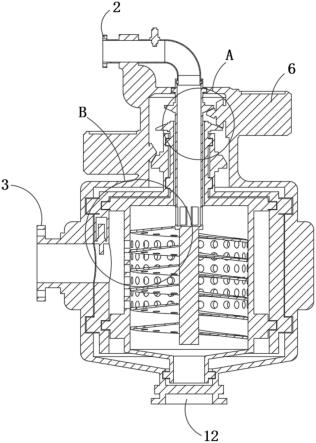
1.本实用新型涉及换向阀技术领域,具体为一种用于叉车的整体式多路换向阀。
背景技术:2.叉车换向阀是实现液压油流的沟通、切断和换向,以及压力卸载和顺序动作控制的阀门,靠阀芯与阀体的相对运动的方向控制阀,有转阀式和滑阀式两种,按阀芯在阀体内停留的工作位置数分为二位、三位等;
3.按与阀体相连的油路数分为二通、三通、四通和六通等,操作阀芯运动的方式有手动、机动、电动、液动、电液等形式。
4.现有的换向阀在油路流通时由于油污的存在,继而导致阀体的内部极易产生堵塞现象,而一旦阻塞,将会降低的降低液压油在换向阀内的流通速率和流通效果,而现有的阀体缺乏对阀内堵塞情况的自检机构同时现有的换向阀缺乏必要的滤油和除污机构,基于此,本实用新型设计了一种用于叉车的整体式多路换向阀,以解决上述问题。
技术实现要素:5.本实用新型的目的在于提供一种用于叉车的整体式多路换向阀,以解决上述背景技术中提出的现有叉车的整体式多路换向阀缺乏对阀体的自检机构及缺乏必要的滤油和除污机构的问题。
6.为实现上述目的,本实用新型提供如下技术方案:一种用于叉车的整体式多路换向阀,包括阀体,所述阀体的顶部固定安装有进油管,所述阀体的周侧面固定连通有一组呈圆周阵列分布的排油支管;
7.所述进油管的内部固定安装有第一流量传感器,所述阀体的周侧面分别固定安装有执行器a和执行器b,所述阀体的内壁转动连接有换向阀筒,所述换向阀筒的周侧面开设有一与排油支管配合的阀孔,所述执行器a的输出轴端与换向阀筒传动连接,所述换向阀筒内部固定安装有与阀孔配合的第二流量传感器,所述换向阀筒的内壁转动连接有外轴管,所述外轴管的底端固定安装有滤油芯筒,所述滤油芯筒的周侧面与换向阀筒转动连接,所述外轴管的内壁转动连接有阀管组件,所述执行器b的输出轴端分别与外轴管和阀管组件传动连接,所述阀体的底部固定连通有与阀管组件配合的排污管,所述滤油芯筒的底端与排污管转动连通。
8.优选的,所述阀管组件包括内阀管,所述内阀管的周侧面与外轴管转动连接,所述内阀管的周侧面与执行器b传动连接,所述内阀管的顶端与进油管转动连通,所述内阀管的周侧面开设有一组呈圆周阵列分布的分油孔,所述内阀管的周侧面且对应分油孔下方的位置固定安装有螺旋滤片,所述螺旋滤片的周侧面与滤油芯筒贴合,所述螺旋滤片的表面开设有一组呈圆周阵列分布的滤油内孔。
9.优选的,所述滤油芯筒的周侧面开设有若干组呈圆周阵列分布的滤油外孔,所述滤油外孔的孔径为滤油内孔孔径的0.2-0.5倍,所述内阀管为顶端开口的中空管状结构。
10.优选的,所述滤油内孔的轴线与阀孔的轴线垂直,所述滤油外孔的轴线与阀孔的轴线平行。
11.优选的,所述阀孔的内径与排油支管的内径相同,所述换向阀筒的周侧面固定设置有与阀体配合的密封胶圈,所述换向阀筒的底部为漏斗状结构,所述排污管的内部固定安装有排污阀。
12.优选的,所述外轴管和内阀管的周侧面均固定安装有与执行器b配合的从动锥齿轮,两个所述从动锥齿轮以执行器b的轴线所在水平面为轴呈对称设置。
13.与现有技术相比,本实用新型的有益效果是:
14.本实用新型通过阀体、滤油芯筒和换向阀筒的设置,使本装置能够高效完成叉车环境中的液压油路换向作业,且本装置在换向作业时,通过第一流量传感器和第二流量传感器的设置,使外部单片机能够通过计算上述两者流量差的方式对阀体内的堵塞情况进行智能自检,通过上述智能自检效果的实现,从而有效提高本换向阀的易维护度和智能化程度,通过滤油芯筒和螺旋滤片的设置,一方面能够在阀体工作时,实现阀体中液压油的高效过滤作业,另一方面在阀体维护时,能够快速将滤出的油污排出。
附图说明
15.为了更清楚地说明本实用新型实施例的技术方案,下面将对实施例描述所需要使用的附图作简单地介绍,显而易见地,下面描述中的附图仅仅是本实用新型的一些实施例,对于本领域普通技术人员来讲,在不付出创造性劳动的前提下,还可以根据这些附图获得其他的附图。
16.图1为本实用新型的结构示意图;
17.图2为本实用新型图1的剖面结构示意图;
18.图3为本实用新型图2中a处的局部放大结构示意图;
19.图4为本实用新型图2中b处的局部放大结构示意图;
20.图5为本实用新型换向阀筒和螺旋滤片的爆炸结构示意图。
21.附图中,各标号所代表的部件列表如下:
22.1-阀体,2-进油管,3-排油支管,4-第一流量传感器,5-执行器a,6-执行器b,7-换向阀筒,8-阀孔,9-第二流量传感器,10-外轴管,11-滤油芯筒,12-排污管,13-内阀管,14-分油孔,15-螺旋滤片,16-滤油内孔,17-滤油外孔,18-从动锥齿轮。
具体实施方式
23.下面将结合本实用新型实施例中的附图,对本实用新型实施例中的技术方案进行清楚、完整地描述,显然,所描述的实施例仅仅是本实用新型一部分实施例,而不是全部的实施例。基于本实用新型中的实施例,本领域普通技术人员在没有作出创造性劳动前提下所获得的所有其它实施例,都属于本实用新型保护的范围。
24.请参阅图1-5,本实用新型提供一种技术方案:一种用于叉车的整体式多路换向阀,包括阀体1,阀体1的顶部固定安装有进油管2,阀体1的周侧面固定连通有一组呈圆周阵列分布的排油支管3;
25.进油管2的内部固定安装有第一流量传感器4,第一流量传感器4设置的作用在于
监测进油管2单位时间内的进油量;
26.阀体1的周侧面分别固定安装有执行器a5和执行器b6,执行器a5和执行器b6均为电机;
27.阀体1的内壁转动连接有换向阀筒7,换向阀筒7的底部为漏斗状结构,换向阀筒7的周侧面固定设置有与阀体1配合的密封胶圈,通过密封胶圈的设置,从而有效保证换向阀筒7与阀体1转动连接处的密封性,执行器a5的输出轴端与换向阀筒7传动连接,换向阀筒7的周侧面开设有一与排油支管3配合的阀孔8,阀孔8的内径与排油支管3的内径相同;
28.换向阀筒7内部固定安装有与阀孔8配合的第二流量传感器9,第二流量传感器9的监测端延伸至阀孔8的内部,第二流量传感器9设置的作用在于监测阀孔8单位时间内的出油量;
29.使用时,本换向阀连接有外部单片机,第一流量传感器4和第二流量传感器9将监测到的数据实时反馈至外部单片机,外部单片机依据第一流量传感器4和第二流量传感器9的数据反馈,以对本换向阀进行自检;
30.第一流量传感器4和第二流量传感器9的型号均为of05zat;
31.换向阀筒7的内壁转动连接有外轴管10,外轴管10的底端固定安装有滤油芯筒11,滤油芯筒11的周侧面开设有若干组呈圆周阵列分布的滤油外孔17,滤油外孔17的轴线与阀孔8的轴线平行,滤油芯筒11的周侧面与换向阀筒7转动连接,外轴管10的内壁转动连接有阀管组件,执行器b6的输出轴端分别与外轴管10和阀管组件传动连接,阀体1的底部固定连通有与阀管组件配合的排污管12,排污管12的内部固定安装有排污阀,滤油芯筒11的底端与排污管12转动连通。
32.阀管组件包括内阀管13,内阀管13为顶端开口的中空管状结构,内阀管13的周侧面与外轴管10转动连接,内阀管13的周侧面与执行器b6传动连接,外轴管10和内阀管13的周侧面均固定安装有与执行器b6配合的从动锥齿轮18,两个从动锥齿轮18以执行器b6的轴线所在水平面为轴呈对称设置;
33.通过两个从动锥齿轮18的上述结构设置,从而使内阀管13和外轴管10的旋向相反;
34.内阀管13的顶端与进油管2转动连通,内阀管13的周侧面开设有一组呈圆周阵列分布的分油孔14,内阀管13的周侧面且对应分油孔14下方的位置固定安装有螺旋滤片15,螺旋滤片15的周侧面与滤油芯筒11贴合,螺旋滤片15的表面开设有一组呈圆周阵列分布的滤油内孔16,滤油外孔17的孔径为滤油内孔16孔径的0.5倍,滤油内孔16的轴线与阀孔8的轴线垂直。
35.工作原理:本装置主要适用于叉车的油路换向作业,使用前,进油管2与叉车中的供油管道连通,各个排油支管3分别与叉车中的使用油路连通,使用时,执行器a5可使阀孔8与指定排油支管3连通,进而进行送油作业,且通过对执行器a5的控制,可转向油路流通方向,继而进行换向作业,本阀体1工作时,执行器b6恒速工作,且通过对执行器b6的输出方向控制,使螺旋滤片15的输料方向向下,通过螺旋滤片15的向下输料设置,从而能够将滤出的杂质不断挤出至排污管12的方向,且在阀体1工作时,第一流量传感器4实时监测进油管2单位时间内的进油量,第二流量传感器9实时监测阀孔8单位时间内的排油量,外部单片机依据第一流量传感器4和第二流量传感器9的流量差以对本换向阀进行堵塞自检,当第一流量
传感器4和第二流量传感器9的流量差超过阈值时,单片机自动报警,相关人员通过打开排污阀或对滤油芯筒11清洁,继而进行本装置的维护和清洁作业。
36.在本说明书的描述中,参考术语“一个实施例”、“示例”、“具体示例”等的描述意指结合该实施例或示例描述的具体特征、结构、材料或者特点包含于本实用新型的至少一个实施例或示例中。在本说明书中,对上述术语的示意性表述不一定指的是相同的实施例或示例。而且,描述的具体特征、结构、材料或者特点可以在任何的一个或多个实施例或示例中以合适的方式结合。
37.以上公开的本实用新型优选实施例只是用于帮助阐述本实用新型。优选实施例并没有详尽叙述所有的细节,也不限制该实用新型仅为所述的具体实施方式。显然,根据本说明书的内容,可作很多的修改和变化。本说明书选取并具体描述这些实施例,是为了更好地解释本实用新型的原理和实际应用,从而使所属技术领域技术人员能很好地理解和利用本实用新型。本实用新型仅受权利要求书及其全部范围和等效物的限制。