置,所述连接管1内设置有滑槽7。
63.所述密封环2,包括基座环a8,凸台环a9,密封环2材质为三元乙丙橡胶,所述基座环a8一端与凸台环a9同轴连接,所述凸台环a9的外径大于基座环a8的外径,密封环2置于滑槽7内形成滑动连接。
64.所述模具组件,包括模具a10,模具b11,所述模具a10上设置有台阶c12,台阶d13,所述台阶c12与台阶d13连接处呈斜面设置,模具a10的一端设置有承口端b14,模具a10的另一端设置有插入端b15,所述模具b11呈环状,模具b11置于台阶c12上与模具a10形成滑动连接。
65.所述模具b11材质为三元乙丙橡胶,模具b11包括基座环b16,凸台环b17,所述基座环b16的一端与凸台环b17同轴连接,基座环b16的宽度为35mm,所述凸台环b17的外径大于基座环b16的外径10mm,凸台环b17的宽度为8mm。
66.一种竹缠绕复合管连接装置的制备方法,包括以下步骤:
67.s1:将模具b11上基座环b16与凸台环b17的连接处打磨呈垂直状态,使用测量工具测量模具b11的尺寸是否符合需求,然后将模具a10贯穿模具b11,使得模具b11置于台阶c12上,然后在模具a10、模具b11上缠绕一层薄膜,
68.s2:在完成步骤s1的薄膜缠绕后,依次缠绕竹纤维无纺布,针织毡,网格布,完成内衬层的制备,然后使用玻璃纤维从模具a10的承口端b14、台阶c12至台阶d13位置上进行缠绕,每缠绕一层玻璃纤维,就在该层玻璃纤维的表面刷一层不饱和树脂,待不饱和树脂固化后,将模具组件脱模即完成制备;
69.s3:使用内腔与密封环2形状对应的模具进行浇筑制备,成型后脱模,对成型件进行整平,修边,即完成密封环2的制备。
70.所述步骤s1中,模具b11的基座环b16端部距离台阶c12远离承口端b14一侧的端部150mm,模具b11的凸台环b17靠承口端b14一侧设置。
71.所述步骤s2中,玻璃纤维缠绕厚度为5mm;所述步骤s2中,玻璃纤维缠绕范围延伸至台阶d13上200mm即可;所述步骤s2中,不饱和树脂为191c型树脂。
72.一种竹缠绕复合管连接装置的连接方法,包括以下步骤:
73.s1:使用连接装置连通管道a18和管道b19,管道a18和管道b19均为竹缠绕复合管,将密封环2分别设置于连接管1与管道b19的滑槽7内(若管道b19无滑槽7,则将密封环2卡至管道b19上对应台阶a5,台阶b6设置的两处台阶连接处的内壁上),使用防护剂对管道a18和管道b19的切割面(管道可根据实际情况决定是否需要切割)进行涂抹,然后将管道a18的一端从连接管1的承口端a3插入,将连接管1的插入端a4插入管道b19内,待防护剂固化(固化时间15-20min,具体视温度情况而定)后,进行闭水试验,试验合格后即完成连接。
74.所述防护剂,以质量份计算,其组分包括胶衣树脂100份,环烷酸钴0.5份,过氧化钾乙酮1份;所述防护剂的制备方法,包括以下步骤:将环烷酸钴加入到胶衣树脂中,搅拌均匀后加入过氧化钾乙酮,再搅拌均匀即可;所述胶衣树脂的黏度在800mpa.s,该黏度下便于防护剂附着在竹缠绕复合管上。
75.防护剂能够对竹缠绕复合管的切割面起到保护作用,具有耐腐蚀、防水、耐候性强的特点,从而提高竹缠绕复合管切割面的使用耐久性及管材强度。防护剂能够在施工现场根据需求量制备。
76.所述闭水试验,根据给水排水管道工程施工及验收规范(gb50268-2008)进行闭水试验法,闭水试验法按设计要求和试验方案进行。试验管段按井距分隔,抽样选取,带井试验。其中,需要竹缠绕复合管及连接处、检查井外观质量已验收合格,全部预留孔应封堵,试验前未出现渗水的情况。
77.试验方法为:1、试验管段上游设计水头不超过试验管段管顶内壁时,试验水头应以试验试验管段上游管段顶内壁高度加2m计;试验段上游设计水头超过管顶内壁时,试验水头应以试验管段上游设计水头加2m计;计算出的试验水头小于10m,但已超过上游检查井井口时、试验水头应以上游检查井井口高度为准;
78.2、试验管段灌满水后浸泡时间不应少于24h;试验水头达规定水头高度时开始计时,观测管道的渗水量,直至观测结束时,应不断地向试验管段内补水,保持试验水头恒定。渗水量的观测时间不得小于30min;
79.3、记录数据计算渗水量,化学建材管道的实测渗水量应小于或等于按下式计算的允许渗水量;
80.q=0.0046di
81.式中,q—允许渗水量(m3/24h
·
km);di—管道内径(mm)。
82.使用实施例1-3的方法制备的连接装置对dn300管道进行连接,且经过闭水试验等测试后,所得结果如表1所示。
83.表1连接装置性能表
[0084][0085][0086]
由表1可知,实施例1-3的连接装置力学性能均达到规定值,其中,作为重要指标之一的平均渗水量最大允许值为13.8
×
10-6
,实施例1-3的平均渗水量均远低于最大允许值。因此,使用实施例1-3的方法制备的,并进行连接的连接装置符合竹缠绕复合管在管段连接时的施工需求。