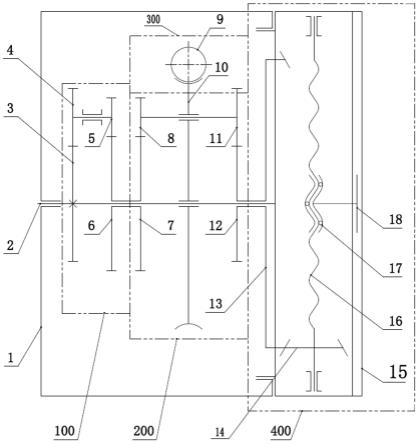
基于中心布置的ww型行星差动的u轴机构
技术领域
1.本实用新型涉及一种实现机床u轴功能的装置,尤其是一种基于中心布置的ww型行星差动的u轴机构。
背景技术:2.重型、细长轴或异形工件上的回转部分,通常采用工件固定、刀具回转的方式来加工。例如:镗铣床配数控平旋盘来加工重型工件的圆柱面、环面、球面、圆锥面、锥螺纹等,平旋盘式数控管螺纹车床套车加工管道两端的锥管螺纹,坐标磨床通过行星磨削的方式磨削精密锥孔、台阶孔,数控坡口机进行管道切断、坡口加工,专用机床镗车端面、内孔等。该加工方式的特点是,在旋转的主轴(及旋转盘)上设置有进行径向运动的进给轴,根据国标gb/t19660,此轴通常定义为u轴。
3.u轴机构的核心在于通过内部的传动机构实现旋转运动和径向运动。现有技术中,u轴机构的传动方式主要有三种:斜面齿纹式、齿轮齿条式和行星差动式。其中,斜面齿纹和齿轮齿条式只能在主轴可伸缩的通用机床,或者是带有推杆机构的专用机床上使用,应用受限。同时,斜面齿纹式一般用于中小规格u轴机构设计;齿轮齿条式本身传动精度低,逐渐被淘汰。因此,现在主流的方案是行星差动机构方案。
4.然而,目前的行星差动机构方案都是基于差动机构偏置的结构。例如申请人于2021年申请的实用新型专利《基于2k-h(c)型行星传动的u轴机构》(公开号为cn216078192u),其行星差动机构位于主轴的一侧,额外占用了部分空间,存在整个装置径向尺寸大、难以小型化的问题。对于一些有空间尺寸要求的工况,这种结构受到很大的限制。而且,为了尽可能地缩减径向尺寸,设计时只能通过减小模数和齿数的方式来控制差动机构齿轮的大小,这必然影响到传动性能。
技术实现要素:5.本实用新型提出了一种基于中心布置的ww型行星差动的u轴机构,其目的是:减小整个装置的径向空间占用,改善行星差动机构的传动性能。
6.本实用新型技术方案如下:
7.一种基于中心布置的ww型行星差动的u轴机构,包括用于与机床固定连接的本体,本体上安装有可转动的回转主轴,回转主轴的后端用于与机床的主轴相连接,回转主轴的前端连接有旋转盘,所述旋转盘上设有径向传动组件,所述径向传动组件用于带动刀具进行径向移动,所述本体上还安装有行星差动机构和径向驱动组件;
8.所述行星差动机构包括后轮系和前轮系;
9.所述后轮系包括第一输入轮、第一轮架、第一中间轮、第二中间轮和第一输出轮;所述第一输入轮和第一输出轮都与回转主轴同轴,第一输入轮与回转主轴固定连接或为一体,第一输出轮则套装在回转主轴上以实现相对于回转主轴的转动;第一中间轮和第二中间轮相互连接或为一体、且通过转动连接方式安装在第一轮架上,第一中间轮和第二中间
轮的轴线与所述回转主轴平行;第一中间轮与第一输入轮相啮合,第二中间轮与第一输出轮相啮合;
10.所述前轮系包括第二输入轮、第二轮架、第三中间轮、第四中间轮和第二输出轮;所述第二输入轮和第二输出轮都与回转主轴同轴,且都套装在回转主轴上以实现相对于回转主轴的转动;第三中间轮和第四中间轮相互连接或为一体、且通过转动连接方式安装在第二轮架上,第三中间轮和第四中间轮的轴线与所述回转主轴平行;第三中间轮与第二输入轮相啮合,第四中间轮与第二输出轮相啮合;
11.所述第一输出轮和第二输入轮固定连接,或者为一体;
12.所述第一轮架固定在本体上,所述径向驱动组件与所述第二轮架相连接、用于驱动第二轮架绕回转主轴转动;或者,所述径向驱动组件与所述第一轮架相连接、用于驱动第一轮架绕回转主轴转动,而所述第二轮架固定在本体上;
13.所述第二输出轮与径向传动组件传动连接。
14.作为所述的基于中心布置的ww型行星差动的u轴机构的进一步改进:所述第一输出轮和第二输入轮为同一个齿轮,该齿轮分别与第二中间轮和第三中间轮进行啮合。
15.作为所述的基于中心布置的ww型行星差动的u轴机构的进一步改进:所述径向驱动组件包括相互啮合的第一蜗杆和第一蜗轮,第一蜗杆通过转动方式安装在本体上;
16.如果第一轮架固定在本体上,则所述第一蜗轮与第二轮架相连接或为一体;如果第二轮架固定在本体上,则所述第一蜗轮与第一轮架相连接或为一体。
17.作为所述的基于中心布置的ww型行星差动的u轴机构的进一步改进:所述径向传动组件包括通安装在旋转盘上、且与回转主轴相垂直的可转动的丝杠;径向传动组件还包括安装在所述丝杠上的螺母,以及通过滑动连接方式安装在旋转盘上的滑座,所述螺母与滑座固定连接;
18.所述径向传动组件还包括中间传动组件,所述第二输出轮通过中间传动组件驱动丝杠相对于旋转盘转动。
19.作为所述的基于中心布置的ww型行星差动的u轴机构的进一步改进:所述丝杠上设有两段外螺纹,所述两段外螺纹的旋向一为左旋、一为右旋,所述螺母和滑座为一一对应的两组,两个螺母分别与两段外螺纹相配合。
20.作为所述的基于中心布置的ww型行星差动的u轴机构的进一步改进:所述中间传动组件包括相互啮合的第一齿轮和第二齿轮,第一齿轮与第二输出轮固定同轴连接或为一体,第二齿轮与所述丝杠固定连接或为一体;
21.第一齿轮和第二齿轮中一个为圆柱齿轮、一个为面齿轮,或者所述第一齿轮和第二齿轮均为锥齿轮。
22.作为所述的基于中心布置的ww型行星差动的u轴机构的进一步改进:所述中间传动组件包括第二齿轮、第三齿轮、第四齿轮和第五齿轮;
23.第三齿轮与第二输出轮固定同轴连接或为一体;第四齿轮和第五齿轮相互连接或为一体、且通过转动连接方式安装在旋转盘上,第四齿轮和第五齿轮的轴线平行于回转主轴;第二齿轮与所述丝杠固定连接或为一体;
24.所述第三齿轮与第四齿轮相啮合;所述第五齿轮和第二齿轮相啮合;
25.第五齿轮和第二齿轮中一个为圆柱齿轮、一个为面齿轮,或者所述第五齿轮和第
二齿轮均为锥齿轮。
26.作为所述的基于中心布置的ww型行星差动的u轴机构的进一步改进:所述中间传动组件包括第三齿轮、第四齿轮、第二蜗杆和第二蜗轮;
27.第三齿轮与第二输出轮固定同轴连接或为一体;第四齿轮和第一蜗杆相互连接或为一体的、且通过转动连接方式安装在旋转盘上,第四齿轮和第二蜗杆的轴线平行于回转主轴;第二蜗轮与所述丝杠固定连接或为一体;
28.所述第三齿轮与第四齿轮相啮合;所述第二蜗杆和第二蜗轮相啮合。
29.相对于现有技术,本实用新型具有以下有益效果:(1)本装置中两大轮系的轴线都与回转主轴的轴线重合,轮系围绕回转主轴布置,不再偏置,这种结构既减小了侧方空间的占用,也可以充分利用本体内部的空间,增大传动机构齿轮的尺寸,从而改善传动性能;(2)径向驱动组件既可以驱动第一轮架,也可以选择驱动第二轮架,空间布置更加灵活;(3)轮系中的齿轮都是相互平行的,可以选择制造技术非常成熟、加工效率高、精度更易保证的圆柱齿轮;(4)本方案适用于大中小型u轴、尤其是小型u轴机构的设计,例如通用机床的一体化平旋盘、独立分体结构的中大型平旋盘、专用机床、坡口机、平旋盘式管螺纹车床、组合机床等中大型机床或机床附件的u轴机构设计,也可用于坐标磨床、加工中心的小规格数控平旋盘、中小直径变径深孔加工用u轴刀具等。
附图说明
30.图1为实施例一的结构示意图;
31.图2为实施例二的结构示意图;
32.图3为实施例三的结构示意图;
33.图4为实施例四中径向传动机构部分的结构示意图;
34.图5为实施例五中径向传动机构部分的结构示意图;
35.图6为实施例六中径向传动机构部分的结构示意图。
具体实施方式
36.下面结合附图详细说明本实用新型的技术方案:
37.实施例一
38.如图1,一种基于中心布置的ww型行星差动的u轴机构,包括用于与机床固定连接的本体1,本体1上安装有可转动的回转主轴2,回转主轴2的后端用于与机床的主轴相连接,回转主轴2的前端连接有旋转盘15。所述回转主轴2、旋转盘15跟随机床的主轴同步转动。
39.所述本体1上还安装有行星差动机构和径向驱动组件300。所述旋转盘15上设有径向传动组件400,所述径向传动组件400用于带动刀具进行径向移动。
40.具体的,所述行星差动机构包括后轮系100和前轮系200。
41.所述后轮系100包括第一输入轮3、第一轮架、第一中间轮4、第二中间轮5和第一输出轮6;所述第一输入轮3和第一输出轮6都与回转主轴2同轴,第一输入轮3与回转主轴2固定连接或为一体,第一输出轮6则空套在回转主轴2上以实现相对于回转主轴2的转动;第一中间轮4和第二中间轮5相互连接或为一体、且通过转动连接方式安装在第一轮架上,第一中间轮4和第二中间轮5的轴线与所述回转主轴2平行;第一中间轮4与第一输入轮3相啮合,
第二中间轮5与第一输出轮6相啮合。
42.所述前轮系200包括第二输入轮7、第二轮架、第三中间轮8、第四中间轮11和第二输出轮12;所述第二输入轮7和第二输出轮12都与回转主轴2同轴,且都空套在回转主轴2上以实现相对于回转主轴2的转动;第三中间轮8和第四中间轮11相互连接或为一体、且通过转动连接方式安装在第二轮架上,第三中间轮8和第四中间轮11的轴线与所述回转主轴2平行;第三中间轮8与第二输入轮7相啮合,第四中间轮11与第二输出轮12相啮合。
43.一般的,上述输入轮、输出轮和中间轮都是圆柱齿轮,其制造技术非常成熟,容易实现高精度制造,生产效率高。目前蜗杆砂轮磨削直齿/斜齿圆柱齿轮最高已经可以实现3级精度(已可以作为测量齿轮),制造成本低,容易获得。
44.所述第一输出轮6和第二输入轮7固定连接,或者为一体。
45.本实施例中,所述第一轮架固定在本体1上,所述径向驱动组件300与所述第二轮架相连接、用于驱动第二轮架绕回转主轴2转动。具体的,所述径向驱动组件300包括相互啮合的第一蜗杆9和第一蜗轮10,第一蜗杆9通过转动方式安装在本体1上,第一蜗轮10与第二轮架相连接或为一体。
46.所述第二输出轮12与径向传动组件400传动连接。
47.具体的,所述径向传动组件400包括通安装在旋转盘15上、且与回转主轴2相垂直的可转动的丝杠16;径向传动组件400还包括安装在所述丝杠16上的螺母17,以及通过滑动连接方式安装在旋转盘15上的滑座18,所述螺母17与滑座18固定连接。滑座18用于安装刀具。
48.所述径向传动组件400还包括中间传动组件,所述第二输出轮12通过中间传动组件驱动丝杠16相对于旋转盘15转动。
49.本实施例中,所述中间传动组件包括相互啮合的第一齿轮13和第二齿轮14,第一齿轮13与第二输出轮12固定同轴连接或为一体,第二齿轮14与所述丝杠16固定连接或为一体。
50.第一齿轮13和第二齿轮14中一个为圆柱齿轮、一个为面齿轮,或者所述第一齿轮13和第二齿轮14均为锥齿轮。在成本合适的情况下,前一种方案更有竞争力。
51.下面对传动部分进行分析:
52.第一部分:
53.后轮系100是一个定轴轮系(正号),其功能是使第一输入轮3和第一输出轮6的传动比为正,且不为1,但最好接近于1。
54.不为1,是为了避免第二部分的ww型行星差动机构产生1:1的传动比。如果第一部分的传动比是1:1,则为了总传动比为1,第二部分必须也是1:1的传动比,此时第二部分的差动会失效(后文会阐述原因)。
55.传动比接近1,是为了提高行星差动机构的传动效率(ww型差动机构传动比越大,效率越低)。
56.因此,第一输入轮3和第一输出轮6之间的传动比为:
57.第二部分:
58.前轮系200和径向驱动组件300构成一个ww型行星差动机构。第二输入轮7和第二
输出轮12为中心轮,第二轮架为行星架,第三中间轮8和第四中间轮11为行星轮。
59.下面采用行星架固定法来说明并计算ww型行星差动机构的两种传动情况:
60.第1种:当第一蜗轮10静止时,第二输入轮7和第二输出轮12之间的传动比为
61.第2种:当第二输入轮7静止即机床主轴静止时,第一蜗轮10(行星架)和第二输出轮12(输出中心轮)之间的传动比为注:根据公式可知z8×z12
≠z7×z11
或或否则计算公式的分母会为0,差动机构失效(无论作为行星架的第一蜗轮10如何旋转,第二输出轮12都不会旋转,无法实现差动)。
62.另外,设计时需要进行配齿,要求当第一蜗轮10静止时,i
3-12
=1(即第一部分和第二部分的传动比互为倒数),以保证第一输入轮3和第二输出轮12能够同步旋转,即:
[0063][0064]
注:上述公式即ww型行星差动机构传动比和各构件转速计算可以参考以下文献:《行星传动机构设计》第二版(作者:饶振纲)第二章中2-2节“用转臂固定法计算行星传动机构的传动比”以及“d型差动机构的传动比计算”等内容。上述设计方式属于现有技术,一般的行星传动教材或手册都记载有计算过程,在此不做赘述。
[0065]
第三部分:
[0066]
旋转盘15和径向传动组件400构成末级行星传动机构。其中,第一齿轮13是行星传动机构的中心轮,丝杠16所连接的第二齿轮14是行星轮,旋转盘15是行星架。
[0067]
显然,当旋转盘15和第一齿轮13同步旋转时,第二齿轮14和丝杠16不产生自转,仅有公转,滑座18及滑座18上的刀具不会相对于旋转盘15出现径向移动。当旋转盘15和第一齿轮13的转速不相等时,第二齿轮14将相对于旋转盘15发生自转,从而驱动滑座18及刀具发生径向移动。
[0068]
本装置共有以下3种工况:
[0069]
工况1:
[0070]
机床主轴带动回转主轴2旋转,第一蜗杆9、第一蜗轮10固定,整个齿轮传动机构为定轴轮系。
[0071]
参照第一部分、第二部分的齿轮参数,此时第一输入轮3和第二输出轮12之间的传动比为i
3-12
=1,即机床主轴、回转主轴2、第一输入轮3、旋转盘15、第二输出轮12和第一齿轮13,共6个元件同步旋转,有ω
13
=ω
15
。
[0072]
此时,在第三部分的末级行星齿轮传动机构中,采用解析法计算第二齿轮14(行星
轮)相对于旋转盘15的自转速度为:轮)相对于旋转盘15的自转速度为:即滑座18和刀具相对于旋转盘15静止。此时,u轴机构相当于定径刀具,可以加工圆柱面、圆柱螺纹等特征。
[0073]
工况2:
[0074]
当机床主轴制动,回转主轴2和旋转盘15都静止,同时第一蜗杆9带动第一蜗轮10旋转时,有ω
15
=0。再根据ww型行星差动机构的运动原理,第一蜗轮10(行星架)与第二输出轮12(中心轮)之间的传动比为故有故有此工况下采用解析法计算第二齿轮14(行星轮)相对于旋转盘15的自转速度为:
[0075][0076]
此时丝杠16齿轮和丝杠16产生自转,根据上述公式可以认为自转来自第一蜗轮10的运动,继而使滑座18和刀具产生径向进给运动,且进给速度仅与第一蜗轮10的转速有关。此工况下可以实现加工前径向对刀,即刀具不做旋转、只做径向运动。
[0077]
工况3:
[0078]
当回转主轴2和第一蜗轮10同时旋转时,此工况相当于工况1和工况2的运动叠加,第二输出轮12由回转主轴2和第一蜗轮10共同驱动,根据复合轮系运动原理,此工况下的第一齿轮13的转速为工况1和工况2下转速的叠加:
[0079][0080]
采用解析法计算第二齿轮14相对于旋转盘15的自转速度为:
[0081]
由公式可知,当齿轮参数确定时,丝杠16和第二齿轮14的转速依然仅取决于第一蜗轮10的转速(与工况2相同)。
[0082]
此工况下,滑座18和刀具既跟随旋转盘15进行旋转,也会相对于旋转盘15进行径向进给运动,u轴机构可以对连续变径回转轮廓进行加工,例如:台阶面、锥面、锥螺纹、环面、球面等。
[0083]
实施例二
[0084]
本实施例是实施例一的一种特例:如图2,当后轮系100和前轮系200设计成互为镜像的结构时,所述第一输出轮6和第二输入轮7的齿数和模数是完全相同的,此时二者可合并为同一个较宽的齿轮,该齿轮分别与第二中间轮5和第三中间轮8进行啮合。
[0085]
同理,本文中所有的双联圆柱齿轮都可以在参数相同的情况下设计成一个齿轮。
[0086]
实施例三
[0087]
本实施例与实施例一的不同之处在于:如图3,所述径向驱动组件300改为与所述第一轮架相连接、用于驱动第一轮架绕回转主轴2转动,即所述第一蜗轮10与第一轮架相连接或为一体,而所述第二轮架固定在本体1上。
[0088]
本实施例中,前轮系200和径向驱动组件300构成ww型行星差动机构,而后轮系100为定轴轮系。
[0089]
可见,改变后的运动原理未发生实质性变化,并不影响上述三种工况的实现。
[0090]
实施例四
[0091]
本实施例是在实施例一至三的基础之上,对径向传动组件400部分的中间传动组件的结构做出改变。
[0092]
如图4,所述中间传动组件包括第二齿轮14、第三齿轮19、第四齿轮20和第五齿轮21。
[0093]
第三齿轮19与第二输出轮12固定同轴连接或为一体;第四齿轮20和第五齿轮21相互连接或为一体、且通过转动连接方式安装在旋转盘15上,第四齿轮20和第五齿轮21的轴线平行于回转主轴2;第二齿轮14与所述丝杠16固定连接或为一体。
[0094]
所述第三齿轮19与第四齿轮20相啮合;所述第五齿轮21和第二齿轮14相啮合。
[0095]
进一步的,第五齿轮21和第二齿轮14中一个为圆柱齿轮、一个为面齿轮,或者所述第五齿轮21和第二齿轮14均为锥齿轮。
[0096]
这种变化对传动性能有所影响,但未改变丝杠16与第二输出轮12之间的传动关系,运动原理并未发生变化,显然并不影响上述三种工况的实现。
[0097]
实施例五
[0098]
本实施例是在实施例一至三的基础之上,对径向传动组件400部分的中间传动组件的结构做出的另一种改变。
[0099]
如图5,所述中间传动组件包括第三齿轮19、第四齿轮20、第二蜗杆22和第二蜗轮23。
[0100]
第三齿轮19与第二输出轮12固定同轴连接或为一体;第四齿轮20和第一蜗杆9相互连接或为一体的、且通过转动连接方式安装在旋转盘15上,第四齿轮20和第二蜗杆22的轴线平行于回转主轴2;第二蜗轮23与所述丝杠16固定连接或为一体。
[0101]
所述第三齿轮19与第四齿轮20相啮合;所述第二蜗杆22和第二蜗轮23相啮合。
[0102]
实施例六
[0103]
本实施例是在实施例一至五的基础之上,对径向传动组件400部分做出改变。
[0104]
如图6,本实施例中,所述丝杠16上设有两段外螺纹,所述两段外螺纹的旋向一为左旋、一为右旋,所述螺母17和滑座18为一一对应的两组,两个螺母17分别与两段外螺纹相配合。
[0105]
在丝杠16自转时,会驱动两组刀具同步相对运动。