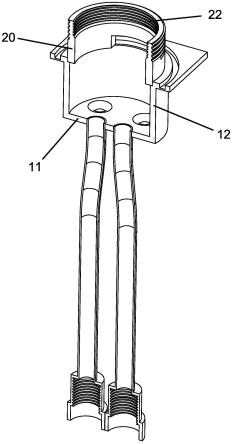
1.本实用新型涉及水龙头领域,具体涉及一种龙头芯子。
背景技术:2.目前的水龙头壳体其内部需要预留用于安装阀芯的阀芯安装位,而现有的水龙头壳体往往采用浇铸或直接棒料切割的方式进行下料,而后在安装阀芯的位置加工出安装孔,同时在阀芯安装孔孔底钻孔;导致了水龙头壳体在生产时消耗材料过多;在后期加工阀芯安装孔、加工位于阀芯安装孔孔底的定位孔及水道时增加了工艺步骤,增加了工艺成本;在后续运输时,过重的水龙头壳体重量无疑又增加了运输成本。
技术实现要素:3.基于上述问题,本实用新型目的在于提供一种结构及工艺简单,生产成本低,且能降低工作噪音的龙头芯子。
4.针对以上问题,提供了如下技术方案:一种龙头芯子,包括固定板,所述固定板中心区域设有与其一体成型且带有底板的安装筒,所述底板设有进水孔;所述安装筒上端或固定板上表面或安装筒上端与固定板上表面交界处设置有固定筒;所述固定筒筒壁上开设有出水孔。
5.上述结构中,在固定板上通过冲压拉伸形成安装筒及底板,阀芯则安装于安装筒内并与底板相抵密封,使阀芯的进水口与进水孔对应;固定筒配合水龙头的其他部件来固定阀芯并对龙头芯子进行辅助安装;龙头体可采用空心管状型材作为外壳,切割下料后与固定板相连或焊接形成主体;固定筒在固定阀芯的同时便于安装龙头的出水支臂,使出水支臂内腔与出水孔对应,从而实现阀芯下端进水,水经阀芯控制从阀芯外圆柱壁进入安装筒内壁与阀芯外圆柱壁之间,而后经固定筒的出水孔进入出水支臂;其整体结构可有效减少材料成本,并减轻重量,便于运输。
6.本实用新型进一步设置为,所述固定筒通过焊接或胶接或螺纹的方式实现固定。
7.上述结构中,固定筒优选采用焊接的方式固定。
8.本实用新型进一步设置为,所述安装筒、底板通过固定板中心区域材料冲压或拉伸或液压成型而成。
9.上述结构中,可有效节约材料,便于降低生产成本。
10.本实用新型进一步设置为,所述固定筒上端内壁及外壁分别设有内螺纹及外螺纹。
11.上述结构中,内螺纹用于安装内压环,使内压环压于阀芯上固定阀芯;外螺纹用于安装外压环,出水支臂通过外压环压于固定板上。
12.本实用新型进一步设置为,所述出水孔自固定筒下端起往其上端方向开设。
13.上述结构中,出水支臂一般为较为扁平截面的瀑布出水,因此为保证出水截面及加工精度,直接在固定筒下端起以开槽的方式设置出水孔,可有效保证出水孔截面呈现扁
平状态。
14.本实用新型进一步设置为,所述进水孔数量为一个或两个或三个,且对应焊接有进水管。
15.上述结构中,进水管远离进水孔的一端设有用于连接水管的接头;进水孔为两个时,分别用于控制冷水引入及热水引入。
16.本实用新型进一步设置为,所述底板设有冲压或拉伸或液压成型形成的定位坑;所述定位坑为两个彼此间隔设置。
17.上述结构中,定位坑用于与阀芯底面的定位柱适配,用于确定阀芯的周向位置。
18.本实用新型进一步设置为,所述固定板上表面设有一圈围绕安装筒外缘设置的密封槽。
19.上述结构中,密封槽用于安装密封圈,在出水支臂与固定板上表面相抵时起到密封作用,避免蹿水。
20.本实用新型进一步设置为,所述安装筒内径大于固定筒内径。
21.上述结构中,阀芯在安装时需要穿过固定筒才能进入安装筒,安装筒内径大于固定筒内径,可保证安装筒与阀芯之间有足够的间隙引导水流进入出水孔,避免间隙过小水流过急带来的噪音。
22.本实用新型进一步设置为,所述安装筒上端内壁设有外径大于安装筒内径的阻挡台阶,所述固定筒端面与阻挡台阶相抵。
23.上述结构中,阻挡台阶用于限制固定筒的轴向位置,便于焊接时定位。
24.本实用新型的有益效果:在固定板上通过冲压拉伸形成安装筒及底板,阀芯则安装于安装筒内并与底板相抵密封,使阀芯的进水口与进水孔对应;固定筒配合水龙头的其他部件来固定阀芯并对龙头芯子进行辅助安装;龙头体可采用空心管状型材作为外壳,切割下料后与固定板相连或焊接形成主体;固定筒在固定阀芯的同时便于安装龙头的出水支臂,使出水支臂内腔与出水孔对应,从而实现阀芯下端进水,水经阀芯控制从阀芯外圆柱壁进入安装筒内壁与阀芯外圆柱壁之间,而后经固定筒的出水孔进入出水支臂;其整体结构可有效减少材料成本,并减轻重量,便于运输。
附图说明
25.图1为本实用新型的整体立体结构图。
26.图2为本实用新型的全剖结构立体图。
27.图3为本实用新型的爆炸立体结构图。
28.图4为本实用新型的爆炸全剖结构图。
29.图中标号含义:10-固定板;11-底板;111-进水孔;112-定位坑;12-安装筒;121-阻挡台阶;13-密封槽;20-固定筒;21-出水孔;22-内螺纹;23-外螺纹;30-进水管;31-接头。
具体实施方式
30.下面结合附图和实施例,对本实用新型的具体实施方式作进一步详细描述。以下实施例用于说明本实用新型,但不用来限制本实用新型的范围。
31.参考图1至图4,如图1至图4所示的一种龙头芯子,包括固定板10,所述固定板10中
心区域设有与其一体成型且带有底板11的安装筒12,所述底板11设有进水孔111;所述安装筒12上端或固定板10上表面或安装筒12上端与固定板10上表面交界处设置有固定筒20;所述固定筒20筒壁上开设有出水孔21。
32.上述结构中,在固定板10上通过冲压拉伸形成安装筒12及底板11,阀芯(图中未示出)则安装于安装筒12内并与底板11相抵密封,使阀芯的进水口(图中未示出)与进水孔111对应;固定筒20配合水龙头的其他部件来固定阀芯并对龙头芯子进行辅助安装;龙头体(图中未示出)可采用空心管状型材作为外壳,切割下料后与固定板10相连或焊接形成主体;固定筒20在固定阀芯的同时便于安装龙头的出水支臂(图中未示出),使出水支臂内腔与出水孔21对应,从而实现阀芯下端进水,水经阀芯控制从阀芯外圆柱壁进入安装筒12内壁与阀芯外圆柱壁之间,而后经固定筒20的出水孔21进入出水支臂;其整体结构可有效减少材料成本,并减轻重量,便于运输。
33.本实施例中,所述固定筒20通过焊接或胶接或螺纹的方式实现固定。
34.上述结构中,固定筒20优选采用焊接的方式固定。
35.本实施例中,所述安装筒12、底板11通过固定板10中心区域材料冲压或拉伸或液压成型而成。
36.上述结构中,可有效节约材料,便于降低生产成本。
37.本实施例中,所述固定筒20上端内壁及外壁分别设有内螺纹22及外螺纹23。
38.上述结构中,内螺纹22用于安装内压环(图中未示出),使内压环压于阀芯上固定阀芯;外螺纹23用于安装外压环(图中未示出),出水支臂通过外压环压于固定板10上。
39.本实施例中,所述出水孔21自固定筒20下端起往其上端方向开设。
40.上述结构中,出水支臂一般为较为扁平截面的瀑布出水,因此为保证出水截面及加工精度,直接在固定筒20下端起以开槽的方式设置出水孔21,可有效保证出水孔21截面呈现扁平状态。
41.本实施例中,所述进水孔111数量为一个或两个或三个,且对应焊接有进水管30。
42.上述结构中,进水管30远离进水孔111的一端设有用于连接水管的接头31;进水孔111为两个时,分别用于控制冷水引入及热水引入。
43.本实施例中,所述底板11设有冲压或拉伸或液压成型形成的定位坑112;所述定位坑112为两个彼此间隔设置。
44.上述结构中,定位坑112用于与阀芯底面的定位柱(图中未示出)适配,用于确定阀芯的周向位置。
45.本实施例中,所述固定板10上表面设有一圈围绕安装筒12外缘设置的密封槽13。
46.上述结构中,密封槽13用于安装密封圈(图中未示出),在出水支臂与固定板10上表面相抵时起到密封作用,避免蹿水。
47.本实施例中,所述安装筒12内径大于固定筒20内径。
48.上述结构中,阀芯在安装时需要穿过固定筒20才能进入安装筒12,安装筒12内径大于固定筒20内径,可保证安装筒12与阀芯之间有足够的间隙引导水流进入出水孔21,避免间隙过小水流过急带来的噪音。
49.本实施例中,所述安装筒12上端内壁设有外径大于安装筒12内径的阻挡台阶121,所述固定筒20端面与阻挡台阶121相抵。
50.上述结构中,阻挡台阶121用于限制固定筒20的轴向位置,便于焊接时定位。
51.本实用新型的有益效果:在固定板10上通过冲压拉伸形成安装筒12及底板11,阀芯(图中未示出)则安装于安装筒12内并与底板11相抵密封,使阀芯的进水口(图中未示出)与进水孔111对应;固定筒20配合水龙头的其他部件来固定阀芯并对龙头芯子进行辅助安装;龙头体(图中未示出)可采用空心管状型材作为外壳,切割下料后与固定板10相连或焊接形成主体;固定筒20在固定阀芯的同时便于安装龙头的出水支臂(图中未示出),使出水支臂内腔与出水孔21对应,从而实现阀芯下端进水,水经阀芯控制从阀芯外圆柱壁进入安装筒12内壁与阀芯外圆柱壁之间,而后经固定筒20的出水孔21进入出水支臂;其整体结构可有效减少材料成本,并减轻重量,便于运输。
52.以上所述仅是本实用新型的优选实施方式,应当指出,对于本技术领域的普通技术人员来说,在不脱离本实用新型技术原理的前提下,还可以做出若干改进和变型,上述假设的这些改进和变型也应视为本实用新型的保护范围。