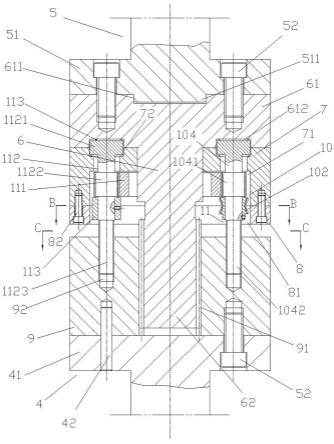
1.本实用新型涉及一种机械传动装置,尤其是一种提高圆锥齿轮传动精度的装置,属于齿轮传动技术领域。
背景技术:2.圆锥齿轮传动是一种用于改变传动方向的机械传动部件,广泛应用于各类机械设备和精密仪器。必须保证圆锥齿轮传动时的平稳性和可靠性,才能满足其传动精度较高的要求。为了达到上述要求,一方面需要保证圆锥齿轮的制造精度,另一方面还需保证其装配精度。齿隙作为一对圆锥齿轮啮合精度的重要装配指标受到广泛的重视,在圆锥齿轮传动中,齿隙过大会导致产生噪声或传动不平稳且导致齿轮磨损加速。目前,齿隙的调整是通过使用不同厚度的垫片来进行的,在一对圆锥齿轮的装配过程中,为了达到所需的齿隙,往往需要从齿轮轴上拆下圆锥齿轮,换上合适的调整垫片后再重新装配圆锥齿轮,费时费力,同时较大尺寸的圆锥齿轮装拆卸时还存在着碰伤人体和损坏零部件的安全隐患。
技术实现要素:3.本实用新型的目的是提供一种结构紧凑、安装简单、调整方便的圆锥齿轮齿隙调整装置。
4.本实用新型通过以下技术方案予以实现:
5.一种圆锥齿轮齿隙调整装置,包括圆柱齿轮、主动圆锥齿轮、从动圆锥齿轮、主动圆锥齿轮轴、从动圆锥齿轮轴、传动轴、中间轴、中间环体、中间盖板、滑块、齿隙调整驱动机构和从动圆锥齿轮轴位移机构,所述圆柱齿轮固定在主动圆锥齿轮一端上,主动圆锥齿轮通过滑动轴承水平支撑在主动圆锥齿轮轴一端上,主动圆锥齿轮轴另一端支撑在传动箱体一侧壁上,从动圆锥齿轮垂直固定在从动圆锥齿轮轴下端上,主动圆锥齿轮和从动圆锥齿轮通过各自对应的锁紧螺母分别锁紧,主动圆锥齿轮与从动圆锥齿轮啮合;传动轴上端伸进传动箱体上侧的输出传动箱内,传动轴下端法兰定位在中间轴上端法兰上,且与中间轴上端法兰固定连接;中间轴下端依次穿过固定连接的中间环体和中间盖板后伸进滑块中心内,从动圆锥齿轮轴上端法兰定位在与滑块下侧上,且与滑块固定连接;齿隙调整驱动机构设置在中间环体和中间盖板之间,从动圆锥齿轮轴位移机构设置在中间环体、中间盖板和滑块之间。
6.本实用新型的目的还可以通过以下技术措施来进一步实现。
7.进一步的,所述齿隙调整驱动机构包括驱动蜗杆、蜗轮、斜支撑杆和驱动齿轮轴,所述中间环体一端设有沉孔,中间盖板为环形结构,中间盖板设有与中间环体的沉孔匹配的通孔;所述驱动蜗杆一端支撑在中间环体与中间盖板相邻的环形面之间,驱动蜗杆另一端支撑在斜支撑杆一端上,斜支撑杆另一端焊接固定在中间环体的沉孔环面上,且与中间盖板相邻;蜗轮固定在驱动齿轮轴中部上,驱动蜗杆中部与蜗轮啮合;驱动齿轮轴和从动圆锥齿轮轴位移机构均布在中间盖板与滑块上;传动轴下端法兰定位且固定在中间轴上端法
兰上。
8.进一步的,所述从动圆锥齿轮轴位移机构包括同步齿圈、数根齿轮轴和数个齿轮轴挡圈,齿轮轴与驱动齿轮轴结构相同,齿轮轴与驱动齿轮轴径向均布在中间轴上端法兰、中间盖板与滑块上;齿轮轴上端和驱动齿轮轴上端分别径向延伸出支撑端,所述支撑端两侧分别支撑在中间轴上端法兰沉孔与相邻的中间环体沉孔之间;齿轮轴下端和驱动齿轮轴下端分别穿过中间环体后拧入滑块一侧各自对应的螺纹孔中;所述同步齿圈套入中间环体的沉孔中,通过固定在齿轮轴中部齿轮下端的挡圈轴向限位;齿轮轴中部齿轮和驱动齿轮轴中部齿轮分别与同步齿圈啮合。
9.进一步的,驱动蜗杆一端端头径向延伸成端面设有内六角沉孔的圆柱头,驱动蜗杆一端与圆柱头相邻处径向延伸出凸肩,所述圆柱头、凸肩和驱动蜗杆一端杆部分别嵌在中间环体和中间盖板外缘相邻面各自对应的半圆槽中。
10.进一步的,中间轴下端为花键轴,滑块中心设有花键孔,所述花键轴与花键孔间隙配合;所述花键轴与花键孔间隙配合的种类为h7/f7。
11.进一步的,圆锥齿轮齿隙调整范围为0.1mm至0.5mm。
12.进一步的,所述支撑端两侧分别通过数个滚珠支撑在中间轴上端法兰一侧沉孔与相邻的中间环体一侧沉孔之间。
13.进一步的,传动轴与中间轴的对接平面之间通过传动轴下端法兰中心向下延伸的中心凸台与中间轴上端法兰的中心沉孔间隙配合得到定位,从动圆锥齿轮轴上端法兰与滑块通过一对圆柱销定位。
14.进一步的,齿轮轴下端螺柱的外螺纹和驱动齿轮轴下端螺柱的外螺纹,以及滑块上侧各螺纹孔的内螺纹均为螺距小于等于1mm的细牙螺纹。
15.本实用新型操作时只需用内六角扳手插入驱动蜗杆一端端头的内六角沉孔中转动驱动蜗杆,驱动蜗杆带动与之啮合的蜗轮转动,从而带动驱动齿轮轴转动,再通过驱动齿轮轴中部齿轮带动同步齿圈转动,同步齿圈带动数根齿轮轴与驱动齿轮轴同步旋转,然后通过齿轮轴另一端和驱动齿轮轴另一端与滑块的螺旋传动,接着通过滑块带动与之固定连接的从动圆锥齿轮轴轴向移动,从而带动固定在从动圆锥齿轮轴上的从动圆锥齿轮轴向移动,来调整从动圆锥齿轮与主动圆锥齿轮的齿隙。本实用新型无需通过拆装圆锥齿轮来调整圆锥齿轮的齿隙,大大提高了圆锥齿轮齿隙调整操作的安全性,降低了劳动强度,操作非常方便。由于蜗杆蜗轮传动的速比大,蜗杆转动一圈蜗轮只转动一个齿的圆心角,且驱动齿轮轴和数根齿轮轴和与滑块的螺旋传动为螺距1mm及以下的细牙螺纹传动,使得从动圆锥齿轮与主动圆锥齿轮的齿隙调整精度可达到0.05mm,显著提高了齿隙调整精度和调整工效。本实用新型利用蜗杆蜗轮传动的自锁性能,确保圆锥齿轮的齿隙调整的稳定性和可靠性。
16.本实用新型的优点和特点,将通过下面优选实施例的非限制性说明进行图示和解释,这些实施例,是参照附图仅作为例子给出的。
附图说明
17.图1是本实用新型安装在船用柴油机调速器上的结构图;
18.图2是图1的a-a剖视放大图;
19.图3是图2的b-b剖视图;
20.图4是图2的c-c剖视图。
具体实施方式
21.下面结合附图和本实用新型安装在船用柴油机调速器上的实施例对本实用新型作进一步说明。
22.如图1~图4所示,本实施例包括圆柱齿轮20、主动圆锥齿轮1、从动圆锥齿轮2、主动圆锥齿轮轴3、从动圆锥齿轮轴4、传动轴5、中间轴6、中间环体7、中间盖板8、滑块9、齿隙调整驱动机构10和从动圆锥齿轮轴位移机构11,圆柱齿轮20通过第一平键201固定在主动圆锥齿轮1左端上,主动圆锥齿轮1通过滑动轴承11水平支撑在主动圆锥齿轮轴3右端上,主动圆锥齿轮轴3左端支撑在传动箱体30左侧壁301上。从动圆锥齿轮2通过第二平键21垂直固定在从动圆锥齿轮轴4下端上,主动圆锥齿轮3和从动圆锥齿轮4啮合,并分别通过各自对应的锁紧螺母31锁紧。传动轴5上端伸进传动箱体30上侧的输出传动箱40内,传动轴5与中间轴6的对接平面之间通过传动轴下端法兰51中心向下延伸的中心凸台511与中间轴上端法兰61的中心沉孔611的间隙配合得到定位,提高了传动轴5连接的同轴度。传动轴下端法兰51与中间轴上端法兰61通过4个紧固螺钉52固定连接成一体。从动圆锥齿轮轴上端法兰41与滑块9通过一对圆柱销42定位,通过4个紧固螺钉52固定连接成一体。
23.中间轴6下端依次穿过通过螺钉82固定连接的中间环体7和中间盖板8,中间轴6下端的花键轴62伸进滑块9的花键孔91中,花键轴62与花键孔91间隙配合,两者的间隙配合的种类为h7/f7,显著提高了滑块9的移动精度,进而通过从动圆锥齿轮轴4来提高从动圆锥齿轮2的移动精度。
24.齿隙调整驱动机构10设置在中间环体7和中间盖板8之间,其包括驱动蜗杆101、蜗轮102、斜支撑杆103和驱动齿轮轴104,中间环体7下端设有沉孔71,中间盖板8为环形结构,其设有与中间环体7的沉孔71匹配的通孔81,驱动蜗杆101一端支撑在中间环体7与中间盖板8相邻的环形面之间,驱动蜗杆101另一端支撑在斜支撑杆103一端上,斜支撑杆103另一端焊接固定在中间环体7的沉孔71环面上,且与中间盖板8相邻。蜗轮102固定在驱动齿轮轴104中部上,驱动蜗杆101中部与蜗轮102啮合。驱动蜗杆101一端端头径向延伸成端面设有内六角沉孔的圆柱头1011,驱动蜗杆101一端与圆柱头相邻处径向延伸出凸肩1012,圆柱头1011、凸肩1012和驱动蜗杆101一端的杆部分别嵌在中间环体7和中间盖板8外缘相邻面各自对应的半圆槽72中。这样的结构既便于安装驱动蜗杆101,也便于驱动蜗杆101平稳运转。
25.从动圆锥齿轮轴位移机构11包括同步齿圈111、3根齿轮轴112和3个齿轮轴挡圈113,齿轮轴112结构与驱动齿轮轴104结构相同,齿轮轴112与驱动齿轮轴104径向均布在中间轴上端法兰61、中间盖板8与滑块9上。齿轮轴112上端和驱动齿轮轴104上端分别径向延伸出支撑端1121,支撑端1121两侧分别通过数个滚珠113支撑在中间轴上端法兰一侧沉孔612与相邻的中间环体一侧沉孔72之间,便于驱动齿轮轴104和3根齿轮轴112的同步灵活旋转。
26.齿轮轴下端螺柱1123和驱动齿轮轴下端螺柱1042分别穿过中间环体7拧入滑块9一侧各自对应的螺纹孔92中。同步齿圈111套入中间环体7的沉孔71中,并通过固定在齿轮轴中部齿轮1122下端的挡圈113轴向限位。齿轮轴中部齿轮1122和驱动齿轮轴中部齿轮
1041分别与同步齿圈111啮合,驱动齿轮轴中部齿轮1041在蜗轮102的驱动下旋转时,通过同步齿圈111带动3根齿轮轴112同步旋转,从而带动滑块9、从动圆锥齿轮轴4和从动圆锥齿轮2微量移动,完成从动圆锥齿轮2和主动圆锥齿轮1之间的齿隙调整。本实施例圆锥齿轮齿隙调整范围为0.1mm至0.5mm。
27.齿轮轴下端螺柱1123的外螺纹和驱动齿轮轴下端螺柱1042的外螺纹,以及滑块9上侧各螺纹孔92的内螺纹均为螺距小于等于1mm的细牙螺纹,可实现圆锥齿轮齿隙的微量调整。以本实施例的驱动蜗杆101与蜗轮102的传动比i=20为例,驱动蜗杆101旋转1圈,蜗轮102转动1/20圈,此时驱动齿轮轴104和3根齿轮轴112亦同步转动1/20圈,带动从动圆锥齿轮2移动0.05mm。从动圆锥齿轮2移动的最小距离为0.05mm,从而可实现主动圆锥齿轮1和从动圆锥齿轮2之间齿隙的精准调整,显著提高了圆锥齿轮齿隙的调整精度。
28.除上述实施例外,本实用新型还可以有其他实施方式,凡采用等同替换或等效变换形成的技术方案,均落在本实用新型要求的保护范围内。