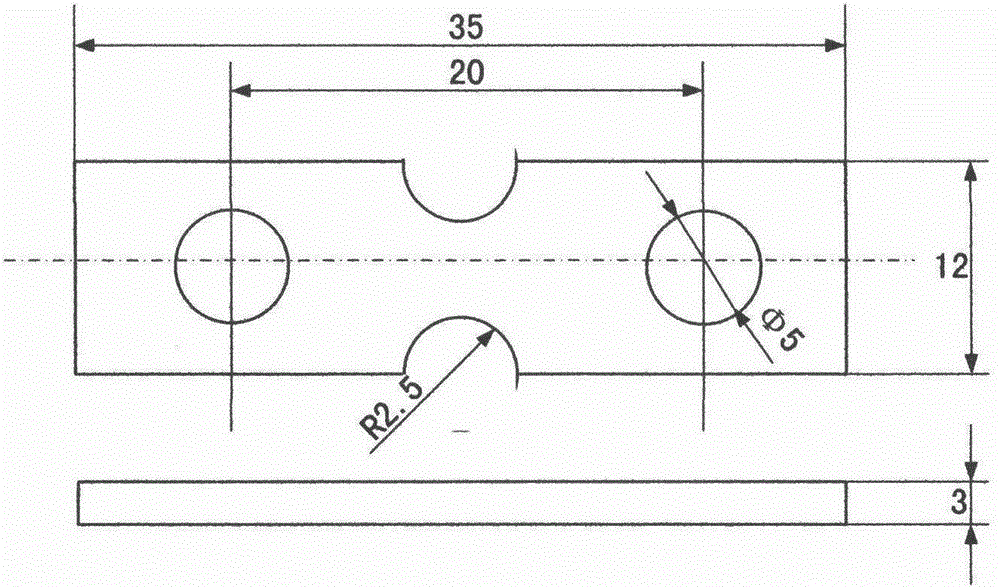
本发明属于含能材料界面性能测试领域,涉及一种用于定量标定含能材料增强颗粒/基体界面特征参数的方法。
背景技术:含能材料的细观结构决定了其宏观性能。在细观尺度上含能材料可以看作是由氧化剂颗粒、金属颗粒、粘合剂以及颗粒与基体之间的粘结界面带所组成的多相非均质颗粒增强复合材料。氧化剂颗粒和粘合剂之间的界面性质是影响整个含能材料性质的重要因素之一,通过改善界面性质可以大大提高材料的性能,改善界面性能的有效方法是在材料中添加微量元素以提高粘合剂和颗粒的粘附性能。当前研究现状下要判断某配方推进剂界面粘附性能,都需要浇注方坯,切成单轴拉伸试件并进行测试,通过测试结果判断配方是否符合要求,这种方法效率低、费用大、效果差,因此在含能材料配方设计和性能评估研究领域急需一种简单方便地标定含能材料颗粒/基体界面性能的方法。表征颗粒/基体界面性能有三个关键参数:界面粘附功、颗粒完全脱粘位移、界面强度。界面粘附功反映了界面分子间作用力的大小,其值越大,表明两者间界面作用越强,界面破坏越困难;颗粒完全脱粘位移表征颗粒与基体完全脱离开时的位移,界面脱粘位移越大,两者的粘附性能越好;界面强度表示颗粒与基体完全脱离时界面的最大抗拉强度。三个参数之间的约束关系如图1所示。其中σn为界面强度,δn为界面脱粘位移,Δ:ABC的面积表示界面粘附功。在本发明以前的现有技术中,以下文献对于含能材料颗粒/基体界面性能的标定进行过一定的尝试,如:[1]H.Tan,Y.Huang,C.Liu,etal.Theuniaxialtensionofparticulatecompositematerialswithnonlinearinterfacedebonding[J].InternationalJournalofSolidsandStructures44(2007)1809-1822[2]MatousK,InglisHM,GuX,elal.MultiscaleModelingofSolidPropellants:FromParticlePackingtoFailure[J].CompositesScienceandTechnology,2007,67(8):1694-1708.[3]周储伟,杨卫,方岱宁.粘聚力界面单元与复合材料的界面损伤分析[J].力学学报,1999,31(3):372-377.[4]李高春,邢耀国,王玉峰,等.基于细观力学的复合固体推进剂模量预估方法[J].推进技术,2007,28(4):441-444.[5]张兴高,张炜,芦伟,等.定应变贮存条件下HTPB推进剂填料/黏合剂界面性能[J].推进技术,2009,30(4):485-489.但是,上述文献中均未提出有效的含能材料颗粒/基体界面性能的定量标定方法。发明目内容针对上述现有技术状况,本发明的目的在于,提供一种基于含能材料组分自身特性的、以界面粘附功、颗粒完全脱粘位移、界面强度作为改善界面性能关键参数的、可以大大缩减配方研制的时间和成本的、简单方便标定界面性能的定量标定方法。现将本发明技术方案叙述如下:本发明含能材料颗粒/基体界面性能的定量标定方法,其特征在于:定量标定界面粘附功、颗粒完全脱粘位移、界面强度三种性能参数,具体步骤如下:步骤1:基于联合点滴法-毛细管上升法接触角测量法进行颗粒/基体界面粘附功标定:步骤1.1:制作基体胶片:根据含能材料粘合剂胶体配方浇注粘合剂胶片,用于步骤1.3的测量;步骤1.2:选择测试液:为防止计算结果出现负值,以确保实验结果的有效性,在测试液的选择上要求:测试液不能溶解待测固体;测试液应具有较高的极性分量,以确保测试液与待测固体的接触角度大于10°;所选择的用于粘合剂基体胶片材料的接触角测量和粉体颗粒材料的接触角测量的测试液应当一个为极性大,另一个为极性小;步骤1.3:粘合剂基体胶片材料的接触角测量:将测试液直接滴在样品表面,每滴体积约5±0.5微升,40±5s时照相,测量读取两种测试液在胶体表面的接触角;将以上测量过程反复进行多次,取多次测定的平均值作为最终的结果;要求环境为温度摄氏25±5℃,相对湿度为65±5%;步骤1.4:粉体颗粒材料的接触角测量:步骤1.4.1:使用测试液测量粉体颗粒材料的毛细管因子c;测量其接触角等于0°时的c值;测量完毕后,选择吸收曲线的斜率,即可以取得毛细管因子c值;测试液应选择已知参数的对粉体颗粒完全润湿的液体,其参数包括:密度、表面张力、粘度;步骤1.4.2:重新选择要测的液体参数,测量粉体颗粒材料的接触角:将粉体颗粒压成多孔柱体,颗粒间隙视为平均等效半径为r的一束毛细管柱,将测试液通过毛细作用渗入粉体柱,在t时间内渗入的高度h可用式(1)描述;h2=cγtr(cosθ/2η)(1)式中γ、η分别为液体的表面张力和粘度,r为粉体毛细管柱的平均等效半径,c为步骤1.4.1所测的毛细管因子;通过相同粉体柱的t-h关系,计算其斜率即为测试液在粉体上的接触角θ;步骤1.5:测试结果及数据处理步骤1.5.1:利用步骤1.3所测得的两种测试液对胶片的接触角,基于式(2)计算得到胶片的表面能参数:极性分量和色散分量;(γld+γld)(1+cosθ)=2(γsdγld)1/2+2(γspγlp)1/2(2)步骤1.5.2:利用1.4所测得的两种测试液对固体颗粒的接触角,基于式(2)计算得到固体颗粒的的表面能参数极性分量和色散分量;步骤1.5.3:利用步骤1.5.1和1.5.2取得颗粒和基体胶片的极性分量和色散分量后,由式(3),即可计算得到颗粒/胶片间界面的粘附功;步骤2:基于原位动态扫描电镜观测拉丝断开长度,标定界面完全脱粘位移:步骤2.1:试样的制作方法是用扫描电镜进行动态观测的关键,所制作的试样要注意保证待观测表面无初始损伤;从复合含能材料中选取一小块试样,切成(如图2所示)微型拉伸试片,送入扫描电镜下进行观测和分析;试件裁剪成哑铃形样条,样条中间部位有效工作距离为2.5±0.5mm;喷镀厚度约为20~30nm;加速电压为10~15kV;步骤2.2:测量完全脱粘位移界面参数:对于完全脱粘位移这一界面参数,从扫描电镜动态拉伸实验可以看出,随着位移的不断增大,颗粒和基体逐渐分离,但仍有连接的粘合剂胶丝,随着拉伸的进一步增大,胶丝越来越少,直到最后完全脱开;这一过程可以视为界面逐渐损伤直至断开的过程;可以观测到:完全脱开时颗粒和基体的距离大约为颗粒的粒径,因此,将颗粒和基体完全脱开时的尺寸作为界面完全脱粘位移;步骤3:基于式(4)标定颗粒/基体的界面强度σb:其中,f为颗粒体积分数,r为颗粒半径,νm为基体泊松比;至此,即得到了含能材料定量标定的界面强度σb值。本发明同现有技术相比的优越性在于:充分考虑了含能材料自身所特有的物理和力学特性,只需要浇注配方中的基体胶片,而不需要浇注方坯,为含能材料颗粒/基体界面参数的选择提供了简单方便性和通用性,大大缩减配方研制的时间和成本。附图说明图1本发明含能材料颗粒/基体界面参数示意图图2:本发明原位拉伸扫描电镜拉伸实验试样尺寸图3:本发明实施例丁羟推进剂扫描图片具体实施方式实施例以下将以丁羟固体推进剂为例,通过其氧化剂颗粒高氯酸铵(AP)和高聚物粘合剂基体间界面参数的标定方法进行说明。步骤1:基于联合点滴法-毛细管上升法接触角测量法的颗粒/基体界面粘附功标定。含能材料中的增强颗粒属于粉体,而粘合剂基体属于固体,其测量接触角的仪器、方法和步骤有所不相同,需采用联合接触角法进行标定;步骤1.1:基体胶片的制作根据含能材料粘合剂胶体配方浇注粘合剂胶片,用于步骤1.3的测量;步骤1.2:测试液的选择为防止计算结果出现负值,以确保实验结果的有效性,在测试液的选择上,有一定的要求:首先,分析醇(即测试液)不能溶解待测固体,其挥发性不能太高;其次,测试液应具有较高的极性分量,以确保接触角度大于10°;第三,为减小测量和计算误差,要选择相同的分析醇来测量胶片和氧化剂粉体的接触角;第四,所选择的两种分析醇应当一个为极性大,另一个极性小;步骤1.3:粘合剂基体胶片材料的接触角测量方法:采用点滴法进行测量基体胶片的接触角;环境要求:温度摄氏25°,相对湿度为65%;测试过程:将测试液直接滴在样品表面,每滴体积约5微升,40s时照相,每种溶液滴5滴,测量读取两种测试液在胶体表面的接触角;将以上测量过程反复进行五次,取五次测定的平均值作为最终的结果;步骤1.4:粉体颗粒材料的接触角测量方法:采用Washburm毛细管上升法测量接触角;测量分两步进行:步骤1.4.1:使用测试液(测试液应选择已知参数的对粉体颗粒完全润湿的液体,其参数包括:密度、表面张力、粘度)测量粉体颗粒材料的毛细管因子c。测量其接触角等于0°时的c值。测量完毕后,选择吸收曲线的斜率,即可以取得毛细管因子c值。步骤1.4.2:重新选择要测的液体参数,测量粉体颗粒材料的接触角;将粉体颗粒压成多孔柱体,颗粒间隙视为平均等效半径为r的一束毛细管柱,将测试液通过毛细作用渗入粉体柱,在t时间内渗入的高度h可用式(1)描述。通过相同粉体柱的t-h关系,计算其斜率即为测试液在粉体上的接触角θ。步骤1.5:测试结果及数据处理步骤1.5.1:利用步骤1.3所测得的两种测试液对胶片的接触角,基于式(2)计算得到胶片的表面能参数极性分量和色散分量;步骤1.5.2:利用1.4所测得的两种测试液对固体颗粒的接触角,基于式(2)计算得到固体颗粒的的表面能参数极性分量和色散分量;步骤1.5.3:利用步骤1.5.1和1.5.2取得颗粒和基体胶片的极性分量和色散分量后,由式(3),即可取得颗粒/胶片间界面的粘附功;步骤2:基于原位动态扫描电镜观测拉丝断开长度步骤2.1:试样的制作方法是用扫描电镜进行动态观测的关键,所制作的试样要注意保证待观测表面无初始损伤。试样的选取是从推进剂材料中,取出一小块。用自制的模具把推进剂材料试片切成如图2所示的微型拉伸试片,送入扫描电镜下进行观测和分析。试件尺寸为35mm×12mm×3mm。裁剪成哑铃形样条,样条中间部位有效工作距离为2.5mm。喷镀厚度约为20~30nm,加速电压为10~15kV。原位动态扫描电镜拉伸试验所得到的图片如图3所示;步骤2.2:从扫描电镜动态拉伸实验可以看出,随着位移的不断增大,颗粒和基体逐渐分离,但仍有连接的粘合剂胶丝,随着拉伸的进一步增大,胶丝越来越少,直到最后完全脱开。这一过程为界面逐渐损伤直至断开的过程。可以观测到:完全脱开时颗粒和基体的距离大约为颗粒的粒径,因此,将AP颗粒和基体完全脱开时的尺寸作为界面完全脱粘位移δn;步骤3:基于式(4)计算颗粒/基体的界面强度σn;最终所确定的本例中丁羟推进剂的界面参数如表1所示。表1界面参数值的确定