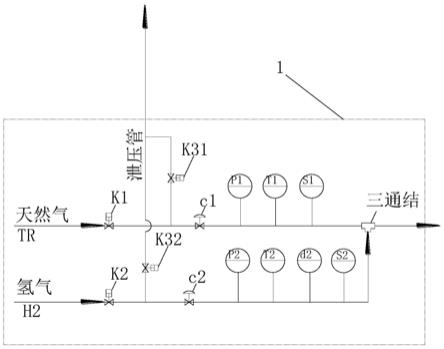
跟踪天然气用户端天然气流量加注氢气并记录减排co2数量的方法及系统
技术领域
1.本发明涉及天然气、氢能源技术领域,进而涉及co2减排领域。
背景技术:2.随着传统化石能源(煤、石油、天然气)储量的日益减少,以及由于使用化石能源带来的环境污染问题,直接威胁着人类的生存和发展,重视和发展可再生、环保能源,减少co2排放已成为各国政府的共识。
3.各种海量研究表明在天然气中添加2%~30%的氢气使用,基本不用更换天然气管网材料及改变用气设备便可提高设备的能效,例如清华大学hcng(加氢天然气)动力机研究团队表示:“hcng发动机ets测试循环的nox co,nmhc,ch4排放和综合燃料消耗率(bsfc)相对于原天然气发动机,掺氢发动机分别下降 51%、36%、60%、47%,而发动机的动力性保持不变”。因此国内的天然气加注氢气的装置也公开很多,如cn105090738a、cn2017215742978a已公开天然气加注氢气的装置,但有如下缺陷:
①
系统复杂、
②
加氢时引起用户端压力波动影响安全使用、
③
加氢系统中出现甲烷与氢气分层现象影响系统安全、
④
加氢系统没有氢气代换天然气而产生的“co2”减排数量记录,从而使清洁能源“执行者”无法参与“碳汇交易市场”获取利益,或享受各种“co2减排政策补贴”。
技术实现要素:4.针对上述已公知技术缺陷,本发明提出“跟踪天然气用户端天然气流量加注氢气并记录减排co2数量的方法及系统”,其发明目的为:在天然气用户端平稳加氢减少加氢时用户端压力波动、加氢时“氢气流量”跟踪“天然气的流量”随用随加、记录氢气代替天然气后的“co2”减排数量,并锁定该数据不可更改。
5.为了实现上述目的,本发明提出的方法有如下四个步序。
6.①“
天然气加注氢气”是在天然气用户端的供气母管有供气流量时随机在线加入氢气的,天然气供气母管流量为零,则氢气加注也停止; 首先对选用的氢气的参数加以修整,使其压力、温度值趋近于天然气的压力、温度,以作到无扰动加注,然后,让氢气管道里的氢气瞬时体积流量跟踪天然气供气母管的瞬时体积流量而变化,其调节模式为“流量随动调节模式”,并气体瞬时体积流量自动折算为瞬时标态体积流量时应满足下列公式:trsi
ꢀꢀꢀ
天然气瞬时标态体积流量;hsi
ꢀꢀꢀꢀ
氢气瞬时标态体积流量;hsi /trsi =b,或
ꢀꢀꢀꢀꢀꢀꢀ
hsi /(trsi+ his) =b
ꢀꢀꢀꢀꢀꢀꢀ
b是上述公式的具体百分比数,其取值范围2%≤b≤30%
②
依据上述现场天然气加注氢气的数据,现场随机自动按等时距(推荐的等时距为每整小时、每整日、每整月)积算出用户燃用标态氢气的累积数,其单位为nm
³
,标准状态
下每燃烧1nm
³
的甲烷气释放出的co2气体为1.9642kg,用户端燃用氢气后的co2气体减排数则为:1.9642
×
燃用标态氢气的累积数,其单位为kg上述等时距的co2气体累计减排数值自动生成电子表格,并电子签章自动锁定为不可更改的数据包;该数据经授权应能随时打印出纸质报表供使用。
7.③
上述
①
的加氢数据、
②
的“co2气体累计减排数据”依据互联网技术同时推送至天然气公司的上位dcs1监控系统及天然气公司所在地的政府环保机关的dcs2系统(仅有监视功能及记录功能),dcs1及dcs2系统收到的“co2气体累计减排数据”也需电子签章确认,dcs1及dcs2系统并与县级、省级、国家环保部的监控系统联网,信息共享。
8.④
为防止现场加氢设备故障,现场应在安全区设立“上位的dcs系统”作为冗余备用,为防止公用因特网故障数据丢失,上述现场dcs系统应具有公用因特网珍断功能,当检测到因特网故障时自动在硬盘上生成“上传输据包”存储,即时的上传输据应源源不断传入“上传输据包”内直至公用因特网故障排出,恢复即时上传数据作业,并同时将“上传输据包”推送到dcs1、dcs2系统;为实施上述方法,本发明的系统由“天然气加氢装置”、“控制及数据采集处理装置”、“数据上传装置”构成,其技术特征是:所述“天然气加氢装置”是在天然气用户端的供气母管上按联通顺序设置气动开关阀k1、带有泄压阀k31的泄压管、气动调节阀c1、防爆压力传感器p1(其读数为p1)、防爆温度传感器t1(其读数为t1)、天然气智能流量积算仪s1(其读数为s1)、天然气管三通结,在氢气的供气母管上按联通顺序设置气动开关阀k2、带有泄压阀k32的泄压管、气动调节阀c2、防爆压力传感器p2(其读数为p2)、防爆温度传感器t2(其读数为t2)、氢气成份含量检测仪d2、氢气智能流量积算仪s2(其读数为s2),并将氢气管道连往天然气管的三通结;泄压阀k31及k32的出口管道连通后,通往安全区高空并排气口应设置防雨罩。
9.上述装置内的气动开关阀、泄压阀可以使用防爆型电磁阀、防爆型电动阀、防爆型液动阀、菲舍尔防爆快速关断阀等同替代,装置内的气动调节阀可以使用防爆型电动调节阀、防爆型液动调节阀、非舍尔防爆调节阀等同替代,替代后的装置依然在本发明的保护范围内。
10.进一步的,上述“现场控制及数据采集处理装置”是由“现场控制柜”、“天然气加氢装置”的各元件及“处于现场安全区的空压机”构成的,其中控制柜为正压运行控制柜,空压机提供净化空气使控制柜正压运行,空压机还为“天然气加氢装置”的气动阀(开关阀、调节阀)提供仪表用标准气源,控制柜外部正面设置有触摸式显示操作屏,控制柜内设置有含plc系统功能芯片的电路板,其具有cpu中央处理功能、di及ai输入输出(嵌入有防爆安全删)功能、pid调节控制功能、网络通讯功能,声光报警功能。
11.ꢀ“
触摸式显示操作屏”在箱内联通“plc系统功能芯片电路板”,再将di及ai输入输出(嵌入有防爆安全删)端子通过埋地电缆与“天然气加氢装置”的气动开关阀k1、泄压阀k31、气动调节阀c1、防爆压力传感器p1、防爆温度传感器t1、天然气智能流量积算仪s1、气动开关阀k2、泄压阀k32、气动调节阀c2、防爆压力传感器p2、防爆温度传感器t2、氢气成份含量检测仪d2、氢气智能流量积算仪s2联通,组成天然气加注氢气的“现场控制及数据采集处理装置”,“现场控制及数据采集处理装置”依据采集到的气体、压力、温度、成分折算出燃
烧氢气替代天然气减排co2的等时距(推荐的等时距为每整小时、每日、每月)累计数量(单位为kg)并在plc显示屏上显示。
12.进一步,所述“数据上传装置”是由上述“现场控制及数据采集处理装置”、设置于用户端现场安全区的上位dcs系统、向用户端供气之地区天然气公司的dcs1系统、负有监管责任的该地区政府环保部门的dcs2系统构成的,其技术特征是:用埋地网线电缆将“现场控制及数据采集处理装置”的通讯模块的输出端子与dcs的通讯模块的输入端子相连通,并且dcs、dcs1、dcs2同时并入公用因特网。
13.为保证加氢现场的安全,上述天然气加注氢气的现场设置有防爆墙将加氢现场分隔为安全区及爆炸危险区,“天然气加氢装置”及“现场控制柜”安装在爆炸危险区内,爆炸危险区内还设置有甲烷检测传感器4、氢气检测传感器5,其信号接入plc的声光报警模块;所述现场dcs系统是由pc1、pc2电脑及dy1、dy2打印机组成的双冗余dcs操作站;pc1操作站、pc2操作站在授权状况下应可接管现场plc的控制权;pc2还兼作工程师站用作编程及调整、修改系统参数。
14.同时安全区还设置有远程监视系统(由dcs操作站管理),其视频监视摄像头应能随时监视并清晰连续拍摄加氢现场情况及现场控制柜上plc显示屏的显示画面,并随时记录。
附图说明
15.图1是“天然气加氢装置”的示意图;图2是现场控制柜的正面布置图,及柜内元件布置图;图3是天然气加氢站的现场布置图;图1、图2、图3中:1是“天然气加氢装置”的集成,其中:气动开关阀k1、气动泄压开关阀k31、气动调节阀c1、防爆压力传感器p1、防爆温度传感器t1、天然气智能流量积算仪s1、气动开关阀k2、气动泄压开关阀k32、气动调节阀c2、防爆压力传感器p2、防爆温度传感器t2、氢气成份含量检测仪d2、氢气智能流量积算仪s2。
16.2是现场控制柜,其中:柜内有交流电源开关ac、给plc供电的直流电源dc、含plc芯片的电路板、应急电源ups,柜外表面有plc显示屏。
17.3是防爆墙、4是甲烷检测传感器、5是氢气检测传感器;pc是电脑、dy是打印机,pc1+pc2+dy1+dy2组成现场双冗余dcs操作系统、pc2还兼作工程师站,dcs操作系统还是现场plc系统的上位机,安全区还设置有远程监视系统(由dcs操作站pc1、pc2管理),其视频监视摄像头应能随时监视现场,并能清晰连续拍摄加氢现场情况及现场控制柜上plc显示屏的显示画面,并随时记录。
具体实施方式
18.下面结合附图及实施例对本发明作进一步的详细描述,但该实施例不应理解为对本发明的限制。
19.实施案例一,社区天然气用户的加氢;此类的天然气供气压力p1通常为2000pa左右,而氢气源的氢气压力p2通常大于2000pa,则在上述“天然气加氢装置”的氢气管道开关
阀k2前加装“自力式压力减压阀”,整定其阀后压力等于2000pa即可。
20.按图3设置加氢站,安排有资质的工程公司安装所有设备并使空压机运转正常,同时甲烷检测传感器4、氢气检测传感器5接入plc系统的声光报警模块,为保证天然气加注氢气的安全,本案例在调试阶段采用“天然气加注氢气的安全模拟调试”,其方法有如下四步序:
⑤
上述“天然气加氢装置”及“现场控制柜”、“上位dcs系统”先在安全区内组装成功,并通电、通气后在安全区内进行模拟调试;先选用空气(压力=p1、温度=t1、瞬时流量=s1)模拟天然气通入天然气母管,再选用99.9%的氮气(压力=p2、温度=t2、瞬时流量=s2)模拟氢气通入氢气管道,将氢气成份检测仪的数值设定为100%(或用仪器模拟检测仪的输出信号加在plc系统的相应输入端子上),通气后,plc系统及dcs系统组态画面显示正常,则在dcs的工程师站上整定pid调节的参数,使空气加注氮气的流量满足“流量随动调节模式”,并气体瞬时体积流量自动折算为瞬时标态体积流量时应满足下列公式:trsi
ꢀꢀꢀ
(空气模拟)天然气瞬时标态体积流量;hsi
ꢀꢀꢀꢀ
(氮气模拟)氢气瞬时标态体积流量;hsi /trsi =b,或
ꢀꢀꢀꢀꢀꢀꢀ
hsi /(trsi+ his) =b
ꢀꢀꢀꢀꢀꢀꢀ
b是上述公式的具体百分比数,其取值范围2%≤b≤30%
⑥
可燃气泄露试验:用试验室微量(安全级别)瓶装甲烷气、氢气分别检验“甲烷检测传感器4”、“氢气检测传感器5”的反应灵敏度,plc及dcs系统的反应能力,如声光报警,应急处理能力(关闭k1、k2同时打开k31、k32);
⑦
系统故障应急试验;人为制造故障,如:控制柜plc系统ac先掉电, plc及dcs系统声光报警,dcs系统自动接管plc系统控制权,画面显示plc的ups电源启动,现场数据采集正常工作,加氢作业继续,(plc故障待处理),1分钟后继续人为制造故障;plc的dc电源掉电,dcs系统自动应急处理(关闭k1、k2同时打开k31、k32);
⑧
上述
⑤
~
⑦
项试验结束,出据试验报告随整套天然气加氢装置移交现场。
21.由于气体的瞬态体积流量与标态体积流量仅与气体的压力、温度有关(与气体密度无关),而氢气的压力、温度事先已修整之与天然气压力、温度趋于相等,则本系统的“流量跟踪调节模拟代换调试”、“数据锁定上传”功能以及本系统的所有功能均可以有效在安全区进行调试检验。
22.模拟调试成功后再将“天然气加氢装置”及“现场控制柜”整体搬运安装在加氢站的实际位置,再实际运行“天然气加氢装置”、“现场控制及数据采集处理装置”、“现场双冗余dcs操作站”,并在dcs的工程师站上修改模拟调试时的pid调节的参数误差,使之符合天然气加氢的实际情况。
23.采用此种方法可以使本发明的系统进行工厂化的生产模式,“天然气加注氢气的安全模拟调试”则成为出厂质量检验的方法之一。
24.实施案例二,乘用车、货运车的天然气用户加气时通常为30mpa,而为维持其加气速率通常加气站采用42.5mpa压力充气,通常的氢气源压力低于42.5mpa本发明在此则需在氢气源母管k2开关阀前增加氢气压缩机,使k2开关阀前氢气压力提升到42.5mpa,再实施天然气加氢的种种事务,上述氢气压力提升后的实施方法与“实施案例一”类同,本文不再赘
述。
25.使用上述本发明的系统及方法进行天然气管道中的氢气加注,加气时供气管道压力始终平稳,保证用气安全,加气时现场生成并锁定“用户端co2减排累积量”数据,并在天然气公司及天然气公司所在地政府环保部门报备,且可随时远程监察,可为加氢实施者参与碳汇交易市场获利、并享受co2减排政策补贴提供支持。